-----BEGIN PRIVACY-ENHANCED MESSAGE-----
Proc-Type: 2001,MIC-CLEAR
Originator-Name: webmaster@www.sec.gov
Originator-Key-Asymmetric:
MFgwCgYEVQgBAQICAf8DSgAwRwJAW2sNKK9AVtBzYZmr6aGjlWyK3XmZv3dTINen
TWSM7vrzLADbmYQaionwg5sDW3P6oaM5D3tdezXMm7z1T+B+twIDAQAB
MIC-Info: RSA-MD5,RSA,
Hi6HnZmNzRcZb5vnIxNF5SeMXQuwSKhByt1oKEO3poxUP+PGRqqT8ZBZTeFfcDCB
vs/DAIyWnmbFhKALA7sArw==
0001104659-07-012740.txt : 20070221
0001104659-07-012740.hdr.sgml : 20070221
20070221164052
ACCESSION NUMBER: 0001104659-07-012740
CONFORMED SUBMISSION TYPE: 10-K
PUBLIC DOCUMENT COUNT: 19
CONFORMED PERIOD OF REPORT: 20061230
FILED AS OF DATE: 20070221
DATE AS OF CHANGE: 20070221
FILER:
COMPANY DATA:
COMPANY CONFORMED NAME: TEXTRON INC
CENTRAL INDEX KEY: 0000217346
STANDARD INDUSTRIAL CLASSIFICATION: AIRCRAFT & PARTS [3720]
IRS NUMBER: 050315468
STATE OF INCORPORATION: DE
FISCAL YEAR END: 1231
FILING VALUES:
FORM TYPE: 10-K
SEC ACT: 1934 Act
SEC FILE NUMBER: 001-05480
FILM NUMBER: 07639308
BUSINESS ADDRESS:
STREET 1: 40 WESTMINSTER ST
CITY: PROVIDENCE
STATE: RI
ZIP: 02903
BUSINESS PHONE: 4014212800
MAIL ADDRESS:
STREET 1: 40 WESTMINSTER ST
CITY: PROVIDENCE
STATE: RI
ZIP: 02903
FORMER COMPANY:
FORMER CONFORMED NAME: AMERICAN TEXTRON INC
DATE OF NAME CHANGE: 19710510
10-K
1
a07-4686_110k.htm
10-K
UNITED
STATES SECURITIES AND EXCHANGE COMMISSION
Washington, D.C. 20549
Form 10-K
x ANNUAL REPORT PURSUANT TO SECTION
13 OR 15(d) OF THE SECURITIES EXCHANGE ACT OF 1934
For the fiscal year ended December 30, 2006
Commission File Number
1-5480
Textron
Inc.
(Exact name of registrant as
specified in its charter)
Delaware
|
|
05-0315468
|
(State or other
jurisdiction of
|
|
(I.R.S. Employer
|
incorporation or
organization)
|
|
Identification
No.)
|
40 Westminster Street, Providence, RI 02903
(401) 421-2800
(Address and telephone number
of principal executive offices)
Securities registered
pursuant to Section 12(b) of the Act:
Title of Each Class
|
|
Name of Each
Exchange on Which Registered
|
Common Stock par value 121¤2
¢
|
|
New York Stock Exchange
|
|
|
Chicago Stock Exchange
|
|
|
|
$2.08 Cumulative Convertible Preferred Stock,
|
|
New York Stock Exchange
|
Series A no par value
|
|
|
|
|
|
$1.40 Convertible Preferred Dividend Stock, Series B
|
|
New York Stock Exchange
|
(preferred only as to dividends) no par value
|
|
|
Securities registered
pursuant to Section 12(g) of the Act: None
Indicate by check mark if registrant is a well-known
seasoned issuer as defined in Rule 405 of the Securities Act. Yes x. No o
Indicate by check mark if registrant is not required
to file reports pursuant to Section 13 or Section 15(d) of the Act. Yes o. No x.
Indicate by check mark whether registrant (1) has
filed all reports required to be filed by Section 13 or 15(d) of the Securities
Exchange Act of 1934 during the preceding 12 months (or for such shorter period
that the registrant was required to file such reports) and (2) has been subject
to such filing requirements for the past 90 days. Yes x. No o.
Indicate by check mark if disclosure of delinquent
filers pursuant to Item 405 of Regulation S-K is not contained herein and will
not be contained, to the best of registrants knowledge, in definitive proxy or
information statements incorporated by reference in Part III of this Form 10-K
or any amendment to this Form 10-K. o
Indicate by check mark
whether registrant is a large accelerated filer, an accelerated filer or a
non-accelerated filer. See definition of accelerated filer and large
accelerated filer in Rule 12b-2 of the Exchange Act. (Check one):
Large accelerated filer x Accelerated filer o Non-accelerated filer o
Indicate by check mark whether registrant is a shell
company (as defined in Rule 12b-2 of the Exchange Act). Yes o. No x.
The aggregate market value of the voting common
equity held by non-affiliates computed by reference to the price at which the
common equity was last sold as of the last business day of the registrants
most recently completed second fiscal quarter, July 1, 2006, was
$11,658,757,618. The registrant has no non-voting common equity.
At February 10, 2007, 125,282,174 shares of Common
Stock were outstanding.
Documents
Incorporated by Reference
Part III of this Report incorporates information from
certain portions of the registrants Proxy Statement for its Annual Meeting of
Shareholders to be held on April 25, 2007.
PART I
Item 1. Business of Textron
Textron Inc. is a global multi-industry company
operating in 32 countries with approximately 40,000 employees. Our business was
founded in 1923 and reincorporated in Delaware on July 31, 1967. Today, we
leverage our global network of aircraft, industrial and finance businesses to
provide customers with innovative solutions and services.
Business Segments
We operate in four business segments Bell, Cessna,
Industrial and Finance. Our business segments include operations that are
unincorporated divisions of Textron Inc. or its subsidiaries and others that
are separately incorporated subsidiaries. A description of the business of each
of our business segments is set forth below. Financial information by business
segment and geographic area appears in Note 20 of the consolidated financial
statements on pages 72 through 74 of this Annual Report on Form 10-K.
Bell Segment
The Bell segment is comprised of Bell Helicopter and
Textron Systems.
Bell Helicopter is one of the leading suppliers of
helicopters, tiltrotor aircraft, and helicopter-related spare parts and
services in the world. Bell Helicopter manufactures for both military and
commercial applications. Revenues for Bell Helicopter accounted for
approximately 20%, 21% and 19% of our total revenues in 2006, 2005 and 2004,
respectively.
Bell Helicopter supplies advanced military
helicopters and support (including spare parts, support equipment, technical
data, trainers, pilot and maintenance training, component repairs, aircraft
modifications, contractor maintenance and field and product support engineering
services) to the U.S. Government and to military customers outside the U.S.
Bell Helicopter is one of the leading suppliers of helicopters to the U.S.
Government and, in association with The Boeing Company, the only supplier of
military tiltrotor aircraft. Bell Helicopter is teamed with The Boeing Company
to develop, produce and support the V-22 Osprey tiltrotor aircraft for the U.S.
Department of Defense. Tiltrotor aircraft are designed to provide the benefits
of both helicopters and fixed-wing aircraft. Through Production Lot 11, the
U.S. Government has issued contracts for 113 production V-22 aircraft. The V-22
program calls for a total of 458 production units.
The U.S. Marine Corps H-1 program includes an
advanced attack and a utility model helicopter, the AH-1Z and UH-1Y,
respectively, both of which are designed to have 84% parts commonality between
the two models. Through Low Rate Initial Production (LRIP) Lot 3, the U.S.
Government has issued contracts for the production of 17 UH-1Y aircraft and six
AH-1Z aircraft. The Lot 3 contract has a priced option for Lot 4 requirements
consisting of nine UH-1Y and two AH-1Z additional aircraft. Phase II of the H-1
Operational Evaluation (OPEVAL) is scheduled to commence later in 2007;
successful completion of OPEVAL is required prior to the Government authorizing
full rate production. The H-1 program calls for a total of 280 production
units.
Bell Helicopter currently is performing under a U.S.
Government contract for System Development and Demonstration (SDD) of the
Armed Reconnaissance Helicopter (ARH). This contract requires the production
of four SDD aircraft and includes priced options for LRIP Lot 1 (6-12 aircraft)
and Lot 2 (18-36 aircraft). The ARH program calls for a total of 368 production
units.
Bell Helicopter also is a leading supplier of
commercially certified helicopters to corporate, offshore petroleum exploration
and development, utility, charter, police, fire, rescue and emergency medical
helicopter operators.
Bell Helicopter is a member of Bell/Agusta Aerospace
Company LLC (AWB LLC), a joint venture with Agusta S.p.A. and two of its
affiliated companies (collectively, Agusta), a leading helicopter manufacturer
based in Italy, for the design, manufacture, sale and customer support of the
revolutionary civil tiltrotor aircraft, the Model BA609.
In 2004, Bell Helicopter formed AgustaWestlandBell
LLC with AgustaWestland North America Inc. for the joint design, development,
manufacture, sale, customer training and product support of the VH-71 Presidential
helicopter, and certain variations and derivatives thereof, to be offered
1
and sold to departments or agencies of the U.S.
Government. AWB LLC currently is performing under a SDD subcontract to Lockheed
Martin to design, develop, manufacture and support VH-71 helicopters for the
U.S. Marine Corps Helicopter Squadron HMX.
Bells helicopter business competes against a number
of competitors based in the U.S. and other countries, and its spare parts
business competes against numerous competitors around the world. Competition is
based primarily on price, quality, product support, performance, reliability
and reputation.
Textron Systems is a primary supplier to the defense,
aerospace and general aviation markets. Its principal strategy is to address
the emphasis being placed by the U.S. Department of Defense on network centric
warfare and the leveraging of advances in information technology by focusing on
the development and production of networked sensors, weapons and the associated
algorithms and software. Textron Systems manufactures smart weapons, airborne
and ground-based surveillance systems, aircraft landing systems, hovercraft,
search and rescue vessels, armored vehicles and turrets, reciprocating piston
aircraft engines, and aircraft and missile control actuators, valves and
related components. Textron Systems is involved in supplying the U.S. Air Force
with some of its premier smart weapons as prime contractor for the Sensor Fuzed
Weapon and is a subcontractor to The Boeing Company for tail actuation systems
on the Joint Direct Attack Munition and the next generation Small Diameter
Bomb. Textron Systems is a tier one supplier of unattended ground sensors and
intelligent munitions systems for the U.S. Armys Future Combat System. In
December 2006, Textron Systems acquired Overwatch Systems, a leading supplier
of networking, situational awareness and intelligence analysis software. While
Textron Systems sells most of its products directly to U.S. customers, it also
sells an increasing number of products in more than 25 other countries through
a growing, global network of sales representatives and distributors.
Actuation products for the aerospace, defense and
industrial markets are sold under trade names of HR Textron and APCO. Specialty
marine, land vehicle and turret products are sold under the trade names of
Textron Marine & Land Systems and Cadillac Gage. The recognized need for
armored vehicles for secure transport of U.S. and other armed forces has
resulted in increased demand for the highly protected and cost-effective
vehicles offered by Textron Marine & Land Systems. Weapons, surveillance
and landing systems are sold under the Textron Defense Systems name.
Reciprocating piston aircraft engines are sold under the Lycoming name directly
to general aviation airframe manufacturers and in the aftermarket through
domestic and international distributors. Lycoming also is the exclusive
supplier of engines for Cessnas product line of new single engine aircraft.
Textron Systems competes against a number of
competitors in the U.S. and other countries on the basis of technology,
performance, price, quality and reliability, product support, installed base
and reputation.
Cessna Segment
Based on unit sales, Cessna Aircraft Company is the
worlds largest manufacturer of general aviation aircraft. Cessna currently has
four major product lines: Citation business jets, single engine turboprop
Caravans, Cessna single engine piston aircraft and aftermarket parts and
services. Revenues in the Cessna segment accounted for approximately 36%, 35%
and 30% of our total revenues in 2006, 2005 and 2004, respectively.
The family of business jets currently produced by
Cessna includes the Mustang, Citation CJ1+, Citation CJ2+, Citation CJ3,
Citation Encore+, Citation XLS, Citation Sovereign and Citation X. The Citation
X is the worlds fastest business jet with a maximum operating speed of Mach
..92. First customer deliveries of the Citation CJ2+, an upgrade to the CJ2,
commenced in April 2006. First deliveries of the Encore+, an upgrade of the
Citation Encore, are scheduled to commence in 2007. The Citation Bravo has been
discontinued with the last delivery in December 2006.
The Cessna Caravan is the worlds best selling
utility turboprop. Caravans are offered in three models: the Grand Caravan, the
Super Cargomaster and the Caravan 675. Caravans are used in the U.S. primarily
for overnight express package shipments and for personal transportation.
International uses of Caravans include humanitarian flights, tourism and
freight transport.
Cessna now has six models in its single engine piston
product line: the four-place 172 Skyhawk and 172 Skyhawk SP, 182 Skylane and
Turbo 182 Skylane, and the six-place 206 Stationair and T206 Turbo Stationair.
The Citation family of aircraft currently is
supported by a total of 10 Citation Service Centers owned and operated by
Cessna, along with authorized independent service stations and centers in more than
18 countries throughout the world. The Wichita Citation Service Center is the
worlds largest general aviation maintenance facility. The Cessna-owned Service
Centers provide customers with 24-hour service and maintenance. Cessna also
provides 24-hour spare parts support for Citation aircraft. Cessna Caravan and
single engine piston customers receive product support through independently
owned service stations and 24-hour spare parts support through Cessna. Cessna
markets its products worldwide
2
primarily through its own sales force, as well as
through a network of authorized independent sales representatives, depending
upon the product line. Cessna has several competitors in various market
segments. Cessnas aircraft compete with other aircraft that vary in size,
speed, range, capacity, handling characteristics and price.
Cessna operates a business jet fractional ownership
business through a joint venture called CitationShares. Cessnas current
ownership interest in CitationShares is 86%. This business offers shares of
Citation aircraft for operation throughout the contiguous U.S. and in Canada,
Mexico, Central America, the Caribbean and Bermuda. CitationShares also has a
limited advance purchase jet aircraft charter product called the Vector Jetcard.
Industrial Segment
The Industrial segment is comprised of our E-Z-GO,
Jacobsen, Kautex, Greenlee and Fluid & Power businesses.
E-Z-GO designs, manufactures and sells golf cars and
off-road utility vehicles powered by electric and internal combustion engines
under the E-Z-GO name, as well as multipurpose utility vehicles under the
E-Z-GO and Cushman brand names. E-Z-GOs commercial customers consist primarily
of golf courses, resort communities and municipalities, as well as commercial
and industrial users such as airports and factories. E-Z-GOs off-road utility
vehicles and golf cars also are sold in the consumer market. Sales are made
through a network of distributors and directly to end users. E-Z-GO has two
major competitors for golf cars and several other competitors for utility
vehicles. Competition is based primarily on price, quality, product support,
performance, reliability and reputation.
Jacobsen designs, manufactures and sells professional
turf maintenance equipment and specialized turf care vehicles. Major brand
names include Ransomes, Jacobsen and Cushman. Jacobsens commercial customers
consist primarily of golf courses, resort communities, sporting venues and
municipalities. Sales are made through a network of distributors and directly
to end users. Jacobsen has two major competitors for professional turf
maintenance equipment and several other competitors for specialized turf care.
Competition is based primarily on price, quality, product support, performance,
reliability and reputation.
Kautex, headquartered in Bonn, Germany, is a leading
global manufacturer of blow-molded fuel systems and other blow-molded parts for
automobile original equipment manufacturers and, to a lesser extent, other
industrial customers. Revenues of Kautex accounted for approximately 13%, 15%
and 19% of our total revenues in 2006, 2005 and 2004, respectively. Kautex
operates plants near its major customers all around the world. Kautex also is a
leading supplier of windshield and headlamp washer systems in the original
equipment automobile market. In North America, Kautex produces metal fuel
fillers and engine camshafts for the automotive market. In Germany, Kautex
produces plastic containers for household and industrial uses. Kautex has a
number of competitors worldwide, some of whom are owned by the automotive
original equipment manufacturers that compose Kautexs targeted customer base.
Competition typically is based on a number of factors, including price,
quality, reputation, prior experience and available manufacturing capacity.
Greenlee consists of Greenlee and Klauke. These
companies manufacture powered equipment, electrical test and measurement
instruments, hand and hydraulic powered tools, and electrical and fiber optic
connectors under the Greenlee, Fairmont, Klauke, Progressive and Tempo brand
names. The products principally are used in the electrical construction and
maintenance, telecommunications and plumbing industries. Greenlee distributes
its products through a global network of sales representatives and
distributors, and sells its products directly to home improvement retailers and
original equipment manufacturers. Rothenberger L.L.C., a 50-50 joint venture
between Greenlee Plumbing Inc. and Rothenberger USA, Inc., a subsidiary of
Rothenberger AG, sells hand and powered tools for the plumbing and mechanical
industries in North America. The Greenlee businesses face competition from
numerous manufacturers based primarily on price, quality, performance,
reliability, delivery and reputation.
Fluid & Power consists of four product lines: Gear
Technologies, Union Pump, Polymer Systems and Hydraulics. Gear Technologies
designs and manufactures industrial gears, mechanical transmission systems,
worm gear speed reducers, screwjacks, gear motors and gear sets under the David
Brown, Benzlers, Cone Drive and Radicon brand names, primarily for the defense,
industrial and mining industries. Union Pump designs and manufactures
industrial pumps for the oil, gas, petrochemical and desalinization industries
under the Union brands. Polymer Systems designs and manufactures industrial
pumps, extrusion equipment and screen changers for the polymer industry under
the Maag brand name. Hydraulics designs, manufactures and sells hydraulic
pumps, valves, pilot controls and power takeoffs under the David Brown, Hydreco
and Powauto brands. These products are sold to a variety of customers,
including original equipment manufacturers, governments, distributors and end
users. Fluid & Power faces competition from other manufacturers based
primarily on price, quality, product support, performance, reliability,
delivery and reputation.
3
Finance Segment
Our Finance segment consists of Textron Financial
Corporation and its subsidiaries. Textron Financial Corporation is a
diversified commercial finance company with core operations in six markets:
· Asset-Based Lending provides asset-based loans to middle-market
companies in several industries, and provides factoring arrangements primarily
for freight companies;
· Aviation Finance provides financing for new and used Cessna
business jets, single engine turboprops, piston-engine airplanes, Bell
helicopters and other general aviation aircraft;
· Distribution Finance primarily offers inventory finance programs
for dealers of products manufactured by Textron and for dealers of a variety of
other household, housing, leisure, agricultural and technology products;
· Golf Finance primarily makes mortgage loans for the
acquisition and refinancing of golf courses and provides term financing for
E-Z-GO golf cars and Jacobsen turf-care equipment;
· Resort Finance primarily extends loans to developers of
vacation interval resorts, secured primarily by notes receivable and interval
inventory; and
· Structured Capital primarily engages in long-term leases of large-ticket
equipment and real estate, primarily with investment grade lessees.
Textron Financial Corporations other financial
services and products include transaction syndication, equipment appraisal and
disposition, and portfolio servicing offered through Textron Business Services,
Inc.
Textron Financial Corporations financing activities
are confined almost exclusively to secured lending and leasing to commercial
markets. Textron Financial Corporations services are offered primarily in
North America. However, Textron Financial Corporation finances certain Textron
products worldwide, principally Bell helicopters and Cessna aircraft. Textron
Financial Corporation also finances many of the sales at E-Z-GO and Jacobsen.
In 2006, 2005 and 2004, Textron Financial Corporation
paid Textron $1.0 billion, $0.8 billion and $0.9 billion, respectively, related
to the sale of Textron-manufactured products that were financed by Textron
Financial Corporation. Textron also received proceeds in those years of $63
million, $41 million and $77 million, respectively, from the sale of equipment
from its manufacturing operations to Textron Financial Corporation for use
under operating lease agreements.
The commercial finance environment in which Textron
Financial Corporation operates is highly fragmented and extremely competitive.
Textron Financial Corporation is subject to competition from various types of
financing institutions, including banks, leasing companies, insurance
companies, commercial finance companies and finance operations of equipment
vendors. Competition within the commercial finance industry is primarily
focused on price, terms, structure and service.
Textron Financial Corporations largest business risk
is the collectibility of its finance receivable portfolio. See Finance
Portfolio Quality in Managements Discussion and Analysis of Financial
Condition and Results of Operations on pages 20 and 21 for a detailed
discussion of the credit quality of this portfolio.
Backlog
U.S. Government backlog was $3.5 billion and $3.3
billion at the end of 2006 and 2005, respectively, including backlog at Bell
Helicopter of $2.4 billion in 2006 and $2.2 billion in 2005. Approximately 96%
of the 2006 backlog was funded at December 30, 2006. Unfunded backlog
represents the award value of U.S. Government contracts received, generally
related to cost-plus type contracts, in excess of the funding formally
appropriated by the U.S. Government. The U.S. Government is obligated only up
to the funded amount of the contract. Additional funding is appropriated as the
contract progresses.
Commercial backlog from unaffiliated customers was
$9.8 billion and $7.4 billion in 2006 and 2005, respectively, including backlog
at Cessna of $8.5 billion in 2006 and $6.3 billion in 2005. A significant portion
of Cessnas backlog represents orders from a major fractional jet customer.
Orders from this fractional aircraft operator are included in backlog when the
customer enters into a definitive master agreement and has established
preliminary delivery dates for the aircraft. Preliminary delivery dates are
subject to change through amendment to the master agreement. Final delivery
dates are established approximately 12 to 18 months prior to delivery. Orders
from other customers are included in backlog upon the customer entering into a
definitive purchase order and receipt of required deposits.
4
The 2006 year-end backlog with the major fractional
jet customer was approximately $1.4 billion. The remaining $7.1 billion of
Cessnas backlog at the end of 2006 is with other commercial customers covering
a wide spectrum of industries. This backlog includes $1.0 billion in orders for
the new Citation CJ4 aircraft with the first customer deliveries in 2010.
Approximately 50% of our total backlog of $13.4
billion at December 30, 2006 represents orders which are not expected to be
filled within our 2007 fiscal year.
U.S. Government Contracts
In 2006, approximately 19% of our consolidated
revenues were generated by or resulted from contracts with the U.S. Government.
This business is subject to competition, changes in procurement policies and
regulations, the continuing availability of congressional appropriations, world
events, and the size and timing of programs in which we may participate.
Our contracts with the U.S. Government generally may
be terminated by the U.S. Government for convenience or default in whole or in
part. If the U.S. Government terminates a contract for convenience, we normally
will be entitled to payment for the cost of contract work performed before the
effective date of termination plus reasonable profit on such work, adjusted to
reflect any rate of loss had the contract been completed, plus reasonable costs
of settlement of the work terminated. If, however, the U.S. Government
terminates a contract for default, generally: (a) we will be paid the contract
price for completed supplies delivered and accepted, an agreed-upon amount for
manufacturing materials delivered and accepted and for the protection and
preservation of property, and for partially completed products accepted by the
U.S. Government; (b) the U.S. Government will not be liable for our costs with
respect to unaccepted items and will be entitled to repayment of advance
payments and progress payments related to the terminated portions of the
contract; and (c) we may be liable for excess costs incurred by the U.S.
Government in procuring undelivered items from another source.
Research and Development
Information regarding our research and development
expenditures is contained in Note 16 to the consolidated financial statements
on pages 68 and 69 of this Annual Report on Form 10-K.
Patents and Trademarks
We own, or are licensed under, numerous patents
throughout the world relating to products, services and methods of
manufacturing. Patents have been of value in the past and are expected to be of
value in the future. However, the loss of any single patent or group of patents
would not, in our opinion, materially affect the conduct of our business. We
also own or license trademarks, trade names and service marks that are
important to our business. Some of these trademarks, trade names and service
marks are used in this Annual Report on Form 10-K and other reports, including:
429; AB Benzlers; AH-1Z; APCO; BA609; Bell/Agusta Aerospace Company, LLC; Bell
Helicopter; Bravo; Cadillac Gage; Caravan; Cessna; Citation; CitationShares;
Citation X; CJ1; CJ1+;CJ2; CJ2+;CJ3; Cone Drive; Cushman; David Brown; Excel;
E-Z-GO; Fairmont; Gear Technologies; 429 Global Ranger; Global Technology
Center; Grand Caravan; Greenlee; H-1; HR Textron; Huey II; Hydraulics; Hydreco;
Jacobsen; Kautex; Kiowa Warrior; Klauke Progressive; 429 Light Twin; Lycoming;
Maag; McCauley; Modular Affordable Product Lines; Mustang; Overwatch Systems;
Polymer Systems; Powauto; Power Advantage; ProParts; Quick Draw Loan; Radicon;
Ransomes; Rothenberger LLC; Sensor Fuzed Weapon; Sovereign; Skyhawk; Skyhawk
SP; Skylane; ST 4X4; Stationair; Super Cargomaster; Tempo; Textron; Textron
Business Systems; Textron Financial Corporation; Textron Fluid & Power;
Textron Marine & Land Systems; Textron Six Sigma; Textron Systems; UH-1Y;
Union Pump; US Helicopter; V-22 Osprey; Vector; Vector Jetcard; and XLS. These
marks and their related trademark designs and logotypes (and variations of the
foregoing) are trademarks, trade names or service marks of Textron Inc., its
subsidiaries, affiliates or joint ventures.
Environmental Considerations
Our operations are subject to numerous laws and
regulations designed to protect the environment. Compliance with these laws and
expenditures for environmental control facilities have not had a material
effect on our capital expenditures, earnings or competitive position.
Additional information regarding environmental matters is contained in Note 15
to the consolidated financial statements on page 68 of this Annual Report on
Form 10-K.
Employees
At December 30, 2006, we had approximately 40,000
employees.
Available Information
We make available free of charge on our Internet
website (http://www.textron.com) our Annual Report on Form 10-K, Quarterly
Reports on Form 10-Q, Current Reports on Form 8-K, and amendments to those
reports filed or furnished pursuant to Section 13(a) or 15(d) of the Securities
Exchange Act of 1934 as soon as reasonably practicable after we electronically
file such material with, or furnish it to, the Securities and Exchange
Commission.
5
Item 1A. Risk Factors
Our business, financial condition and results of
operations are subject to various risks, including those discussed below, which
may affect the value of our securities. The risks discussed below are those
that we believe currently are the most significant, although additional risks
not presently known to us or that we currently deem less significant also may
impact our business, financial condition and results of operations, perhaps
materially.
We may be unable to effectively
mitigate pricing pressures.
In some markets, particularly where we deliver
component products and services to original equipment manufacturers, we face
ongoing customer demands for price reductions, which sometimes are
contractually obligated. In some cases, we are able to offset these reductions
through technological advances or by lowering our cost base through improved
operating and supply chain efficiencies. However, if we are unable to
effectively mitigate future pricing pressures, our financial results of
operations could be adversely affected.
Delays in aircraft delivery
schedules or cancellation of orders may adversely affect our financial results.
Aircraft customers, including sellers of fractional
share interests, may respond to weak economic conditions by delaying delivery
of orders or canceling orders. Weakness in the economy also may result in fewer
hours flown on existing aircraft and, consequently, lower demand for spare
parts and maintenance. Weak economic conditions also may cause reduced demand
for used business jets or helicopters. We may accept used aircraft on trade-in
that would be subject to fluctuations in the fair market value of the aircraft
while in inventory. Reduced demand for new and used aircraft, spare parts and
maintenance can have an adverse effect on our financial results of operations.
Developing new products and
technologies entails significant risks and uncertainties.
Delays or cost overruns in the development and
acceptance of new products, or certification of new aircraft products and other
products, could affect our financial results of operations. These delays could
be caused by unanticipated technological hurdles, production changes to meet customer
demands, coordination with joint venture partners or failure on the part of our
suppliers to deliver components as agreed. We also could be adversely affected
if the general efficacy of our research and development investments to develop
products is less than expected.
We have customer concentration with
the U.S. Government.
During 2006, we derived approximately 19% of our
revenues from sales to a variety of U.S. Government entities. Our ability to
compete successfully for and retain this business is highly dependent on
technical excellence, management proficiency, strategic alliances,
cost-effective performance, and the ability to recruit and retain key
personnel. U.S. Government programs are subject to uncertain future funding
levels, which can result in the extension or termination of programs. Our
business also is highly sensitive to changes in national and international
priorities and U.S. Government budgets.
U.S. Government contracts may be
terminated at any time and may contain other unfavorable provisions.
The U.S. Government typically can terminate or modify
any of its contracts with us either for its convenience or if we default by
failing to perform under the terms of the applicable contract. A termination
arising out of our default could expose us to liability and have an adverse
effect on our ability to compete for future contracts and orders.
If any of our contracts are terminated by the U.S.
Government, our backlog would be reduced, in accordance with contract terms, by
the expected value of the remaining work under such contracts, and our
financial condition and results of operations could be adversely affected. In
addition, on those contracts for which we are teamed with others and are not
the prime contractor, the U.S. Government could terminate a prime contract
under which we are a subcontractor, irrespective of the quality of our products
and services as a subcontractor.
In addition to these termination provisions, our U.S.
Government contracts contain provisions that allow the U.S. Government to
unilaterally suspend us from receiving new contracts pending resolution of
alleged violations of procurement laws or regulations, reduce the value of
existing contracts, issue modifications to a contract, and control and
potentially prohibit the export of our products, services and associated
materials.
Cost overruns on U.S. Government
contracts could subject us to losses or adversely affect our future business.
Contract and program accounting require judgment
relative to assessing risks, estimating contract revenues and costs, and making
assumptions for schedule and technical issues. Due to the size and nature of
many of our contracts, the estimation of total revenues and cost at completion
is complicated and subject to many variables. Assumptions have to be made
regarding the length of time to complete the contract because costs
6
include expected increases in wages and prices for
materials. Incentives or penalties related to performance on contracts are
considered in estimating sales and profit rates and are recorded when there is
sufficient information for us to assess anticipated performance. Estimates of
award fees also are used in estimating sales and profit rates based on actual
and anticipated awards.
Because of the significance of the estimates
described above, it is likely that different amounts could be recorded if we
used different assumptions or if the underlying circumstances were to change.
Changes in underlying assumptions, circumstances or estimates may adversely
affect our future financial results of operations.
Under fixed-price contracts, we receive a fixed price
irrespective of the actual costs we incur, and, consequently, any costs in
excess of the fixed price are absorbed by us. Under time and materials
contracts, we are paid for labor at negotiated hourly billing rates and for
certain expenses. Under cost reimbursement contracts, which are subject to a
contract-ceiling amount, we are reimbursed for allowable costs and paid a fee,
which may be fixed or performance based. However, if our costs exceed the
contract ceiling or are not allowable under the provisions of the contract or
applicable regulations, we may not be able to obtain reimbursement for all such
costs. Under each type of contract, if we are unable to control costs we incur
in performing under the contract, our financial condition and results of
operations could be adversely affected. Cost overruns also may adversely affect
our ability to sustain existing programs and obtain future contract awards.
We may make acquisitions that
increase the risks of our business.
We may enter into acquisitions in the future in an
effort to enhance shareholder value. Acquisitions involve a certain amount of
risks and uncertainties that could result in our not achieving expected
benefits. Such risks include difficulties in integrating newly acquired
businesses and operations in an efficient and cost-effective manner; challenges
in achieving expected strategic objectives, cost savings and other benefits;
the risk that the acquired businesses markets do not evolve as anticipated and
that the technologies acquired do not prove to be those needed to be successful
in those markets; the risk that we pay a purchase price that exceeds what the
future results of operations would have merited; the potential loss of key
employees of the acquired businesses; and the risk of diverting the attention
of senior management from our existing operations.
Our operations could be adversely
affected by interruptions of production that are beyond our control.
Our business and financial results may be affected by
certain events that we cannot anticipate or that are beyond our control, such
as natural disasters and national emergencies that could curtail production at
our facilities and cause delayed deliveries and canceled orders. In addition,
we purchase components and raw materials and information technology and other
services from numerous suppliers, and even if our facilities are not directly
affected by such events, we could be affected by interruptions at such suppliers.
Such suppliers may be less likely than our own facilities to be able to quickly
recover from such events and may be subject to additional risks such as
financial problems that limit their ability to conduct their operations.
Our business could be adversely
affected by strikes or work stoppages and other labor issues.
Approximately 18,000 of our employees are unionized,
which represented approximately 45% of our employees at December 30, 2006. As a
result, we may experience work stoppages, which could negatively impact our
ability to manufacture our products on a timely basis, resulting in strain on
our relationships with our customers and a loss of revenues. In addition, the
presence of unions may limit our flexibility in responding to competitive pressures
in the marketplace, which could have an adverse effect on our financial results
of operations.
In addition to our workforce, the workforces of many
of our customers and suppliers are represented by labor unions. Work stoppages
or strikes at the plants of our key customers could result in delayed or
canceled orders for our products. Work stoppages and strikes at the plants of
our key suppliers could disrupt our manufacturing processes. Any of these
results could adversely affect our financial results of operations.
Our Finance borrowing groups
business is dependent on its continuing access to the capital markets.
Our financings are conducted through two borrowing
groups: Finance and Manufacturing. Our Finance group consists of Textron
Financial Corporation and its subsidiaries, which are the entities through
which we operate in the Finance segment. Our Finance group relies on its access
to the capital markets to fund asset growth, fund operations, and meet debt
obligations and other commitments. This group raises funds through commercial
paper borrowings, issuances of medium-term notes and other term debt
securities, and syndication and securitization of receivables. Additional
liquidity is provided to our Finance group through bank lines of credit. Much
of the capital markets funding is made possible by the maintenance of credit
ratings that are acceptable to investors. If the credit ratings of our Finance
group were to be lowered, it might face higher borrowing costs, a disruption of
its access to the capital markets or both. Our Finance group also could lose
access to financing for other reasons, such as a general disruption of the
capital markets. Any disruption of our Finance groups access to the capital
markets could adversely affect its business and our profitability.
7
If our Finance group is unable to
maintain portfolio credit quality, our financial performance could be adversely
affected.
A key determinant of financial performance of our
Finance group will be its ability to maintain the quality of loans, leases and
other credit products in its finance asset portfolios. Portfolio quality may
adversely be affected by several factors, including finance receivable
underwriting procedures, collateral quality, geographic or industry
concentrations or general economic downturns. Any inability by our Finance
group to successfully collect its finance receivable portfolio and to resolve
problem accounts may adversely affect our cash flow, profitability and
financial condition.
We are subject to legal proceedings
and other claims.
We are subject to legal proceedings and other claims
arising out of the conduct of our business, including proceedings and claims
relating to private sector transactions; government contracts; compliance with
applicable laws and regulations; production partners; product liability;
employment; and environmental, safety and health matters. Under federal
government procurement regulations, certain claims brought by the U.S.
Government could result in our being suspended or debarred from U.S. Government
contracting for a period of time. On the basis of information presently
available, we do not believe that existing proceedings and claims will have a
material effect on our financial position or results of operations. However,
litigation is inherently unpredictable, and we could incur judgments or enter
into settlements for current or future claims that could adversely affect our
financial position or our results of operations in any particular period.
The levels of our reserves are
subject to many uncertainties and may not be adequate to cover writedowns or
losses.
In addition to reserves at our Finance group, we
establish reserves in our Manufacturing group to cover uncollectible accounts
receivable, excess or obsolete inventory, fair market value writedowns on used
aircraft and golf cars, recall campaigns, warranty costs and litigation. These
reserves are subject to adjustment from time to time depending on actual
experience and are subject to many uncertainties, including bankruptcy or other
financial problems at key customers.
In the case of litigation matters for which reserves
have not been established because the loss is not deemed probable, it is
reasonably possible such matters could be decided against us and could require
us to pay damages or make other expenditures in amounts that are not presently
estimable.
The effect on our financial results of many of these
factors depends in some cases on our ability to obtain insurance covering
potential losses at reasonable rates.
Currency, raw material price and
interest rate fluctuations may adversely affect our results.
We are exposed to a variety of market risks,
including the effects of changes in foreign currency exchange rates, raw
material prices and interest rates. We monitor and manage these exposures as an
integral part of our overall risk management program. In some cases, we
purchase derivatives or enter into contracts to insulate our financial results
of operations from these fluctuations. Nevertheless, changes in currency exchange
rates, raw material prices and interest rates can have substantial adverse
effects on our financial results of operations.
The increasing costs of certain
employee and retiree benefits could adversely affect our results.
Our earnings and cash flow may be impacted by the
amount of income or expense we expend or record for employee benefit plans.
This is particularly true for our pension plans, which are dependent on actual
plan asset returns and factors used to determine the value and current costs of
plan benefit obligations.
In addition, medical costs are rising at a rate
faster than the general inflation rate. Continued medical cost inflation in
excess of the general inflation rate increases the risk that we will not be
able to mitigate the rising costs of medical benefits. Increases to the costs
of pension and medical benefits could have an adverse effect on our financial
results of operations.
Unanticipated changes in our tax
rates or exposure to additional income tax liabilities could affect our profitability.
We are subject to income taxes in both the U.S. and
various foreign jurisdictions, and our domestic and international tax
liabilities are subject to the allocation of income among these different
jurisdictions. Our effective tax rates could be adversely affected by changes
in the mix of earnings in countries with differing statutory tax rates, changes
in the valuation of deferred tax assets and liabilities, or in tax laws, which
could affect our profitability. In particular, the carrying value of deferred
tax assets is dependent on our ability to generate future taxable income. In
addition, the amount of income taxes we pay is subject to audits in various
jurisdictions, and a material assessment by a tax authority could affect our
profitability.
8
Item 1B. Unresolved Staff Comments
None
Item 2. Properties
On December 30, 2006, we operated a total of 77
plants located throughout the U.S. and 60 plants outside the U.S. Of the total
of 137 plants, we owned 69, and the balance were leased. In the aggregate, the
total manufacturing space was approximately 22.9 million square feet.
We also own or lease offices, warehouse and other
space at various locations. We consider the productive capacity of the plants
operated by each of our business segments to be adequate. In general, our
facilities are in good condition, are considered to be adequate for the uses to
which they are being put and are substantially in regular use.
Item 3. Legal Proceedings
Two identical lawsuits purporting to be class actions
were filed in 2002 in the United States District Court in Rhode Island against
Textron and certain present and former officers of Textron and Bell Helicopter
by Textron shareholders suing on their own behalf and on behalf of a purported
class of Textron shareholders. A consolidated amended complaint alleged that
the defendants failed to make certain accounting adjustments in response to
alleged problems with Bell Helicopters V-22 and H-1 programs and that the
company failed to timely write down certain assets of its OmniQuip unit. The
complaint sought unspecified compensatory damages. On June 15, 2004, the
District Court ruled that the plaintiffs could not maintain the claims that
were based on allegations relating to the H-1 program or to OmniQuip and also
ruled that all claims against one of the individual defendants should be
dismissed. The District Court certified the class of shareholders on May 11,
2005. All claims in the litigation were subsequently settled for a cash amount
that was paid by Textrons insurer. The settlement received final approval of
the District Court on December 13, 2006, and the matter has been concluded.
We are subject to actual and threatened legal
proceedings arising out of the conduct of our business. These proceedings
include claims arising from private transactions, government contracts, product
liability, employment, and environmental, safety and health matters. Some of
these legal proceedings seek damages, fines or penalties in substantial amounts
or remediation of environmental contamination. Under federal government
procurement regulations, certain claims brought by the U.S. Government could
result in our suspension or debarment from U.S. Government contracting for a
period of time. On the basis of information presently available, we believe
that these legal proceedings will not have a material effect on our financial
position or results of operations.
Item 4. Submission of Matters to a Vote of Security
Holders
No matters were submitted to a vote of our security
holders during the last quarter of the period covered by this Annual Report on
Form 10-K.
9
Executive Officers of the Registrant
The following table sets forth certain information
concerning our executive officers as of February 22, 2007. All of our executive
officers are members of our Management Committee and Transformation Leadership
Team.
Name
|
|
Age
|
|
Current Position with Textron Inc.
|
|
|
|
|
|
Lewis B. Campbell
|
|
60
|
|
Chairman, President and Chief Executive Officer;
Director
|
Kenneth C. Bohlen
|
|
54
|
|
Executive Vice President and Chief Innovation
Officer
|
John D. Butler
|
|
59
|
|
Executive Vice President Administration and Chief
Human Resources Officer
|
Ted R. French
|
|
52
|
|
Executive Vice President and Chief Financial Officer
|
Mary L. Howell
|
|
54
|
|
Executive Vice President Government, Strategy
Development and International, Communications and Investor Relations
|
Terrence ODonnell
|
|
62
|
|
Executive Vice President and General Counsel
|
Mr. Campbell joined Textron in September 1992 as
Executive Vice President and Chief Operating Officer. He was named Chief
Executive Officer in July 1998 and appointed Chairman of our Board of Directors
in February 1999. Mr. Campbell served as President and Chief Operating Officer
from January 1994 to July 1998 and reassumed the position of President in
September 2001. Mr. Campbell has been a Director of Textron since January
1994 and is Chairman of our International Advisory Council.
Mr. Bohlen joined Textron in November 1999 as Senior
Vice President and Chief Information Officer and became Executive Vice
President and Chief Innovation Officer in April 2000.
Mr. Butler joined Textron in July 1997 as Executive
Vice President and Chief Human Resources Officer and became Executive Vice
President Administration and Chief Human Resources Officer in January 1999.
Mr. French joined Textron in December 2000 as
Executive Vice President and Chief Financial Officer of Textron Inc. and
assumed the additional position of Chairman and Chief Executive Officer of
Textron Financial Corporation in January 2004.
Ms. Howell has been Executive Vice President
Government, Strategy Development and International, Communications and Investor
Relations since October 2000 and serves on our International Advisory Council.
Ms. Howell joined Textron in 1980 and became an Executive Vice President in August
1995.
Mr. ODonnell joined Textron as Executive Vice
President and General Counsel in March 2000. Mr. ODonnell is a Senior Partner
in the Washington, D.C.-based law firm of Williams & Connolly, which he
first joined in 1977. From 1989 to 1992, he served as General Counsel of the
U.S. Department of Defense.
PART II
Item 5. Market for Registrants Common Equity, Related
Stockholder Matters and Issuer Purchases of Equity Securities
The principal market on which our common stock is
traded is the New York Stock Exchange. Our stock also is traded on the Chicago
Stock Exchange. At December 30, 2006, there were approximately 16,000 holders
of Textron common stock. The high and low common stock prices per share as
reported on the New York Stock Exchange, and the dividends paid per share, in
each case for the periods described below, were as follows:
10
|
|
2006
|
|
2005
|
|
|
|
|
|
|
|
Dividends
|
|
|
|
|
|
Dividends
|
|
|
|
High
|
|
Low
|
|
per Share
|
|
High
|
|
Low
|
|
per Share
|
|
First quarter
|
|
$
|
94.40
|
|
$
|
75.76
|
|
$
|
0.3875
|
|
$
|
80.05
|
|
$
|
68.61
|
|
$
|
0.350
|
|
Second quarter
|
|
98.10
|
|
82.51
|
|
0.3875
|
|
78.30
|
|
71.11
|
|
0.350
|
|
Third quarter
|
|
93.13
|
|
81.10
|
|
0.3875
|
|
78.80
|
|
65.85
|
|
0.350
|
|
Fourth quarter
|
|
98.38
|
|
88.19
|
|
0.3875
|
|
80.00
|
|
69.00
|
|
0.350
|
|
|
|
|
|
|
|
|
|
|
|
|
|
|
|
|
|
|
|
|
|
Issuer
Repurchases of Equity Securities
|
|
|
|
Average
|
|
Total Number
|
|
Maximum
|
|
|
|
Total
|
|
Price Paid
|
|
of Shares
|
|
Number of
|
|
|
|
Number of
|
|
per Share
|
|
Purchased as
|
|
Shares That May
|
|
|
|
Shares
|
|
(excluding
|
|
Part of Publicly
|
|
Be Purchased
|
|
Fourth Quarter
|
|
Purchased
|
|
commissions)
|
|
Announced Plan*
|
|
under the Plan*
|
|
Month 1 (October
1, 2006 November 4, 2006)
|
|
|
|
|
|
|
|
4,617,800
|
|
Month 2
(November 5, 2006 December 2, 2006)
|
|
|
|
|
|
|
|
4,617,800
|
|
Month 3
(December 3, 2006 December 30, 2006)
|
|
230,000
|
|
$
|
94.46
|
|
230,000
|
|
4,387,800
|
|
Total
|
|
230,000
|
|
$
|
94.46
|
|
230,000
|
|
|
|
* These shares were purchased
pursuant to a plan authorizing the repurchase of up to 12 million shares of
Textron common stock that was announced on January 26, 2006 and has no
expiration date.
Stock
Performance Graph
Set forth below is a stock performance graph which shows
the change in market value of $100 invested on December 31, 2001 in our common
stock, Standard & Poors 500 Stock Index and a peer group index. The
cumulative total shareholder return assumes dividends are reinvested. We are a
global, multi-industry company with manufacturing and finance operations
primarily in North America and Europe. Our principal markets are in four
business segments Bell, Cessna, Industrial and Finance. Our peer group
consists of 17 companies in comparable industries in the following Standard
& Poors 500 price index industry groups: aerospace/defense The Boeing
Company, General Dynamics Corporation, Lockheed Martin Corporation and Northrop
Grumman Corporation; auto parts and equipment ITT Industries, Inc.; defense
electronics Raytheon Company; diversified machinery Dover Corporation;
diversified manufacturing Crane Co., Honeywell International, Inc., Illinois
Tool Works Inc., Johnson Controls Inc., Tyco International LTD. and United
Technologies Corporation; electrical equipment Rockwell International
Company; specialized manufacturing Millipore Corporation, Pall Corp. and
Parker Hannifin Corp. The companies in the indices are weighted by market
capitalization.
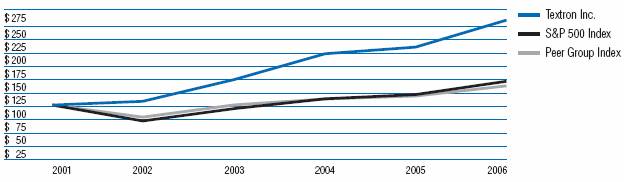
|
|
Dec. 31,
|
|
Dec. 31,
|
|
Dec. 31,
|
|
Dec. 31,
|
|
Dec. 31,
|
|
Dec. 31,
|
|
|
|
2001
|
|
2002
|
|
2003
|
|
2004
|
|
2005
|
|
2006
|
|
Textron Inc.
|
|
$
|
100.00
|
|
$
|
106.82
|
|
$
|
146.55
|
|
$
|
193.69
|
|
$
|
205.78
|
|
$
|
255.05
|
|
S&P 500
|
|
$
|
100.00
|
|
$
|
70.95
|
|
$
|
93.52
|
|
$
|
111.38
|
|
$
|
119.17
|
|
$
|
143.40
|
|
Peer group
|
|
$
|
100.00
|
|
$
|
77.90
|
|
$
|
100.25
|
|
$
|
111.15
|
|
$
|
116.61
|
|
$
|
135.03
|
|
11
Item 6. Selected Financial Data
(Dollars in millions, except per share amounts and where otherwise noted)
|
|
2006
|
|
2005
|
|
2004
|
|
2003
|
|
2002
|
|
Revenues
|
|
|
|
|
|
|
|
|
|
|
|
Bell
|
|
$
|
3,408
|
|
$
|
2,881
|
|
$
|
2,254
|
|
$
|
2,348
|
|
$
|
2,235
|
|
Cessna
|
|
4,156
|
|
3,480
|
|
2,473
|
|
2,299
|
|
3,175
|
|
Industrial
|
|
3,128
|
|
3,054
|
|
3,046
|
|
2,836
|
|
2,627
|
|
Finance
|
|
798
|
|
628
|
|
545
|
|
572
|
|
584
|
|
Total
revenues
|
|
$
|
11,490
|
|
$
|
10,043
|
|
$
|
8,318
|
|
$
|
8,055
|
|
$
|
8,621
|
|
Segment
profit
|
|
|
|
|
|
|
|
|
|
|
|
Bell
|
|
$
|
249
|
|
$
|
368
|
|
$
|
250
|
|
$
|
234
|
|
$
|
169
|
|
Cessna
|
|
645
|
|
457
|
|
267
|
|
199
|
|
376
|
|
Industrial
|
|
163
|
|
150
|
|
194
|
|
150
|
|
169
|
|
Finance
|
|
210
|
|
171
|
|
139
|
|
122
|
|
118
|
|
Total
segment profit
|
|
1,267
|
|
1,146
|
|
850
|
|
705
|
|
832
|
|
Special charges
|
|
|
|
(118
|
)
|
(59
|
)
|
(77
|
)
|
(109
|
)
|
Gain on sale of
businesses
|
|
|
|
|
|
|
|
15
|
|
25
|
|
Corporate
expenses and other, net
|
|
(202
|
)
|
(199
|
)
|
(157
|
)
|
(123
|
)
|
(119
|
)
|
Interest
expense, net
|
|
(90
|
)
|
(90
|
)
|
(94
|
)
|
(96
|
)
|
(105
|
)
|
Income taxes
|
|
(269
|
)
|
(223
|
)
|
(165
|
)
|
(109
|
)
|
(157
|
)
|
Distributions on
preferred securities, net of income taxes
|
|
|
|
|
|
|
|
(13
|
)
|
(26
|
)
|
Income
from continuing operations*
|
|
$
|
706
|
|
$
|
516
|
|
$
|
375
|
|
$
|
302
|
|
$
|
341
|
|
Per
share of common stock
|
|
|
|
|
|
|
|
|
|
|
|
Income from
continuing operations basic*
|
|
$
|
5.53
|
|
$
|
3.86
|
|
$
|
2.73
|
|
$
|
2.22
|
|
$
|
2.46
|
|
Income from
continuing operations diluted*
|
|
$
|
5.43
|
|
$
|
3.78
|
|
$
|
2.68
|
|
$
|
2.20
|
|
$
|
2.43
|
|
Dividends
declared
|
|
$
|
1.55
|
|
$
|
1.40
|
|
$
|
1.33
|
|
$
|
1.30
|
|
$
|
1.30
|
|
Book value at
year-end
|
|
$
|
21.03
|
|
$
|
25.10
|
|
$
|
26.91
|
|
$
|
26.81
|
|
$
|
24.87
|
|
Common stock
price: High
|
|
$
|
98.38
|
|
$
|
80.05
|
|
$
|
74.63
|
|
$
|
57.70
|
|
$
|
53.17
|
|
Low
|
|
$
|
75.76
|
|
$
|
65.85
|
|
$
|
50.84
|
|
$
|
26.85
|
|
$
|
32.49
|
|
Year-end
|
|
$
|
93.77
|
|
$
|
76.98
|
|
$
|
73.80
|
|
$
|
57.19
|
|
$
|
42.16
|
|
Common
shares outstanding (In thousands)
|
|
|
|
|
|
|
|
|
|
|
|
Basic average
|
|
127,549
|
|
133,531
|
|
137,337
|
|
135,875
|
|
138,745
|
|
Diluted
average**
|
|
130,222
|
|
136,446
|
|
140,169
|
|
137,217
|
|
140,252
|
|
Year-end
|
|
125,596
|
|
130,185
|
|
135,373
|
|
137,238
|
|
136,500
|
|
Financial
position
|
|
|
|
|
|
|
|
|
|
|
|
Total assets
|
|
$
|
17,550
|
|
$
|
16,499
|
|
$
|
15,875
|
|
$
|
15,171
|
|
$
|
15,692
|
|
Debt:
|
|
|
|
|
|
|
|
|
|
|
|
Manufacturing group
|
|
$
|
1,800
|
|
$
|
1,934
|
|
$
|
1,770
|
|
$
|
2,008
|
|
$
|
1,681
|
|
Finance group
|
|
$
|
6,862
|
|
$
|
5,420
|
|
$
|
4,783
|
|
$
|
4,407
|
|
$
|
4,840
|
|
Mandatorily redeemable preferred securities trusts:
|
|
|
|
|
|
|
|
|
|
|
|
Manufacturing group
|
|
$
|
|
|
$
|
|
|
$
|
|
|
$
|
|
|
$
|
485
|
|
Finance group
|
|
$
|
|
|
$
|
|
|
$
|
|
|
$
|
26
|
|
$
|
27
|
|
Shareholders
equity
|
|
$
|
2,649
|
|
$
|
3,276
|
|
$
|
3,652
|
|
$
|
3,690
|
|
$
|
3,406
|
|
Manufacturing
group debt-to-capital (net of cash)
|
|
29
|
%
|
26
|
%
|
25
|
%
|
30
|
%
|
36
|
%
|
Manufacturing
group debt-to-capital
|
|
40
|
%
|
37
|
%
|
33
|
%
|
35
|
%
|
39
|
%
|
Investment
data
|
|
|
|
|
|
|
|
|
|
|
|
Capital
expenditures, including capital leases
|
|
$
|
447
|
|
$
|
380
|
|
$
|
294
|
|
$
|
289
|
|
$
|
272
|
|
Depreciation
|
|
$
|
271
|
|
$
|
284
|
|
$
|
265
|
|
$
|
260
|
|
$
|
259
|
|
Research and
development
|
|
$
|
786
|
|
$
|
692
|
|
$
|
574
|
|
$
|
573
|
|
$
|
575
|
|
Other
data
|
|
|
|
|
|
|
|
|
|
|
|
Number of
employees at year-end
|
|
40,000
|
|
37,000
|
|
34,000
|
|
31,000
|
|
36,000
|
|
Number of common
shareholders at year-end
|
|
16,000
|
|
17,000
|
|
18,000
|
|
19,000
|
|
20,000
|
|
*
|
|
Income from continuing operations is before the
cumulative effect of a change in accounting principle in 2002.
|
|
|
|
**
|
|
Diluted average common shares outstanding assumes
full conversion of outstanding preferred stock and exercise of stock options.
|
12
Item 7. Managements Discussion and Analysis of
Financial Condition and Results of Operations
Business Overview and Outlook
We had a strong year in 2006 with many notable
accomplishments across the enterprise. From a financial perspective, revenues,
earnings and operating cash flows from continuing operations were all up
significantly, despite the challenges at Bell with the H-1 upgrade and Armed
Reconnaissance Helicopter (ARH) programs. From a portfolio perspective, we
completed several strategic actions to strengthen our product mix.
Our continued focus on the generation and support of
organic growth through strong investments in engineering, research and
development and capacity expansion were evident across the enterprise. For
example, at Bell Helicopter, our reinvigorated commercial line contributed to a
30% increase in commercial deliveries in 2006 and we are optimistic about
continued helicopter growth, in large part, due to the markets enthusiasm for
our recently introduced 429 model.
New products at Cessna also are generating
extraordinary customer interest and expanding the scope of our market. This
year we introduced two additions to our line of Citation jets, the XLS+ and the
CJ4. We also were the first to certify and deliver a jet, the Mustang, in the
new entry-level jet category. For the year, we booked 496 new jet orders, which
demonstrates the strength of our product line and the market in general.
Some of the more notable financial highlights for
2006 include:
Revenues increased 14% to $11.5
billon in 2006, primarily driven by growth in our aerospace, defense and
finance businesses. Our
organic growth rate, which excludes the effects of acquisitions and
dispositions, was 15%.
Earnings per share from continuing
operations increased 44% to $5.43. The combination of higher revenues and our ongoing cost-containment and
operational efficiency initiatives, along with a decrease in the average of
diluted common shares outstanding, translated into a growth rate more than
triple our revenue growth rate.
Operating cash flows from our
Manufacturing businesses increased by 25% to $1.1 billion. With our strong operating cash flows and solid
balance sheet, we were able to make strategic business acquisitions and return
value to our shareholders as follows:
· We repurchased 8.6 million shares of our
common stock for $751 million.
· We increased our dividend by $0.15 per share
to $1.55 per share, resulting in total dividend payments of $244 million.
· We added two companies, Innovative
Survivability Technologies and Overwatch Systems, to our defense business for
$338 million.
· We acquired a distribution finance business from Electrolux in our
Finance segment for $164 million.
Commercial backlog increased 32% to
$9.8 billion, primarily
related to Cessna. In addition, our U.S. Government backlog increased 6% to
$3.5 billion, primarily in the Bell segment.
We received $644 million in
proceeds related to the disposition of non-core manufacturing businesses. These dispositions include the sale of our
Fastening Systems business and Jacobsens commercial grounds care business.
Revenues
|
|
Earnings
per Share*
|
|
Manufacturing Cash Provided
by Operating Activities*
|
|
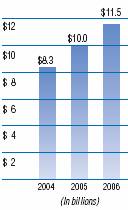
|
|
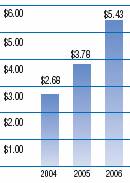
|
|
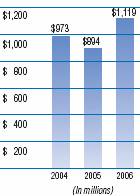
|
* Diluted earnings
per share and Manufacturing cash provided by operating activities are for
continuing operations only.
13
Outlook
Looking ahead, we expect 2007 revenues in excess of
$12 billion, with growth led by our aerospace and defense businesses. We expect
strong growth in business jet deliveries as we deliver against our record
backlog and respond to increasing global demand. We also are preparing to
deliver more commercial helicopters in 2007 as we execute against backlog in
this market. Our defense businesses are expected to remain strong as we
continue to support the U.S. Governments efforts in Iraq and elsewhere. We
expect segment profit to increase reflecting improvements in each of the
manufacturing segments.
Consolidated Results of Operations
Revenues
In 2006, our revenues increased $1.5 billion
primarily due to higher manufacturing sales volume of $1.0 billion, higher
pricing of $274 million and higher revenues in the Finance segment of $170
million. In 2005, revenues increased $1.7 billion primarily due to higher
manufacturing sales volume of $1.3 billion, higher pricing of $159 million,
additional revenues of $115 million from acquisitions and higher revenues in
the Finance segment of $83 million.
Segment Profit
In 2006, our segment profit increased $121 million
primarily due to higher pricing of $274 million, higher sales volume of $198
million, improved cost performance of $54 million in the Industrial segment,
favorable warranty performance at Cessna of $39 million and higher profit in
the Finance segment of $39 million. These increases were partially offset by
inflation of $272 million, higher spending for engineering and new product
development of $74 million, higher overhead of $55 million in Bells commercial
business and increased charges related to the H-1 Low Rate Initial Production
(LRIP) contracts of $68 million. In 2005, segment profit increased $296
million primarily due to higher sales volume of $319 million, higher pricing of
$159 million and higher profit in the Finance segment of $26 million. These
increases were partially offset by inflation of $227 million.
Special Charges
Special charges totaled $118 million for 2005 and
included $112 million in charges related to the 2001 disposition of the
Automotive Trim business (Trim) and $6 million in restructuring expense in
the Industrial segment. In 2004, special charges totaled $59 million and included
$71 million in restructuring expense principally in the Industrial segment,
partially offset by a $12 million gain on the sale of common stock acquired in
connection with the Trim disposition.
In connection with the disposition of Trim to
subsidiaries of Collins & Aikman Corporation (C&A), we acquired
preferred stock in C&A Products Co. (C&A Products) and C&A common
stock. In the first quarter of 2005, we recorded a $52 million impairment
charge to write down the preferred stock based on an agreement to sell the
stock to a third party. In the second quarter of 2005, based on C&A
Products filing for Chapter 11 bankruptcy protection and relevant market
considerations, we wrote off the remaining book value of the preferred stock of
$39 million.
In connection with the Trim disposition, our Finance
group has recourse to our Manufacturing group for equipment leases with the
subsidiaries of C&A. The outstanding balance on these leases totaled
approximately $61 million at December 30, 2006. Based on uncertainties related
to these leases, our Manufacturing group recorded a $10 million reserve to
special charges in the fourth quarter of 2005.
Certain other operating leases were transferred and
assigned to subsidiaries of C&A upon the sale of Trim. As discussed in Note
17 to the consolidated financial statements, we guaranteed C&As payments
under these operating leases and for an environmental matter. In the fourth
quarter of 2005, based on C&As failure to pay certain leases, as well as
the negotiations entered into at the time for the sale of C&As European
operations, we recorded an $11 million charge to special charges to cover our
exposure under these leases, along with certain environmental and workers
compensation matters.
We substantially completed our company-wide
restructuring program at the end of 2005. See Note 14 to the consolidated
financial statements for more information about this program. In 2005, we
recorded $6 million in restructuring expense under the program for severance
and other associated costs. In 2004, we recorded $71 million in restructuring
expense under the program with $37 million in contract termination costs, $28
million in severance costs and $6 million in other associated costs. We have
approximately $30 million in restructuring reserves remaining at the end of
2006 primarily related to contract termination costs for one lease in the
Industrial segment which will be paid out over the next 13 years.
Corporate Expenses and Other, net
Corporate expenses and other, net increased $3 million
in 2006 principally due to $7 million of higher share-based compensation
expense and $4 million of higher incentive compensation, partially offset by $8
million of lower expenses related to corporate initiatives.
14
Corporate expenses and other, net increased $42
million in 2005, principally due to $16 million for higher compensation and
pension costs, $9 million for corporate initiatives and $7 million for the
corporate portion of share-based compensation expense recorded upon the
adoption of a new accounting standard.
Income Taxes
A reconciliation of the federal statutory income tax
rate to the effective income tax rate is provided below:
|
|
2006
|
|
2005
|
|
2004
|
|
Federal
statutory income tax rate
|
|
35.0
|
%
|
35.0
|
%
|
35.0
|
%
|
Increase
(decrease) in taxes resulting from:
|
|
|
|
|
|
|
|
Valuation allowance on contingent receipts
|
|
|
|
2.1
|
|
|
|
State income taxes
|
|
2.3
|
|
0.9
|
|
1.3
|
|
Special foreign dividend
|
|
|
|
0.1
|
|
2.1
|
|
Favorable tax settlements
|
|
(2.4
|
)
|
|
|
|
|
Canadian dollar functional currency
|
|
(1.2
|
)
|
|
|
|
|
Foreign tax rate differential
|
|
(2.7
|
)
|
(5.0
|
)
|
(4.8
|
)
|
Export sales benefit
|
|
(0.8
|
)
|
(1.1
|
)
|
(1.0
|
)
|
Other, net
|
|
(2.6
|
)
|
(1.8
|
)
|
(2.0
|
)
|
Effective income tax
rate
|
|
27.6
|
%
|
30.2
|
%
|
30.6
|
%
|
Discontinued Operations
Discontinued operations reflect after-tax results of
Fastening Systems, InteSys, OmniQuip and the Small Business Direct financing
business, all of which have been sold. See Note 2 to the consolidated financial
statements for additional discussion of these divestiture activities.
Operating results of these discontinued businesses,
primarily related to Fastening Systems, are as follows:
(In millions)
|
|
2006
|
|
2005
|
|
2004
|
|
Revenue
|
|
$
|
1,101
|
|
$
|
1,936
|
|
$
|
1,994
|
|
(Loss) income
from discontinued operations before special charges
|
|
(94
|
)
|
(388
|
)
|
72
|
|
Special charges
|
|
|
|
(11
|
)
|
(91
|
)
|
Loss from
discontinued operations
|
|
(94
|
)
|
(399
|
)
|
(19
|
)
|
Income tax
(expense) benefit
|
|
(11
|
)
|
40
|
|
9
|
|
Operating loss
from discontinued operations, net of income taxes
|
|
(105
|
)
|
(359
|
)
|
(10
|
)
|
Gain on
disposal, net of income taxes
|
|
|
|
46
|
|
|
|
Loss from discontinued
operations, net of income taxes
|
|
$
|
(105
|
)
|
$
|
(313
|
)
|
$
|
(10
|
)
|
In 2005, the loss from discontinued operations
includes a $335 million goodwill impairment charge related to our Fastening
Systems business. In addition, we recorded an after-tax charge of approximately
$52 million in the fourth quarter of 2005, which included $37 million related
to previously deferred foreign currency translation losses and $7 million in
curtailment losses for employee retirement plans. After these charges, we
assessed the estimated fair value of the business and determined that no
further adjustment to the carrying value was required at that time. In the
second quarter of 2006, we recorded an additional $120 million after-tax
impairment charge to record the business at the estimated fair value less cost
to sell at the time based on offers received from potential purchasers.
In 2005, we recorded a net $46 million gain on
disposal, primarily related to a tax benefit recorded upon the sale of InteSys.
Segment Analysis
Our four reportable segments are: Bell, Cessna,
Industrial and Finance. These segments reflect the manner in which we manage
our operations. Segment profit is an important measure used to evaluate
performance and for decision-making purposes. Segment profit for the manufacturing
segments excludes interest expense, certain corporate expenses and special
charges. The measurement for the Finance segment includes interest income and
expense and excludes special charges.
15
Each segments revenues and profit as a percentage of
consolidated revenues and profit are provided below:
2006 Revenues $11.5 Billion
|
2006
Segment Profit $1.3 Billion
|
|
|
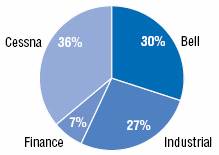
|
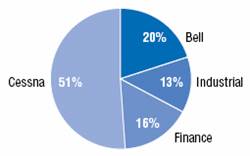
|
Bell
(Dollars in millions)
|
|
2006
|
|
2005
|
|
2004
|
|
Revenues
|
|
$
|
3,408
|
|
$
|
2,881
|
|
$
|
2,254
|
|
Segment profit
|
|
$
|
249
|
|
$
|
368
|
|
$
|
250
|
|
Profit margin
|
|
7
|
%
|
13
|
%
|
11
|
%
|
Backlog at Bell
Helicopter
|
|
$
|
3,119
|
|
$
|
2,812
|
|
$
|
2,842
|
|
Bell Helicopter currently is in the early stages of
development or production for a number of government and commercial programs
that are anticipated to significantly drive revenue and profit growth in future
years. Government programs generally follow a three-phase cycle consisting of:
development, transition to production, and full-rate production ramp-up. Each
phase has specific risks and operational challenges. Over the next few years,
Bell Helicopters major government programs will be transitioning through
various phases of this cycle.
Bell Helicopter programs with the U.S. Government
include the V-22 military tiltrotor aircraft, the H-1 upgrade program and the
ARH program. The V-22 program is in full-rate production and delivered 16
aircraft in 2006. The H-1 upgrade program is in the transition to production
phase, and the ARH program is in the System Development and Demonstration
(SDD) phase.
In 2006, we made significant investments to conduct
research and development, transition development contracts to production,
increase our production capacity and implement improved operational systems to manage
anticipated growth in Bell Helicopters programs. These investments have
negatively impacted our financial results, and include significant ongoing
production ramp-up (primarily for the V-22 program), ongoing development
efforts related primarily to the 429 model and the ARH program, and the H-1s
transition to production.
The costs of investing in improved operational
systems resulted in higher overhead expenses during 2006. While these higher
overhead costs have been reflected in lower 2006 earnings in the commercial
business, a portion of these costs have been absorbed into overhead in the
government business due to the relatively long production cycle, particularly
into V-22 production inventory. The overhead costs are anticipated to moderate
in 2007. However, as V-22 aircraft currently in production are delivered in
future periods, the 2006 overhead expenses reflected in inventory will result
in lower margins on these shipments.
Textron Systems has continued to experience strong
growth in its U.S. Government business, delivering 471 Armored Security
Vehicles (ASV) in 2006 to support our troops in Iraq and elsewhere. During
2006, Textron Systems added to its offerings to the defense industry by
acquiring two businesses, Innovative Survivability Technologies and Overwatch
Systems.
Bell Revenues
U.S. Government Business
In 2006, revenues increased $376 million, compared
with 2005 primarily due to higher net volume and mix of $343 million and the
benefit from acquisitions of $28 million. The volume increase is primarily due
to higher ASV deliveries of $286 million, higher ARH SDD development revenue of
$94 million, increased spares and service sales of $37 million, and additional
Intelligent Battlefield Systems volume of $22 million, partially offset by
lower V-22 volume of $80 million and lower H-1 revenue of $18 million.
In 2005, revenues increased $491 million, compared
with 2004 primarily due to higher revenue of $288 million from the V-22
program, higher ASV volume of $61 million, the benefit of $36 million from the
US Helicopter acquisition, higher military spares volume of $32 million and
increased sales of $20 million for air-launched weapons. Additionally, Bell
recognized $21 million on the ARH SDD contract.
16
Commercial Business
In 2006, commercial revenues increased $151 million,
compared with 2005 due to higher volume of $105 million and pricing of $46
million. The volume increase is primarily due to higher civil aircraft
deliveries of $176 million, higher spares and service sales of $53 million and
additional deliveries of Huey II kits of $10 million, partially offset by lower
international military deliveries of $116 million.
In 2005, commercial revenues increased $136 million,
compared with 2004 primarily due to higher aircraft sales of $68 million,
higher spares volume of $41 million and higher international military sales of
$26 million. International military sales increased primarily due to higher ASV
deliveries to foreign customers of $58 million, partially offset by lower
helicopter volume of $32 million.
Bell Segment Profit
U.S. Government Business
In 2006, profit in our U.S. Government business
decreased $25 million, compared with 2005. The decrease was primarily due to
inflation of $33 million and unfavorable cost performance of $24 million,
partially offset by the impact of higher net volume and mix of $35 million. The
unfavorable performance reflected higher anticipated costs for the H-1 LRIP
contracts of $68 million and charges of $14 million related to the ARH SDD
contract, partially offset by favorable program performance at Textron Systems
of $34 million, primarily related to Hurricane Katrina.
In 2005, profit in our U.S. Government business
increased $33 million, compared with 2004. The increase was principally due to
higher V-22 volume of $26 million, reflecting the delivery of 12 aircraft from
Lots 7 and 8, higher volume and improved performance of air-launched weapons
totaling $13 million, and increased ASV deliveries and improved performance of
$10 million. These increases were partially offset by $18 million of costs
associated with Hurricane Katrina.
H-1 Program The H-1 program continues in development and
currently is undergoing its Operational Evaluation. We also entered into three
firm fixed-price LRIP contracts with the U.S. Government under this program
that represent the first H-1 program production aircraft. In addition, a firm
fixed-price option exists for a fourth production lot. During the transition to
production phase, we anticipate incurring costs in excess of contractual
reimbursement on the first two H-1 LRIP contracts. We anticipate that once the
initial H-1 LRIP aircraft are delivered and the production operations are
validated, costs will moderate as the production configuration is stabilized,
production inefficiencies are resolved and learning curve improvements are
realized.
During 2006, we estimated that the costs to complete
H-1 LRIP Lot 1 would exceed contractual reimbursement. Through the third
quarter of 2006, we recorded $29 million in charges related to the H-1 LRIP Lot
1 contract. These charges primarily reflected the impact of higher estimated
incremental costs for resources added to meet the contractual schedule
requirements and higher anticipated efforts in final assembly. At the end of
the third quarter, we had anticipated that acceptance of the initial H-1 LRIP
Lot 1 aircraft by the U.S. Government would occur in the fourth quarter of
2006. However, acceptance was delayed and no aircraft were delivered. This
delay was due to changes in the development and engineering requirements that
were identified in the final stages of assembly and acceptance testing. Due to
this delay and the costs associated with the additional development efforts,
rework of in-process units and resulting inefficiencies, we increased our
estimate of the completion costs in the fourth quarter. Accordingly, we
recorded an additional $20 million charge related to the H-1 LRIP Lot 1
contract in the fourth quarter of 2006. In January 2007, the U.S. Government accepted
two aircraft and we expect the remaining seven H-1 LRIP Lot 1 units to be
accepted later in 2007.
The H-1 LRIP Lot 2 contract is in the early stages of
production, with first aircraft delivery anticipated in the second half of
2007. We now anticipate that the disruption and delays experienced with the H-1
LRIP Lot 1 contract in the fourth quarter will result in increased costs for
the H-1 LRIP Lot 2 contract due to delays in its completion, as well as a
reduction in previously anticipated learning curve improvements. Due to these
higher cost estimates, the H-1 LRIP Lot 2 contract now is in a loss position
resulting in a fourth quarter charge of $33 million.
The net H-1 program charge, including favorable
performance on the Engineering and Manufacturing Development contract of $3
million, was $50 million in the fourth quarter of 2006.
ARH Program The ARH SDD contract is a cost plus incentive
fee contract under which our eligibility for fees is reduced as total contract
costs increase. During 2006, we continued our development activities for this
program and expensed $14 million in unreimbursed costs related to this effort.
We continue to work with the U.S. Government on development issues,
configuration changes and schedule requirements. We no longer are eligible to
earn fees under this contract; however, we anticipate that any subsequent cost
increases are reimbursable by the U.S. Government.
The U.S. Government had two firm fixed-price options under
this program, representing the first two LRIP lots for the delivery of 24 to 48
aircraft. Certain development
requirements under the ARH SDD contract must be met before the U.S. Government
can exercise the options. We presently
anticipate that the development requirements will be met in mid-2007. The option for the first LRIP lot (for 6-12
aircraft) has expired, while the option for the second lot (for 18-36 aircraft)
expires in December 2007.
17
In the fourth quarter of 2006, we completed certain
phases of the critical design review under the ARH SDD contract and determined
the initial production configuration of the aircraft, which includes aircraft
configuration changes required by the U.S. Government. Our cost estimates based
on this configuration, which include anticipated transition to production
costs, exceed the fixed pricing contained in the options. We currently are in
discussions with the U.S. Government related to the possible reinstatement of
the ARH Lot 1 option, extension of the options, delivery schedule, number of
units to be exercised under the options and possible additional aircraft to be
contracted, in addition to those under the options, at revised pricing. We also
are reviewing our ability to claim equitable adjustment recovery from the U.S.
Government related to certain costs that potentially could be incurred related
to the exercise of these options.
Depending on the results of the SDD contract, our
cost-containment efforts, the availability of U.S. Government funding, the
number of aircraft exercised or ultimately contracted for, and the resolution
of our discussions with the U.S. Government, we currently estimate that it is
reasonably possible that our exposure could be in the range of no loss to a
possible loss of $4 million per aircraft. This estimate excludes the impact of
discussions with the U.S. Government or any potential recoveries including
claims for equitable adjustment under the contracts. Due to the uncertainty of
this exposure and the ultimate outcome of our discussions, we do not believe
that a loss is probable under the guidelines established by Statement of
Financial Accounting Standards (SFAS) No.5, Accounting for Contingencies.
Accordingly, we have not established a reserve at December 30, 2006.
Commercial Business
In 2006, commercial profit decreased $94 million,
compared with 2005 primarily due to unfavorable cost performance of $140
million and inflation of $28 million, partially offset by higher pricing of $46
million and the impact of increased volume and mix of $42 million. The
unfavorable cost performance reflected increased overhead costs of $55 million,
the impact of the $30 million gain on the sale of our interest in the Model
AB139 program in 2005, higher net research and development expense of $29
million and the $13 million prior year impact of the resolution of
uncertainties and receipt of cash related to a collaborative research and
development agreement, partially offset by $18 million in additional reserves
recorded by Lycoming in 2005 for a crankshaft retirement program and related
service bulletins.
In 2005, commercial profit increased $85 million,
compared with 2004 primarily due to the $30 million gain on the sale of our
interest in the Model AB139 helicopter program, the $29 million impact of
higher international military volume and improved performance, higher spares
volume of $22 million and a $13 million impact upon resolution of uncertainties
and receipt of cash related to a prior year collaborative research and
development sharing agreement. In addition, commercial profit reflected a $16
million decrease in net research and development, as higher gross research and
development expenses of $28 million were more than offset by the commercial
share of reimbursements related to risk-sharing agreements from codevelopment
partners. These increases were partially offset by $28 million of higher
selling and administrative expense and $18 million in additional reserves
recorded by Lycoming in 2005 for a crankshaft retirement program and related
service bulletins.
Cessna
(Dollars in millions)
|
|
2006
|
|
2005
|
|
2004
|
|
Revenues
|
|
$
|
4,156
|
|
$
|
3,480
|
|
$
|
2,473
|
|
Segment profit
|
|
$
|
645
|
|
$
|
457
|
|
$
|
267
|
|
Profit margin
|
|
16
|
%
|
13
|
%
|
11
|
%
|
Backlog
|
|
$
|
8,467
|
|
$
|
6,342
|
|
$
|
5,352
|
|
Demand in the business jet market continued to
strengthen in 2006, which was reflected in a 34% increase in our backlog,
despite a 22% increase in business jet deliveries. Over the past three years,
Cessna has increased its annual production rate and has continued to focus on
improving margins while investing in engineering, research and development in
Cessnas continual effort to bring new technology and products to market.
Citation business jets are the largest component of Cessnas revenues. We
delivered 307, 252 and 179 Citation business jets in 2006, 2005 and 2004,
respectively, representing 77%, 76% and 72% of Cessnas total revenues.
Cessna Revenues
Revenues at Cessna increased $676 million in 2006,
compared with 2005 due to higher volume of $493 million, primarily related to
Citation business jets, and favorable pricing of $183 million. In 2005,
Cessnas revenues increased $1.0 billion, compared with 2004 primarily due to
higher Citation business jet volume of $737 million, higher pricing of $82
million and a benefit from the consolidation of CitationShares of $78 million.
18
Cessna Segment Profit
Segment profit increased $188 million at Cessna in
2006, compared with 2005 primarily due to higher pricing of $183 million, the
impact of higher volume of $102 million and favorable warranty performance of
$39 million, partially offset by inflation of $112 million and higher
engineering and product development costs of $41 million. Favorable warranty
performance included the $24 million impact of lower estimated warranty costs
for aircraft sold in 2006, as well as a $15 million incremental benefit from
other favorable warranty performance in 2006 (a $33 million benefit in 2006
compared with $18 million in 2005).
During initial model launches, Cessna typically
incurs higher warranty-related costs until the production process matures, at
which point warranty costs moderate. Based on historical production and
warranty patterns, management estimated that the Sovereign and CJ3 production
lines had reached this maturity level, and that Sovereign and CJ3 aircraft
produced in the third and fourth quarter of 2006 would incur lower warranty
costs than earlier production aircraft. In 2006, Cessnas profit improved by
approximately $24 million as a result of lower point of sale warranty costs for
aircraft sold during the year, primarily Sovereign and CJ3, compared with 2005.
Management expects improved performance on these models to continue in the
foreseeable future.
In 2005, Cessnas segment profit increased $190
million, compared to 2004, largely due to the $229 million impact of higher
volume across all product lines and $82 million of higher pricing, partially
offset by $99 million of inflation.
Industrial
(Dollars in millions)
|
|
2006
|
|
2005
|
|
2004
|
|
Revenues
|
|
$
|
3,128
|
|
$
|
3,054
|
|
$
|
3,046
|
|
Segment profit
|
|
$
|
163
|
|
$
|
150
|
|
$
|
194
|
|
Profit margin
|
|
5
|
%
|
5
|
%
|
6
|
%
|
The Industrial segment is composed of five
businesses, including E-Z-GO, Jacobsen, Kautex, Greenlee and Fluid & Power.
During 2006, we experienced positive organic growth in each of this segments
businesses as we continued to focus on our customers. Both Fluid & Power
and Kautex increased their presence in China to capitalize on the expanding
market. Greenlee prepared to launch their new hand tool product line to
complement their existing products. In our golf and turf care businesses, we
completed the sale of our commercial grounds care business, allowing us to
focus on our core golf, resort, sport turf and municipal markets.
Industrial Revenues
Revenues in the Industrial segment increased $74
million in 2006, compared with 2005 primarily due to higher volume of $89
million, higher pricing of $46 million and a favorable foreign exchange impact
of $10 million, partially offset by the divestiture of non-core product lines
of $72 million.
Revenues in the Industrial segment increased $8
million in 2005, compared with 2004 as higher pricing of $36 million and
favorable foreign exchange of $31 million were largely offset by lower volume
of $63 million. The lower sales volume primarily reflected decreases of $80
million at Kautex, largely due to product model changeovers, and $39 million at
Jacobsen primarily related to the strategic realignment of its North American
commercial distribution network. These decreases were partially offset by
higher volume of $31 million at Greenlee.
Industrial Segment Profit
Segment profit in the Industrial segment increased
$13 million in 2006, compared with 2005 mainly due to $54 million of improved
cost performance, higher pricing of $46 million and the $24 million impact of
higher net volume and mix, partially offset by $100 million of inflation and a
$7 million impact from divestitures of non-core product lines.
Segment profit in the Industrial segment decreased
$44 million in 2005, compared with 2004 largely due to inflation of $84 million
and the impact of lower volume and an unfavorable mix of $21 million, partially
offset by higher pricing of $36 million and improved cost performance of $24
million, primarily at Kautex.
Finance
(Dollars in millions)
|
|
2006
|
|
2005
|
|
2004
|
|
Revenues
|
|
$
|
798
|
|
$
|
628
|
|
$
|
545
|
|
Segment profit
|
|
$
|
210
|
|
$
|
171
|
|
$
|
139
|
|
Profit margin
|
|
26
|
%
|
27
|
%
|
26
|
%
|
19
During 2006, the Finance segment generated
significant growth in its owned and managed finance receivables. Owned finance
receivables grew by $1.5 billion, up 23% from 2005 and we expect continued
growth in 2007. Portfolio quality statistics reflected continued improvements
in 2006. Our nonperforming assets as a percentage of total finance assets
decreased to 1.28% at the end of 2006, compared with 1.53% at the end of 2005
and 2.18% at the end of 2004. While portfolio quality statistics continue to
improve, the collectibility of this segments finance receivable portfolio
remains one of its most significant business risks. The continued strength of
our portfolio quality, combined with continued reductions in the level of loan
losses, resulted in a reduction of the rate utilized to establish the allowance
for losses in several of our portfolios in 2006. This resulted in a $7 million
reduction in the provision for losses during 2006. We expect relative stability
in our portfolio statistics during 2007.
Finance Revenues
Revenues in the Finance segment increased $170
million in 2006, compared with 2005. The increase was primarily due to a $103
million increase related to higher average finance receivables and a $90
million increase from the higher interest rate environment, partially offset by
an $18 million decrease in other income largely due to lower fees and
securitization income. Average finance receivables increased $1.3 billion from
levels in the corresponding period in 2005 primarily due to growth in the
distribution, golf and aviation finance businesses.
Revenues in the Finance segment increased $83 million
in 2005, compared with 2004. The increase was primarily due to higher finance
charges and discounts of $95 million, partially offset by lower prepayment
income of $10 million. The increase in finance charges was largely due to a
higher interest rate environment, which accounted for $98 million of the
increase, and $62 million related to higher average finance receivables of $855
million, partially offset by lower relative receivable pricing of $65 million.
The increase in average finance receivables was primarily related to growth in
distribution, golf and aviation finance, and asset-based lending, partially
offset by reductions in liquidating non-core portfolios.
Finance Segment Profit
Segment profit in the Finance segment increased $39
million in 2006, compared with 2005 due to an increase in net interest margin.
The growth in average finance receivables generated $54 million of higher net
margin, which was partially offset by an $18 million decrease in other income.
Segment profit in the Finance segment increased $32
million in 2005, compared with 2004 primarily due to a $29 million decrease in
the provision for loan losses as a result of sustained improvements in
portfolio quality and an $18 million increase in net interest margin, which was
partially offset by higher selling and administrative expenses of $15 million.
The increase in net interest margin was primarily attributable to portfolio
growth. Selling and administrative expenses increased primarily due to $9
million in higher variable compensation associated with portfolio growth and $5
million related to improved profitability and increased pension and benefits
cost.
Finance Portfolio Quality
The following table presents information about the
Finance segments portfolio quality:
(In millions, except for ratios)
|
|
2006
|
|
2005
|
|
2004
|
|
Finance
receivables
|
|
$
|
8,310
|
|
$
|
6,763
|
|
$
|
5,837
|
|
Allowance for
losses on finance receivables
|
|
$
|
93
|
|
$
|
96
|
|
$
|
99
|
|
Nonperforming
assets
|
|
$
|
113
|
|
$
|
111
|
|
$
|
140
|
|
Provision for
loan losses
|
|
$
|
26
|
|
$
|
29
|
|
$
|
58
|
|
Net charge-offs
|
|
$
|
29
|
|
$
|
32
|
|
$
|
79
|
|
Ratio of
nonperforming assets to total finance assets
|
|
1.28
|
%
|
1.53
|
%
|
2.18
|
%
|
Ratio of
allowance for losses on receivables to nonaccrual finance receivables
|
|
123.1
|
%
|
108.6
|
%
|
83.7
|
%
|
60+ days contractual
delinquency as a percentage of finance receivables
|
|
0.77
|
%
|
0.79
|
%
|
1.47
|
%
|
Nonperforming assets by business are as follows:
(In millions)
|
|
2006
|
|
2005
|
|
2004
|
|
Golf finance
|
|
$
|
29
|
|
$
|
13
|
|
$
|
26
|
|
Resort finance
|
|
16
|
|
31
|
|
53
|
|
Asset-based
lending
|
|
16
|
|
6
|
|
7
|
|
Aviation finance
|
|
12
|
|
14
|
|
12
|
|
Distribution
finance
|
|
7
|
|
2
|
|
5
|
|
Liquidating
portfolios
|
|
33
|
|
45
|
|
37
|
|
Total nonperforming
assets
|
|
$
|
113
|
|
$
|
111
|
|
$
|
140
|
|
20
Nonperforming assets include nonaccrual finance
receivables and repossessed assets that are not guaranteed by our Manufacturing
group. We believe that nonperforming assets generally will be in the range of
1% to 4% of finance assets depending on economic conditions. In 2006, the $16
million increase in golf finance is primarily the result of two delinquent golf
course mortgage loans whose operations were affected by the prolonged effects
of Hurricane Katrina, while the $10 million increase in asset-based lending is
the result of two loans in unrelated industries. The $27 million improvement in
resort finance and the liquidating portfolios in 2006, principally reflected
charge-offs against existing reserves and remedial collection activity. In
2005, nonperforming assets decreased primarily due to resort and golf finance,
reflecting improvement in general economic conditions, partially offset by an
increase in our liquidating portfolios due to two loans. The non-core
liquidating portfolios continue to compose a disproportionate amount of the
nonperforming assets accounting for 29% of total nonperforming assets while
comprising less than 2% of the total finance assets at December 30, 2006.
Liquidity and Capital Resources
Our financings are conducted through two separate
borrowing groups. The Manufacturing group consists of Textron Inc.,
consolidated with the entities that operate in the Bell, Cessna and Industrial
segments, while the Finance group consists of the Finance segment, comprised of
Textron Financial Corporation and its subsidiaries. We designed this framework
to enhance our borrowing power by separating the Finance group. Our
Manufacturing group operations include the development, production and delivery
of tangible goods and services, while our Finance group provides financial
services. Due to the fundamental differences between each borrowing groups
activities, investors, rating agencies and analysts use different measures to
evaluate each groups performance. To support those evaluations, we present balance
sheet and cash flow information for each borrowing group within the
consolidated financial statements.
Through our Finance group, we provide diversified
commercial financing to third parties. In addition, this group finances retail
purchases and leases for new and used aircraft and equipment manufactured by
our Manufacturing group, otherwise known as captive financing. In the
consolidated statements of cash flows, cash received from customers or from
securitizations is reflected as operating activities when received. However, in
the cash flow information provided for the separate borrowing groups, cash
flows related to captive financing activities are reflected based on the
operations of each group. For example, when product is sold by our Manufacturing
group to a customer that is financed by the Finance group, the origination of
the finance receivable is recorded within investing activities as a cash
outflow on our Finance groups statement of cash flows. Meanwhile, the
Manufacturing group records the cash received from the Finance group on the
customers behalf within operating cash flows as a cash inflow on our
Manufacturing groups statement of cash flows. Although cash is transferred
between the two borrowing groups, there is no cash transaction reported in the
consolidated cash flows at the time of the original financing. These captive
financing activities, along with all significant intercompany transactions, are
reclassified or eliminated from the consolidated statements of cash flows, as
detailed below in the operating cash flows of continuing operations section.
Under a support agreement, Textron Inc. is required
to maintain 100% ownership of Textron Financial Corporation. The agreement also
requires Textron Inc. to ensure that Textron Financial Corporation maintains
fixed charge coverage of no less than 125% and consolidated shareholders
equity of no less than $200 million.
Operating Cash Flows of Continuing
Operations
(In millions)
|
|
2006
|
|
2005
|
|
2004
|
|
Manufacturing
group
|
|
$
|
1,119
|
|
$
|
894
|
|
$
|
973
|
|
Finance group
|
|
338
|
|
247
|
|
161
|
|
Reclassifications
and elimination adjustments
|
|
(440
|
)
|
(189
|
)
|
(185
|
)
|
Consolidated
|
|
$
|
1,017
|
|
$
|
952
|
|
$
|
949
|
|
Cash flows from operations are the primary source of
funds for our operating needs, dividends and capital expenditures. We analyze
operating cash flows for our Manufacturing group by tracking free cash flow. We
calculate free cash flow using net cash provided by operating activities,
adding back proceeds on the sale of property, plant and equipment, then
subtracting capital expenditures, including those financed with capital leases.
21
The Manufacturing groups operating cash flows
increased in 2006 compared with 2005 primarily due to the increase in income
from continuing operations and a decrease in working capital components.
Consolidated operating cash flows increased primarily due to the increase in
income from continuing operations for both borrowing groups and a decrease in
working capital components, partially offset by a $224 million increase in net
captive financing activity as explained below.
Reclassification and Elimination
Adjustments
(In millions)
|
|
2006
|
|
2005
|
|
2004
|
|
Reclassifications
from investing activities:
|
|
|
|
|
|
|
|
Finance receivable originations for Manufacturing
group inventory sales
|
|
$
|
(1,015
|
)
|
$
|
(824
|
)
|
$
|
(892
|
)
|
Cash received from customers and securitizations for
captive financing
|
|
691
|
|
724
|
|
727
|
|
Other
|
|
(36
|
)
|
11
|
|
51
|
|
Total
reclassifications from investing activities
|
|
(360
|
)
|
(89
|
)
|
(114
|
)
|
Dividends paid
by Finance group to Manufacturing group
|
|
(80
|
)
|
(100
|
)
|
(71
|
)
|
Total reclassifications
and adjustments
|
|
$
|
(440
|
)
|
$
|
(189
|
)
|
$
|
(185
|
)
|
Finance receivable originations for Manufacturing
group inventory sales increased in 2006 compared with 2005 primarily due to
financings related to aircraft sales growth during the period. However, cash
received for these captive receivables decreased in 2006 as higher cash
receipts from our customers were offset by $126 million in lower proceeds from
securitizations.
Investing Cash Flows of Continuing
Operations
(In millions)
|
|
2006
|
|
2005
|
|
2004
|
|
Manufacturing
group
|
|
$
|
(742
|
)
|
$
|
(362
|
)
|
$
|
(158
|
)
|
Finance group
|
|
(1,680
|
)
|
(950
|
)
|
(756
|
)
|
Reclassifications
to operating activities
|
|
360
|
|
89
|
|
114
|
|
Consolidated
|
|
$
|
(2,062
|
)
|
$
|
(1,223
|
)
|
$
|
(800
|
)
|
Over the past three years, consolidated investing
cash flows have been largely driven by increases in cash outflows at our
Finance group due to higher non-captive finance receivable originations, net of
cash collections from repayments, sales and securitizations, of $301 million,
$198 million and $744 million, respectively.
The $380 million increase in cash used for the
Manufacturing group in 2006 is largely due to the acquisition of two businesses
in the Bell segment for $338 million in cash, along with an increase in capital
expenditures of $63 million. In 2005, the Manufacturing group increased its use
of cash for investing by $204 million with $118 million in higher capital
expenditures, along with a $38 million decrease in proceeds that were received
in 2004 from the sale of C&A common stock. The increases in capital
expenditures in 2006 and 2005 are primarily related to higher spending at the
Bell segment in response to increased production demands. Capital expenditures
related to our manufacturing operations totaled $435 million in 2006, $371
million in 2005 and $282 million in 2004, including expenditures purchased
through capital leases of $16 million in 2006, $15 million in 2005 and $44
million in 2004.
Financing Cash Flows of Continuing
Operations
(In millions)
|
|
2006
|
|
2005
|
|
2004
|
|
Manufacturing
group
|
|
$
|
(1,072
|
)
|
$
|
(403
|
)
|
$
|
(708
|
)
|
Finance group
|
|
1,391
|
|
587
|
|
361
|
|
Dividends paid
by Finance group to Manufacturing group
|
|
80
|
|
100
|
|
71
|
|
Consolidated
|
|
$
|
399
|
|
$
|
284
|
|
$
|
(276
|
)
|
Our Manufacturing group used $669 million more cash
for financing activities in 2006 compared with 2005. The increase is primarily
due to the paydown of $242 million of short-term debt in 2006 compared with the
issuance of $281 million of short-term debt in 2005, and to a $164 million
increase in purchases of our common stock. Our Manufacturing group used less
cash for financing activities in 2005 than in 2004 principally due to the
issuance of the short-term debt in 2005 and the retirement of debt of $300
million in 2004, partially offset by a $182 million increase in purchases of
our common stock and $81 million in lower proceeds from employee stock
ownership plans. Our Finance group has continued to increase its debt
outstanding over the past three years to fund asset growth.
22
Stock Repurchases
In 2006, 2005 and 2004, we repurchased approximately
8,574,000, 8,035,000 and 6,534,000 shares of common stock, respectively, under
Board-authorized share repurchase programs for an aggregate cost of $751
million, $606 million and $425 million, respectively. On January 26, 2006, our
Board of Directors authorized a new 12 million-share repurchase program of
which 4.4 million shares remained at December 30, 2006.
Dividends
On January 26, 2006, the Board of Directors
authorized a $0.15 per share increase in our annualized common stock dividend
to $1.55 per share. Dividend payments to shareholders totaled $244 million,
$189 million and $135 million in 2006, 2005 and 2004, respectively. The timing
of our quarterly dividend payments resulted in five payments in 2006, four
payments in 2005 and three payments in 2004.
Discontinued Operations Cash Flows
(In millions)
|
|
2006
|
|
2005
|
|
2004
|
|
Operating
activities
|
|
$
|
(48
|
)
|
$
|
84
|
|
$
|
1
|
|
Investing
activities
|
|
$
|
653
|
|
$
|
28
|
|
$
|
(18
|
)
|
Financing activities
|
|
$
|
2
|
|
$
|
(1
|
)
|
$
|
|
|
Discontinued operations cash flows from investing
activities increased in 2006 primarily due to net cash proceeds of $636 million
related to the sale of the Fastening Systems business. See Note 2 to the
consolidated financial statements for details concerning our discontinued
operations.
Capital Resources
The debt (net of cash)-to-capital ratio for our
Manufacturing group as of December 30, 2006 was 29%, compared with 26% at
December 31, 2005, and the gross debt-to-capital ratio as of December 30, 2006
was 40%, compared with 37% at December 30, 2005. The 2006 ratio reflects the
adoption of SFAS No. 158 Employers Accounting for Defined Benefit Pension and
Other Postretirement Plans An amendment of Financial Accounting Standards
Board (FASB) Statement Nos. 87, 88, 106, 132(R). Our Manufacturing group
targets a gross debt-to-capital ratio that is consistent with an A rated
company. Consistent with the methodology used by members of the financial
community, leverage of the Manufacturing group excludes the debt of our Finance
group. In turn, our Finance group limits its borrowings to an amount, taking
into account the risk profile of its assets, consistent with a single A credit
rating. Surplus capital of Textron Financial Corporation is returned to Textron
Inc.
Borrowings historically have been a secondary source
of funds for our Manufacturing group and, along with the collection of finance
receivables, are a primary source of funds for our Finance group. Both
borrowing groups utilize a broad base of financial sources for their respective
liquidity and capital needs. Our credit ratings are predominantly a function of
our ability to generate operating cash flows and satisfy certain financial
ratios. Since high-quality credit ratings provide us with access to a broad
base of global investors at an attractive cost, we target a long-term A rating
from the independent debt-rating agencies. The credit ratings and outlooks of
these three debt-rating agencies by borrowing group are as follows:
|
|
|
|
|
|
Standard &
|
|
|
|
Fitch
|
|
Moodys
|
|
Poors
|
|
Long-term ratings:
|
|
|
|
|
|
|
|
Manufacturing
|
|
A-
|
|
A3
|
|
A-
|
|
Finance
|
|
A-
|
|
A3
|
|
A-
|
|
Short-term
ratings:
|
|
|
|
|
|
|
|
Manufacturing
|
|
F2
|
|
P2
|
|
A2
|
|
Finance
|
|
F2
|
|
P2
|
|
A2
|
|
Outlook
|
|
Positive
|
|
Stable
|
|
Stable
|
|
We have a policy of maintaining unused committed bank
lines of credit in an amount not less than outstanding commercial paper
balances. These facilities are in support of commercial paper and letters of
credit issuances only, and neither of these primary lines of credit was drawn
at December 30, 2006 or December 31, 2005.
23
Our primary committed credit facilities at December
30, 2006 include the following:
|
|
|
|
|
|
|
|
Amount Not
|
|
|
|
|
|
|
|
|
|
Reserved as
|
|
|
|
|
|
|
|
|
|
Support for
|
|
|
|
|
|
Commercial
|
|
Letters of
|
|
Commercial
|
|
|
|
Facility
|
|
Paper
|
|
Credit
|
|
Paper and
|
|
(In millions)
|
|
Amount
|
|
Outstanding
|
|
Outstanding
|
|
Letters of Credit
|
|
Manufacturing
group - multi-year facility expiring in 2011*
|
|
$
|
1,250
|
|
$
|
|
|
$
|
23
|
|
$
|
1,227
|
|
Finance group -
multi-year facility expiring in 2011
|
|
$
|
1,750
|
|
$
|
1,719
|
|
$
|
13
|
|
$
|
18
|
|
* The Finance group is permitted to
borrow under this multi-year facility.
Under a shelf registration statement filed with the
Securities and Exchange Commission, the Manufacturing group may issue public
debt and other securities in one or more offerings up to a total maximum
offering of $2.0 billion. At December 30, 2006, we had $1.6 billion available
under the Manufacturing groups registration statement.
During the fourth quarter of 2006, the Finance group
renewed a previously filed statement to enable it to issue an unlimited amount
of public debt. Our Finance group issued $1.8 billion of term debt and CAD 100
million of term debt during 2006 under its registration statements. We used the
proceeds from these issuances to fund receivable growth and repay short-term
debt.
Contractual Obligations
Manufacturing Group
The following table summarizes the known contractual
obligations of our Manufacturing group to make future payments or other
consideration pursuant to certain contracts as of December 30, 2006, as well as
an estimate of the timing in which these obligations are expected to be
satisfied:
|
|
Payment Due by Period
|
|
|
|
Less than
|
|
|
|
|
|
|
|
|
|
More than
|
|
|
|
(In millions)
|
|
1 Year
|
|
2 Years
|
|
3 Years
|
|
4 Years
|
|
5 Years
|
|
5 Years
|
|
Total
|
|
Liabilities
reflected in balance sheet:
|
|
|
|
|
|
|
|
|
|
|
|
|
|
|
|
Long-term debt (a)
|
|
$
|
75
|
|
$
|
346
|
|
$
|
|
|
$
|
251
|
|
$
|
16
|
|
$
|
976
|
|
$
|
1,664
|
|
Capital lease obligations (a)
|
|
5
|
|
5
|
|
3
|
|
3
|
|
3
|
|
117
|
|
136
|
|
Pension benefits for unfunded plans (b)
|
|
13
|
|
15
|
|
16
|
|
16
|
|
15
|
|
173
|
|
248
|
|
Postretirement benefits other than pensions (b)
|
|
77
|
|
69
|
|
66
|
|
63
|
|
60
|
|
493
|
|
828
|
|
Other long-term liabilities (c)
|
|
138
|
|
75
|
|
46
|
|
33
|
|
30
|
|
300
|
|
622
|
|
Liabilities not
reflected in balance sheet:
|
|
|
|
|
|
|
|
|
|
|
|
|
|
|
|
Operating leases (a)
|
|
57
|
|
49
|
|
42
|
|
36
|
|
28
|
|
201
|
|
413
|
|
Purchase obligations (d)
|
|
1,980
|
|
378
|
|
118
|
|
36
|
|
15
|
|
22
|
|
2,549
|
|
Total Manufacturing
group
|
|
$
|
2,345
|
|
$
|
937
|
|
$
|
291
|
|
$
|
438
|
|
$
|
167
|
|
$
|
2,282
|
|
$
|
6,460
|
|
(a) Long-term debt and capital
lease obligations exclude interest payments. Operating leases represent
undiscounted obligations under noncancelable leases.
(b) We maintain defined benefit
pension plans and postretirement benefit plans other than pensions as discussed
in Note 12 to the consolidated financial statements. Included in the table
above are discounted estimated benefit payments we expect to make related to
unfunded pension and other postretirement benefit plans. Actual benefit
payments are dependent on a number of factors, including mortality assumptions,
expected retirement age, rate of compensation increases and medical trend
rates, which are subject to change in future years. We also expect to make
contributions to our funded pension plans in the range of approximately $45
million to $60 million per year over the next five years, which are not
reflected in this table.
(c) Other long-term liabilities
primarily include undiscounted amounts on the consolidated balance sheet as of
December 30, 2006 representing obligations under deferred compensation
arrangements and estimated environmental remediation costs. Payments under
deferred compensation arrangements have been estimated based on managements
assumptions of expected retirement age, mortality, stock price and rates of
return on participant deferrals. Timing of cash flows associated with
environmental remediation costs are largely based on historical experience.
Many of our other long-term liabilities have been excluded from the table due
to the uncertainty of the timing of payments combined with the absence of
historical trends to be used as a predictor for such payments. These excluded
liabilities primarily include deferred income taxes.
(d) Purchase obligations represent
undiscounted obligations for which we are committed to purchase goods and
services as of December 30, 2006. The ultimate liability for these obligations
may be reduced based upon termination provisions included in certain purchase
contracts, the costs incurred to date by vendors under these contracts or by
recourse under firm contracts with the U.S. Government under normal termination
clauses.
In January 2005, we contracted with a third-party
service provider for the oversight of our information technology
infrastructure, including maintenance, operational oversight and purchases of
hardware (the IT Contract). The IT Contract covers a 10-year period and is
subject to variable pricing and quantity provisions for both purchases of
computer hardware and system design modifications. We have retained the right
to approve significant design, equipment purchase and related decisions by the
service provider. We can terminate the IT Contract for convenience prior to
24
its full term and would consequently be subject to
variable termination fees that decline over time and do not exceed $59 million
at December 30, 2006.
Finance Group
The following table summarizes our Finance groups
known contractual obligations to make future payments. Due to the nature of
finance companies, we also have contractual cash receipts that will be received
in the future. We generally borrow funds at various contractual maturities to
match the maturities of our finance receivables. The contractual payments and
receipts as of December 30, 2006 are detailed below:
|
|
Payments/Receipts Due by Period
|
|
|
|
Less than
|
|
|
|
|
|
|
|
|
|
More than
|
|
|
|
(In millions)
|
|
1 Year
|
|
2 Years
|
|
3 Years
|
|
4 Years
|
|
5 Years
|
|
5 Years
|
|
Total
|
|
Contractual
payments:
|
|
|
|
|
|
|
|
|
|
|
|
|
|
|
|
Commercial paper and other short-term debt
|
|
$
|
1,779
|
|
$
|
|
|
$
|
|
|
$
|
|
|
$
|
|
|
$
|
|
|
$
|
1,779
|
|
Term debt
|
|
1,118
|
|
966
|
|
1,562
|
|
833
|
|
442
|
|
209
|
|
5,130
|
|
Operating leases
|
|
6
|
|
5
|
|
4
|
|
3
|
|
3
|
|
1
|
|
22
|
|
Total
contractual payments
|
|
2,903
|
|
971
|
|
1,566
|
|
836
|
|
445
|
|
210
|
|
6,931
|
|
Cash and
receipts:
|
|
|
|
|
|
|
|
|
|
|
|
|
|
|
|
Finance receivables
|
|
3,554
|
|
1,396
|
|
821
|
|
497
|
|
504
|
|
1,538
|
|
8,310
|
|
Operating leases
|
|
30
|
|
23
|
|
20
|
|
18
|
|
15
|
|
26
|
|
132
|
|
Total receipts
|
|
3,584
|
|
1,419
|
|
841
|
|
515
|
|
519
|
|
1,564
|
|
8,442
|
|
Cash
|
|
47
|
|
|
|
|
|
|
|
|
|
|
|
47
|
|
Total cash and
receipts
|
|
3,631
|
|
1,419
|
|
841
|
|
515
|
|
519
|
|
1,564
|
|
8,489
|
|
Net cash and
receipts (payments)
|
|
$
|
728
|
|
$
|
448
|
|
$
|
(725
|
)
|
$
|
(321
|
)
|
$
|
74
|
|
$
|
1,354
|
|
$
|
1,558
|
|
Cumulative net cash and
receipts
|
|
$
|
728
|
|
$
|
1,176
|
|
$
|
451
|
|
$
|
130
|
|
$
|
204
|
|
$
|
1,558
|
|
|
|
Finance receivable receipts related to finance leases
and term loans are based on contractual cash flows. Finance receivable receipts
related to revolving loans are based on historical cash flow experience. These
amounts could differ due to prepayments, charge-offs and other factors.
Receipts and contractual payments exclude finance charges from receivables,
debt interest payments, proceeds from sale of operating lease equipment and
other items.
As shown in the preceding table, our cash and
receipts are expected to be sufficient to cover maturing debt and other
contractual liabilities. At December 30, 2006, our Finance group had $2.9
billion in debt and $426 million in other liabilities that are payable within
the next 12 months.
At December 30, 2006, our Finance group had unused commitments
to fund new and existing customers under $1.3 billion of committed revolving
lines of credit, compared with $1.2 billion at December 31, 2005. These loan
commitments generally have an original duration of less than three years and do
not necessarily represent future cash requirements, since many of the
agreements will not be used to the extent committed or will expire unused. We
are not exposed to interest rate changes on these commitments since the
interest rates are not set until the loans are funded.
Off-Balance Sheet Arrangements and
Guarantees
We extend a variety of financial and performance
guarantees to third parties as provided in the table below:
|
|
December 30, 2006
|
|
December 31, 2005
|
|
|
|
Maximum
|
|
Carrying
|
|
Maximum
|
|
Carrying
|
|
|
|
Potential
|
|
Amount of
|
|
Potential
|
|
Amount of
|
|
(In millions)
|
|
Payment*
|
|
Liability
|
|
Payment*
|
|
Liability
|
|
Manufacturing
group:
|
|
|
|
|
|
|
|
|
|
Performance
guarantee
|
|
$
|
227
|
|
$
|
|
|
$
|
114
|
|
$
|
|
|
Guaranteed
minimum resale contracts
|
|
30
|
|
3
|
|
31
|
|
3
|
|
Guarantees
related to dispositions
|
|
46
|
|
23
|
|
29
|
|
8
|
|
Debt obligations
of joint ventures
|
|
4
|
|
|
|
10
|
|
|
|
Finance
group:
|
|
|
|
|
|
|
|
|
|
Loss-sharing agreements
|
|
$
|
29
|
|
$
|
|
|
$
|
71
|
|
$
|
13
|
|
* These
agreements include uncapped guarantees as described below.
25
Performance Guarantee
In 2004, through our Bell Helicopter business, we
formed AgustaWestlandBell LLC (AWB LLC) with AgustaWestland North America
Inc. (AWNA). This venture was created for the joint design, development,
manufacture, sale, customer training and product support of the VH-71
helicopter, and certain variations and derivatives thereof, to be offered and
sold to departments or agencies of the U.S. Government. In March 2005, AWB LLC
received a $1.2 billion cost reimbursement-type subcontract from Lockheed
Martin for the System Development and Demonstration phase of the U.S. Marine
Corps Helicopter Squadron Program. We guaranteed to Lockheed Martin the due and
prompt performance by AWB LLC of all its obligations under this subcontract,
provided that our liability under the guaranty shall not exceed 49% of AWB LLCs
aggregate liability to Lockheed Martin under the subcontract. AgustaWestland
N.V., AWNAs parent company, has guaranteed the remaining 51% to Lockheed
Martin. We have entered into cross-indemnification agreements with
AgustaWestland N.V. in which each party indemnifies the other related to any
payments required under these agreements that result from the indemnifying
partys workshare under any subcontracts received.
For 2006, AWB LLCs maximum obligation was 40% of the
total contract value, which equates to $464 million based on the current
contract value of $1.2 billion. In 2007 and thereafter, AWB LLCs maximum
obligation increases to 50%, or $580 million. Accordingly, the maximum amount
of our liability under the guarantee was $227 million at December 30, 2006 and
will be $284 million thereafter through completion.
Guaranteed Minimum Resale Contracts
We have a number of guaranteed minimum resale value
contracts associated with certain past aircraft sales. If the fair value of an
aircraft falls below a minimum guaranteed amount, we may be required to make a
future payment to the customer or provide a minimum trade-in value toward a new
aircraft. These agreements generally include operating restrictions such as
maximum usage over the contract period or minimum maintenance requirements. We
also have guaranteed the minimum resale value of certain customer-owned
aircraft anticipated to be traded in upon completion of a model currently under
development. These contracts expire as follows: $2 million in 2008, $3 million
in 2009, $3 million in 2010, $3 million in 2011 and $19 million in 2012.
Guarantees Related to Dispositions
We have guaranteed payment on certain credit
facilities and bank-issued letters of credit and guarantees of the Fastening
Systems business, where the total guarantee is capped at approximately $9
million, for which the buyer has provided a letter of credit of approximately
$4 million as collateral. We also have guaranteed payment and performance on
certain other credit facilities and leases of the Fastening Systems business
totaling approximately $14 million, where we also are liable for unpaid
interest, fees and other costs associated with claims that may arise from these
guarantees. While potential interest and fees are not capped, we have
monitoring provisions that mitigate the exposure to these additional costs. The
buyer has provided a letter of credit of approximately $9 million as collateral
on these guarantees.
We also have indemnified the purchaser of the
Fastening Systems business for remediation costs related to pre-existing
environmental conditions to the extent they exist at the sold locations. We
have estimated the fair value of these indemnifications at approximately $12
million. Potential payments under these obligations are not capped, and as a
result the maximum potential obligation cannot be determined.
In connection with the disposition of Trim to
subsidiaries of C&A, certain equipment and operating leases were
transferred and assigned to subsidiaries of C&A. We guaranteed C&As
payments under these leases and for an environmental matter.
We also have obligations arising from sales of
certain other businesses, including representations and warranties and related
indemnities for environmental, health and safety, and tax and employment
matters. The maximum potential payment related to these obligations is not a
specified amount as a number of the obligations do not contain financial caps.
Loss-Sharing Agreements
In connection with the sale of a note receivable in
2005, our Finance group has indemnified the purchaser against potential losses
in limited circumstances. The maximum potential exposure of the indemnity is
estimated to be $29 million, but due to the extremely low probability of
occurrence and several other mitigating factors, including a specific
indemnification from the original note issuer, no significant fair value has
been attributed to the indemnity.
In connection with the sale of the Small Business
Direct financing business in 2003, our Finance group entered into a
loss-sharing agreement. This agreement required us to reimburse the purchaser
for 50% of losses incurred on the portfolio above a 4% annual level. A
liability of $14 million was originally recorded representing the estimated
fair value of the guarantee. During the fourth quarter of 2006, we entered into
a settlement agreement with the purchaser, which terminated our obligation to
reimburse the purchaser for future losses. The settlement resulted in a $1
million loss, net of tax, from discontinued operations in 2006.
At December 31, 2005, our Finance group had a
contingent liability related to the sale of equipment lease streams with a
maximum liability of $42 million. These lease streams were sold in 2006, and we
had no remaining liability at the end of 2006.
26
Software Indemnifications
With the acquisition of Overwatch Systems in 2006, we
now are a party to software license agreements with customers. These software
license agreements generally include certain provisions for indemnifying
customers against liabilities if our software products infringe a third partys
intellectual property rights. To date, we have not incurred any material costs
as a result of such indemnifications and have not accrued any liabilities
related to such obligations in our consolidated financial statements.
Forward Contract
We enter into a forward contract in our common stock
on an annual basis. The contract is intended to hedge the earnings and cash
volatility of stock-based incentive compensation indexed to our stock. The
forward contract requires annual cash settlement between the counterparties
based upon a number of shares multiplied by the difference between the strike
price and the prevailing common stock price. As of December 30, 2006, the
contract was for approximately 1.5 million shares with a strike price of
$77.62. The market price of the stock was $93.77 at December 30, 2006,
resulting in a receivable of $24 million, compared with a receivable of $10 million
at December 31, 2005.
Finance Receivable Securitizations
and Sales
We sell finance receivables utilizing both
securitizations and whole-loan sales. As a result of these transactions,
finance receivables are removed from the balance sheet, and the proceeds
received are used to reduce the recorded debt levels. Despite the reduction in
the recorded balance sheet position, we generally retain a subordinated
interest in the finance receivables sold through securitizations, which may
affect operating results through periodic fair value adjustments. These
retained interests are more fully discussed in the Securitizations section of
Note 5 to the consolidated financial statements. We utilize these off-balance
sheet financing arrangements (primarily asset-backed securitizations) to
further diversify funding alternatives. These arrangements provided net
proceeds from operations of $50 million and $361 million in 2006 and 2005,
respectively. Proceeds from securitizations include amounts received related to
incremental increases in the level of distribution finance receivables sold and
exclude amounts received related to the ongoing replenishment of the
outstanding sold balance of these short-duration receivables. We have used the
proceeds from these arrangements to fund the origination of new finance
receivables and to retire commercial paper.
Whole-loan finance receivable sales in which we
maintain a continuing interest differ from securitizations as loans are sold
directly to investors and no portion of the sale proceeds is deferred. Limited
credit enhancement occasionally is provided for these transactions in the form
of a contingent liability related to finance receivable credit losses and, to a
lesser extent, prepayment risk. At December 30, 2006, we had no remaining
contingent liabilities related to credit losses or prepayment risk associated
with whole-loan sales. Termination of our off-balance sheet financing
arrangements would reduce our short-term funding alternatives. While these
arrangements do not contain provisions that require us to repurchase
significant amounts of receivables previously sold, there are risks that could
reduce the availability of these funding alternatives in the future. Potential
barriers to the continued use of these arrangements include deterioration in
finance receivable portfolio quality, downgrades in our Finance groups debt
credit ratings and a reduction of new finance receivable originations in the
businesses that utilize these funding arrangements. We do not expect any of
these factors to have a material impact on our liquidity or income from
operations.
Critical Accounting Policies
To prepare our consolidated financial statements to
be in conformity with generally accepted accounting principles, we must make
complex and subjective judgments in the selection and application of accounting
policies. The accounting policies that we believe are most critical to the
portrayal of our financial condition and results of operations are listed
below. We believe these policies require our most difficult, subjective and
complex judgments in estimating the effect of inherent uncertainties. This
section should be read in conjunction with Note 1 to the consolidated financial
statements, which includes other significant accounting policies.
Allowance for Losses on Finance
Receivables
Our allowance for losses on finance receivables is
intended to provide for losses inherent in the portfolio, which requires the
application of estimates and significant judgment as to the ultimate outcome of
collection efforts and realization of collateral values, among other factors.
Therefore, changes in economic conditions or credit metrics, including past due
and nonperforming accounts, or other events affecting specific obligors or
industries may require additions or reductions to our reserves.
We evaluate the collectibility of our finance
receivables based on a combination of factors. For homogeneous loan pools, we
examine current delinquencies, characteristics of the existing accounts,
historical loss experience, underlying collateral value, and general economic
conditions and trends. We estimate losses will range from 0.3% to 6.0% of
finance receivables depending on the specific homogeneous loan pool. For larger
balance commercial loans, we also consider borrower specific information,
industry trends and estimated discounted cash flows. Our process involves the
use of estimates and a high degree of management judgment. While we believe
that our consideration of the factors and assumptions
27
referred to above results in an accurate evaluation
of existing losses in the portfolio based on prior trends and experience,
changes in the assumptions or trends within reasonable historical volatility
may have a material impact on our allowance for losses. The allowance for losses
on finance receivables currently represents 1.1% of total finance receivables.
During the last five years, net charge-offs as a percentage of finance
receivables have ranged from 0.38% to 2.08%.
Long-Term Contracts
We make a substantial portion of our sales to
government customers pursuant to long-term contracts. These contracts require
development and delivery of products over multiple years and may contain
fixed-price purchase options for additional products. We accounted for these
long-term contracts under the percentage-of-completion method of accounting.
Under the percentage-of-completion method, we
estimate profit as the difference between total estimated revenue and total
estimated cost of a contract and recognize that profit over the contract term
based on either input (e.g., costs incurred under the cost-to-cost method,
which typically is used for development effort) or output (e.g., units
delivered under the units-of-delivery method, which is used for production
effort), as appropriate under the circumstances. The percentage-of-completion
method of accounting involves the use of various estimating techniques to
project costs at completion and, in some cases includes estimates of recoveries
asserted against the customer for changes in specifications. Due to the size,
length of time and nature of many of our contracts, the estimation of total
contract costs and revenue through completion is complicated and subject to
many variables relative to the outcome of future events over a period of several
years. We are required to make numerous assumptions and estimates relating to
items such as expected engineering requirements, complexity of design and
related development costs, performance of subcontractors, availability and cost
of materials, labor productivity and cost, overhead and capital costs,
manufacturing efficiencies and the achievement of contract milestones,
including product deliveries.
Our cost estimation process is based on the
professional knowledge and experience of engineers and program managers along
with finance professionals. We update our projections of costs at least
semiannually or when circumstances significantly change. Adjustments to
projected costs are recognized in earnings when determinable. Anticipated
losses on contracts are recognized in full in the period in which losses become
probable and estimable. Due to the significance of judgment in the estimation
process described above, it is likely that materially different revenues and/or
cost of sales amounts could be recorded if we used different assumptions or if
the underlying circumstances were to change. Our earnings could be reduced by a
material amount resulting in a charge to earnings if (a) total estimated
contract costs are significantly higher than expected due to changes in
customer specifications prior to contract amendment, (b) total estimated
contract costs are significantly higher than previously estimated due to cost
overruns or inflation, (c) there is a change in engineering efforts required
during the development stage of the contract or (d) we are unable to meet
contract milestones.
Goodwill
We evaluate the recoverability of goodwill annually
in the fourth quarter or more frequently if events or changes in circumstances,
such as declines in sales, earnings or cash flows, or material adverse changes
in the business climate, indicate that the carrying value of an asset might be
impaired. We completed our annual impairment test in the fourth quarter of 2006
using the estimates from our long-term strategic plans. No adjustment was
required to the carrying value of our goodwill based on the analysis performed.
Goodwill is considered to be impaired when the net
book value of a reporting unit exceeds its estimated fair value. Fair values
are primarily established using a discounted cash flow methodology using
assumptions consistent with market participants. The determination of
discounted cash flows is based on the businesses strategic plans and
long-range planning forecasts. The revenue growth rates included in the forecasts
represent our best estimates based on current and forecasted market conditions,
and the profit margin assumptions are projected by each reporting unit based on
the current cost structure and anticipated net cost reductions. If different
assumptions were used in these forecasts, the related undiscounted cash flows
used in measuring impairment could be different, potentially resulting in an
impairment charge.
The impact of reducing our fair value estimates by
10% would have no impact on our goodwill assessment, with the exception of two
reporting units as described below. Assuming a 10% reduction in our fair value
estimates, the carrying value of these reporting units would approximate or
exceed fair value.
Our operating plans and projections anticipate
investments in capital expenditures at our Fluid Handling Products reporting
unit to resolve current capacity issues as well as to capture additional
business in the oil and gas markets over the next two years. The related volume
increases are anticipated to result in approximately 25% annual operating
profit growth over this period. In the remaining five-year planning period, we
anticipate an annual operating profit growth rate of approximately 7%, driven
by anticipated revenue growth of 4% annually with increased profit margins from
improvements resulting from ongoing transformation efforts. Should the revenue
growth rates over the next two years approximate
28
historical levels, the estimated fair value would be
reduced by up to approximately $50 million and may result in the carrying value
of the reporting unit exceeding its estimated fair value, potentially resulting
in an impairment charge. At December 30, 2006, the goodwill allocated to this
reporting unit totaled approximately $206 million.
Our operating plans and projections for the Golf and
Turf care reporting unit anticipate operating margin improvements over the
five-year planning period resulting in high single-digit margins, with
anticipated annual revenue growth of approximately 4%. A 100-basis-point
decline in our operating margin assumptions would reduce the estimated fair
value by up to approximately $60 million and may result in the carrying value
of the reporting unit exceeding its estimated fair value, potentially resulting
in an impairment charge. At December 30, 2006, the goodwill allocated to this
reporting unit totaled approximately $141 million.
Retirement Benefits
We maintain various pension and postretirement plans
for our employees globally. These plans include significant pension and
postretirement benefit obligations, which are calculated based on actuarial
valuations. Key assumptions used in determining these obligations and related
expenses include expected long-term rates of return on plan assets, discount
rates and healthcare cost projections. We evaluate and update these assumptions
annually in consultation with third-party actuaries and investment advisors. We
also make assumptions regarding employee demographic factors such as retirement
patterns, mortality, turnover and the rate of compensation increases.
To determine the expected long-term rate of return on
plan assets, we consider the current and expected asset allocation, as well as
historical and expected returns on each plan asset class. A lower expected rate
of return on plan assets will increase pension expense. For 2006, the assumed
expected long-term rate of return on plan assets used in calculating pension
expense was 8.54%, compared with 8.57% in 2005. In 2006 and 2005, the assumed
rate of return for our qualified domestic plans, which represent approximately
82% of our total pension obligations, was 8.75%. A 50-basis-point decrease in
this long-term rate of return would result in a $20 million annual increase in
pension expense for our qualified domestic plans.
The discount rate enables us to state expected future
benefit payments as a present value on the measurement date, reflecting the
current rate at which the pension liabilities could be effectively settled.
This rate should be in line with rates for high-quality fixed income
investments available for the period to maturity of the pension benefits, which
fluctuate as long-term interest rates change. A lower discount rate increases
the present value of the benefit obligations and increases pension expense. In
2006, we lowered the weighted-average discount rate used in calculating pension
expense to 5.55% from 5.69% in 2005. For our qualified domestic plans, the
assumed discount rate was 5.65% for 2006. A 50-basis-point decrease in this
discount rate would result in a $29 million annual increase in pension expense
for our qualified domestic plans.
The trend in healthcare costs is difficult to
estimate, and it has an important effect on postretirement liabilities. The
2006 medical and prescription drug healthcare cost trend rates represent the
weighted-average annual projected rate of increase in the per capita cost of
covered benefits. The 2006 medical rate of 8% is assumed to decrease to 5% by
2009 and then remain at that level. The 2006 prescription drug rate of 12% is
assumed to decrease to 5% by 2013 and then remain at that level. See Note 12 to
the consolidated financial statements for the impact of a one-percentage-point
change in the cost trend rate.
Income Taxes
Deferred tax assets and liabilities are determined
based on temporary differences between the financial reporting and tax bases of
assets and liabilities, applying enacted tax rates that we expect to be in
effect for the year in which we expect the differences will reverse. Based on
the evaluation of available evidence, we recognize future tax benefits, such as
net operating loss carryforwards, to the extent that we believe it is more
likely than not that we will realize these benefits. We periodically assess the
likelihood that we will be able to recover our deferred tax assets and reflect
any changes in our estimates in the valuation allowance, with a corresponding
adjustment to earnings or other comprehensive income (loss), as appropriate.
In assessing the need for a valuation allowance, we
look to the future reversal of existing taxable temporary differences, taxable
income in carryback years, the feasibility of tax planning strategies and
estimated future taxable income. The valuation allowance can be affected by
changes to tax laws, changes to statutory tax rates and changes to future
taxable income estimates.
The amount of income taxes we pay is subject to
ongoing audits by federal, state and foreign tax authorities, which may result
in proposed assessments. Our estimate for the potential outcome for any
uncertain tax issue is highly judgmental. We believe we have adequately
provided for any reasonably foreseeable outcome related to these matters.
However, our future results may include favorable or unfavorable adjustments to
our estimated tax liabilities due to closure of income tax examinations, new
regulatory or judicial pronouncements, or other relevant events. As a result,
our effective tax rate may fluctuate significantly on a quarterly basis.
29
Recently Announced Accounting
Pronouncements
In July 2006, the FASB issued Interpretation No. 48, Accounting
for Uncertainty in Income Taxes An interpretation of FASB Statement No. 109
(FIN 48). This Interpretation provides a comprehensive model for the
financial statement recognition, measurement, presentation and disclosure of
uncertain tax positions taken or expected to be taken in income tax returns. We
will adopt this Interpretation in the first quarter of 2007 and do not expect
the adoption to have a material impact on our financial position or results of
operations.
In July 2006, the FASB issued FASB Staff Position FAS
13-2, Accounting for a Change or Projected Change in the Timing of Cash Flows
Relating to Income Taxes Generated by a Leveraged Lease Transaction. This
Staff Position amends SFAS No. 13, Accounting for Leases and requires a
recalculation of returns on leveraged leases if there is a change or projected
change in the timing of cash flows related to income taxes generated by the
leveraged lease. In accordance with this guidance, the difference between the
revised calculation of earnings since lease inception and the actual amount of
cumulative earnings recognized is recorded in income from continuing
operations. We are required to adopt this guidance in the first quarter of
2007. Upon adoption, the estimated change in the projected cash flows must be
reported as an adjustment to retained earnings. The adoption of this Staff
Position resulted in a $33 million reduction in retained earnings at the
beginning of fiscal 2007.
In September 2006, the FASB issued SFAS No. 157, Fair
Value Measurements. This Statement replaces multiple existing definitions of
fair value with a single definition, establishes a consistent framework for
measuring fair value and expands financial statement disclosures regarding fair
value measurements. This Statement applies only to fair value measurements that
already are required or permitted by other accounting standards and does not
require any new fair value measurements. SFAS No. 157 is effective for fiscal years
beginning subsequent to November 15, 2007. We will adopt this Statement in the
first quarter of 2008 and currently are evaluating its impact on our financial
position and results of operations.
Item 7A. Quantitative and Qualitative Disclosures
about Market Risk
Interest Rate Risks
Our financial results are affected by changes in U.S.
and foreign interest rates. As part of managing this risk, we enter into
interest rate exchange agreements to convert certain floating-rate debt to
fixed-rate debt and vice versa. The overall objective of our interest rate risk
management is to achieve a prudent balance between floating- and fixed-rate
debt. We continually monitor our mix of floating- and fixed-rate debt and
adjust the mix, as necessary, based on our evaluation of internal and external
factors. The difference between the rates our Manufacturing group received and
the rates it paid on interest rate exchange agreements did not significantly
impact interest expense in 2006, 2005 or 2004.
Our Finance group limits its risk to changes in
interest rates with its strategy of matching floating-rate assets with
floating-rate liabilities. This strategy includes the use of interest rate
exchange agreements. At December 30, 2006, floating-rate liabilities in excess
of floating-rate assets were $431 million, net of $2.9 billion of interest rate
exchange agreements that effectively converted fixed-rate debt to a
floating-rate equivalent, and $46 million of interest rate exchange agreements
that effectively converted fixed-rate finance receivables to a floating-rate
equivalent. Interest rate exchange agreements designated as hedges of debt had
the net effect of increasing interest expense for our Finance group by $27
million in 2006 and decreasing interest expense by $11 million and $40 million
in 2005 and 2004, respectively.
Foreign Exchange Risks
Our financial results are affected by changes in
foreign currency exchange rates and economic conditions in the foreign markets
in which products are manufactured and/or sold. For 2006, the impact of foreign
exchange rate changes from 2005 increased revenues by approximately $11 million
(0.1%) and increased segment profit by approximately $2 million (0.2%).
For our manufacturing operations, we manage exposures
to foreign currency assets and earnings primarily by funding certain foreign
currency denominated assets with liabilities in the same currency so that
certain exposures are naturally offset. We primarily use borrowings denominated
in euro and British pound sterling for these purposes.
In managing its foreign currency transaction
exposures, we also enter into foreign currency forward exchange and option
contracts. These contracts generally are used to fix the local currency cost of
purchased goods or services or selling prices denominated in currencies other
than the functional currency. The notional amount of outstanding foreign
exchange contracts, foreign currency options and currency swaps was
approximately $765 million at the end of 2006 and $699 million at the end of
2005.
30
Quantitative Risk Measures
In the normal course of business, we enter into
financial instruments for purposes other than trading. To quantify the market
risk inherent in our financial instruments, we utilize a sensitivity analysis.
The financial instruments that are subject to market risk (interest rate risk,
foreign exchange rate risk and equity price risk) include finance receivables
(excluding lease receivables), debt (excluding lease obligations), interest
rate exchange agreements, foreign currency exchange contracts and marketable
security price forward contracts.
Presented below is a sensitivity analysis of the fair
value of financial instruments outstanding at year-end. We estimate the fair
value of the financial instruments using discounted cash flow analysis and
independent investment bankers. This sensitivity analysis is most likely not
indicative of actual results in the future. The following table illustrates the
sensitivity to a hypothetical change in the fair value of the financial
instruments assuming a 10% decrease in interest rates, a 10% strengthening in
exchange rates against the U.S. dollar and a 10% decrease in the quoted market
price of the marketable equity security.
|
|
2006
|
|
2005
|
|
|
|
|
|
|
|
Sensitivity of
|
|
|
|
|
|
Sensitivity of
|
|
|
|
|
|
|
|
Fair Value
|
|
|
|
|
|
Fair Value
|
|
|
|
Carrying
|
|
Fair
|
|
to a 10%
|
|
Carrying
|
|
Fair
|
|
to a 10%
|
|
(In millions)
|
|
Value*
|
|
Value*
|
|
Change
|
|
Value*
|
|
Value*
|
|
Change
|
|
Interest
rate risk
|
|
|
|
|
|
|
|
|
|
|
|
|
|
Manufacturing
group:
|
|
|
|
|
|
|
|
|
|
|
|
|
|
Debt
|
|
$
|
(1,800
|
)
|
$
|
(1,833
|
)
|
$
|
(36
|
)
|
$
|
(1,934
|
)
|
$
|
(2,012
|
)
|
$
|
(36
|
)
|
Interest rate exchanges
|
|
(8
|
)
|
(8
|
)
|
2
|
|
(10
|
)
|
(10
|
)
|
3
|
|
Finance group:
|
|
|
|
|
|
|
|
|
|
|
|
|
|
Finance receivables
|
|
7,019
|
|
6,982
|
|
27
|
|
5,589
|
|
5,515
|
|
32
|
|
Interest rate exchanges receivables
|
|
1
|
|
1
|
|
1
|
|
8
|
|
8
|
|
3
|
|
Debt
|
|
(6,862
|
)
|
(6,868
|
)
|
(82
|
)
|
(5,420
|
)
|
(5,423
|
)
|
(92
|
)
|
Interest rate exchanges debt
|
|
(52
|
)
|
(52
|
)
|
31
|
|
(47
|
)
|
(47
|
)
|
32
|
|
Foreign
exchange rate risk
|
|
|
|
|
|
|
|
|
|
|
|
|
|
Manufacturing
group:
|
|
|
|
|
|
|
|
|
|
|
|
|
|
Debt
|
|
(741
|
)
|
(756
|
)
|
(76
|
)
|
(932
|
)
|
(974
|
)
|
(97
|
)
|
Foreign currency exchange contracts
|
|
12
|
|
12
|
|
58
|
|
23
|
|
23
|
|
56
|
|
Equity
price risk
|
|
|
|
|
|
|
|
|
|
|
|
|
|
Manufacturing
group:
|
|
|
|
|
|
|
|
|
|
|
|
|
|
Marketable
security price forward contracts
|
|
24
|
|
24
|
|
(14
|
)
|
10
|
|
10
|
|
(13
|
)
|
|
|
|
|
|
|
|
|
|
|
|
|
|
|
|
|
|
|
|
|
* The value represents an asset or
(liability).
Forward-Looking
Information
Certain statements in this Annual Report on Form 10-K
and other oral and written statements made by Textron from time to time are
forward-looking statements, including those that discuss strategies, goals,
outlook or other non-historical matters; or project revenues, income, returns
or other financial measures. These forward-looking statements speak only as of
the date on which they are made, and we undertake no obligation to update or
revise any forward-looking statements. These forward-looking statements are
subject to risks and uncertainties that may cause actual results to differ
materially from those contained in the statements, including the following: [a]
changes in worldwide economic and political conditions that impact demand for
our products, interest rates and foreign exchange rates; [b] the interruption
of production at Textron facilities or Textrons customers or suppliers; [c]
Textrons ability to perform as anticipated and to control costs under
contracts with the U.S. Government; [d] the U.S. Governments ability to unilaterally
modify or terminate its contracts with Textron for the U.S. Governments
convenience or for Textrons failure to perform, to change applicable
procurement and accounting policies, and, under certain circumstances, to
suspend or debar Textron as a contractor eligible to receive future contract
awards; [e] changes in national or international funding priorities and
government policies on the export and import of military and commercial
products; [f] the ability to control costs and successful implementation of
various cost-reduction programs; [g] the timing of new product launches and
certifications of new aircraft products; [h] the occurrence of slowdowns or
downturns in customer markets in which Textron products are sold or supplied or
where Textron Financial Corporation offers financing; [i] changes in aircraft
31
delivery schedules or cancellation of orders; [j] the
impact of changes in tax legislation; [k] the extent to which Textron is able
to pass raw material price increases through to customers or offset such price
increases by reducing other costs; [l] Textrons ability to offset, through
cost reductions, pricing pressure brought by original equipment manufacturer
customers; [m] Textrons ability to realize full value of receivables; [n] the availability
and cost of insurance; [o] increases in pension expenses and other
postretirement employee costs; [p] Textron Financial Corporations ability to
maintain portfolio credit quality; [q] Textron Financial Corporations access
to debt financing at competitive rates; [r] uncertainty in estimating
contingent liabilities and establishing reserves to address such contingencies;
[s] performance of acquisitions; [t] the efficacy of research and development
investments to develop new products; [u] the launching of significant new
products or programs which could result in unanticipated expenses; and [v]
bankruptcy or other financial problems at major suppliers or customers that
could cause disruptions in Textrons supply chain or difficulty in collecting amounts
owed by such customers.
Further information on risks and uncertainties that
may impact forward-looking statements is discussed under Risk Factors on
pages 6 through 8 of this Annual Report on Form 10-K.
Item 8. Financial Statements and Supplementary Data
Our consolidated financial statements and the related
reports of our independent registered public accounting firm thereon are
included in this Annual Report on Form 10-K on the pages indicated below.
All other schedules are omitted either because they
are not applicable or not required or because the required information is
included in the financial statements or notes thereto.
32
Report of Management
Management is responsible for the integrity and
objectivity of the financial data presented in this Annual Report on Form 10-K.
The consolidated financial statements have been prepared in conformity with
accounting principles generally accepted in the United States and include
amounts based on managements best estimates and judgments. Management also is
responsible for establishing and maintaining adequate internal control over
financial reporting for Textron Inc. as such term is defined in Exchange Act
Rules 13a-15(f). With the participation of our management, we conducted an
evaluation of the effectiveness of our internal control over financial
reporting based on the framework in Internal Control Integrated Framework
issued by the Committee of Sponsoring Organizations of the Treadway Commission.
Based on our evaluation under the framework in Internal Control Integrated
Framework, we have concluded that Textron Inc. maintained, in all material
respects, effective internal control over financial reporting as of December
30, 2006.
The independent registered public accounting firm,
Ernst & Young LLP, has audited the consolidated financial statements of
Textron Inc. and has issued an attestation report on our assessment of the
effectiveness of Textrons internal control over financial reporting as of
December 30, 2006, as stated in its reports, which are included herein.
We conduct our business in accordance with the
standards outlined in the Textron Business Conduct Guidelines, which are
communicated to all employees. Honesty, integrity and high ethical standards
are the core values of how we conduct business. Every Textron business prepares
and carries out an annual Compliance Plan to ensure these values and standards
are maintained. Our internal control structure is designed to provide
reasonable assurance, at appropriate cost, that assets are safeguarded and that
transactions are properly executed and recorded. The internal control structure
includes, among other things, established policies and procedures, an internal
audit function, and the selection and training of qualified personnel. Textrons
management is responsible for implementing effective internal control systems
and monitoring their effectiveness, as well as developing and executing an
annual internal control plan.
The Audit Committee of our Board of Directors, on
behalf of the shareholders, oversees managements financial reporting
responsibilities. The Audit Committee, composed of four directors who are not
officers or employees of Textron, meets regularly with the independent
auditors, management and our internal auditors to review matters relating to financial
reporting, internal accounting controls and auditing. Both the independent
auditors and the internal auditors have free and full access to senior
management and the Audit Committee.
/s/ Lewis B. Campbell
|
|
/s/ Ted R. French
|
Lewis B. Campbell
|
|
Ted R. French
|
Chairman,
President and Chief
|
|
Executive Vice President and
|
Executive
Officer
|
|
Chief Financial
Officer
|
February 14, 2007
33
Report of Independent Registered Public Accounting
Firm on Internal Control over Financial Reporting
To the Board of Directors and
Shareholders of Textron Inc.
We have audited managements assessment, included in
the accompanying Report of Management, that Textron Inc. maintained effective
internal control over financial reporting as of December 30, 2006, based on
criteria established in Internal Control Integrated Framework issued by the
Committee of Sponsoring Organizations of the Treadway Commission (the COSO
criteria). Textron Inc.s management is responsible for maintaining effective
internal control over financial reporting and for its assessment of the
effectiveness of internal control over financial reporting. Our responsibility
is to express an opinion on managements assessment and an opinion on the
effectiveness of Textron Inc.s internal control over financial reporting based
on our audit.
We conducted our audit in accordance with the
standards of the Public Company Accounting Oversight Board (United States).
Those standards require that we plan and perform the audit to obtain reasonable
assurance about whether effective internal control over financial reporting was
maintained in all material respects. Our audit included obtaining an
understanding of internal control over financial reporting, evaluating
managements assessment, testing and evaluating the design and operating
effectiveness of internal control, and performing such other procedures as we
considered necessary in the circumstances. We believe that our audit provides a
reasonable basis for our opinion.
A companys internal control over financial reporting
is a process designed to provide reasonable assurance regarding the reliability
of financial reporting and the preparation of financial statements for external
purposes in accordance with generally accepted accounting principles. A companys
internal control over financial reporting includes those policies and
procedures that (1) pertain to the maintenance of records that, in reasonable
detail, accurately and fairly reflect the transactions and dispositions of the
assets of the company; (2) provide reasonable assurance that transactions are
recorded as necessary to permit preparation of financial statements in
accordance with generally accepted accounting principles, and that receipts and
expenditures of the company are being made only in accordance with
authorizations of management and directors of the company; and (3) provide
reasonable assurance regarding prevention or timely detection of unauthorized
acquisition, use, or disposition of the companys assets that could have a
material effect on the financial statements.
Because of its inherent limitations, internal control
over financial reporting may not prevent or detect misstatements. Also,
projections of any evaluation of effectiveness to future periods are subject to
the risk that controls may become inadequate because of changes in conditions,
or that the degree of compliance with the policies or procedures may
deteriorate.
In our opinion, managements assessment that Textron
Inc. maintained effective internal control over financial reporting as of
December 30, 2006, is fairly stated, in all material respects, based on the
COSO criteria. Also, in our opinion, Textron Inc. maintained, in all material
respects, effective internal control over financial reporting as of December
30, 2006, based on the COSO criteria.
We also have audited, in accordance with the
standards of the Public Company Accounting Oversight Board (United States), the
consolidated balance sheets of Textron Inc. as of December 30, 2006 and
December 31, 2005, and the related consolidated statements of operations, cash
flows and changes in shareholders equity for each of the three years in the
period ended December 30, 2006 of Textron Inc. and our report dated February
14, 2007 expressed an unqualified opinion thereon.
/s/ Ernst & Young LLP
|
|
Boston, Massachusetts
|
|
February 14,
2007
|
|
34
Report of Independent Registered Public Accounting Firm
on the Consolidated Financial Statements and Schedule
To the Board of Directors and
Shareholders of Textron Inc.
We have audited the accompanying consolidated balance
sheets of Textron Inc. as of December 30, 2006 and December 31, 2005, and the
related consolidated statements of operations, cash flows and changes in
shareholders equity for each of the three years in the period ended December
30, 2006. Our audits also included the financial statement schedule contained
on page 76. These financial statements and schedule are the responsibility of
Textron Inc.s management. Our responsibility is to express an opinion on these
financial statements based on our audits.
We conducted our audits in accordance with the
standards of the Public Company Accounting Oversight Board (United States).
Those standards require that we plan and perform the audit to obtain reasonable
assurance about whether the financial statements are free of material
misstatement. An audit includes examining, on a test basis, evidence supporting
the amounts and disclosures in the financial statements. An audit also includes
assessing the accounting principles used and significant estimates made by
management, as well as evaluating the overall financial statement presentation.
We believe that our audits provide a reasonable basis for our opinion.
In our opinion, the consolidated financial statements
referred to above present fairly, in all material respects, the consolidated
financial position of Textron Inc. at December 30, 2006 and December 31, 2005
and the consolidated results of its operations and its cash flows for each of
the three years in the period ended December 30, 2006, in conformity with U.S.
generally accepted accounting principles. Also, in our opinion, the related
financial statement schedule, when considered in relation to the basic
financial statements taken as a whole, presents fairly in all material respects
the information set forth therein.
We also have audited, in accordance with the
standards of the Public Company Accounting Oversight Board (United States), the
effectiveness of Textron Inc.s internal control over financial reporting as of
December 30, 2006, based on criteria established in Internal Control
Integrated Framework issued by the Committee of Sponsoring Organizations of
the Treadway Commission and our report dated February 14, 2007 expressed an
unqualified opinion thereon.
As discussed in Note 12 to the consolidated financial
statements, in 2006 Textron Inc. adopted Statement of Financial Accounting
Standards (SFAS) No. 158, Employers Accounting for Defined Benefit Pension
and Other Postretirement Plans - An amendment of FASB Statement Nos. 87, 88,
106, and 132(R), and as discussed in Note 11 to the consolidated financial
statements, in 2005 Textron Inc. adopted SFAS No. 123 (Revised 2004), Share-Based
Payment.
/s/ Ernst & Young LLP
|
|
Boston, Massachusetts
|
|
February 14,
2007
|
|
35
Consolidated Statements of Operations
For each of the years in the three-year period ended
December 30, 2006
(In millions, except per share amounts)
|
|
2006
|
|
2005
|
|
2004
|
|
Revenues
|
|
|
|
|
|
|
|
Manufacturing
revenues
|
|
$
|
10,692
|
|
$
|
9,415
|
|
$
|
7,773
|
|
Finance revenues
|
|
798
|
|
628
|
|
545
|
|
Total revenues
|
|
11,490
|
|
10,043
|
|
8,318
|
|
Costs,
expenses and other
|
|
|
|
|
|
|
|
Cost of sales
|
|
8,528
|
|
7,464
|
|
6,206
|
|
Selling and
administrative
|
|
1,523
|
|
1,403
|
|
1,209
|
|
Interest
expense, net
|
|
438
|
|
290
|
|
246
|
|
Provision for
losses on finance receivables
|
|
26
|
|
29
|
|
58
|
|
Special charges
|
|
|
|
118
|
|
59
|
|
Total costs, expenses and other
|
|
10,515
|
|
9,304
|
|
7,778
|
|
Income from
continuing operations before income taxes
|
|
975
|
|
739
|
|
540
|
|
Income taxes
|
|
(269
|
)
|
(223
|
)
|
(165
|
)
|
Income
from continuing operations
|
|
706
|
|
516
|
|
375
|
|
Loss from
discontinued operations, net of income taxes
|
|
(105
|
)
|
(313
|
)
|
(10
|
)
|
Net
income
|
|
$
|
601
|
|
$
|
203
|
|
$
|
365
|
|
Per
common share:
|
|
|
|
|
|
|
|
Basic:
|
|
|
|
|
|
|
|
Income from continuing operations
|
|
$
|
5.53
|
|
$
|
3.86
|
|
$
|
2.73
|
|
Loss from discontinued operations, net of income
taxes
|
|
(0.82
|
)
|
(2.34
|
)
|
(0.07
|
)
|
Net income
|
|
$
|
4.71
|
|
$
|
1.52
|
|
$
|
2.66
|
|
Diluted:
|
|
|
|
|
|
|
|
Income from continuing operations
|
|
$
|
5.43
|
|
$
|
3.78
|
|
$
|
2.68
|
|
Loss from discontinued operations, net of income
taxes
|
|
(0.81
|
)
|
(2.29
|
)
|
(0.07
|
)
|
Net
income
|
|
$
|
4.62
|
|
$
|
1.49
|
|
$
|
2.61
|
|
See Notes to the consolidated
financial statements.
36
Consolidated Balance Sheets
As of December 30, 2006 and December 31, 2005
(Dollars in millions, except share data)
|
|
2006
|
|
2005
|
|
Assets
|
|
|
|
|
|
Manufacturing
group
|
|
|
|
|
|
Cash and cash
equivalents
|
|
$
|
733
|
|
$
|
786
|
|
Accounts
receivable, net
|
|
964
|
|
891
|
|
Inventories
|
|
2,069
|
|
1,712
|
|
Other current
assets
|
|
448
|
|
464
|
|
Assets of
discontinued operations
|
|
73
|
|
1,122
|
|
Total current assets
|
|
4,287
|
|
4,975
|
|
Property, plant
and equipment, net
|
|
1,773
|
|
1,574
|
|
Goodwill
|
|
1,257
|
|
979
|
|
Other assets
|
|
1,233
|
|
1,530
|
|
Total Manufacturing group assets
|
|
8,550
|
|
9,058
|
|
Finance
group
|
|
|
|
|
|
Cash
|
|
47
|
|
10
|
|
Finance
receivables, net
|
|
8,217
|
|
6,667
|
|
Goodwill
|
|
169
|
|
169
|
|
Other assets
|
|
567
|
|
595
|
|
Total Finance group assets
|
|
9,000
|
|
7,441
|
|
Total assets
|
|
$
|
17,550
|
|
$
|
16,499
|
|
Liabilities
and shareholders equity
|
|
|
|
|
|
Liabilities
|
|
|
|
|
|
Manufacturing
group
|
|
|
|
|
|
Current portion
of long-term debt and short-term debt
|
|
$
|
80
|
|
$
|
275
|
|
Accounts payable
|
|
814
|
|
677
|
|
Accrued
liabilities
|
|
1,958
|
|
1,749
|
|
Liabilities of
discontinued operations
|
|
142
|
|
446
|
|
Total current liabilities
|
|
2,994
|
|
3,147
|
|
Other
liabilities
|
|
2,329
|
|
2,026
|
|
Long-term debt
|
|
1,720
|
|
1,659
|
|
Total Manufacturing group liabilities
|
|
7,043
|
|
6,832
|
|
Finance
group
|
|
|
|
|
|
Other
liabilities
|
|
499
|
|
510
|
|
Deferred income
taxes
|
|
497
|
|
461
|
|
Debt
|
|
6,862
|
|
5,420
|
|
Total Finance group liabilities
|
|
7,858
|
|
6,391
|
|
Total liabilities
|
|
14,901
|
|
13,223
|
|
Shareholders
equity
|
|
|
|
|
|
Capital stock:
|
|
|
|
|
|
Preferred stock:
|
|
|
|
|
|
$2.08 Cumulative Convertible Preferred Stock, Series
A (liquidation value $11)
|
|
4
|
|
4
|
|
$1.40 Convertible Preferred Dividend Stock, Series B
(preferred only as to dividends)
|
|
6
|
|
6
|
|
Common stock (208,983,713 and 205,613,104 shares
issued and 125,595,770 and 130,184,723 outstanding)
|
|
26
|
|
26
|
|
Capital surplus
|
|
1,786
|
|
1,533
|
|
Retained
earnings
|
|
6,211
|
|
5,808
|
|
Accumulated
other comprehensive loss
|
|
(644
|
)
|
(78
|
)
|
|
|
7,389
|
|
7,299
|
|
Less cost of
treasury shares
|
|
4,740
|
|
4,023
|
|
Total
shareholders equity
|
|
2,649
|
|
3,276
|
|
Total liabilities and
shareholders equity
|
|
$
|
17,550
|
|
$
|
16,499
|
|
See Notes to the consolidated
financial statements.
37
Consolidated Statements of Changes in Shareholders
Equity
For each of the years in the three-year period ended December 30, 2006
|
|
Shares Outstanding*
|
|
Dollars
|
|
|
|
(In thousands)
|
|
(In millions)
|
|
|
|
2006
|
|
2005
|
|
2004
|
|
2006
|
|
2005
|
|
2004
|
|
$2.08 Preferred stock
|
|
|
|
|
|
|
|
|
|
|
|
|
|
Beginning balance
|
|
84
|
|
105
|
|
112
|
|
$
|
4
|
|
$
|
4
|
|
$
|
4
|
|
Conversion to common
stock
|
|
(6
|
)
|
(21
|
)
|
(7
|
)
|
|
|
|
|
|
|
Ending balance
|
|
78
|
|
84
|
|
105
|
|
$
|
4
|
|
$
|
4
|
|
$
|
4
|
|
$1.40 Preferred stock
|
|
|
|
|
|
|
|
|
|
|
|
|
|
Beginning balance
|
|
47
|
|
50
|
|
52
|
|
$
|
6
|
|
$
|
6
|
|
$
|
6
|
|
Conversion to common
stock
|
|
(6
|
)
|
(3
|
)
|
(2
|
)
|
|
|
|
|
|
|
Ending balance
|
|
41
|
|
47
|
|
50
|
|
$
|
6
|
|
$
|
6
|
|
$
|
6
|
|
Common stock
|
|
|
|
|
|
|
|
|
|
|
|
|
|
Beginning balance
|
|
130,185
|
|
135,373
|
|
137,238
|
|
$
|
26
|
|
$
|
25
|
|
$
|
25
|
|
Purchases
|
|
(8,574
|
)
|
(8,035
|
)
|
(6,534
|
)
|
|
|
|
|
|
|
Exercise of stock
options
|
|
3,317
|
|
2,149
|
|
4,351
|
|
|
|
1
|
|
|
|
Conversion of preferred
stock to common stock
|
|
51
|
|
101
|
|
41
|
|
|
|
|
|
|
|
Other issuances of
common stock
|
|
617
|
|
597
|
|
277
|
|
|
|
|
|
|
|
Ending balance
|
|
125,596
|
|
130,185
|
|
135,373
|
|
$
|
26
|
|
$
|
26
|
|
$
|
25
|
|
Capital surplus
|
|
|
|
|
|
|
|
|
|
|
|
|
|
Beginning balance
|
|
|
|
|
|
|
|
$
|
1,533
|
|
$
|
1,369
|
|
$
|
1,148
|
|
Conversion of preferred
stock to common stock
|
|
|
|
|
|
|
|
|
|
1
|
|
|
|
Exercise of stock
options and stock-based compensation
|
|
|
|
|
|
|
|
253
|
|
163
|
|
221
|
|
Ending balance
|
|
|
|
|
|
|
|
$
|
1,786
|
|
$
|
1,533
|
|
$
|
1,369
|
|
Retained earnings
|
|
|
|
|
|
|
|
|
|
|
|
|
|
Beginning balance
|
|
|
|
|
|
|
|
$
|
5,808
|
|
$
|
5,792
|
|
$
|
5,606
|
|
Net income
|
|
|
|
|
|
|
|
601
|
|
203
|
|
365
|
|
Dividends declared
($1.55, $1.40 and $1.33 per share, respectively)
|
|
|
|
|
|
|
|
(198
|
)
|
(187
|
)
|
(179
|
)
|
Ending balance
|
|
|
|
|
|
|
|
$
|
6,211
|
|
$
|
5,808
|
|
$
|
5,792
|
|
Treasury stock
|
|
|
|
|
|
|
|
|
|
|
|
|
|
Beginning balance
|
|
|
|
|
|
|
|
$
|
4,023
|
|
$
|
3,447
|
|
$
|
3,035
|
|
Purchases of common
stock
|
|
|
|
|
|
|
|
750
|
|
606
|
|
425
|
|
Issuance of common stock
|
|
|
|
|
|
|
|
(33
|
)
|
(30
|
)
|
(13
|
)
|
Ending balance
|
|
|
|
|
|
|
|
$
|
4,740
|
|
$
|
4,023
|
|
$
|
3,447
|
|
Accumulated other comprehensive
loss
|
|
|
|
|
|
|
|
|
|
|
|
|
|
Beginning balance
|
|
|
|
|
|
|
|
$
|
(78
|
)
|
$
|
(97
|
)
|
$
|
(64
|
)
|
Currency translation
adjustment
|
|
|
|
|
|
|
|
(2
|
)
|
(17
|
)
|
97
|
|
Deferred (losses) gains
on hedge contracts
|
|
|
|
|
|
|
|
(14
|
)
|
2
|
|
4
|
|
Unrealized losses on
securities
|
|
|
|
|
|
|
|
|
|
|
|
(3
|
)
|
Pension and postretirement
benefit adjustments
|
|
|
|
|
|
|
|
(550
|
)
|
34
|
|
(131
|
)
|
Other comprehensive
(loss) income and adjustments
|
|
|
|
|
|
|
|
(566
|
)
|
19
|
|
(33
|
)
|
Ending balance
|
|
|
|
|
|
|
|
$
|
(644
|
)
|
$
|
(78
|
)
|
$
|
(97
|
)
|
Comprehensive income
|
|
|
|
|
|
|
|
|
|
|
|
|
|
Net income
|
|
|
|
|
|
|
|
$
|
601
|
|
$
|
203
|
|
$
|
365
|
|
Other comprehensive
(loss) income
|
|
|
|
|
|
|
|
81
|
|
19
|
|
(33
|
)
|
Comprehensive income
|
|
|
|
|
|
|
|
$
|
682
|
|
$
|
222
|
|
$
|
332
|
|
* Shares issued at the end of 2006, 2005 and 2004 were as
follows (In thousands): $2.08 Preferred 147, 153 and 174 shares,
respectively; $1.40 Preferred 527, 534 and 537 shares, respectively; Common
208,984, 205,613 and 203,361 shares, respectively.
See Notes to the consolidated financial statements.
38
Consolidated Statements of Cash Flows
For each of the years in the three-year period ended December 30, 2006
|
|
Consolidated
|
|
(In millions)
|
|
2006
|
|
2005
|
|
2004
|
|
Cash
flows from operating activities:
|
|
|
|
|
|
|
|
Net income
|
|
$
|
601
|
|
$
|
203
|
|
$
|
365
|
|
Loss from
discontinued operations
|
|
105
|
|
313
|
|
10
|
|
Income from
continuing operations
|
|
706
|
|
516
|
|
375
|
|
Adjustments to
reconcile income from continuing operations to net cash provided by operating
activities:
|
|
|
|
|
|
|
|
Earnings of Finance group, net of distributions
|
|
|
|
|
|
|
|
Depreciation and amortization
|
|
290
|
|
303
|
|
280
|
|
Provision for losses on finance receivables
|
|
26
|
|
29
|
|
58
|
|
Special charges
|
|
|
|
118
|
|
59
|
|
Share-based compensation
|
|
30
|
|
28
|
|
8
|
|
Deferred income taxes
|
|
37
|
|
17
|
|
29
|
|
Changes in assets and liabilities excluding those
related to acquisitions and divestitures:
|
|
|
|
|
|
|
|
Accounts receivable, net
|
|
(14
|
)
|
(87
|
)
|
(3
|
)
|
Inventories
|
|
(427
|
)
|
(188
|
)
|
(201
|
)
|
Other assets
|
|
107
|
|
26
|
|
25
|
|
Accounts payable
|
|
115
|
|
173
|
|
(8
|
)
|
Accrued and other liabilities
|
|
401
|
|
77
|
|
414
|
|
Captive finance receivables, net
|
|
(324
|
)
|
(100
|
)
|
(105
|
)
|
Other operating activities, net
|
|
70
|
|
40
|
|
18
|
|
Net cash provided by operating activities of
continuing operations
|
|
1,017
|
|
952
|
|
949
|
|
Net cash (used in) provided by operating activities
of discontinued operations
|
|
(48
|
)
|
84
|
|
1
|
|
Net cash provided by operating activities
|
|
969
|
|
1,036
|
|
950
|
|
Cash
flows from investing activities:
|
|
|
|
|
|
|
|
Finance
receivables:
|
|
|
|
|
|
|
|
Originated or purchased
|
|
(11,225
|
)
|
(10,116
|
)
|
(9,725
|
)
|
Repaid
|
|
9,534
|
|
8,982
|
|
8,762
|
|
Proceeds on receivables sales and securitization
sales
|
|
493
|
|
237
|
|
264
|
|
Net cash used in
acquisitions
|
|
(502
|
)
|
(28
|
)
|
(5
|
)
|
Net proceeds
from sale of businesses
|
|
8
|
|
(1
|
)
|
3
|
|
Capital
expenditures
|
|
(431
|
)
|
(365
|
)
|
(250
|
)
|
Proceeds on sale
of property, plant and equipment
|
|
7
|
|
6
|
|
16
|
|
Proceeds on sale
of investments
|
|
|
|
|
|
38
|
|
Other investing
activities, net
|
|
54
|
|
62
|
|
97
|
|
Net cash used in
investing activities of continuing operations
|
|
(2,062
|
)
|
(1,223
|
)
|
(800
|
)
|
Net cash
provided by (used in) investing activities of discontinued operations
|
|
653
|
|
28
|
|
(18
|
)
|
Net cash used in
investing activities
|
|
(1,409
|
)
|
(1,195
|
)
|
(818
|
)
|
Cash flows
from financing activities:
|
|
|
|
|
|
|
|
Increase
(decrease) in short-term debt
|
|
337
|
|
171
|
|
788
|
|
Proceeds from
issuance of long-term debt
|
|
2,000
|
|
1,957
|
|
963
|
|
Principal
payments and retirements of long-term debt and mandatorily redeemable preferred
securities
|
|
(1,137
|
)
|
(1,178
|
)
|
(1,664
|
)
|
Proceeds from
employee stock ownership plans
|
|
173
|
|
106
|
|
187
|
|
Purchases of
Textron common stock
|
|
(761
|
)
|
(597
|
)
|
(415
|
)
|
Dividends paid
|
|
(244
|
)
|
(189
|
)
|
(135
|
)
|
Dividends paid
to Manufacturing group
|
|
|
|
|
|
|
|
Capital
contributions paid to Finance group
|
|
|
|
|
|
|
|
Excess tax
benefit received on share-based payments
|
|
31
|
|
14
|
|
|
|
Net cash
provided by (used in) financing activities of continuing operations
|
|
399
|
|
284
|
|
(276
|
)
|
Net cash
provided by (used in) financing activities of discontinued operations
|
|
2
|
|
(1
|
)
|
|
|
Net cash
provided by (used in) financing activities
|
|
401
|
|
283
|
|
(276
|
)
|
Effect of
exchange rate changes on cash and cash equivalents
|
|
23
|
|
(25
|
)
|
33
|
|
Net
(decrease) increase in cash and cash equivalents
|
|
(16
|
)
|
99
|
|
(111
|
)
|
Cash and cash
equivalents at beginning of year
|
|
796
|
|
697
|
|
808
|
|
Cash and cash
equivalents at end of year
|
|
$
|
780
|
|
$
|
796
|
|
$
|
697
|
|
Supplemental
schedule of non-cash investing and financing activities from continuing
operations:
|
|
|
|
|
|
|
|
Capital expenditures
financed through capital leases
|
|
$
|
16
|
|
$
|
15
|
|
$
|
44
|
|
See Notes to the consolidated
financial statements.
39
|
|
Manufacturing Group*
|
|
Finance Group*
|
|
(In millions)
|
|
2006
|
|
2005
|
|
2004
|
|
2006
|
|
2005
|
|
2004
|
|
Cash
flows from operating activities:
|
|
|
|
|
|
|
|
|
|
|
|
|
|
Net income
|
|
$
|
601
|
|
$
|
203
|
|
$
|
365
|
|
$
|
152
|
|
$
|
111
|
|
$
|
94
|
|
Loss from
discontinued operations
|
|
105
|
|
313
|
|
10
|
|
1
|
|
3
|
|
|
|
Income from
continuing operations
|
|
706
|
|
516
|
|
375
|
|
153
|
|
114
|
|
94
|
|
Adjustments to
reconcile income from continuing operations to net cash provided by operating
activities:
|
|
|
|
|
|
|
|
|
|
|
|
|
|
Earnings of Finance group, net of distributions
|
|
(73
|
)
|
(14
|
)
|
(23
|
)
|
|
|
|
|
|
|
Depreciation and amortization
|
|
251
|
|
257
|
|
234
|
|
39
|
|
46
|
|
46
|
|
Provision for losses on finance receivables
|
|
|
|
|
|
|
|
26
|
|
29
|
|
58
|
|
Special charges
|
|
|
|
118
|
|
59
|
|
|
|
|
|
|
|
Share-based compensation
|
|
30
|
|
28
|
|
8
|
|
|
|
|
|
|
|
Deferred income taxes
|
|
(1
|
)
|
10
|
|
(40
|
)
|
38
|
|
7
|
|
69
|
|
Changes in assets and liabilities excluding those
related to acquisitions and divestitures:
|
|
|
|
|
|
|
|
|
|
|
|
|
|
Accounts receivable, net
|
|
(14
|
)
|
(87
|
)
|
(3
|
)
|
|
|
|
|
|
|
Inventories
|
|
(379
|
)
|
(181
|
)
|
(171
|
)
|
|
|
|
|
|
|
Other assets
|
|
87
|
|
(6
|
)
|
2
|
|
8
|
|
14
|
|
2
|
|
Accounts payable
|
|
115
|
|
173
|
|
(8
|
)
|
|
|
|
|
|
|
Accrued and other liabilities
|
|
335
|
|
42
|
|
524
|
|
66
|
|
35
|
|
(110
|
)
|
Captive finance receivables, net
|
|
|
|
|
|
|
|
|
|
|
|
|
|
Other operating activities, net
|
|
62
|
|
38
|
|
16
|
|
8
|
|
2
|
|
2
|
|
Net cash provided by operating activities of
continuing operations
|
|
1,119
|
|
894
|
|
973
|
|
338
|
|
247
|
|
161
|
|
Net cash (used in) provided by operating activities
of discontinued operations
|
|
(35
|
)
|
87
|
|
1
|
|
(13
|
)
|
(3
|
)
|
|
|
Net cash provided by operating activities
|
|
1,084
|
|
981
|
|
974
|
|
325
|
|
244
|
|
161
|
|
Cash
flows from investing activities:
|
|
|
|
|
|
|
|
|
|
|
|
|
|
Finance
receivables:
|
|
|
|
|
|
|
|
|
|
|
|
|
|
Originated or purchased
|
|
|
|
|
|
|
|
(12,240
|
)
|
(10,940
|
)
|
(10,617
|
)
|
Repaid
|
|
|
|
|
|
|
|
10,205
|
|
9,560
|
|
9,359
|
|
Proceeds on receivables sales and securitization
sales
|
|
|
|
|
|
|
|
513
|
|
383
|
|
394
|
|
Net cash used in
acquisitions
|
|
(338
|
)
|
(28
|
)
|
(5
|
)
|
(164
|
)
|
|
|
|
|
Net proceeds
from sale of businesses
|
|
8
|
|
(1
|
)
|
3
|
|
|
|
|
|
|
|
Capital
expenditures
|
|
(419
|
)
|
(356
|
)
|
(238
|
)
|
(12
|
)
|
(9
|
)
|
(12
|
)
|
Proceeds on sale
of property, plant and equipment
|
|
7
|
|
23
|
|
38
|
|
|
|
|
|
|
|
Proceeds on sale
of investments
|
|
|
|
|
|
38
|
|
|
|
|
|
|
|
Other investing
activities, net
|
|
|
|
|
|
6
|
|
18
|
|
56
|
|
120
|
|
Net cash used in
investing activities of continuing operations
|
|
(742
|
)
|
(362
|
)
|
(158
|
)
|
(1,680
|
)
|
(950
|
)
|
(756
|
)
|
Net cash
provided by (used in) investing activities of discontinued operations
|
|
653
|
|
28
|
|
(18
|
)
|
|
|
|
|
|
|
Net cash used in
investing activities
|
|
(89
|
)
|
(334
|
)
|
(176
|
)
|
(1,680
|
)
|
(950
|
)
|
(756
|
)
|
Cash flows
from financing activities:
|
|
|
|
|
|
|
|
|
|
|
|
|
|
Increase
(decrease) in short-term debt
|
|
(242
|
)
|
277
|
|
1
|
|
579
|
|
(106
|
)
|
787
|
|
Proceeds from
issuance of long-term debt
|
|
5
|
|
403
|
|
14
|
|
1,995
|
|
1,554
|
|
949
|
|
Principal
payments and retirements of long-term debt and mandatorily redeemable preferred
securities
|
|
(16
|
)
|
(417
|
)
|
(360
|
)
|
(1,121
|
)
|
(761
|
)
|
(1,304
|
)
|
Proceeds from
employee stock ownership plans
|
|
173
|
|
106
|
|
187
|
|
|
|
|
|
|
|
Purchases of
Textron common stock
|
|
(761
|
)
|
(597
|
)
|
(415
|
)
|
|
|
|
|
|
|
Dividends paid
|
|
(244
|
)
|
(189
|
)
|
(135
|
)
|
|
|
|
|
|
|
Dividends paid
to Manufacturing group
|
|
|
|
|
|
|
|
(80
|
)
|
(100
|
)
|
(71
|
)
|
Capital
contributions paid to Finance group
|
|
(18
|
)
|
|
|
|
|
18
|
|
|
|
|
|
Excess tax
benefit received on share-based payments
|
|
31
|
|
14
|
|
|
|
|
|
|
|
|
|
Net cash
provided by (used in) financing activities of continuing operations
|
|
(1,072
|
)
|
(403
|
)
|
(708
|
)
|
1,391
|
|
587
|
|
361
|
|
Net cash
provided by (used in) financing activities of discontinued operations
|
|
2
|
|
(1
|
)
|
|
|
|
|
|
|
|
|
Net cash
provided by (used in) financing activities
|
|
(1,070
|
)
|
(404
|
)
|
(708
|
)
|
1,391
|
|
587
|
|
361
|
|
Effect of
exchange rate changes on cash and cash equivalents
|
|
22
|
|
(27
|
)
|
29
|
|
1
|
|
2
|
|
4
|
|
Net
(decrease) increase in cash and cash equivalents
|
|
(53
|
)
|
216
|
|
119
|
|
37
|
|
(117
|
)
|
(230
|
)
|
Cash and cash
equivalents at beginning of year
|
|
786
|
|
570
|
|
451
|
|
10
|
|
127
|
|
357
|
|
Cash and cash
equivalents at end of year
|
|
$
|
733
|
|
$
|
786
|
|
$
|
570
|
|
$
|
47
|
|
$
|
10
|
|
$
|
127
|
|
Supplemental
schedule of non-cash investing and financing activities from continuing
operations:
|
|
|
|
|
|
|
|
|
|
|
|
|
|
Capital expenditures
financed through capital leases
|
|
$
|
16
|
|
$
|
15
|
|
$
|
44
|
|
$
|
|
|
$
|
|
|
$
|
|
|
* Textron is segregated into a
Manufacturing group and a Finance group as described in Note 1 to the
consolidated financial statements. The Finance groups pre-tax income in excess
of dividends paid is excluded from the Manufacturing groups cash flows. All
significant transactions between the borrowing groups have been eliminated from
the consolidated column.
See Notes to the consolidated financial statements.
40
Notes to the Consolidated Financial Statements
Note 1. Summary of Significant
Accounting Policies
Principles of Consolidation and
Financial Statement Presentation
Our consolidated financial statements include the
accounts of Textron Inc. and all of its majority-owned subsidiaries and
variable interest entities that are required to be consolidated. See Note 18
for the variable interest entities included within these consolidated financial
statements.
Our financings are conducted through two separate
borrowing groups. The Manufacturing group consists of Textron Inc.,
consolidated with the entities that operate in the Bell, Cessna and Industrial
segments, while the Finance group consists of the Finance segment, comprised of
Textron Financial Corporation and its subsidiaries. We designed this framework
to enhance our borrowing power by separating the Finance group. Our
Manufacturing group operations include the development, production and delivery
of tangible goods and services, while our Finance group provides financial
services. Due to the fundamental differences between each borrowing groups
activities, investors, rating agencies and analysts use different measures to
evaluate each groups performance. To support those evaluations, we present
balance sheet and cash flow information for each borrowing group within the
consolidated financial statements.
Through our Finance group, we provide diversified
commercial financing to third parties. In addition, this group finances retail
purchases and leases for new and used aircraft and equipment manufactured by our
Manufacturing group, otherwise known as captive financing. In the consolidated
statements of cash flows, cash received from customers or from securitizations
is reflected as operating activities when received. However, in the cash flow
information provided for the separate borrowing groups, cash flows related to
captive financing activities are reflected based on the operations of each
group. For example, when product is sold by our Manufacturing group to a
customer that is financed by the Finance group, the origination of the finance
receivable is recorded within investing activities as a cash outflow on our
Finance groups statement of cash flows. Meanwhile, the Manufacturing group
records the cash received from the Finance group on the customers behalf
within operating cash flows as a cash inflow on our Manufacturing groups
statement of cash flows. Although cash is transferred between the two borrowing
groups, there is no cash transaction reported in the consolidated cash flows at
the time of the original financing. These captive financing activities, along
with all significant intercompany transactions, are reclassified or eliminated
in consolidation.
Certain amounts have been reclassified to conform to
the current year presentation.
Use of Estimates
We prepare our financial statements in conformity
with generally accepted accounting principles, which require us to make
estimates and assumptions that affect the amounts reported in the financial
statements. Estimates are used in accounting for, among other items, long-term
contracts, inventory valuation, residual values of leased assets, allowance for
credit losses on receivables, the amount and timing of future cash flows
expected to be received on impaired loans, product liability, workers
compensation, actuarial assumptions for the pension and postretirement plans,
future cash flows associated with goodwill and long-lived asset valuations, and
environmental and warranty reserves. Our estimates are based on the facts and
circumstances available at the time estimates are made, historical experience,
risk of loss, general economic conditions and trends, and our assessments of
the probable future outcomes of these matters. Actual results could differ from
those estimates. Estimates and assumptions are reviewed periodically, and the
effects of changes, if any, are reflected in the statement of operations in the
period that they are determined.
Cash and Cash Equivalents
Cash and cash equivalents consist of cash and
short-term, highly liquid investments with original maturities of three months
or less.
Revenue Recognition
We generally recognize revenue from the sale of our
products that are not under long-term contracts upon delivery. For commercial
aircraft, delivery is upon completion of manufacturing, customer acceptance,
and the transfer of the risk and rewards of ownership. Service revenue is
recognized when the service is performed.
When a sale arrangement involves multiple elements,
such as sales of products that include customization and other services, we
evaluate the arrangement to determine whether there are separate items that are
required to be delivered under the arrangement that qualify to be recorded as
separate units of accounting. We then allocate the total fee from the
arrangement to each unit of accounting based on its relative fair value, taking
into consideration any performance, cancellation, termination or refund type
provisions. Fair value generally is established for each unit of accounting
using the sales price charged when the same or similar items are sold
separately. We recognize revenue when the recognition criteria for each unit of
accounting are met.
41
Leases Certain qualifying noncancelable aircraft and
other product lease contracts are accounted for as sales-type leases. Upon delivery,
we record the present value of all payments (net of executory costs and any
guaranteed residual values) under these leases as revenues, and the related
costs of the product are charged to cost of sales. For lease financing
transactions that do not qualify as sales-type leases, we record revenue as
earned over the lease period.
Aircraft sales in which we guarantee our customer a
minimum future resale value are viewed as leases in accordance with Emerging
Issues Task Force No. 95-1, Revenue Recognition on Sales with a Guaranteed
Minimum Resale Value. To determine whether the transaction should be
classified as an operating lease or as a sales-type lease, the minimum lease
payments generally represent the difference between a) the proceeds upon the
equipments initial transfer and b) the present value of the residual value
guarantee to the purchaser as of the first exercise date of the guarantee, less
proceeds from any residual value insurance obtained. To assess the market value
of the aircraft, we use industry publications as well as actual sales of used
aircraft. These market value assessments are adjusted based on available
information related to the individual aircraft and any physical condition
minimums required by the arrangement. Losses are recorded currently if the
projected market value of the aircraft at the exercise date is less than the
guaranteed amount.
Long-Term Contracts Revenues under long-term contracts are
accounted for under the percentage-of-completion method of accounting in accordance
with American Institute of Certified Public Accountants Statement of Position
No. 81-1, Accounting for Performance of Construction-Type and Certain
Production-Type Contracts. Under the percentage-of-completion method, we
estimate profit as the difference between total estimated revenue and total
estimated cost of a contract and recognize that profit over the contract term
based on either input (e.g., costs incurred under the cost-to-cost method which
is typically used for development effort) or output (e.g., units delivered
under the units-of-delivery method, which is used for production effort), as
appropriate under the circumstances. Revenues under fixed-price contracts
generally are recorded using the units-of-delivery method. However, certain fixed-price
contracts provide for periodic delivery after a lengthy period of time over
which significant costs are incurred or require a significant amount of
development effort in relation to total contract volume. Revenues under those
contracts and all cost-reimbursement-type contracts are recorded using the
cost-to-cost method.
Our long-term contract profits are based on estimates
of total contract cost and revenue utilizing current contract specifications,
expected engineering requirements and the achievement of contract milestones,
including product deliveries. Certain contracts are awarded with fixed-price
incentive fees which also are considered when estimating revenues and profit
rates. Contract costs typically are incurred over a period of several years,
and the estimation of these costs requires substantial judgment. We review and
revise these estimates periodically throughout the contract term. Revisions to
contract profits are recorded when the revisions to estimated revenues or costs
are made. Anticipated losses on contracts are recognized in full in the period
in which losses become probable and estimable.
Our Bell Helicopter business has a joint venture with
The Boeing Company (Boeing) to provide engineering, development and test
services related to the V-22 aircraft, as well as to produce the V-22 aircraft,
under a number of separate contracts with the U.S. Government (the V-22
Contracts). The V-22 Contracts include the development contract and various
production release contracts (i.e., lots) that may run concurrently with
multiple earlier lots still being produced as new lots are started. The
development contract and the first three production lots are under
cost-reimbursement-type contracts, while subsequent lots are under
fixed-price-type contracts. We account for the first three fixed-price
incentive contract lots using the cost-to-cost method, primarily as a result of
the significant engineering effort required over a lengthy period of time
during the initial development phase in relation to total contract volume. The
production releases on the first six production lots include separately
contracted modifications to meet additional requirements of the U.S. Governments
Blue Ribbon Panel. The development effort for new production releases was
considered substantially complete at the beginning of 2003 since a consistent
production specification had been met with these units incorporating many of
the required modifications on the production line. Accordingly, revenue is
recognized on the new production releases that began in 2003 using the
units-of-delivery method.
Our joint venture agreement with Boeing creates
contractual, rather than ownership, rights related to the V-22. Accordingly, we
do not account for this joint venture under the equity method of accounting. We
account for all of our rights and obligations under the specific requirements
of the V-22 Contracts allocated to us under the joint venture agreement.
Revenues and cost of sales reflect our performance under the V-22 Contracts. We
include all assets used in performance of the V-22 Contracts that we own,
including inventory and unpaid receivables, and all liabilities arising from
our obligations under the V-22 Contracts in the consolidated balance sheets.
Finance Revenues Finance revenues include interest on finance
receivables, direct loan origination costs and fees received. We recognize
interest using the interest method to provide a constant rate of return over
the terms of the receivables. Revenues on direct loan origination costs and
fees received are deferred and amortized to finance revenues over the
contractual lives of the respective receivables using the interest method. When
receivables are sold or prepaid, unamortized amounts are recognized in
revenues. We generally suspend the accrual of interest income for
42
accounts that are contractually delinquent by more
than three months. In addition, detailed reviews of loans may result in earlier
suspension. We resume the accrual of interest when the loan becomes
contractually current and recognize the suspended interest income at that time.
Cash payments on nonaccrual accounts, including finance charges, generally are
applied to reduce loan principal.
Losses on Finance Receivables
Provisions for losses on finance receivables are charged
to income in amounts sufficient to maintain the allowance at a level considered
adequate to cover losses in the existing receivable portfolio. We evaluate the
allowance by examining current delinquencies, characteristics of the existing
accounts, historical loss experience, underlying collateral value, and general
economic conditions and trends. In addition, for larger balance commercial
loans, we consider borrower specific information, industry trends and estimated
discounted cash flows. Finance receivables generally are written down to the
fair value (less estimated costs to sell) of the related collateral at the
earlier of the date when the collateral is repossessed or when no payment has
been received for six months. Finance receivables are charged off when they are
deemed to be uncollectible.
Loan Impairment
We periodically evaluate our finance receivables,
excluding homogeneous loan portfolios and finance leases, for impairment. A
loan is considered impaired when it is probable that we will be unable to
collect all amounts due according to the contractual terms of the loan
agreement. We also identify loans that are considered impaired due to the
significant modification of the original loan terms. These modified loans
reflect deferred principal payments, generally at market interest rates, and
continue to accrue finance charges since collection of principal and interest
is not doubtful. We measure impairment by comparing the fair value of a loan
with its carrying amount. Fair value is based on the present value of expected
future cash flows discounted at the loans effective interest rate, the loans
observable market price or, if the loan is collateral dependent, at the fair
value of the collateral, less selling costs. If the fair value of the loan is
less than its carrying amount, we establish a reserve based on this difference.
Securitized Transactions
Securitized transactions involve the sale of finance
receivables to qualified special purpose trusts. Through our Finance group, we
sell or securitize loans and leases and may retain an interest in the assets
sold in the form of servicing responsibilities and subordinated interests,
including interest-only securities, seller certificates and cash reserves.
These retained interests are subordinate to other investors interests in the
securitizations. A gain or loss on the sale of the loans or leases depends, in
part, on the previous carrying amount of the finance assets involved in the
transfer, allocated between the assets sold and the retained interests based on
their relative fair values at the date of transfer.
Retained interests are recorded at fair value in
other assets. We estimate the fair value based on the present value of future
expected cash flows using our best estimates of key assumptions: credit losses,
prepayment speeds, discount rates and forward interest rate yield curves
commensurate with the risks involved. Each quarter we review the fair values of
the retained interests using updated assumptions and compare such amounts with
the carrying value of the retained interests. When the carrying value exceeds
the fair value of the retained interests and the decline in fair value is
determined to be other than temporary, we write down the retained interest to
fair value with a corresponding charge to earnings. When a change in the fair
value of the retained interest is deemed temporary, any unrealized gains or
losses are included in shareholders equity as a component of accumulated other
comprehensive loss.
Investments
We classify our investments in marketable equity
securities as available for sale. We record these investments at fair value in
other assets with any unrealized gains and losses included in shareholders
equity as a component of accumulated other comprehensive loss, net of income
taxes. Investments in non-marketable equity securities are accounted for under
either the cost or equity method of accounting. For investments in joint
ventures for which we do not have control or are not the primary beneficiary,
but where we do have the ability to exercise significant influence over the
ventures operating and financial policies, we use the equity method.
We periodically review our investment securities for
impairment based on criterion that include the duration of the market value
decline, our ability to hold to recovery, information regarding the market and
industry trends for the investees business, the investees financial strength
and specific prospects, and investment analyst reports, if available. If a
decline in the fair value of an investment security is judged to be other than
temporary, we write down the cost basis to fair value with a corresponding
charge to earnings.
Inventories
Inventories are stated at the lower of cost or
estimated net realizable value. We value our inventories generally using the
first-in, first-out method (FIFO) or the last-in, first-out (LIFO) method
for certain qualifying inventories in the U.S. We determine costs for our
commercial helicopters on an average cost basis by model considering the expended
and estimated costs for the current production release. Costs on long-term
contracts represent costs incurred for production, allocable operating
overhead, advances to suppliers, and, in the case of contracts with the
43
U.S. Government, allocable research and development
and general and administrative expenses. Pursuant to contract provisions,
agencies of the U.S. Government have title to, or security interest in,
inventories related to such contracts as a result of advances, performance-based
payments and progress payments. Such advances and payments are reflected as an
offset against the related inventory balances. In accordance with industry
practice, our inventoried costs include amounts related to contracts with long
production cycles, a portion of which is not expected to be realized within one
year.
Customer deposits are recorded against inventory when
the right of offset exists. All other customer deposits are recorded in accrued
liabilities.
Property, Plant and Equipment
Property, plant and equipment are recorded at cost
and are depreciated primarily using the straight-line method. Land improvements
and buildings are depreciated primarily over estimated lives ranging from five
to 40 years, while machinery and equipment are depreciated primarily over three
to 15 years. We capitalize expenditures for improvements that increase asset
values and extend useful lives.
Long-Lived Assets
Long-lived assets, including intangible assets
subject to amortization, are reviewed for impairment whenever events or changes
in circumstances indicate that the carrying amount of the asset may not be
recoverable. If the carrying value of the asset held for use exceeds the sum of
the undiscounted expected future cash flows, the carrying value of the asset is
written down to fair value. Long-lived assets held for sale are stated at the
lower of cost or fair value less cost to sell. Fair value is determined using
pertinent market information, including appraisals or brokers estimates and/or
estimated future discounted cash flows.
Goodwill
We evaluate the recoverability of goodwill annually
or more frequently if events or changes in circumstances, such as declines in
sales, earnings or cash flows, or material adverse changes in the business
climate, indicate that the carrying value of a reporting unit might be
impaired. The reporting unit represents the operating segment unless discrete
financial information is prepared and reviewed by segment management for
businesses one level below that operating segment (a component), in which
case such component is the reporting unit. In certain instances, we have
aggregated components of an operating segment into a single reporting unit
based on similar economic characteristics. Goodwill is considered to be
potentially impaired when the net book value of a reporting unit exceeds its
estimated fair value. Fair values are established primarily using a discounted
cash flow methodology. The determination of discounted cash flows is based on
the businesses strategic plans and long-range planning forecasts. When
available, comparative market multiples are used to corroborate discounted cash
flow results.
Derivative Financial Instruments
We are exposed to market risk primarily from changes
in interest rates, currency exchange rates and securities pricing. To manage
the volatility relating to these exposures, we net these exposures on a
consolidated basis to take advantage of natural offsets. For the residual
portion, we enter into various derivative transactions pursuant to our policies
in areas such as counterparty exposure and hedging practices. All derivative
instruments are reported on the consolidated balance sheets at fair value.
Designation to support hedge accounting is performed on a specific exposure
basis. We record changes in fair value of financial instruments qualifying as
fair value hedges in income, offset, in part or in whole, by corresponding
changes in the fair value of the underlying exposures being hedged. Changes in
fair values of derivatives accounted for as cash flow hedges, to the extent
they are effective as hedges, are recorded in other comprehensive (loss)
income, net of deferred taxes. We report changes in fair value of derivatives
not qualifying as hedges in income. We do not hold or issue derivative financial
instruments for trading or speculative purposes.
Foreign currency denominated assets and liabilities
are translated into U.S. dollars with the adjustments from the currency rate
changes recorded in the cumulative translation adjustment account in shareholders
equity until the related foreign entity is sold or substantially liquidated. We
use foreign currency financing transactions, including currency swaps, to
effectively hedge long-term investments in foreign operations with the same
corresponding currency. Foreign currency gains and losses on the hedge of the
long-term investments are recorded in the cumulative translation adjustment
account with the offset recorded as an adjustment to the non-U.S. dollar
financing liability.
Fair Values of Financial Instruments
The fair value of our cash and cash equivalents,
accounts receivable, accounts payable, and variable-rate receivables and debt
approximates the carrying value of these financial instruments. We determine
the estimated fair values of other financial instruments, including debt,
equity and risk management instruments, using available market information and
valuation methodologies, primarily discounted cash flow analysis or independent
investment bankers.
44
Product and Environmental
Liabilities
We accrue product liability claims on the occurrence
method when a loss is probable and reasonably estimable based on historical
experience and the insurance coverage and deductibles in effect at the date of
the incident.
Liabilities for environmental matters are recorded on
a site-by-site basis when it is probable that an obligation has been incurred
and the cost can be reasonably estimated. Our environmental liabilities are
undiscounted and do not take into consideration possible future insurance
proceeds or significant amounts from claims against other third parties.
Research and Development Costs
Research and development costs that are either not
specifically covered by contracts or represent our share under cost-sharing
arrangements are charged to expense as incurred. Research and development costs
incurred under contracts with others are reported as cost of sales over the
period that revenue is recognized.
Income Taxes
Deferred tax assets and liabilities are determined
based on temporary differences between the financial reporting and tax bases of
assets and liabilities, applying enacted tax rates expected to be in effect for
the year in which the differences are expected to reverse. Based on the
evaluation of available evidence, we recognize future tax benefits, such as net
operating loss carryforwards, to the extent that we believe it is more likely
than not that we will realize these benefits. We periodically assess the
likelihood that we will be able to recover our deferred tax assets and reflect
any changes in our estimates in the valuation allowance, with a corresponding
adjustment to earnings or other comprehensive income (loss), as appropriate. In
assessing the need for a valuation allowance, we look to the future reversal of
existing taxable temporary differences, taxable income in carryback years, the
feasibility of tax planning strategies and estimated future taxable income.
Recently Announced Accounting
Pronouncements
In July 2006, the Financial Accounting Standards
Board (FASB) issued Interpretation No. 48, Accounting for Uncertainty in
Income Taxes An interpretation of FASB Statement No. 109 (FIN 48). This
Interpretation provides a comprehensive model for the financial statement
recognition, measurement, presentation and disclosure of uncertain tax
positions taken or expected to be taken in income tax returns. We will adopt
this Interpretation in the first quarter of 2007 and do not expect the adoption
to have a material impact on our financial position or results of operations.
In July 2006, the FASB issued FASB Staff Position FAS
13-2, Accounting for a Change or Projected Change in the Timing of Cash Flows
Relating to Income Taxes Generated by a Leveraged Lease Transaction. This
Staff Position amends Statement of Financial Accounting Standards (SFAS) No.
13, Accounting for Leases and requires a recalculation of returns on
leveraged leases if there is a change or projected change in the timing of cash
flows related to income taxes generated by the leveraged lease. In accordance
with this guidance, the difference between the revised calculation of earnings
since lease inception and the actual amount of cumulative earnings recognized
is recorded in income from continuing operations. We are required to adopt this
guidance in the first quarter of 2007. Upon adoption, the estimated change in
the projected cash flows must be reported as an adjustment to retained
earnings. The adoption of this Staff Position resulted in a $33 million
reduction in retained earnings at the beginning of fiscal 2007.
In September 2006, the FASB issued SFAS No. 157, Fair
Value Measurements. This Statement replaces multiple existing definitions of
fair value with a single definition, establishes a consistent framework for
measuring fair value and expands financial statement disclosures regarding fair
value measurements. This Statement applies only to fair value measurements that
already are required or permitted by other accounting standards and does not
require any new fair value measurements. SFAS No. 157 is effective for fiscal
years beginning subsequent to November 15, 2007. We will adopt this Statement
in the first quarter of 2008 and currently are evaluating its impact on our
financial position and results of operations.
45
Note 2. Discontinued Operations
Our consolidated financial statements and related
footnote disclosures reflect the sold businesses of Fastening Systems, InteSys,
OmniQuip and the Small Business Direct financing business as discontinued
operations, net of applicable income taxes, for all periods presented in
accordance with SFAS No. 144, Accounting for the Impairment or Disposal of
Long-Lived Assets.
We generally use a centralized approach to the cash
management and financing of our manufacturing operations and, accordingly, do
not allocate debt or interest expense to our discontinued businesses. Any debt
and related interest expense of a specific entity within a business is recorded
by the respective entity. General corporate overhead previously allocated to
the businesses for reporting purposes is excluded from amounts reported as
discontinued operations.
In August 2006, we completed the sale of our
Fastening Systems business to Platinum Equity, a private equity investment
firm, for approximately $613 million in cash and the assumption of $16 million
of net indebtedness and certain liabilities. There was no gain or loss recorded
upon completion of the sale. The purchase price is subject to final adjustment
based on the audited net asset value, net debt and cash balances at the closing
date. We currently are negotiating with Platinum Equity and expect to finalize
the purchase price in early 2007.
Prior to the consummation of the sale of the
Fastening Systems business, we recorded impairment and other charges of $120
million in 2006 and $387 million in 2005, which are described below.
In September 2005, our Board of Directors approved
managements recommendation to explore strategic alternatives for the Fastening
Systems business. Based on the approval of this recommendation and the
likelihood of execution, we determined that an impairment indicator existed for
both the Fastening Systems goodwill and its long-lived assets. In our
assessment of potential impairment of the goodwill, we estimated the fair value
of the business using independent third-party valuations. This fair value
amount then was compared with the carrying amount of the business. As the
carrying amount exceeded the fair value, we then measured the amount of
goodwill impairment loss. The excess of the fair value of the business over the
fair value amounts assigned to its assets and liabilities represents the
implied fair value of goodwill. The carrying amount of the goodwill exceeded
the implied fair value of that goodwill, resulting in an impairment loss of
$335 million, which was recorded in the third quarter of 2005.
In December 2005, our Board
of Directors authorized the divestiture of the Fastening Systems business, and
we recorded an after-tax charge of approximately $52 million, which included
$37 million related to previously deferred foreign currency translation losses
and $7 million in curtailment losses for employee retirement plans. After these
charges, we assessed the estimated fair value of the business and determined
that no further adjustment to the carrying value was required at that time. In
the second quarter of 2006, we recorded an additional $120 million after-tax
impairment charge to record the business at the estimated fair value less cost
to sell at that time based on offers received from potential purchasers.
In 2005, we recorded a net
$46 million gain on disposal primarily related to a tax benefit recorded upon
the sale of InteSys.
Operating results of these
discontinued businesses, primarily related to Fastening Systems, are as
follows:
(In millions)
|
|
2006
|
|
2005
|
|
2004
|
|
Revenue
|
|
$
|
1,101
|
|
$
|
1,936
|
|
$
|
1,994
|
|
(Loss) income
from discontinued operations before special charges
|
|
(94
|
)
|
(388
|
)
|
72
|
|
Special charges
|
|
|
|
(11
|
)
|
(91
|
)
|
Loss from
discontinued operations
|
|
(94
|
)
|
(399
|
)
|
(19
|
)
|
Income tax
(expense) benefit
|
|
(11
|
)
|
40
|
|
9
|
|
Operating loss
from discontinued operations, net of income taxes
|
|
(105
|
)
|
(359
|
)
|
(10
|
)
|
Gain on
disposal, net of income taxes
|
|
|
|
46
|
|
|
|
Loss from discontinued
operations, net of income taxes
|
|
$
|
(105
|
)
|
$
|
(313
|
)
|
$
|
(10
|
)
|
At December 30, 2006, assets
of discontinued operations included current assets of $69 million related to
the sale of the Fastening Systems business, and liabilities of discontinued
operations included current liabilities of $57 million, representing
liabilities retained upon the sale of the Fastening Systems business.
46
Note 3.
Business Acquisitions, Goodwill and Intangible Assets
Business
Acquisitions
In 2006, we acquired three
businesses for a total cost of $338 million in the Bell segment and $164
million in the Finance segment, all of which were paid for in cash. These
acquisitions include the following:
· Overwatch Systems (Overwatch), a developer
and provider of intelligence analysis software tools for the defense industry,
was acquired on December 1.
· Innovative Survivability Technologies, Inc., a
supplier of innovative defensive systems to military and homeland security
customers, was acquired on July 19.
· Electrolux Financial Corporations dealer
inventory finance business, which provides consumer appliance and electronics dealers
with wholesale inventory financing, was acquired on June 30.
The operating results of
these businesses have been included in the consolidated financial statements
since the date of each respective acquisition. Pro forma information has not
been included as the amounts are immaterial.
In connection with these
acquisitions, we recorded $259 million of goodwill in the Bell segment and $112
million of identifiable intangible assets. The intangible assets and the
weighted-average amortization periods are as follows: $37 million in unpatented
technology (nine years), $35 million in customer agreements (15 years), $17
million in trademarks (nine years) and $23 million in other intangible assets
(five to 10 years).
The purchase price for
Overwatch is subject to adjustment based on actual working capital, cash and
debt balances at the closing date. We have allocated the purchase price of this
business to the estimated fair value of the net tangible and intangible assets
acquired, with any excess recorded as goodwill. These estimates are preliminary
as of the end of 2006 as we are awaiting the completion of the identification
and valuation of intangible assets acquired. We expect these analyzes to be
completed during the first half of 2007, along with the finalization of the
purchase price.
CitationShares is our joint
venture with TAG Aviation USA, Inc. (TAG) to sell fractional share interests
in business jets and limited advance purchase jet charter. On June 30, 2004, we
acquired an additional 25% interest in CitationShares from TAG for cash and the
assumption of debt guarantees previously provided by TAG. As a result of this
transaction, we owned 75% of CitationShares and consolidated its financial
results prospectively as of June 30, 2004. In 2006 and 2005, our ownership
interest was 86% and 82% as a result of additional capital contributions of $11
million and $26 million, respectively.
Additional cash consideration
also may be payable to TAG based on CitationShares future operating results.
TAG has the right to sell its remaining interest to us in the years 2009
through 2011, and we have the right to purchase the remaining interest in 2010
or 2011 for an amount based on a multiple of earnings.
Goodwill
The changes in the carrying
amount of goodwill, by segment, are as follows:
(In millions)
|
|
Bell
|
|
Cessna
|
|
Industrial
|
|
Finance
|
|
Total
|
|
Balance at
January 3, 2004
|
|
$
|
101
|
|
$
|
306
|
|
$
|
593
|
|
$
|
169
|
|
$
|
1,169
|
|
Acquisitions/dispositions
|
|
|
|
16
|
|
(20
|
)
|
|
|
(4
|
)
|
Foreign currency
translation
|
|
|
|
|
|
20
|
|
|
|
20
|
|
Other
|
|
|
|
|
|
(14
|
)
|
|
|
(14
|
)
|
Balance at
January 1, 2005
|
|
$
|
101
|
|
$
|
322
|
|
$
|
579
|
|
$
|
169
|
|
$
|
1,171
|
|
Acquisitions
|
|
1
|
|
|
|
4
|
|
|
|
5
|
|
Foreign currency
translation
|
|
|
|
|
|
(22
|
)
|
|
|
(22
|
)
|
Other
|
|
|
|
|
|
(6
|
)
|
|
|
(6
|
)
|
Balance at
December 31, 2005
|
|
$
|
102
|
|
$
|
322
|
|
$
|
555
|
|
$
|
169
|
|
$
|
1,148
|
|
Acquisitions
|
|
259
|
|
|
|
|
|
|
|
259
|
|
Foreign currency
translation
|
|
|
|
|
|
21
|
|
|
|
21
|
|
Other
|
|
|
|
|
|
(2
|
)
|
|
|
(2
|
)
|
Balance at December 30,
2006
|
|
$
|
361
|
|
$
|
322
|
|
$
|
574
|
|
$
|
169
|
|
$
|
1,426
|
|
47
Intangible
Assets
All of our acquired
intangible assets are subject to amortization and are composed of the
following:
|
|
|
|
|
|
|
|
|
|
Weighted-
|
|
|
|
|
|
|
|
Average
|
|
December 30, 2006
|
|
December 31, 2005
|
|
|
|
Amortization
|
|
Gross
|
|
|
|
|
|
Gross
|
|
|
|
|
|
|
|
Period
|
|
Carrying
|
|
Accumulated
|
|
|
|
Carrying
|
|
Accumulated
|
|
|
|
(Dollars in millions)
|
|
(In years)
|
|
Amount
|
|
Amortization
|
|
Net
|
|
Amount
|
|
Amortization
|
|
Net
|
|
Trademarks
|
|
16
|
|
$
|
46
|
|
$
|
8
|
|
$
|
38
|
|
$
|
29
|
|
$
|
7
|
|
$
|
22
|
|
Unpatented
technology
|
|
9
|
|
39
|
|
1
|
|
38
|
|
2
|
|
|
|
2
|
|
Customer
agreements
|
|
15
|
|
35
|
|
1
|
|
34
|
|
|
|
|
|
|
|
Patents
|
|
16
|
|
15
|
|
9
|
|
6
|
|
12
|
|
8
|
|
4
|
|
Other
|
|
6
|
|
32
|
|
11
|
|
21
|
|
12
|
|
8
|
|
4
|
|
|
|
|
|
$
|
167
|
|
$
|
30
|
|
$
|
137
|
|
$
|
55
|
|
$
|
23
|
|
$
|
32
|
|
We amortize intangible assets
using the straight-line method over the useful lives of the assets.
Amortization expense totaled $7 million in 2006, $4 million in 2005 and $6
million in 2004. Amortization expense is estimated to be approximately $15
million in both 2007 and 2008, $14 million in both 2009 and 2010, and $12
million in 2011.
Note 4.
Accounts Receivable
Accounts receivable is
composed of the following:
|
|
December 30,
|
|
December 31,
|
|
(In millions)
|
|
2006
|
|
2005
|
|
Commercial
|
|
$
|
690
|
|
$
|
660
|
|
U.S. Government
contracts
|
|
308
|
|
269
|
|
|
|
998
|
|
929
|
|
Less allowance
for doubtful accounts
|
|
(34
|
)
|
(38
|
)
|
|
|
$
|
964
|
|
$
|
891
|
|
We
have unbillable receivables on U.S. Government contracts that arise when the
revenues we have appropriately recognized based on performance cannot be billed
yet under terms of the contract. Unbillable receivables within accounts
receivable totaled $144 million at December 30, 2006 and $125 million at
December 31, 2005. Long-term contract receivables due from the U.S. Government
exclude significant amounts billed but unpaid due to contractual retainage
provisions or subject to collection uncertainty.
48
Note 5. Finance Receivables and
Securitizations
Finance Receivables
Through our Finance group, we provide financial
services primarily to the aircraft, golf, vacation interval resort, dealer
floorplan and middle market industries under a variety of financing vehicles
with various contractual maturities. The contractual maturities of finance
receivables outstanding at December 30, 2006 were as follows:
|
|
|
|
|
|
|
|
|
|
|
|
|
|
Finance Receivables
|
|
|
|
Contractual Maturities
|
|
Outstanding
|
|
(In millions)
|
|
2007
|
|
2008
|
|
2009
|
|
2010
|
|
2010
|
|
Thereafter
|
|
2006
|
|
2005
|
|
Distribution
finance receivables
|
|
$
|
1,519
|
|
$
|
559
|
|
$
|
233
|
|
$
|
44
|
|
$
|
66
|
|
$
|
2
|
|
$
|
2,423
|
|
$
|
1,654
|
|
Revolving loans
|
|
1,422
|
|
287
|
|
127
|
|
60
|
|
28
|
|
24
|
|
1,948
|
|
1,633
|
|
Installment
contracts
|
|
273
|
|
185
|
|
188
|
|
165
|
|
215
|
|
648
|
|
1,674
|
|
1,374
|
|
Golf course and
resort mortgages
|
|
149
|
|
171
|
|
137
|
|
146
|
|
167
|
|
290
|
|
1,060
|
|
1,020
|
|
Leveraged leases
|
|
(11
|
)
|
70
|
|
35
|
|
(5
|
)
|
14
|
|
512
|
|
615
|
|
569
|
|
Finance leases
|
|
202
|
|
124
|
|
101
|
|
87
|
|
14
|
|
62
|
|
590
|
|
513
|
|
|
|
$
|
3,554
|
|
$
|
1,396
|
|
$
|
821
|
|
$
|
497
|
|
$
|
504
|
|
$
|
1,538
|
|
8,310
|
|
6,763
|
|
Less allowance
for credit losses
|
|
|
|
|
|
|
|
|
|
|
|
|
|
93
|
|
96
|
|
|
|
|
|
|
|
|
|
|
|
|
|
|
|
$
|
8,217
|
|
$
|
6,667
|
|
This table does not necessarily reflect future cash
collections as receivables are often repaid or refinanced prior to contractual
maturity.
Distribution finance receivables and revolving loans
generally mature within one to five years. Distribution finance receivables
generally are secured by the inventory of the financed distributor and include
floorplan financing for third-party dealers for inventory sold by the E-Z-GO
and Jacobsen businesses. Revolving loans are secured by trade receivables,
inventory, plant and equipment, pools of vacation interval notes receivables,
pools of residential and recreational land loans, and the underlying property.
Installment contracts and finance leases have initial
terms ranging from two to 20 years and primarily are secured by the financed
equipment. Installment contracts generally require the customer to pay a
significant down payment, along with periodic scheduled principal payments that
reduce the outstanding balance through the term of the loan. Finance leases
include residual values expected to be realized at contractual maturity. Leases
with no significant residual value at the end of the contractual term are
classified as installment contracts, as their legal and economic substance is
more equivalent to a secured borrowing than a finance lease with a significant
residual value. Contractual maturities for finance leases classified as
installment contracts in the table above include the minimum lease payments,
net of the unearned income to be recognized over the life of the lease. Total
minimum lease payments and unearned income related to these contracts were $719
million and $222 million, respectively, at December 30, 2006 and $751 million
and $164 million, respectively, at December 31, 2005. Minimum lease payments due
under these contracts for each of the next five years are as follows: $132
million in 2007, $117 million in 2008, $104 million in 2009, $88 million in
2010 and $97 million in 2011.
Golf course and resort mortgages are secured by real
property and generally are limited to 75% or less of the property's appraised
market value at loan origination. Golf course mortgages have initial terms
ranging from five to seven years with amortization periods from 15 to 25 years.
Resort mortgages generally represent construction and inventory loans with
terms up to two years.
Leveraged leases are secured by the ownership of the
leased equipment and real property and have initial terms up to approximately
30 years. Leveraged leases reflect contractual maturities net of contractual
nonrecourse debt payments and include residual values expected to be realized
at contractual maturity.
49
The net investments in
finance leases, excluding leases classified as installment contracts, and
leveraged leases are provided below:
(In millions)
|
|
2006
|
|
2005
|
|
Finance leases:
|
|
|
|
|
|
Total minimum lease
payments receivable
|
|
$
|
517
|
|
$
|
457
|
|
Estimated residual
values of leased equipment
|
|
267
|
|
241
|
|
|
|
784
|
|
698
|
|
Less unearned income
|
|
(194
|
)
|
(185
|
)
|
Net investment in
finance leases
|
|
$
|
590
|
|
$
|
513
|
|
Leveraged leases:
|
|
|
|
|
|
Rental receivable, net
of nonrecourse debt
|
|
$
|
546
|
|
$
|
520
|
|
Estimated residual
values of leased assets
|
|
329
|
|
311
|
|
|
|
875
|
|
831
|
|
Less unearned income
|
|
(260
|
)
|
(262
|
)
|
Investment in leveraged
leases
|
|
615
|
|
569
|
|
Deferred income taxes
|
|
(410
|
)
|
(349
|
)
|
Net investment in leveraged leases
|
|
$
|
205
|
|
$
|
220
|
|
Minimum lease payments due under finance leases for
each of the next five years are as follows: $144 million in 2007, $104 million
in 2008, $70 million in 2009, $34 million in 2010 and $8 million in 2011.
Our Finance group manages and services finance
receivables for a variety of investors, participants and third-party portfolio
owners. The total managed and serviced finance receivable portfolio, including
owned finance receivables, was $11.4 billion at the end of 2006 and $9.9
billion at the end of 2005. Managed receivables include owned finance receivables
and finance receivables sold in securitizations and private transactions where
we retain some element of credit risk and continue to service the portfolio.
Our finance receivables are diversified across
geographic region, borrower industry and type of collateral. At December 30,
2006, 83% of our finance receivables were distributed throughout the United
States, compared with 86% at the end of 2005. The most significant collateral
concentration was in general aviation, which accounted for 19% of managed receivables
at the end of 2006 and 2005. Industry concentrations in the golf and vacation
interval industries each accounted for 16% and 13%, respectively, of managed
receivables at December 30, 2006, compared with 17% and 13%, respectively at
the end of 2005.
Transactions between Finance and
Manufacturing Groups
A portion of our Finance groups business involves
financing retail purchases and leases for new and used aircraft and equipment
manufactured by our Manufacturing group. The captive finance receivables for
these inventory sales that are included in our Finance groups balance sheets
are composed of the following:
|
|
December 30,
|
|
December 31,
|
|
(In millions)
|
|
2006
|
|
2005
|
|
Installment
contracts
|
|
$
|
912
|
|
$
|
628
|
|
Distribution
finance
|
|
73
|
|
51
|
|
Finance leases
|
|
487
|
|
400
|
|
Total
|
|
$
|
1,472
|
|
$
|
1,079
|
|
Operating agreements specify that our Finance group
has recourse to our Manufacturing group for certain uncollected amounts related
to these transactions. Our Manufacturing group has established reserves for
losses on its balance sheet within accrued and other liabilities for the
receivables it guarantees. These reserves are established for amounts that
potentially are uncollectible or if the collateral values are considered
insufficient to cover the outstanding receivable. If an account is deemed
uncollectible and the collateral is repossessed by our Finance group, our
Manufacturing group is charged for the deficiency. If the collateral is not
repossessed, the receivable is transferred from the Finance groups balance
sheet to the Manufacturing groups balance sheet. The Manufacturing group then
is responsible for any additional collection efforts. When this occurs, any
related reserve previously established by the Manufacturing group is
reclassified from accrued or other liabilities and netted against the
receivable or asset transferred from the Finance group.
50
In 2006, 2005 and 2004, our Finance group paid the
Manufacturing group $1.0 billion, $0.8 billion and $0.9 billion, respectively,
related to the sale of Textron-manufactured products that were financed by the
Finance group. Our Manufacturing group also received proceeds in those years of
$63 million, $41 million and $77 million, respectively, from the sale of
equipment to the Finance group for use under operating lease agreements. At the
end of 2006 and 2005, the amounts guaranteed by the Manufacturing group totaled
$335 million and $414 million, respectively, which included equipment leases
with Collins & Aikman Corporation (C&A) that had an outstanding balance
of $61 million at the end of 2006 and $70 million at the end of 2005.
Impairment
Nonaccrual finance receivables include accounts that
are contractually delinquent by more than three months for which the accrual of
interest income is suspended. These receivables are considered impaired when it
is probable that we will be unable to collect all amounts due according to the
contractual terms of the loan agreement. Impaired accrual finance receivables
represent loans with original loan terms that have been significantly modified
to reflect deferred principal payments, generally at market interest rates, for
which collection of principal and interest is not doubtful. The impaired
finance receivables and related reserves at the end of 2006 and 2005 are as follows:
|
|
December 30,
|
|
December 31,
|
|
(In millions)
|
|
2006
|
|
2005
|
|
Impaired
nonaccrual finance receivables
|
|
$
|
60
|
|
$
|
67
|
|
Impaired accrual
finance receivables
|
|
101
|
|
36
|
|
Total impaired
finance receivables
|
|
$
|
161
|
|
$
|
103
|
|
|
|
|
|
|
|
Impaired
nonaccrual finance receivables with identified reserve requirements
|
|
$
|
36
|
|
$
|
53
|
|
Allowance for losses on
finance receivables related to impaired loans
|
|
$
|
17
|
|
$
|
18
|
|
The average recorded investment in impaired finance
receivables during 2006 was $142 million, compared with $106 million in 2005.
The increase primarily reflects one restructured loan in golf finance for which
payments are being made.
The table above excludes finance receivables for
which the Finance group has recourse to the Manufacturing group. The Finance
group continues to recognize income on past-due receivables that meet the
nonaccrual criteria that are guaranteed by the Manufacturing group. On a
consolidated basis, there are no earnings for these receivables since the
Manufacturing group is charged for its obligation to the Finance group. At the
end of 2006 and 2005, these past-due loans totaled $2 million and $8 million,
respectively. In addition, while C&A continues to make payments on its
equipment leases, these leases are considered impaired since C&A currently
is under bankruptcy protection and the lease terms have expired. The
Manufacturing group has total reserves for losses for its guarantees to the
Finance group of $39 million at the end of 2006 and $40 million at the end of
2005.
Securitizations
We received proceeds from the securitization and sale
(with servicing rights retained) of finance receivables of $50 million in 2006,
$361 million in 2005 and $394 million in 2004. Gains from securitized trust
sales were approximately $42 million in 2006, $49 million in 2005 and $56
million in 2004. For securitizations in 2006, key economic assumptions used in
measuring the retained interests at the date of securitization included a
weighted-average life of three months, expected annual credit losses of 0.2%
and a residual cash flows discount rate of 10%.
We retain subordinated interests in the trusts, which
are approximately 2% to 10% of the total trust. Servicing fees range from 75 to
150 basis points. At the end of 2006, $2.1 billion in securitized loans were outstanding,
with $13 million in past-due loans. Our Finance group has securitized certain
receivables for which it has retained full recourse to our Manufacturing group.
At the end of 2006, we had $179 million in retained
interest recorded in other assets, which primarily included $111 million in
distribution finance receivables and $56 million in general aviation loans. In
comparison, retained interest totaled $208 million at the end of 2005. Cash
flows received on these retained interests totaled $63 million in 2006, $64
million in 2005 and $70 million in 2004. At the end of 2006, key economic
assumptions used in measuring our retained interests were as follows: for the
distribution finance receivables: weighted-average life of three months,
expected annual credit loss rate of 0.2% and residual cash flow discount rate
of 10.2%; and for general aviation loans: weighted-average life of 1.7 years,
annual prepayment speed of 25%, expected annual credit loss rate of 0.3% and
residual cash flow discount rate of 5.5%.
51
Note 6. Inventories
Inventories are composed of the following:
|
|
December 30,
|
|
December 31,
|
|
(In millions)
|
|
2006
|
|
2005
|
|
Finished goods
|
|
$
|
665
|
|
$
|
527
|
|
Work in process
|
|
1,562
|
|
1,410
|
|
Raw materials
|
|
435
|
|
267
|
|
|
|
2,662
|
|
2,204
|
|
Less
progress/milestone payments
|
|
593
|
|
492
|
|
|
|
$
|
2,069
|
|
$
|
1,712
|
|
Inventories valued by the LIFO method totaled $1.5
billion and $1.3 billion at the end of 2006 and 2005, respectively. Had our
LIFO inventories been valued at current costs, their carrying values would have
been approximately $276 million and $251 million higher at those respective
dates. Inventories related to long-term contracts, net of progress/milestone
payments were $380 million at the end of 2006 and $350 million at the end of
2005.
Bell Helicopters H-1 program with the U.S.
Government is currently transitioning to the production phase of the program
with manufacturing of the first three production lots for Low Rate Initial
Production (LRIP) aircraft. Inventories related to the H-1 LRIP Lot 1 and Lot
2 contracts have been written down to net realizable value to reflect charges
related to these contracts as discussed below.
During 2006, we estimated that the costs to complete
H-1 LRIP Lot 1 would exceed contractual reimbursement. Through the third
quarter of 2006, we recorded $29 million in charges related to the H-1 LRIP Lot
1 contract. These charges primarily reflected the impact of higher estimated
incremental costs for resources added to meet the contractual schedule
requirements and higher anticipated efforts in final assembly. At the end of
the third quarter, we had anticipated that acceptance of the initial H-1 LRIP
Lot 1 aircraft by the U.S. Government would occur in the fourth quarter of
2006. However, acceptance was delayed and no aircraft were delivered. This
delay was due to changes in the development and engineering requirements that
were identified in the final stages of assembly and acceptance testing. Due to
this delay and the costs associated with the additional development efforts,
rework of in-process units and resulting inefficiencies, we increased our
estimate of the completion costs in the fourth quarter. Accordingly, we
recorded an additional $20 million charge related to the H-1 LRIP Lot 1
contract in the fourth quarter of 2006. In January 2007, the U.S. Government
accepted two aircraft, and we expect the remaining seven H-1 LRIP Lot 1 units
to be accepted later in 2007.
The H-1 LRIP Lot 2 contract is in the early stages of
production, with first aircraft delivery anticipated in the second half of
2007. We now anticipate that the disruption and delays experienced with the H-1
LRIP Lot 1 contract in the fourth quarter will result in increased costs for
the H-1 LRIP Lot 2 contract due to delays in its completion, as well as a
reduction in previously anticipated learning curve improvements. Due to these
higher cost estimates, the H-1 LRIP Lot 2 contract now is in a loss position
resulting in a fourth quarter charge of $33 million.
The net H-1 program charge, including favorable
performance on the Engineering and Manufacturing Development contract of $3
million, was $50 million in the fourth quarter of 2006.
Note 7. Property, Plant and
Equipment, net
Our Manufacturing groups property, plant and
equipment, net are composed of the following:
|
|
December 30,
|
|
December 31,
|
|
(In millions)
|
|
2006
|
|
2005
|
|
Land and
buildings
|
|
$
|
1,093
|
|
$
|
1,008
|
|
Machinery and
equipment
|
|
2,827
|
|
2,565
|
|
|
|
3,920
|
|
3,573
|
|
Less accumulated
depreciation and amortization
|
|
2,147
|
|
1,999
|
|
|
|
$
|
1,773
|
|
$
|
1,574
|
|
Depreciation expense for the Manufacturing group
totaled $243 million in 2006, $250 million in 2005 and $229 million in 2004.
52
We have incurred asset retirement obligations
primarily related to costs to remove and dispose of underground storage tanks
and asbestos materials used in insulation, adhesive fillers and floor tiles.
There is no legal requirement to remove these items, and there currently is no
plan to remodel the related facilities or otherwise cause the impacted items to
require disposal. As a result, these asset retirement obligations are not
estimable, and in accordance with the provisions of FASB Interpretation No. 47,
Conditional Asset Retirement Obligations, we have not recorded a liability.
Note 8. Debt and Credit Facilities
Debt and credit facilities are composed of the
following:
|
|
December 30,
|
|
December 31,
|
|
(In millions)
|
|
2006
|
|
2005
|
|
Manufacturing
group:
|
|
|
|
|
|
Short-term debt:
|
|
|
|
|
|
Revolving lines of credit
|
|
$
|
41
|
|
$
|
267
|
|
Current portion of long-term debt
|
|
39
|
|
8
|
|
Total short-term debt
|
|
$
|
80
|
|
$
|
275
|
|
Long-term senior
debt:
|
|
|
|
|
|
Medium-term notes due 2010 to 2011 (average rate of
9.85%)
|
|
17
|
|
17
|
|
6.375% due 2008
|
|
300
|
|
300
|
|
4.50% due 2010
|
|
250
|
|
250
|
|
6.50% due 2012
|
|
300
|
|
300
|
|
3.875% due 2013
|
|
396
|
|
356
|
|
6.625% due 2020
|
|
295
|
|
260
|
|
Other long-term debt (average rate of 5.3% and 6.2%,
respectively)
|
|
201
|
|
184
|
|
|
|
1,759
|
|
1,667
|
|
Current portion
of long-term debt
|
|
(39
|
)
|
(8
|
)
|
Total long-term debt
|
|
1,720
|
|
1,659
|
|
Total Manufacturing group debt
|
|
$
|
1,800
|
|
$
|
1,934
|
|
|
|
|
|
|
|
Finance
group:
|
|
|
|
|
|
Borrowings under
or supported by credit facilities*
|
|
$
|
1,779
|
|
$
|
1,200
|
|
Fixed-rate debt
at average rate of 5.03% and 4.71%, respectively
|
|
3,264
|
|
3,209
|
|
Variable-rate
notes at average rate of 5.52% and 4.73%, respectively
|
|
1,819
|
|
1,011
|
|
Total Finance group
debt
|
|
$
|
6,862
|
|
$
|
5,420
|
|
* The weighted-average
interest rates on these borrowings before the effect of interest rate exchange
agreements were 5.3% and 4.4% at the end of 2006 and 2005, respectively, and
5.0% for the year 2006 and 3.3% for the year 2005.
We have a policy of maintaining unused committed bank
lines of credit in an amount not less than outstanding commercial paper
balances. These facilities are in support of commercial paper and letters of
credit issuances only, and neither of these primary lines of credit was drawn
at December 30, 2006 or December 31, 2005. Our Manufacturing group had no
commercial paper outstanding at December 30, 2006 or December 31, 2005. The
Manufacturing groups weighted-average interest rate on its commercial paper
borrowings throughout the year was 5.3% in 2006 and 3.0% in 2005. Our primary
committed credit facilities at December 30, 2006 include the following:
|
|
|
|
|
|
|
|
Amount Not
|
|
|
|
|
|
|
|
|
|
Reserved as
|
|
|
|
|
|
|
|
|
|
Support for
|
|
|
|
|
|
Commercial
|
|
Letters of
|
|
Commercial
|
|
|
|
Facility
|
|
Paper
|
|
Credit
|
|
Paper and
|
|
(In millions)
|
|
Amount
|
|
Outstanding
|
|
Outstanding
|
|
Letters of Credit
|
|
Manufacturing
group - multi-year facility expiring in 2011*
|
|
$
|
1,250
|
|
$
|
|
|
$
|
23
|
|
$
|
1,227
|
|
Finance group -
multi-year facility expiring in 2011
|
|
$
|
1,750
|
|
$
|
1,719
|
|
$
|
13
|
|
$
|
18
|
|
* Our Finance group is permitted to
borrow under this multi-year facility.
53
Lending agreements limit our Finance groups net
assets available for dividends and other payments to the Manufacturing group to
approximately $304 million of the Finance groups net assets of $1.1 billion at
the end of 2006. These lending agreements also contain various restrictive
provisions regarding additional debt (not to exceed 800% of consolidated net
worth and qualifying subordinated obligations), minimum net worth ($200
million), the creation of liens and the maintenance of a fixed charges coverage
ratio (no less than 125%).
The following table shows required payments during
the next five years on debt outstanding at the end of 2006. The payment
schedule excludes amounts that are payable under or supported by the primary
revolving credit facilities or revolving lines of credit:
(In millions)
|
|
2007
|
|
2008
|
|
2009
|
|
2010
|
|
2011
|
|
Manufacturing
group
|
|
$
|
80
|
|
$
|
351
|
|
$
|
3
|
|
$
|
254
|
|
$
|
19
|
|
Finance group
|
|
1,118
|
|
966
|
|
1,562
|
|
833
|
|
442
|
|
|
|
$
|
1,198
|
|
$
|
1,317
|
|
$
|
1,565
|
|
$
|
1,087
|
|
$
|
461
|
|
Under a support agreement, our Manufacturing group
has agreed to ensure that the Finance group maintains certain minimum levels of
financial performance. No payments have ever been required to meet these
standards.
Note 9. Derivatives and Other
Financial Instruments
Fair Value Interest Rate Hedges
We manage interest cost for our Manufacturing group
using a mix of fixed- and variable-rate debt. To manage this mix in a cost efficient
manner, we enter into interest rate exchange agreements to swap, at specified
intervals, the difference between fixed and variable interest amounts
calculated by reference to an agreed-upon notional principal amount. These
hedges are considered perfectly effective since the critical terms of the debt
and the interest rate exchange match and the other conditions of SFAS No. 133, Accounting
for Derivative Instruments and Hedging Activities, are met. The mark-to-market
values of both the fair value hedge instruments and underlying debt obligations
are recorded as equal and offsetting amounts in interest expense. Our
Manufacturing group had interest rate exchange agreements with a fair value
liability of $8 million at the end of 2006 and $10 million at the end of 2005.
Our Finance group enters into interest rate exchange
agreements to mitigate exposure to changes in the fair value of its fixed-rate
receivables and debt due to fluctuations in interest rates. By using these
agreements, we are able to convert our fixed-rate cash flows to floating-rate
cash flows. At December 30, 2006, the Finance group had interest rate exchange
agreements with a fair value liability of $45 million designated as fair value
hedges, compared with a $43 million liability at December 31, 2005.
Our Finance group has a Canadian dollar functional
currency subsidiary with $60 million in U.S. dollar-denominated fixed-rate
debt. To hedge our exposure to changes in both foreign currency exchange rates
and Canadian Bankers Acceptance rates, we utilize foreign currency interest
rate exchange agreements. At December 30, 2006 and December 31, 2005, these
instruments had a fair value liability of $9 million. Our fair value hedges are
highly effective, resulting in an immaterial net impact to earnings due to
hedge ineffectiveness.
Cash Flow Interest Rate Hedges
We experience variability in the cash flows we
receive from our Finance groups investments in interest-only securities due to
fluctuations in interest rates. To mitigate our exposure to this variability,
our Finance group enters into interest rate exchange, cap and floor agreements.
The combination of these instruments converts net residual floating-rate cash
flows expected to be received by our Finance group to fixed-rate cash flows.
Changes in the fair value of these instruments are recorded net of the income
tax effect in other comprehensive income (loss). At December 30, 2006, these
instruments had a fair value liability of less than $1 million, compared with a
$5 million liability at December 31, 2005. We do not expect a significant
amount of deferred gains, net of tax to be reclassified to earnings related to
these hedge relationships in 2007.
For cash flow hedges, our Finance group recorded an
after-tax gain of $1 million in 2006 and after-tax losses of $5 million and $7
million in 2005 and 2004, respectively, to accumulated other comprehensive loss
with no impact to the statements of operations. We have not incurred a
significant net gain or loss in earnings as the result of the ineffectiveness,
or the exclusion of any component from our assessment of hedge effectiveness,
in 2006 or 2005.
Our exposure to loss from nonperformance by the
counterparties to our interest rate exchange agreements at the end of 2006 is
minimal. We do not anticipate nonperformance by counterparties in the periodic
settlements of amounts due. We currently minimize this potential for risk by
entering into contracts exclusively with major, financially sound
counterparties having no less than a long-term bond rating of A, by
54
continuously monitoring such credit ratings and by
limiting exposure to any one financial institution. The credit risk generally
is limited to the amount by which the counterparties contractual obligations
exceed our obligations to the counterparty.
Cash Flow Foreign Exchange Rate
Hedges
Since we manufacture and sell our products in a
number of countries throughout the world, we are exposed to movements in
foreign currency exchange rates. The primary purpose of our foreign currency
hedging activities is to manage the volatility associated with foreign currency
purchases of materials, foreign currency sales of its products, and other
assets and liabilities created in the normal course of business. We primarily
utilize forward exchange contracts and purchased options with maturities of no
more than 18 months that qualify as cash flow hedges. These are intended to
offset the effect of exchange rate fluctuations on forecasted sales, inventory
purchases and overhead expenses. The fair value of these instruments at
December 30, 2006 was a $13 million asset. At year-end 2006, $8 million in
after-tax income was reported in accumulated other comprehensive loss from
qualifying cash flow hedges. This income generally is expected to be reclassified
to earnings in the next 12 months as the underlying transactions occur.
Our Manufacturing group also enters into certain
foreign currency derivative instruments that do not meet hedge accounting
criteria and primarily are intended to protect against exposure related to
intercompany financing transactions and income from international operations.
The fair value of these instruments at the end of 2006 and 2005 and the net
impact of the related gains and losses on selling and administrative expense in
2006 and 2005 were not material.
Net Investment Hedging
We hedge our net investment position in major
currencies and generate foreign currency interest payments that offset other
transactional exposures in these currencies. To accomplish this, we borrow
directly in foreign currency and designate a portion of foreign currency debt
as a hedge of net investments. We also may utilize currency forwards as hedges
of our related foreign net investments. Currency effects of these hedges, which
are reflected in the cumulative translation adjustment account within other
comprehensive income (loss), produced a $49 million after-tax loss during 2006,
leaving an accumulated net loss balance of $19 million.
Stock-Based Compensation Hedging
We manage the expense related to stock-based
compensation awards using cash settlement forward contracts on our common
stock. The use of these forward contracts modifies compensation expense
exposure to changes in the stock price with the intent to reduce potential
variability. The fair value of these instruments at December 30, 2006 and
December 31, 2005 was a receivable of $24 million and $10 million,
respectively. Gains and losses on these instruments are recorded as an
adjustment to compensation expense when the award is charged to expense. These
contracts increased net income by $21 million in 2006, $8 million in 2005 and
$28 million in 2004. Cash received or paid on the contract settlement is
included in cash flows from operating activities, consistent with the
classification of the cash flows on the underlying hedged compensation expense.
Fair Values of Financial Instruments
The carrying amounts and estimated fair values of our
financial instruments that are not reflected in the financial statements at
fair value are as follows:
|
|
December 30, 2006
|
|
December 31, 2005
|
|
|
|
|
|
Estimated
|
|
|
|
Estimated
|
|
|
|
Carrying
|
|
Fair
|
|
Carrying
|
|
Fair
|
|
(In millions)
|
|
Value
|
|
Value
|
|
Value
|
|
Value
|
|
Manufacturing
group:
|
|
|
|
|
|
|
|
|
|
Debt
|
|
$
|
(1,800
|
)
|
$
|
(1,833
|
)
|
$
|
(1,934
|
)
|
$
|
(2,012
|
)
|
Finance
group:
|
|
|
|
|
|
|
|
|
|
Finance
receivables
|
|
$
|
7,019
|
|
$
|
6,982
|
|
$
|
5,589
|
|
$
|
5,515
|
|
Debt
|
|
$
|
(6,862
|
)
|
$
|
(6,868
|
)
|
$
|
(5,420
|
)
|
$
|
(5,423
|
)
|
Finance receivables exclude the fair value of finance
and leveraged leases totaling $1.2 billion at December 30, 2006 and $1.1
billion at December 31, 2005 as these leases are recorded at fair value in the
consolidated balance sheets.
55
Note 10. Shareholders Equity
Capital Stock
We have authorization for 15,000,000 shares of
preferred stock and 500,000,000 shares of 12.5 cent per share par value common
stock. Each share of $2.08 Preferred Stock ($23.63 approximate stated value) is
convertible into 4.4 shares of common stock, and we can redeem it for $50 per
share. Each share of $1.40 Preferred Dividend Stock ($11.82 approximate stated
value) is convertible into 3.6 shares of common stock, and we can redeem it for
$45 per share.
Reserved Shares of Common Stock
At the end of 2006, common stock reserved for the
subsequent conversion of preferred stock and shares reserved for the exercise
of stock options were 2,546,000 and 5,420,000, respectively.
Income per Common Share
A reconciliation of income from continuing operations
and basic to diluted share amounts is presented below:
|
|
2006
|
|
2005
|
|
2004
|
|
|
|
|
|
Average
|
|
|
|
Average
|
|
|
|
Average
|
|
(Dollars in millions, shares in thousands)
|
|
Income
|
|
Shares
|
|
Income
|
|
Shares
|
|
Income
|
|
Shares
|
|
Income from
continuing operations available to common shareholders
|
|
$
|
706
|
|
127,549
|
|
$
|
516
|
|
133,531
|
|
$
|
375
|
|
137,337
|
|
Dilutive effect
of convertible preferred stock and stock options
|
|
|
|
2,673
|
|
|
|
2,915
|
|
|
|
2,832
|
|
Available to common
shareholders and assumed conversions
|
|
$
|
706
|
|
130,222
|
|
$
|
516
|
|
136,446
|
|
$
|
375
|
|
140,169
|
|
Accumulated Other Comprehensive Loss
The components of accumulated other comprehensive
loss are presented below:
|
|
|
|
|
|
Pension
|
|
Deferred
|
|
|
|
|
|
|
|
Unrealized
|
|
and Post-
|
|
Gains
|
|
|
|
|
|
Currency
|
|
Gains
|
|
retirement
|
|
(Losses)
|
|
|
|
|
|
Translation
|
|
(Losses)
|
|
Benefits
|
|
on Hedge
|
|
|
|
(In millions)
|
|
Adjustment
|
|
on Securities
|
|
Adjustments
|
|
Contracts
|
|
Total
|
|
Balance at
January 3, 2004
|
|
$
|
47
|
|
$
|
3
|
|
$
|
(132
|
)
|
$
|
18
|
|
$
|
(64
|
)
|
Other
comprehensive income (loss), net of tax
|
|
97
|
|
|
|
(131
|
)
|
4
|
|
(30
|
)
|
Reclassification
adjustment, net of tax
|
|
|
|
(3
|
)
|
|
|
|
|
(3
|
)
|
Balance at
January 1, 2005
|
|
$
|
144
|
|
$
|
|
|
$
|
(263
|
)
|
$
|
22
|
|
$
|
(97
|
)
|
Other
comprehensive income (loss), net of tax
|
|
(17
|
)
|
|
|
34
|
|
2
|
|
19
|
|
Balance at
December 31, 2005
|
|
$
|
127
|
|
$
|
|
|
$
|
(229
|
)
|
$
|
24
|
|
$
|
(78
|
)
|
Transition
adjustment due to change in accounting, net of taxes
|
|
|
|
|
|
(647
|
)
|
|
|
(647
|
)
|
Other
comprehensive income (loss), net of tax
|
|
45
|
|
|
|
58
|
|
(5
|
)
|
98
|
|
Reclassification
due to sale of Fastening Systems, net of tax
|
|
(47
|
)
|
|
|
39
|
|
|
|
(8
|
)
|
Reclassification
adjustment, net of tax
|
|
|
|
|
|
|
|
(9
|
)
|
(9
|
)
|
Balance at December 30,
2006
|
|
$
|
125
|
|
$
|
|
|
$
|
(779
|
)
|
$
|
10
|
|
$
|
(644
|
)
|
Included in other comprehensive income (loss) is an
income tax benefit (expense) of $359 million, $(12) million and $(22) million
in 2006, 2005 and 2004, respectively. In 2006, pension and postretirement
benefit adjustments included a $348 million income tax benefit related to the
transition adjustment due to the adoption of SFAS No. 158.
56
Note 11. Share-Based Compensation
Summary of Share-Based Compensation
Plans
Our 1999 Long-Term Incentive Plan (the Plan)
authorizes awards to our key employees in the form of options to purchase our
shares and restricted stock. Options to purchase our shares have a maximum term
of 10 years and vest ratably over a three-year period. Restricted stock grants
vest one-third each in the third, fourth and fifth year following the grant.
The maximum number of shares authorized under the Plan includes 17.5 million
options to purchase our shares and 2 million shares of restricted stock. We
also provide share-based compensation awards payable in cash, including
retention awards to certain executives and performance share units. Payouts
under performance share units vary based on certain performance criteria
measured over a three-year period. The performance share units vest at the end
of three years.
Through our Deferred Income Plan for Textron Key
Executives (the DIP), we provide participants the opportunity to voluntarily
defer up to 25% of their base salary and up to 100% of annual and long-term
incentive compensation and other compensation. Elective deferrals may be put
into either a stock unit account or an interest bearing account. We generally
contribute a 10% premium on amounts deferred into the stock unit account.
Executives who are eligible to participate in the DIP who have not achieved
and/or maintained the required minimum stock ownership level are required to
defer annual incentive compensation in excess of 100% of the executives annual
target into a deferred stock unit account and are not entitled to the 10%
premium contribution on the amount deferred. Participants cannot move amounts
between the two accounts while actively employed by us and cannot receive
distributions until termination of employment.
Change in Accounting for Share-Based
Compensation
We adopted SFAS No. 123 (Revised 2004), Share-Based
Payment (SFAS No. 123-R), which replaces SFAS No. 123, Accounting for
Stock-Based Compensation and supersedes Accounting Principles Board Opinion
No. 25, Accounting for Stock Issued to Employees (APB No. 25), in the first
quarter of 2005 using the modified prospective transition method. SFAS No.
123-R requires companies to measure compensation costs for share-based payments
to employees, including stock options, at fair value and to expense such
compensation over the service period. Under the transition method, compensation
expense recognized in 2005 includes: a) compensation cost for all stock options
and restricted stock granted prior to but not yet vested as of January 1, 2005,
based on the grant-date fair value estimated and recognized in accordance with
the provisions of SFAS No. 123 and b) compensation cost for all stock options
and restricted stock granted subsequent to January 1, 2005 and all share-based
compensation awards accounted for as liabilities, based upon the measurement
and recognition provisions of SFAS No. 123-R. For awards granted or modified in
2005 and prospectively, compensation costs for awards with only service
conditions that vest ratably are recognized on a straight-line basis over the
requisite service period for each separately vesting portion of the award.
Compensation costs for awards granted prior to 2005 are recognized using the
attribution methods required under SFAS No. 123. Prior to 2005, we accounted
for share-based payments, including stock options issued under our Plan, using
the intrinsic value method of APB No. 25.
Upon adoption, we remeasured our share-based
compensation awards that are accounted for as liabilities at fair value. The
cumulative effect of adoption upon this remeasurement increased net income by
approximately $1 million in the first quarter of 2005, which is not considered
to be material and is recorded in selling and administrative expense. SFAS No.
123-R requires that the excess tax benefits received related to stock option
exercises be presented as financing cash inflows. For 2006 and 2005, $31
million and $14 million, respectively, of these excess tax benefits have been
presented as cash provided by financing activities in the consolidated
statement of cash flows.
The compensation expense that has been recorded in
net income for our share-based compensation plans is as follows:
(In millions)
|
|
2006
|
|
2005
|
|
2004
|
|
Compensation
expense, net of hedge income or expense
|
|
$
|
71
|
|
$
|
64
|
|
$
|
31
|
|
Income tax
benefit
|
|
(28
|
)
|
(24
|
)
|
(11
|
)
|
Total net
compensation cost included in net income
|
|
$
|
43
|
|
$
|
40
|
|
$
|
20
|
|
Net compensation
costs included in discontinued operations
|
|
(2
|
)
|
2
|
|
1
|
|
Net compensation costs
included in continuing operations
|
|
$
|
45
|
|
$
|
38
|
|
$
|
19
|
|
Share-based compensation costs are reflected
primarily in selling and administrative expenses. For 2006 and 2005, the
expense includes attribution of the fair value of options issued, as well as
the portion of previously granted options for which the requisite service was
rendered, totaling approximately $16 million in 2006 and $17 million in 2005.
Of this amount, approximately $18 million and $15 million, respectively, have
been recorded in continuing operations and $(2) million and $2 million,
respectively, in discontinued operations. During 2006, Textron recorded
approximately $4 million of share-based award forfeitures related to
discontinued operations.
57
The net impact of the adoption of SFAS No. 123-R was
as follows for the year ended December 31, 2005:
|
|
Upon
|
|
If Not
|
|
(In millions, except per share data)
|
|
Adoption
|
|
Adopted
|
|
Income from
continuing operations before income taxes
|
|
$
|
739
|
|
$
|
755
|
|
Net income
|
|
$
|
203
|
|
$
|
214
|
|
Cash flows from
operating activities of continuing operations
|
|
$
|
952
|
|
$
|
966
|
|
Cash flows from
financing activities of continuing operations
|
|
$
|
284
|
|
$
|
270
|
|
Basic earnings
per share
|
|
$
|
1.52
|
|
$
|
1.60
|
|
Diluted earnings per
share
|
|
$
|
1.49
|
|
$
|
1.57
|
|
Impact of SFAS No. 123-R Adoption on
Prior Periods
For the year ended January 1, 2005, no compensation
expense related to stock option grants has been recorded in the consolidated
statements of operations as the options granted had an exercise price equal to
the market value of the underlying stock on the date of grant. Results for
prior periods have not been restated.
The following table illustrates the effect on net
income and earnings per share if we had applied the fair value recognition
provisions required by SFAS No. 123-R prior to January 2, 2005:
(In millions, except per share data)
|
|
2004
|
|
Net
income, as reported
|
|
$
|
365
|
|
Add back:
Share-based employee compensation expense included in reported net income*
|
|
20
|
|
Deduct: Total
share-based employee compensation expense determined under fair value based
method for all awards*
|
|
(26
|
)
|
Pro
forma net income
|
|
$
|
359
|
|
Income per
share:
|
|
|
|
Basic - as reported
|
|
$
|
2.66
|
|
Basic - pro forma
|
|
$
|
2.61
|
|
Diluted - as reported
|
|
$
|
2.61
|
|
Diluted - pro
forma
|
|
$
|
2.56
|
|
* Amounts are net of related taxes
and hedge income or expense.
Stock Options
The stock option compensation cost calculated under
the fair value approach is recognized over the vesting period of the stock
options. The weighted-average fair value of options granted per share was $25,
$20 and $14 for 2006, 2005 and 2004, respectively. We estimate the fair value
of options granted on the date of grant using the Black-Scholes option-pricing
model. Expected volatilities are based on implied volatilities from traded
options on our common stock, historical volatilities and other factors. We use
historical data to estimate option exercise behavior, adjusted to reflect
anticipated increases in expected life.
The weighted-average assumptions used in our
Black-Scholes option-pricing model for awards issued during the respective
periods are as follows:
|
|
2006
|
|
2005
|
|
2004
|
|
Dividend yield
|
|
2
|
%
|
2
|
%
|
2
|
%
|
Expected
volatility
|
|
25
|
%
|
25
|
%
|
37
|
%
|
Risk-free
interest rate
|
|
4
|
%
|
4
|
%
|
3
|
%
|
Expected term (In
years)
|
|
6.0
|
|
6.0
|
|
3.7
|
|
58
The following table summarizes information related to
stock option activity for the respective periods:
(In millions)
|
|
2006
|
|
2005
|
|
2004
|
|
Intrinsic value
of options exercised
|
|
$
|
120
|
|
$
|
59
|
|
$
|
81
|
|
Cash received
from option exercises
|
|
$
|
173
|
|
$
|
106
|
|
$
|
187
|
|
Actual tax benefit
realized for tax deductions from option exercises
|
|
$
|
38
|
|
$
|
18
|
|
$
|
26
|
|
Stock option activity under the Plan is summarized as
follows:
|
|
2006
|
|
2005
|
|
2004
|
|
|
|
|
|
Weighted-
|
|
|
|
Weighted-
|
|
|
|
Weighted-
|
|
|
|
|
|
Average
|
|
|
|
Average
|
|
|
|
Average
|
|
|
|
Number of
|
|
Exercise
|
|
Number of
|
|
Exercise
|
|
Number of
|
|
Exercise
|
|
(Shares in thousands)
|
|
Options
|
|
Price
|
|
Options
|
|
Price
|
|
Options
|
|
Price
|
|
Outstanding at
beginning of year
|
|
8,146
|
|
$
|
56.23
|
|
9,261
|
|
$
|
52.05
|
|
13,158
|
|
$
|
49.24
|
|
Granted
|
|
1,000
|
|
87.97
|
|
1,208
|
|
76.69
|
|
1,532
|
|
54.07
|
|
Exercised
|
|
(3,319
|
)
|
52.34
|
|
(2,151
|
)
|
48.62
|
|
(4,363
|
)
|
42.48
|
|
Canceled,
expired or forfeited
|
|
(407
|
)
|
65.54
|
|
(172
|
)
|
70.09
|
|
(1,066
|
)
|
59.52
|
|
Outstanding at
end of year
|
|
5,420
|
|
$
|
63.77
|
|
8,146
|
|
$
|
56.23
|
|
9,261
|
|
$
|
52.05
|
|
Exercisable at end of
year
|
|
3,473
|
|
$
|
55.64
|
|
6,206
|
|
$
|
52.41
|
|
7,176
|
|
$
|
52.70
|
|
Options that were outstanding and exercisable as of
December 30, 2006 are as follows:
|
|
|
|
|
|
Weighted-
|
|
|
|
|
|
|
|
|
|
Average
|
|
|
|
|
|
|
|
|
|
Remaining
|
|
Aggregate
|
|
|
|
Number of
|
|
Weighted-
|
|
Contractual
|
|
Intrinsic
|
|
|
|
Options
|
|
Average
|
|
Life
|
|
Value
|
|
|
|
(In thousands)
|
|
Exercise Price
|
|
(In years)
|
|
(In millions)
|
|
Outstanding
|
|
5,420
|
|
$
|
63.77
|
|
6.08
|
|
$
|
163
|
|
Exercisable
|
|
3,473
|
|
$
|
55.64
|
|
4.76
|
|
$
|
132
|
|
Restricted Stock
The fair value of restricted stock is based on the
trading price of our common stock on the date of grant, less required
adjustments to reflect the fair value of the award as dividends are not paid or
accrued until the restricted stock vests. The weighted-average grant-date fair
value of restricted stock granted in 2006, 2005 and 2004 was approximately $82,
$71 and $57 per share, respectively.
Restricted stock activity under the Plan for 2006 is
as follows:
|
|
|
|
Weighted-
|
|
|
|
|
|
Average
|
|
|
|
Number of
|
|
Grant Date
|
|
(Shares in thousands)
|
|
Shares
|
|
Fair Value
|
|
Outstanding at
beginning of year, nonvested
|
|
1,156
|
|
$
|
55.99
|
|
Granted
|
|
408
|
|
82.39
|
|
Vested
|
|
(117
|
)
|
42.02
|
|
Forfeited*
|
|
(228
|
)
|
60.16
|
|
Outstanding at end of
year, nonvested
|
|
1,219
|
|
$
|
65.38
|
|
* Forfeitures during the year
relate primarily to the sale of the Fastening Systems business.
Share-Based Compensation Awards
Accounted for as Liabilities
The fair value of share-based compensation awards
accounted for as liabilities includes performance share units, retention awards
and DIP stock unit awards. The fair value of these awards is based on the
trading price of our common stock, less adjustments to reflect the fair value
of the award as dividends are not paid or accrued until vested, and is
remeasured at each reporting period date.
59
Share-Based Compensation Awards
The value of the share-based compensation awards that
vested and/or were paid during the respective periods is as follows:
(In millions)
|
|
2006
|
|
2005
|
|
2004
|
|
Subject only to
service conditions:
|
|
|
|
|
|
|
|
Value of shares, options or units vested
|
|
$
|
32
|
|
$
|
21
|
|
$
|
36
|
|
Intrinsic value of cash awards paid
|
|
$
|
13
|
|
$
|
9
|
|
$
|
8
|
|
Subject to
performance vesting conditions:
|
|
|
|
|
|
|
|
Value of units vested
|
|
$
|
42
|
|
$
|
37
|
|
$
|
26
|
|
Intrinsic value of cash awards paid
|
|
$
|
37
|
|
$
|
25
|
|
$
|
15
|
|
Intrinsic value of
amounts paid under DIP
|
|
$
|
1
|
|
$
|
18
|
|
$
|
7
|
|
As of December 30, 2006, we had not recognized $58
million in the total compensation cost associated with unvested awards subject
only to service conditions. As of December 30, 2006, we had not recognized $28
million in the total compensation cost associated with unvested share-based
compensation awards subject to performance vesting conditions. We expect to
recognize compensation expense for these awards over a weighted-average period
of approximately two years.
Note 12. Retirement Plans
Our defined benefit and defined contribution pension
plans together cover substantially all of our employees. Our defined
contribution plans cost approximately $50 million in 2006, $45 million in 2005
and $23 million in 2004. In 2005, the cost related to these defined
contribution plans increased in comparison to 2004 primarily due to changes in
our matching contribution rate. A significant number of our U.S.-based
employees participate in the Textron Master Retirement Plan (TMRP), which is
subject to the provisions of the Employee Retirement Income Security Act of
1974 and primarily is a noncontributory defined benefit pension plan. Certain
U.S.-based employees also are eligible for supplemental pension benefit plans
that are not separately funded. In addition, we sponsor both funded and
unfunded pension plans for certain of our foreign subsidiaries. We also provide
postretirement benefits other than pensions for certain retired employees,
which include healthcare and life insurance benefits.
In October 2006, we transferred $281 million of plan
assets from the TMRP to a plan established by the purchaser of our Fastening
Systems business. This settled our obligation to the U.S.-based employees of
this business. Upon this settlement, we recognized a loss of $35 million, which
is included in discontinued operations. Obligations related to the Fastening
Systems business foreign plans were assumed by the purchaser.
Impact of Adoption of New Accounting
Standard
On December 30, 2006, we adopted SFAS No. 158, Employers
Accounting for Defined Benefit Pension and Other Postretirement Plans - An
amendment of FASB Statement Nos. 87, 88, 106, and 132(R). This Statement
requires an employer to: (a) recognize in its statement of financial position
an asset for a plans overfunded status or a liability for a plans underfunded
status; (b) measure a plans assets and its obligations that determine its
funded status as of the end of the employers fiscal year; and (c) recognize
changes in the funded status of a defined benefit postretirement plan in the
year in which the changes occur and report these changes in comprehensive
income. The measurement date provisions did not impact us as all of our plans
have a measurement date of December 30 of the current fiscal year.
The impact of implementing SFAS No. 158 reduced total
assets by $313 million, increased total liabilities by $334 million and reduced
shareholders equity (increase to accumulated other comprehensive loss) by $647
million, net of tax. In addition, we have classified an additional $92 million
of pension and postretirement benefit liabilities as current. The adoption did
not affect our consolidated balance sheet at December 31, 2005 or our
consolidated statement of operations for each of the three years in the period
ended December 30, 2006.
The adjustment to accumulated other comprehensive
loss upon the adoption of SFAS No. 158 represents the net unrecognized
actuarial losses, unrecognized prior service costs (credits) and unrecognized
transition obligation remaining from the initial adoption of SFAS No. 87. These
amounts were previously netted against the plans funded status in our
consolidated balance sheet. We will recognize these amounts in future periods
as net periodic pension cost pursuant to our accounting policy for amortizing
such amounts.
In addition, with the adoption of this Statement,
actuarial gains and losses that are not immediately recognized as net periodic
pension cost will be recognized as a component of other comprehensive loss and
amortized into net periodic pension cost in future periods.
60
Periodic Benefit Cost (Income)
The components of our net periodic benefit cost
(income) and other amounts we recognized in other comprehensive income are as
follows:
|
|
Pension Benefits
|
|
Postretirement Benefits
Other Than Pensions
|
|
(In millions)
|
|
2006
|
|
2005
|
|
2004
|
|
2006
|
|
2005
|
|
2004
|
|
Net
periodic benefit cost (income):
|
|
|
|
|
|
|
|
|
|
|
|
|
|
Service cost
|
|
$
|
142
|
|
$
|
129
|
|
$
|
106
|
|
$
|
10
|
|
$
|
9
|
|
$
|
8
|
|
Interest cost
|
|
283
|
|
271
|
|
265
|
|
40
|
|
37
|
|
37
|
|
Expected return on plan assets
|
|
(386
|
)
|
(387
|
)
|
(400
|
)
|
|
|
|
|
|
|
Amortization of unrecognized transition asset
|
|
1
|
|
1
|
|
1
|
|
|
|
|
|
|
|
Amortization of prior service cost (credit)
|
|
19
|
|
18
|
|
16
|
|
(5
|
)
|
(6
|
)
|
(9
|
)
|
Amortization of net loss
|
|
44
|
|
35
|
|
7
|
|
19
|
|
13
|
|
9
|
|
Net periodic benefit cost (income)
|
|
$
|
103
|
|
$
|
67
|
|
$
|
(5
|
)
|
$
|
64
|
|
$
|
53
|
|
$
|
45
|
|
Other
changes in plan assets and benefit obligations recognized in other
comprehensive loss (including foreign exchange):
|
|
|
|
|
|
|
|
|
|
|
|
|
|
Net loss (gain)
|
|
$
|
538
|
|
$
|
(49
|
)
|
$
|
95
|
|
$
|
246
|
|
$
|
|
|
$
|
|
|
Prior service cost (credit)
|
|
160
|
|
|
|
|
|
(12
|
)
|
|
|
|
|
Total recognized in other comprehensive loss
|
|
$
|
698
|
|
$
|
(49
|
)
|
$
|
95
|
|
$
|
234
|
|
$
|
|
|
$
|
|
|
Total recognized in net
periodic benefit cost (income) and other comprehensive loss
|
|
$
|
801
|
|
$
|
18
|
|
$
|
90
|
|
$
|
298
|
|
$
|
53
|
|
$
|
45
|
|
We estimate that the net loss and prior service cost
for the defined benefit pension plans that will be amortized from other
comprehensive income into net periodic benefit costs in 2007 will be $47 million
and $18 million, respectively. The estimated net loss and prior service credit
for postretirement benefits other than pensions that will be amortized from
other comprehensive income into net periodic benefit costs in 2007 will be $22
million and $(5) million, respectively.
Obligations and Funded Status
The changes in the projected benefit obligation and
in the fair value of plan assets, along with our funded status are as follows:
|
|
Pension Benefits
|
|
Postretirement Benefits
Other Than Pensions
|
|
(In millions)
|
|
2006
|
|
2005
|
|
2006
|
|
2005
|
|
Change
in benefit obligation:
|
|
|
|
|
|
|
|
|
|
Benefit
obligation at beginning of year
|
|
$
|
5,119
|
|
$
|
4,931
|
|
$
|
744
|
|
$
|
658
|
|
Service cost
|
|
142
|
|
129
|
|
10
|
|
9
|
|
Interest cost
|
|
283
|
|
271
|
|
40
|
|
37
|
|
Amendments
|
|
18
|
|
16
|
|
6
|
|
1
|
|
Plan participants
contributions
|
|
3
|
|
3
|
|
5
|
|
5
|
|
Actuarial losses
|
|
39
|
|
97
|
|
12
|
|
108
|
|
Benefits paid
|
|
(288
|
)
|
(277
|
)
|
(67
|
)
|
(73
|
)
|
Foreign exchange
rate changes
|
|
66
|
|
(51
|
)
|
|
|
(1
|
)
|
Benefit obligation at end of year
|
|
$
|
5,382
|
|
$
|
5,119
|
|
$
|
750
|
|
$
|
744
|
|
Change
in fair value of plan assets:
|
|
|
|
|
|
|
|
|
|
Fair value of
plan assets at beginning of year
|
|
$
|
4,746
|
|
$
|
4,537
|
|
$
|
|
|
$
|
|
|
Actual return on
plan assets
|
|
595
|
|
506
|
|
|
|
|
|
Employer
contributions
|
|
33
|
|
20
|
|
|
|
|
|
Plan
participants contributions
|
|
3
|
|
3
|
|
|
|
|
|
Benefits paid
|
|
(288
|
)
|
(277
|
)
|
|
|
|
|
Foreign exchange
rate changes
|
|
58
|
|
(43
|
)
|
|
|
|
|
Fair value of plan assets at end of year
|
|
$
|
5,147
|
|
$
|
4,746
|
|
$
|
|
|
$
|
|
|
Funded status at end of
year
|
|
$
|
(235
|
)
|
$
|
(373
|
)
|
$
|
(750
|
)
|
$
|
(744
|
)
|
61
Amounts recognized in the
balance sheets are as follows:
|
|
Pension Benefits
|
|
Postretirement Benefits
Other Than Pensions
|
|
(In millions)
|
|
2006
|
|
2005
|
|
2006
|
|
2005
|
|
Non-current assets
|
|
$
|
294
|
|
$
|
906
|
|
$
|
|
|
$
|
|
|
Current liabilities
|
|
(13
|
)
|
|
|
(79
|
)
|
|
|
Non-current liabilities
|
|
(516
|
)
|
(326
|
)
|
(671
|
)
|
(515
|
)
|
Amounts recognized in
accumulated other comprehensive income (loss):
|
|
|
|
|
|
|
|
|
|
Net loss
|
|
748
|
|
210
|
|
246
|
|
|
|
Prior service cost
(credit)
|
|
160
|
|
|
|
(12
|
)
|
|
|
|
|
|
|
|
|
|
|
|
|
|
|
|
|
Assumptions
The weighted-average
assumptions and the healthcare trend assumptions we used for our postretirement
plans are as follows:
|
|
Pension Benefits
|
|
Postretirement Benefits
Other Than Pensions
|
|
|
|
2006
|
|
2005
|
|
2004
|
|
2006
|
|
2005
|
|
2004
|
|
Net periodic benefit cost
(income):
|
|
|
|
|
|
|
|
|
|
|
|
|
|
Discount rate
|
|
5.55
|
%
|
5.69
|
%
|
6.17
|
%
|
5.66
|
%
|
5.78
|
%
|
6.31
|
%
|
Expected long-term rate
of return on assets
|
|
8.54
|
%
|
8.57
|
%
|
8.72
|
%
|
|
|
|
|
|
|
Rate of compensation
increase
|
|
4.36
|
%
|
4.35
|
%
|
4.33
|
%
|
|
|
|
|
|
|
Benefit obligations at
year-end:
|
|
|
|
|
|
|
|
|
|
|
|
|
|
Discount rate
|
|
5.57
|
%
|
5.55
|
%
|
5.69
|
%
|
5.67
|
%
|
5.66
|
%
|
5.78
|
%
|
Rate of compensation
increases
|
|
4.38
|
%
|
4.36
|
%
|
4.35
|
%
|
|
|
|
|
|
|
Healthcare cost trend rates:
|
|
|
|
|
|
|
|
|
|
|
|
|
|
Initial medical drug
rate*
|
|
|
|
|
|
|
|
8.0
|
%
|
11.0
|
%
|
10.0
|
%
|
Initial prescription drug rate*
|
|
|
|
|
|
|
|
12.0
|
%
|
11.0
|
%
|
|
|
* For 2006, we estimate that
the medical cost trend rate will decline to 5% for 2009 and thereafter, and the
prescription drug cost trend rate will decline to 5% for 2013 and thereafter.
Assumed healthcare cost trend rates have a
significant effect on the amounts reported for the postretirement benefits
other than pensions. A one-percentage-point change in assumed healthcare cost
trend rates would have the following effects:
|
|
One-
|
|
One-
|
|
|
|
Percentage-
|
|
Percentage-
|
|
|
|
Point
|
|
Point
|
|
(In millions)
|
|
Increase
|
|
Decrease
|
|
Effect on total
of service and interest cost components
|
|
$
|
4
|
|
$
|
(4
|
)
|
Effect on
postretirement benefit obligations other than pensions
|
|
$
|
54
|
|
$
|
(47
|
)
|
Pension Benefits
The accumulated benefit obligation for all defined
benefit pension plans was $4.9 billion at December 30, 2006 and $4.7 billion at
December 31, 2005. Pension plans with accumulated benefit obligations exceeding
the fair value of plan assets were as follows:
(In millions)
|
|
2006
|
|
2005
|
|
Projected
benefit obligation
|
|
$
|
862
|
|
$
|
2,202
|
|
Accumulated
benefit obligation
|
|
$
|
737
|
|
$
|
1,949
|
|
Fair value of plan
assets
|
|
$
|
433
|
|
$
|
1,643
|
|
62
In addition to the plans in the above table, we have
plans with the projected benefit obligation in excess of the fair value of plan
assets at year-end as follows:
(In millions)
|
|
2006
|
|
2005
|
|
Projected
benefit obligation
|
|
$
|
1,449
|
|
$
|
|
|
Accumulated
benefit obligation
|
|
$
|
1,336
|
|
$
|
|
|
Fair value of plan
assets
|
|
$
|
1,350
|
|
$
|
|
|
Pension Assets
We invest our pension assets with the objective of
achieving a total rate of return, over the long term, sufficient to fund future
pension obligations and to minimize future pension contributions. We are
willing to tolerate a commensurate level of risk to achieve this objective
based on the funded status of the plans and the long-term nature of our pension
liability. Risk is controlled by maintaining a portfolio of assets that is
diversified across a variety of asset classes, investment styles and investment
managers. All of the assets are managed by external investment managers, and
the majority of the assets are actively managed. Where possible, investment
managers are prohibited from owning our stock in the portfolios that they
manage on our behalf.
For U.S. plan assets, comprising the majority of plan
assets, asset allocation target ranges were established consistent with the
investment objectives, and the assets are rebalanced periodically. The expected
long-term rate of return on plan assets was determined based on a variety of
considerations, including the established asset allocation targets and
expectations for those asset classes, historical returns of the plans assets
and the advice of outside advisors. At December 30, 2006, the target allocation
range is 44% to 70% for equity securities, 13% to 33% for debt securities and
7% to 13% for each of real estate and other alternative assets. For foreign
plan assets, allocations are based on expected cash flow needs and assessments
of the local practices and markets. The percentages of the fair value of total
pension plan assets by major category are as follows:
|
|
December 30,
|
|
December 31,
|
|
Asset Category
|
|
2006
|
|
2005
|
|
Equity
securities
|
|
59
|
%
|
58
|
%
|
Debt securities
|
|
22
|
%
|
23
|
%
|
Real estate
|
|
10
|
%
|
9
|
%
|
Other
|
|
9
|
%
|
10
|
%
|
Total
|
|
100
|
%
|
100
|
%
|
Estimated Future Cash Flow Impact
Defined benefits under salaried plans are based on
salary and years of service. Hourly plans generally provide benefits based on
stated amounts for each year of service. Our funding policy is consistent with
applicable laws and regulations. In 2007, we expect to contribute in the range
of $45 million to $50 million to fund our qualified pension plans. We do not
expect to contribute to our other postretirement benefit plans. The benefit
payments provided below reflect expected future employee service, as appropriate,
that are expected to be paid, net of estimated participant contributions. The
benefit payments are based on the same assumptions used to measure our benefit
obligation at the end of fiscal 2006. While pension benefit payments primarily
will be paid out of qualified pension trusts, we will pay postretirement
benefits other than pensions out of our general corporate assets as follows:
|
|
|
|
Post-
|
|
|
|
|
|
|
|
retirement
|
|
Expected
|
|
|
|
|
|
Benefits
|
|
Medicare
|
|
|
|
Pension
|
|
Other Than
|
|
Part D
|
|
(In millions)
|
|
Benefits
|
|
Pensions
|
|
Subsidy
|
|
2007
|
|
$
|
292
|
|
$
|
79
|
|
$
|
(6
|
)
|
2008
|
|
298
|
|
75
|
|
(6
|
)
|
2009
|
|
305
|
|
76
|
|
(6
|
)
|
2010
|
|
311
|
|
77
|
|
(7
|
)
|
2011
|
|
316
|
|
77
|
|
(7
|
)
|
2012 - 2016
|
|
1,792
|
|
352
|
|
(34
|
)
|
|
|
|
|
|
|
|
|
|
|
|
63
Note 13. Income Taxes
We file a consolidated federal income tax return for
all of our U.S. subsidiaries and separate returns for our foreign subsidiaries.
Income from continuing operations before income taxes is as follows:
(In millions)
|
|
2006
|
|
2005
|
|
2004
|
|
United States
|
|
$
|
796
|
|
$
|
574
|
|
$
|
333
|
|
Foreign
|
|
179
|
|
165
|
|
207
|
|
Total
|
|
$
|
975
|
|
$
|
739
|
|
$
|
540
|
|
Income tax expense for continuing operations is
summarized as follows:
(In millions)
|
|
2006
|
|
2005
|
|
2004
|
|
Current:
|
|
|
|
|
|
|
|
Federal
|
|
$
|
152
|
|
$
|
128
|
|
$
|
49
|
|
State
|
|
8
|
|
17
|
|
2
|
|
Foreign
|
|
43
|
|
26
|
|
59
|
|
|
|
203
|
|
171
|
|
110
|
|
Deferred:
|
|
|
|
|
|
|
|
Federal
|
|
44
|
|
64
|
|
59
|
|
State
|
|
28
|
|
(7
|
)
|
9
|
|
Foreign
|
|
(6
|
)
|
(5
|
)
|
(13
|
)
|
|
|
66
|
|
52
|
|
55
|
|
Income tax expense
|
|
$
|
269
|
|
$
|
223
|
|
$
|
165
|
|
The following table reconciles the federal statutory
income tax rate to our effective income tax rate:
|
|
2006
|
|
2005
|
|
2004
|
|
Federal
statutory income tax rate
|
|
35.0
|
%
|
35.0
|
%
|
35.0
|
%
|
Increase
(decrease) in taxes resulting from:
|
|
|
|
|
|
|
|
Valuation allowance on contingent receipts
|
|
|
|
2.1
|
|
|
|
State income taxes
|
|
2.3
|
|
0.9
|
|
1.3
|
|
Special foreign dividend
|
|
|
|
0.1
|
|
2.1
|
|
Favorable tax settlements
|
|
(2.4
|
)
|
|
|
|
|
Canadian dollar functional currency
|
|
(1.2
|
)
|
|
|
|
|
Foreign tax rate differential
|
|
(2.7
|
)
|
(5.0
|
)
|
(4.8
|
)
|
Export sales benefit
|
|
(0.8
|
)
|
(1.1
|
)
|
(1.0
|
)
|
Other, net
|
|
(2.6
|
)
|
(1.8
|
)
|
(2.0
|
)
|
Effective income tax
rate
|
|
27.6
|
%
|
30.2
|
%
|
30.6
|
%
|
The amount of income taxes we pay is subject to
ongoing audits by federal, state and foreign tax authorities, which may result
in proposed assessments. Our estimate for the potential outcome for any
uncertain tax issue is highly judgmental. We believe we have adequately
provided for any reasonably foreseeable outcome related to these matters.
However, our future results may include favorable or unfavorable adjustments to
our estimated tax liabilities due to closure of income tax examinations, new
regulatory or judicial pronouncements, or other relevant events. As a result,
our effective tax rate may fluctuate significantly on a quarterly basis.
64
The tax effects of temporary differences that give
rise to significant portions of our net deferred tax assets and liabilities
were as follows:
|
|
December 30,
|
|
December 31,
|
|
(In millions)
|
|
2006
|
|
2005
|
|
Deferred
tax assets:
|
|
|
|
|
|
Deferred revenue
|
|
$
|
16
|
|
$
|
18
|
|
Warranty and product maintenance reserves
|
|
115
|
|
109
|
|
Self-insured liabilities, including environmental
|
|
97
|
|
83
|
|
Deferred compensation
|
|
190
|
|
170
|
|
Allowance for credit losses
|
|
57
|
|
59
|
|
Amortization of goodwill and other intangibles
|
|
|
|
22
|
|
Loss carryforwards
|
|
79
|
|
45
|
|
Obligation for postretirement benefits
|
|
330
|
|
6
|
|
Foreign currency debt
|
|
21
|
|
|
|
Other, principally timing of other expense deductions
|
|
147
|
|
157
|
|
Total deferred tax assets
|
|
1,052
|
|
669
|
|
Valuation
allowance for deferred tax assets
|
|
(159
|
)
|
(116
|
)
|
|
|
$
|
893
|
|
$
|
553
|
|
Deferred
tax liabilities:
|
|
|
|
|
|
Finance group transactions, principally leasing
|
|
$
|
(597
|
)
|
$
|
(525
|
)
|
Property, plant and equipment, principally
depreciation
|
|
(76
|
)
|
(94
|
)
|
Inventory
|
|
(53
|
)
|
(62
|
)
|
Amortization of goodwill and other intangibles
|
|
(19
|
)
|
|
|
Foreign currency debt
|
|
|
|
(10
|
)
|
Total deferred tax liabilities
|
|
(745
|
)
|
(691
|
)
|
Net deferred tax asset
(liability)
|
|
$
|
148
|
|
$
|
(138
|
)
|
We have recognized a valuation allowance at December
30, 2006 and December 31, 2005 of $159 million and $116 million, respectively,
to offset certain deferred tax assets due to the uncertainty of realizing the
related benefits.
We have net operating loss and credit carryforwards
at the end of each year as follows:
|
|
December 30,
|
|
December 31,
|
|
(In millions)
|
|
2006
|
|
2005
|
|
Non-U.S. net
operating loss carryforwards with no expiration
|
|
$
|
146
|
|
$
|
78
|
|
Non-U.S. net
operating loss carryforwards expiring through 2021
|
|
$
|
15
|
|
$
|
17
|
|
Federal credit
carryforwards beginning to expire in 2015 discontinued operations
|
|
$
|
60
|
|
$
|
18
|
|
Federal and state
credit carryforwards beginning to expire in 2015
|
|
$
|
11
|
|
$
|
5
|
|
Our income taxes payable for federal and state purposes
have been reduced by the tax benefits we receive from employee stock options.
The income tax benefits we receive for certain stock options are calculated as
the difference between the fair market value of the stock issued at the time of
exercise and the option price, tax effected. See Note 11 for the net tax
benefits to employee stock options.
The undistributed earnings of our foreign
subsidiaries approximated $376 million at the end of 2006. We consider the
undistributed earnings on which taxes have not previously been provided to be
indefinitely reinvested; therefore, tax is not provided on these earnings. If
the earnings on which tax has not been provided had been distributed in 2006,
our taxes, net of foreign tax credits, would have increased by approximately
$19 million.
On October 22, 2004, the American Jobs Creation Act (AJCA)
was signed into law and includes a deduction of 85% of certain foreign earnings
that are repatriated, as defined in the AJCA. During 2005, we repatriated $435
million in cash from foreign subsidiaries under this provision related to
continuing operations. Tax expense of $0.9 million and $11 million was
recognized in 2005 and 2004, respectively, related to this repatriation. In
addition, we repatriated approximately $183 million in cash related to
discontinued operations and recorded related tax expense of $2 million in 2005.
65
Note 14. Special Charges
Special charges totaled $118 million for 2005 and
included $112 million in charges related to the 2001 disposition of the Automotive
Trim business (Trim) and $6 million in restructuring expense in the
Industrial segment. In 2004, special charges totaled $59 million and included
$71 million in restructuring expense principally in the Industrial segment,
partially offset by a $12 million gain on the sale of common stock acquired in
connection with the Trim disposition.
In connection with the disposition of Trim to
subsidiaries of C&A, we acquired preferred stock in C&A Products Co. (C&A
Products) and C&A common stock. In the first quarter of 2005, we recorded
a $52 million impairment charge to write down the preferred stock based on an
agreement to sell the stock to a third party. In the second quarter of 2005,
based on C&A Products filing for Chapter 11 bankruptcy protection and
relevant market considerations, we wrote off the remaining book value of the
preferred stock of $39 million.
In connection with the Trim disposition, our Finance
group has recourse to our Manufacturing group for equipment leases with the
subsidiaries of C&A. The outstanding balance on these leases totaled
approximately $61 million at December 30, 2006. Based on uncertainties related
to these leases, our Manufacturing group recorded a $10 million reserve to
special charges in the fourth quarter of 2005.
Certain other operating leases were transferred and
assigned to subsidiaries of C&A upon the sale of Trim. As discussed in Note
17, we guaranteed C&As payments under these operating leases and for an
environmental matter. In the fourth quarter of 2005, based on C&As failure
to pay certain leases, as well as the negotiations entered into at the time for
the sale of C&As European operations, we recorded an $11 million charge to
cover our exposure under these leases, along with certain environmental and workers
compensation matters.
Restructuring Our company-wide restructuring program was
substantially completed at the end of 2005. We approved and committed to a
restructuring program in the fourth quarter of 2000 to improve returns at core
businesses and to complete the integration of certain acquisitions. This
program subsequently was expanded as part of our strategic effort to improve
operating efficiencies. This restructuring program included corporate and
segment direct and indirect workforce reductions, consolidation of facilities,
rationalization of certain product lines, outsourcing of non-core production
activity, the divestiture of non-core businesses, and the streamlining of sales
and administrative overhead. Under this program, we reduced our workforce by
approximately 8,000 employees from continuing operations, representing
approximately 19% of our global workforce since the program was first
announced, and closed 85 facilities.
Since inception of this program through December 31,
2005, we incurred total program costs of $306 million, which is composed of
$164 million in severance costs, $44 million in contract termination costs, $34
million in asset impairment charges (net of gains on the sale of fixed assets)
and $64 million in other associated costs. Total program costs incurred by
segment include $219 million in the Industrial segment, $38 million in the
Cessna segment, $29 million in the Bell segment, $9 million in the Finance
segment and $11 million at Corporate.
An analysis of restructuring reserves is summarized
below:
|
|
|
|
|
|
|
|
Other
|
|
|
|
|
|
Severance
|
|
Contract
|
|
Fixed Asset
|
|
Associated
|
|
|
|
(In millions)
|
|
Costs
|
|
Terminations
|
|
Impairments
|
|
Costs
|
|
Total
|
|
Balance at
January 3, 2004
|
|
$
|
9
|
|
$
|
2
|
|
$
|
|
|
$
|
|
|
$
|
11
|
|
Additions
|
|
30
|
|
37
|
|
4
|
|
6
|
|
77
|
|
Reserves deemed
unnecessary
|
|
(2
|
)
|
|
|
|
|
|
|
(2
|
)
|
Gains on sale of
fixed assets
|
|
|
|
|
|
(4
|
)
|
|
|
(4
|
)
|
Cash paid
|
|
(25
|
)
|
(3
|
)
|
|
|
(6
|
)
|
(34
|
)
|
Balance at
January 1, 2005
|
|
$
|
12
|
|
$
|
36
|
|
$
|
|
|
$
|
|
|
$
|
48
|
|
Additions
|
|
2
|
|
|
|
|
|
4
|
|
6
|
|
Cash paid
|
|
(11
|
)
|
(2
|
)
|
|
|
(4
|
)
|
(17
|
)
|
Balance at December 31,
2005
|
|
$
|
3
|
|
$
|
34
|
|
$
|
|
|
$
|
|
|
$
|
37
|
|
During 2006, our restructuring reserves were reduced
to $30 million by cash payments and immaterial refinements to previous
estimates. The remaining reserve primarily is related to contract termination costs
for one lease in the Industrial segment, which will be paid out over the next
13 years.
66
Note 15. Commitments and
Contingencies
We are subject to legal proceedings and other claims
arising out of the conduct of our business, including proceedings and claims
relating to private sector transactions; government contracts; compliance with
applicable laws and regulations; production partners; product liability;
employment; and environmental, safety and health matters. Some of these legal
proceedings and claims seek damages, fines or penalties in substantial amounts
or remediation of environmental contamination. As a government contractor, we
are subject to audits, reviews and investigations to determine whether our
operations are being conducted in accordance with applicable regulatory
requirements. Under federal government procurement regulations, certain claims
brought by the U.S. Government could result in our being suspended or debarred
from U.S. Government contracting for a period of time. On the basis of
information presently available, we do not believe that existing proceedings
and claims will have a material effect on our financial position or results of
operations.
In connection with the 2002 recall of certain of our
Lycoming turbocharged airplane engines, a former third-party supplier filed a
lawsuit against Lycoming claiming that the former supplier had been wrongly
blamed for aircraft engine failures resulting from its crankshaft forging
process and that Lycomings design was the cause of the engine failures. In
February 2005, a jury returned a verdict against Lycoming for $86 million in
punitive damages, $2.7 million in expert fees and $1.7 million in increased
insurance costs. The jury also found that the former suppliers claim that it
had incurred $5.3 million in attorneys fees was reasonable. Judgment was
entered on the verdict on March 29, 2005, awarding the former supplier $9.7
million in alleged compensatory damages and attorneys fees and $86 million in
alleged punitive damages. While the ultimate outcome of the litigation cannot
be assured, management strongly disagrees with the verdict and believes that it
is probable that it will be reversed through the appellate process.
During the fourth quarter of 2005, we developed a
plan to institute a retirement program for approximately 5,100 crankshafts,
representing the remaining crankshafts manufactured by the former supplier
using the same forging technique as the crankshafts covered by prior service
bulletins. A service bulletin was issued in the first quarter of 2006
implementing this plan, which requires the retirement of an affected crankshaft
at the next crankshaft access or scheduled overhaul, whichever occurs first,
but not to exceed three years from the issuance of the service bulletin. On
September 29, 2006, the U.S. Federal Aviation Administration issued an
Airworthiness Directive requiring compliance within 12 years of that date, or
the next access. These crankshafts have not been the subject of a recall. As of
December 30, 2006, reserves to cover costs for this program totaled $9 million.
The Internal Revenue Service (IRS) has challenged
both the ability to accelerate the timing of tax deductions and the amounts of
those deductions related to certain leveraged lease transactions within the
Finance segment. These transactions, along with other transactions with similar
characteristics, have an initial investment of approximately $209 million.
Resolution of these issues may result in an adjustment to the timing of taxable
income and deductions that reduce the effective yield of the leveraged lease
transactions. In addition, resolution of these issues could result in the
acceleration of cash payments to the IRS. At December 30, 2006, $182 million of
deferred tax liabilities are recorded on our consolidated balance sheets
related to these leases. We believe that the proposed IRS adjustments are
inconsistent with the tax law in existence at the time the leases were
originated and intend to vigorously defend our position.
Armed Reconnaissance Helicopter
Program
The Armed Reconnaissance Helicopter (ARH) System
Development and Demonstration (SDD) contract is a cost plus incentive fee
contract under which our eligibility for fees is reduced as total contract
costs increase. During 2006, we continued our development activities for this
program and expensed $14 million in unreimbursed costs related to this effort.
We continue to work with the U.S. Government on development issues,
configuration changes and schedule requirements. We no longer are eligible to
earn fees under this contract; however, we anticipate that any subsequent cost
increases are reimbursable by the U.S. Government.
The U.S. Government had two firm fixed-price options under
this program, representing the first two LRIP lots for the delivery of 24 to 48
aircraft. Certain development
requirements under the ARH SDD contract must be met before the U.S. Government
can exercise the options. We presently
anticipate that the development requirements will be met in mid-2007. The option for the first LRIP lot (for 6-12
aircraft) has expired, while the option for the second lot (for 18-36 aircraft)
expires in December 2007.
In the fourth quarter of 2006, we completed certain
phases of the critical design review under the ARH SDD contract and determined
the initial production configuration of the aircraft, which includes aircraft
configuration changes required by the U.S. Government. Our cost estimates based
on this configuration, which include anticipated transition to production
costs, exceed the fixed pricing contained in the options. We currently are in
discussions with the U.S. Government related to the possible reinstatement of
the ARH Lot 1 option, extension of the options, delivery schedule, number of
units to be exercised under the options and possible additional aircraft to be
contracted, in addition to those under the options, at
67
revised pricing. We also are reviewing our ability to
claim equitable adjustment recovery from the U.S. Government related to certain
costs that potentially could be incurred related to the exercise of these
options.
Depending on the results of the SDD contract, our
cost-containment efforts, the availability of U.S. Government funding, the
number of aircraft exercised or ultimately contracted for, and the resolution
of our discussions with the U.S. Government, we currently estimate that it is
reasonably possible that our exposure could be in the range of no loss to a
possible loss of $4 million per aircraft. This estimate excludes the impact of
discussions with the U.S. Government or any potential recoveries including
claims for equitable adjustment under the contracts. Due to the uncertainty of
this exposure and the ultimate outcome of our discussions, we do not believe
that a loss is probable under the guidelines established by SFAS No.5, Accounting
for Contingencies. Accordingly, we have not established a reserve at December
30, 2006.
Environmental Remediation
As with other industrial enterprises engaged in
similar businesses, we are involved in a number of remedial actions under
various federal and state laws and regulations relating to the environment that
impose liability on companies to clean up, or contribute to the cost of
cleaning up, sites on which hazardous wastes or materials were disposed or
released. Expenditures to evaluate and remediate contaminated sites
approximated $7 million, $6 million and $6 million in 2006, 2005 and 2004,
respectively.
We estimate our accrued environmental liabilities
using currently available facts, existing technology, and presently enacted
laws and regulations, which all are subject to a number of factors and
uncertainties. Our accrued liabilities relate to disposal costs, U.S.
Environmental Protection Agency oversight costs, legal fees, and operating and
maintenance costs for both currently and formerly owned or operated facilities.
Circumstances that can affect the reliability and precision of the accruals
include the identification of additional sites, environmental regulations,
level of cleanup required, technologies available, number and financial
condition of other contributors to remediation, and the time period over which
remediation may occur. We believe that any changes to the accruals that may
result from these factors and uncertainties will not have a material effect on
our financial position or results of operations. Based upon information
currently available, we estimate that our potential environmental liabilities
are within the range of $51 million to $168 million. At the end of 2006,
environmental reserves of approximately $85 million, of which $10 million are
classified as current liabilities, have been established to address these
specific estimated potential liabilities. We estimate that we will likely pay
our accrued environmental remediation liabilities over the next five to 10
years.
Leases
Rental expense approximated $89 million for each year
in 2006, 2005 and 2004. Future minimum rental commitments for noncancelable
operating leases in effect at the end of 2006 approximated $63 million for
2007, $54 million for 2008, $46 million for 2009, $39 million for 2010, $31
million for 2011 and a total of $202 million thereafter.
Loan Commitments
At December 30, 2006, our Finance group had unused
commitments to fund new and existing customers under $1.3 billion of committed
revolving lines of credit, compared with $1.2 billion at December 31, 2005.
These loan commitments generally have an original duration of less than three
years and do not necessarily represent future cash requirements, since many of
the agreements will not be used to the extent committed or will expire unused.
We are not exposed to interest rate changes on these commitments since the
interest rates are not set until the loans are funded.
Note 16. Research and Development
Company-funded and customer-funded research and
development costs are as follows:
(In millions)
|
|
2006
|
|
2005
|
|
2004
|
|
Company-funded
|
|
$
|
351
|
|
$
|
326
|
|
$
|
291
|
|
Customer-funded
|
|
435
|
|
366
|
|
283
|
|
Total research and
development
|
|
$
|
786
|
|
$
|
692
|
|
$
|
574
|
|
Our customer-funded research and development costs
primarily are related to U.S. Government contracts, including the ARH, V-22 and
H-1 development contracts.
As part of the realignment of Bell/Agusta Aerospace
Company LLC (BAAC) (see Note 18), Bell Helicopter, Agusta S.p.A. and two of
its affiliated companies (collectively, Agusta) agreed to share certain Model
BA609 development costs. On behalf of BAAC, Agusta will incur development costs
to enhance its investment in BAAC. We record these development costs in consolidation
as research and development expense, with a credit to minority interest for
Agustas share. Agusta also may make cash contributions to reimburse portions
of Bell Helicopters development
68
costs incurred on behalf of BAAC. Based on
development costs incurred, Bell Helicopter received $19 million and $43
million in cash contributions from Agusta, which were recorded in income in
2006 and 2005, respectively.
During 2005, Bell Helicopter entered into four
separate risk-sharing arrangements. Two of the arrangements are with commercial
participants in the development of the Bell Model 429 aircraft. The
arrangements require contributions from the participants totaling $20 million,
which are due once the development effort reaches certain predetermined milestones,
as well as in-kind development contributions from one participant. The other
two arrangements are with Canadian governmental organizations. These
arrangements, which currently include the Model 429 aircraft and may
potentially include certain future aircraft, each require cash contributions of
up to CAD 115 million from the participants, based on a percentage of
qualifying research and development costs incurred.
Each of the participants under these arrangements is
entitled to payments from Bell Helicopter, with the commercial participants
also entitled to discounts, based on future sales of the Model 429 aircraft. In
addition, there are certain requirements related to production of future Model
429 aircraft in Canada, and one of the commercial participants is entitled to
perform certain manufacturing functions for the Model 429 aircraft. Based on
the development activities completed and costs incurred, we have recorded
income of $22 million in 2006 and $35 million in 2005 related to these arrangements.
In 2006 and 2005, we received, or were due to
receive, $41 million and $78 million, respectively, in cost reimbursements of
company-funded amounts from our risk-sharing partners. Based on these
reimbursements, our net company-funded costs totaled $310 million in 2006 and
$248 million in 2005.
Note 17. Guarantees and
Indemnifications
We extend a variety of financial and performance
guarantees to third parties as provided in the table below:
|
|
December 30, 2006
|
|
December 31, 2005
|
|
|
|
Maximum
|
|
Carrying
|
|
Maximum
|
|
Carrying
|
|
|
|
Potential
|
|
Amount of
|
|
Potential
|
|
Amount of
|
|
(In millions)
|
|
Payment*
|
|
Liability
|
|
Payment*
|
|
Liability
|
|
Manufacturing
group:
|
|
|
|
|
|
|
|
|
|
Performance
guarantee
|
|
$
|
227
|
|
$
|
|
|
$
|
114
|
|
$
|
|
|
Guaranteed
minimum resale contracts
|
|
30
|
|
3
|
|
31
|
|
3
|
|
Guarantees
related to dispositions
|
|
46
|
|
23
|
|
29
|
|
8
|
|
Debt obligations
of joint ventures
|
|
4
|
|
|
|
10
|
|
|
|
Finance
group:
|
|
|
|
|
|
|
|
|
|
Loss-sharing agreements
|
|
$
|
29
|
|
$
|
|
|
$
|
71
|
|
$
|
13
|
|
* These agreements include uncapped
guarantees as described below.
Performance Guarantee
In 2004, through our Bell Helicopter business, we
formed AgustaWestlandBell LLC (AWB LLC) with AgustaWestland North America
Inc. (AWNA). This venture was created for the joint design, development,
manufacture, sale, customer training and product support of the VH-71
helicopter, and certain variations and derivatives thereof, to be offered and
sold to departments or agencies of the U.S. Government. In March 2005, AWB LLC
received a $1.2 billion cost reimbursement-type subcontract from Lockheed
Martin for the System Development and Demonstration phase of the U.S. Marine
Corps Helicopter Squadron Program. We guaranteed to Lockheed Martin the due and
prompt performance by AWB LLC of all its obligations under this subcontract,
provided that our liability under the guaranty shall not exceed 49% of AWB LLCs
aggregate liability to Lockheed Martin under the subcontract. AgustaWestland
N.V., AWNAs parent company, has guaranteed the remaining 51% to Lockheed
Martin. We have entered into cross-indemnification agreements with
AgustaWestland N.V. in which each party indemnifies the other related to any
payments required under these agreements that result from the indemnifying
partys workshare under any subcontracts received.
For 2006, AWB LLCs maximum obligation was 40% of the
total contract value, which equates to $464 million based on the current
contract value of $1.2 billion. In 2007 and thereafter, AWB LLCs maximum
obligation increases to 50%, or $580 million. Accordingly, the maximum amount
of our liability under the guarantee was $227 million at December 30, 2006 and
will be $284 million thereafter through completion.
69
Guaranteed Minimum Resale Contracts
We have a number of guaranteed minimum resale value
contracts associated with certain past aircraft sales. If the fair value of an
aircraft falls below a minimum guaranteed amount, we may be required to make a
future payment to the customer or provide a minimum trade-in value toward a new
aircraft. These agreements generally include operating restrictions such as
maximum usage over the contract period or minimum maintenance requirements. We
also have guaranteed the minimum resale value of certain customer-owned
aircraft anticipated to be traded in upon completion of a model currently under
development. These contracts expire as follows: $2 million in 2008, $3 million
in 2009, $3 million in 2010, $3 million in 2011 and $19 million in 2012.
Guarantees Related to Dispositions
We have guaranteed payment on certain credit
facilities and bank-issued letters of credit and guarantees of the Fastening
Systems business, where the total guarantee is capped at approximately $9
million, for which the buyer has provided a letter of credit of approximately
$4 million as collateral. We also have guaranteed payment and performance on
certain other credit facilities and leases of the Fastening Systems business
totaling approximately $14 million, where we also are liable for unpaid
interest, fees and other costs associated with claims that may arise from these
guarantees. While potential interest and fees are not capped, we have
monitoring provisions that mitigate the exposure to these additional costs. The
buyer has provided a letter of credit of approximately $9 million as collateral
on these guarantees.
We also have indemnified the purchaser of the
Fastening Systems business for remediation costs related to pre-existing
environmental conditions to the extent they exist at the sold locations. We
have estimated the fair value of these indemnifications at approximately $12
million. Potential payments under these obligations are not capped, and as a
result the maximum potential obligation cannot be determined.
In connection with the disposition of Trim to
subsidiaries of C&A, certain equipment and operating leases were transferred
and assigned to subsidiaries of C&A. We guaranteed C&As payments under
these leases and for an environmental matter.
We also have obligations arising from sales of
certain other businesses, including representations and warranties and related
indemnities for environmental, health and safety, and tax and employment
matters. The maximum potential payment related to these obligations is not a
specified amount as a number of the obligations do not contain financial caps.
Loss-Sharing Agreements
In connection with the sale of a note receivable in
2005, our Finance group has indemnified the purchaser against potential losses
in limited circumstances. The maximum potential exposure of the indemnity is
estimated to be $29 million, but due to the extremely low probability of
occurrence and several other mitigating factors, including a specific
indemnification from the original note issuer, no significant fair value has
been attributed to the indemnity.
In connection with the sale of the Small Business
Direct financing business in 2003, our Finance group entered into a
loss-sharing agreement. This agreement required us to reimburse the purchaser
for 50% of losses incurred on the portfolio above a 4% annual level. A
liability of $14 million was originally recorded representing the estimated
fair value of the guarantee. During the fourth quarter of 2006, we entered into
a settlement agreement with the purchaser, which terminated our obligation to
reimburse the purchaser for future losses. The settlement resulted in a $1
million loss, net of tax, from discontinued operations in 2006.
At December 31, 2005, our Finance group had a
contingent liability related to the sale of equipment lease streams with a
maximum liability of $42 million. These lease streams were sold in 2006, and we
had no remaining liability at the end of 2006.
Software Indemnifications
With the acquisition of Overwatch Systems in 2006, we
now are a party to software license agreements with customers. These software
license agreements generally include certain provisions for indemnifying
customers against liabilities if our software products infringe a third partys
intellectual property rights. To date, we have not incurred any material costs
as a result of such indemnifications and have not accrued any liabilities
related to such obligations in our consolidated financial statements.
Forward Contract
We enter into a forward contract in our common stock
on an annual basis. The contract is intended to hedge the earnings and cash
volatility of stock-based incentive compensation indexed to our stock. The
forward contract requires annual cash settlement between the counterparties
based upon a number of shares multiplied by the difference between the strike
price and the prevailing common stock price. As of December 30, 2006, the
contract was for approximately 1.5 million shares with a strike price of
$77.62. The market price of the stock was $93.77 at December 30, 2006,
resulting in a receivable of $24 million, compared with a receivable of $10
million at December 31, 2005.
70
Warranty and Product Maintenance
Contracts
We provide limited warranty and product maintenance
programs, including parts and labor, for certain products for periods ranging
from one to five years. We estimate the costs that may be incurred under
warranty programs and record a liability in the amount of such costs at the
time product revenue is recognized. Factors that affect this liability include
the number of products sold, historical and anticipated rates of warranty
claims, and cost per claim. We assess the adequacy of our recorded warranty and
product maintenance liabilities periodically and adjust the amounts as
necessary.
Changes in our warranty and product maintenance
liability are as follows:
(In millions)
|
|
2006
|
|
2005
|
|
2004
|
|
Accrual at
beginning of year
|
|
$
|
318
|
|
$
|
280
|
|
$
|
302
|
|
Provision
|
|
189
|
|
188
|
|
146
|
|
Settlements
|
|
(167
|
)
|
(149
|
)
|
(151
|
)
|
Adjustments to
prior accrual estimates
|
|
(25
|
)
|
(1
|
)
|
(17
|
)
|
Accrual at end of year
|
|
$
|
315
|
|
$
|
318
|
|
$
|
280
|
|
Note 18. Variable Interest Entities
BAAC is a joint venture established in 1998 between
our Bell Helicopter unit and a predecessor of Agusta S.p.A. to share certain
costs and profits for the joint design, development, manufacture, marketing,
sale, customer training and product support of the civil tiltrotor Model BA609
and, through December 2005, the commercial helicopter Model AB139. This venture
is a variable interest entity since it relies on its partners to fund the
development and to provide services for substantially all of the ventures
operations.
On December 20, 2005, we entered into an agreement
with Agusta to realign BAAC. Under this agreement, we sold our 25% profit
interest in the Model AB139 medium twin helicopter program to Agusta. Agusta
assumed ownership of all aspects of the Model AB139 program from BAAC,
including all existing customer obligations. In exchange for our interest, we
received $10 million in cash, a $20 million note and a note for contingent
payments from Agusta based on future Model AB139 sales. We recognized a $30 million
pre-tax gain upon the sale of our interest, which is included in segment
profit. The contingent receipts are expected to begin with aircraft deliveries
in 2008 and will be recorded into income prospectively as the future sales
occur.
The realignment also allows Agusta to increase its
profit interest in the Model BA609 to a maximum of 40% by increasing its
investment during the development phase. These development activities may
include cash contributions to reimburse us for certain development costs incurred
on behalf of BAAC (see Note 16). At year-end, Agustas profit interest was
approximately 30%.
Prior to the realignment, only certain marketing and
administrative costs were charged to BAAC, while development costs were
recorded separately by the parties, with our share of the development costs
charged to our earnings as a period expense. As a result of the realignment,
BAAC now includes only the Model BA609 tiltrotor, and we have a controlling
voting interest in BAAC. Accordingly, we will absorb more than half of BAACs
expected losses and residual returns. As its primary beneficiary, we have
consolidated BAAC prospectively as of December 20, 2005.
Note 19. Supplemental Cash Flow and
Other Information
Supplemental Cash Flow Information
We have made the following cash payments:
(In millions)
|
|
2006
|
|
2005
|
|
2004
|
|
Interest paid:
|
|
|
|
|
|
|
|
Manufacturing group
|
|
$
|
111
|
|
$
|
108
|
|
$
|
106
|
|
Finance group
|
|
$
|
341
|
|
$
|
204
|
|
$
|
157
|
|
Taxes paid, net
of refunds received:
|
|
|
|
|
|
|
|
Manufacturing group
|
|
$
|
173
|
|
$
|
107
|
|
$
|
(16
|
)
|
Finance group
|
|
$
|
2
|
|
$
|
22
|
|
$
|
61
|
|
Discontinued
operations
|
|
$
|
(40
|
)
|
$
|
(33
|
)
|
$
|
(16
|
)
|
71
Cash paid for interest by the Manufacturing group
includes amounts paid to our Finance group of $4 million, $5 million and $4
million in 2006, 2005 and 2004, respectively. Cash paid for the Manufacturing
group includes the excess tax benefit received on share-based payments of $31
million in 2006 and $14 million in 2005.
Accrued Liabilities
The accrued liabilities of our Manufacturing group
are composed of the following:
|
|
December 30,
|
|
December 31,
|
|
(In millions)
|
|
2006
|
|
2005
|
|
Customer
deposits
|
|
$
|
663
|
|
$
|
521
|
|
Warranty and
product maintenance contracts
|
|
315
|
|
318
|
|
Salaries, wages
and employer taxes
|
|
276
|
|
258
|
|
Deferred revenue
|
|
107
|
|
102
|
|
Accrued interest
|
|
39
|
|
37
|
|
Dividends
payable
|
|
|
|
46
|
|
Other
|
|
558
|
|
467
|
|
Total accrued
liabilities
|
|
$
|
1,958
|
|
$
|
1,749
|
|
Note 20. Segment and Geographic Data
Our four reportable segments are: Bell, Cessna,
Industrial and Finance. These segments reflect the manner in which we manage
our operations. The accounting policies of the segments are the same as those
described in Note 1.
Bell products include military and commercial
helicopters, tiltrotor aircraft, piston aircraft engines, armored security
vehicles, smart weapons, munitions airborne and ground surveillance systems,
aircraft landing systems, aircraft and missile control actuators and
networking, situational awareness and intelligence analysis software for U.S.
and non-U.S. governments in the defense and aerospace industries and general
aviation markets.
Cessna products include business jets, single engine
turboprop and piston aircraft and aftermarket services sold to a diverse base
of corporate and individual buyers.
Industrial products and markets include the following:
· Kautex products include blow-molded fuel
systems, windshield and headlamp washer systems, metal fuel fillers, engine
camshafts and other parts that are marketed primarily to automobile original
equipment manufacturers;
· E-Z-GO and Jacobsen products include golf
cars, professional turf-maintenance equipment and off-road, multipurpose
utility and specialized turf care vehicles that are marketed primarily to golf
courses, resort communities, municipalities, commercial and industrial users
and consumers;
· Greenlee products include hand, hydraulic and
electrically powered tools, wire and cable terminations, electrical and
communications testing/measurement, and bending and pulling equipment,
principally used in the electrical construction and maintenance,
telecommunications and plumbing industries; and
· Fluid & Power products include industrial
and hydraulic pumps, mechanical transmission systems, gears and extrusion
equipment marketed to original equipment manufacturers, governments, and the
oil, gas, petrochemical and desalinization industries.
Finance provides secured commercial loans and leases
primarily in North America to the asset-based lending, aviation, distribution
finance, golf finance, resort finance and structured capital markets.
Segment profit is an important measure used to
evaluate performance and for decision-making purposes. Segment profit for the
manufacturing segments excludes interest expense, certain corporate expenses
and special charges. The measurement for the Finance segment includes interest
income and expense and excludes special charges. Provisions for losses on
finance receivables involving the sale or lease of our products are recorded by
the selling manufacturing division when our Finance group has recourse to the
Manufacturing group.
72
Our revenues by segment, along with a reconciliation
of segment profit to income from continuing operations before income taxes, are
as follows:
|
|
Revenues
|
|
Segment Profit
|
|
(In millions)
|
|
2006
|
|
2005
|
|
2004
|
|
2006
|
|
2005
|
|
2004
|
|
Bell
|
|
$
|
3,408
|
|
$
|
2,881
|
|
$
|
2,254
|
|
$
|
249
|
|
$
|
368
|
|
$
|
250
|
|
Cessna
|
|
4,156
|
|
3,480
|
|
2,473
|
|
645
|
|
457
|
|
267
|
|
Industrial
|
|
3,128
|
|
3,054
|
|
3,046
|
|
163
|
|
150
|
|
194
|
|
Finance
|
|
798
|
|
628
|
|
545
|
|
210
|
|
171
|
|
139
|
|
|
|
$
|
11,490
|
|
$
|
10,043
|
|
$
|
8,318
|
|
1,267
|
|
1,146
|
|
850
|
|
Special charges
|
|
|
|
|
|
|
|
|
|
(118
|
)
|
(59
|
)
|
Corporate expenses and other, net
|
|
|
|
|
|
|
|
(202
|
)
|
(199
|
)
|
(157
|
)
|
Interest expense, net
|
|
|
|
|
|
|
|
(90
|
)
|
(90
|
)
|
(94
|
)
|
Income from
continuing operations before income taxes
|
|
|
|
|
|
|
|
$
|
975
|
|
$
|
739
|
|
$
|
540
|
|
Revenues by product type within each segment are
summarized below:
|
|
Revenues
|
|
(In millions)
|
|
2006
|
|
2005
|
|
2004
|
|
Bell:
|
|
|
|
|
|
|
|
Rotor aircraft
|
|
$
|
2,347
|
|
$
|
2,075
|
|
$
|
1,615
|
|
Armored vehicles,
advanced military systems and piston aircraft engines
|
|
1,061
|
|
806
|
|
639
|
|
Cessna: Fixed-wing aircraft
|
|
4,156
|
|
3,480
|
|
2,473
|
|
Industrial:
|
|
|
|
|
|
|
|
Fuel systems and
functional components
|
|
1,542
|
|
1,523
|
|
1,582
|
|
Golf and turf-care products
|
|
696
|
|
705
|
|
708
|
|
Industrial and
hydraulic pumps, gears and other
|
|
517
|
|
495
|
|
463
|
|
Powered tools, testing
and measurement equipment and other
|
|
373
|
|
331
|
|
293
|
|
Finance
|
|
798
|
|
628
|
|
545
|
|
|
|
$
|
11,490
|
|
$
|
10,043
|
|
$
|
8,318
|
|
Our revenues include sales to the U.S. Government of
approximately $2.2 billion in 2006, $1.8 billion in 2005 and $1.3 billion in
2004, primarily in the Bell segment.
Other information by segment is provided below:
|
|
Assets
|
|
(In millions)
|
|
2006
|
|
2005
|
|
2004
|
|
Bell
|
|
$
|
2,598
|
|
$
|
1,966
|
|
$
|
1,674
|
|
Cessna
|
|
2,091
|
|
1,866
|
|
1,751
|
|
Industrial
|
|
2,495
|
|
2,383
|
|
2,601
|
|
Finance
|
|
9,000
|
|
7,441
|
|
6,738
|
|
Corporate
|
|
1,293
|
|
1,721
|
|
1,478
|
|
Discontinued operations
|
|
73
|
|
1,122
|
|
1,633
|
|
|
|
$
|
17,550
|
|
$
|
16,499
|
|
$
|
15,875
|
|
73
|
|
Capital Expenditures*
|
|
Depreciation and Amortization
|
|
(In millions)
|
|
2006
|
|
2005
|
|
2004
|
|
2006
|
|
2005
|
|
2004
|
|
Bell
|
|
$
|
225
|
|
$
|
152
|
|
$
|
62
|
|
$
|
67
|
|
$
|
54
|
|
$
|
49
|
|
Cessna
|
|
121
|
|
105
|
|
98
|
|
78
|
|
84
|
|
71
|
|
Industrial
|
|
82
|
|
101
|
|
100
|
|
91
|
|
104
|
|
107
|
|
Finance
|
|
12
|
|
9
|
|
12
|
|
39
|
|
46
|
|
46
|
|
Corporate
|
|
7
|
|
13
|
|
22
|
|
15
|
|
15
|
|
7
|
|
|
|
$
|
447
|
|
$
|
380
|
|
$
|
294
|
|
$
|
290
|
|
$
|
303
|
|
$
|
280
|
|
* Capital expenditures includes
amounts financed through capital leases.
Geographic Data
Presented below is selected financial information of
our continuing operations by geographic area:
|
|
Revenues*
|
|
Property, Plant and
Equipment, net**
|
|
(In millions)
|
|
2006
|
|
2005
|
|
2004
|
|
2006
|
|
2005
|
|
2004
|
|
United States
|
|
$
|
7,006
|
|
$
|
6,390
|
|
$
|
5,260
|
|
$
|
1,381
|
|
$
|
1,211
|
|
$
|
1,093
|
|
Europe
|
|
2,099
|
|
1,737
|
|
1,696
|
|
259
|
|
237
|
|
311
|
|
Canada
|
|
462
|
|
323
|
|
247
|
|
75
|
|
68
|
|
61
|
|
Latin America and Mexico
|
|
631
|
|
533
|
|
404
|
|
21
|
|
23
|
|
30
|
|
Asia and Australia
|
|
636
|
|
617
|
|
547
|
|
65
|
|
62
|
|
52
|
|
Middle East and Africa
|
|
656
|
|
443
|
|
164
|
|
6
|
|
6
|
|
7
|
|
|
|
$
|
11,490
|
|
$
|
10,043
|
|
$
|
8,318
|
|
$
|
1,807
|
|
$
|
1,607
|
|
$
|
1,554
|
|
* Revenues are
attributed to countries based on the location of the customer.
** Property, plant and equipment,
net are based on the location of the asset.
74
Quarterly Data
(Unaudited)
|
|
2006
|
|
2005
|
|
(Dollars in millions, except per share amounts)
|
|
Q4
|
|
Q3
|
|
Q2
|
|
Q1
|
|
Q4
|
|
Q3
|
|
Q2
|
|
Q1
|
|
Revenues
|
|
|
|
|
|
|
|
|
|
|
|
|
|
|
|
|
|
Bell
|
|
$
|
965
|
|
$
|
855
|
|
$
|
805
|
|
$
|
783
|
|
$
|
805
|
|
$
|
674
|
|
$
|
786
|
|
$
|
616
|
|
Cessna
|
|
1,232
|
|
1,050
|
|
1,005
|
|
869
|
|
967
|
|
890
|
|
910
|
|
713
|
|
Industrial
|
|
792
|
|
720
|
|
818
|
|
798
|
|
744
|
|
686
|
|
824
|
|
800
|
|
Finance
|
|
212
|
|
212
|
|
192
|
|
182
|
|
185
|
|
155
|
|
147
|
|
141
|
|
Total revenues
|
|
$
|
3,201
|
|
$
|
2,837
|
|
$
|
2,820
|
|
$
|
2,632
|
|
$
|
2,701
|
|
$
|
2,405
|
|
$
|
2,667
|
|
$
|
2,270
|
|
Segment profit
|
|
|
|
|
|
|
|
|
|
|
|
|
|
|
|
|
|
Bell
|
|
$
|
48
|
|
$
|
67
|
|
$
|
65
|
|
$
|
69
|
|
$
|
121
|
|
$
|
89
|
|
$
|
83
|
|
$
|
75
|
|
Cessna
|
|
213
|
|
162
|
|
153
|
|
117
|
|
132
|
|
117
|
|
121
|
|
87
|
|
Industrial
|
|
32
|
|
28
|
|
54
|
|
49
|
|
16
|
|
21
|
|
58
|
|
55
|
|
Finance
|
|
52
|
|
53
|
|
56
|
|
49
|
|
51
|
|
43
|
|
44
|
|
33
|
|
Total segment profit
|
|
345
|
|
310
|
|
328
|
|
284
|
|
320
|
|
270
|
|
306
|
|
250
|
|
Special charges
|
|
|
|
|
|
|
|
|
|
(21
|
)
|
(2
|
)
|
(41
|
)
|
(54
|
)
|
Corporate expenses and other, net
|
|
(60
|
)
|
(45
|
)
|
(48
|
)
|
(49
|
)
|
(54
|
)
|
(47
|
)
|
(55
|
)
|
(43
|
)
|
Interest expense, net
|
|
(20
|
)
|
(23
|
)
|
(25
|
)
|
(22
|
)
|
(21
|
)
|
(23
|
)
|
(22
|
)
|
(24
|
)
|
Income taxes
|
|
(69
|
)
|
(67
|
)
|
(78
|
)
|
(55
|
)
|
(56
|
)
|
(52
|
)
|
(70
|
)
|
(45
|
)
|
Income from continuing operations
|
|
196
|
|
175
|
|
177
|
|
158
|
|
168
|
|
146
|
|
118
|
|
84
|
|
(Loss) income from discontinued operations, net of
income taxes
|
|
(1
|
)
|
(6
|
)
|
(108
|
)
|
10
|
|
(50
|
)
|
(310
|
)
|
5
|
|
42
|
|
Net income (loss)
|
|
$
|
195
|
|
$
|
169
|
|
$
|
69
|
|
$
|
168
|
|
$
|
118
|
|
$
|
(164
|
)
|
$
|
123
|
|
$
|
126
|
|
Earnings per common share
|
|
|
|
|
|
|
|
|
|
|
|
|
|
|
|
|
|
Basic:
|
|
|
|
|
|
|
|
|
|
|
|
|
|
|
|
|
|
Income from
continuing operations
|
|
$
|
1.57
|
|
$
|
1.39
|
|
$
|
1.38
|
|
$
|
1.21
|
|
$
|
1.28
|
|
$
|
1.10
|
|
$
|
0.88
|
|
$
|
0.62
|
|
(Loss) income
from discontinued operations, net of income taxes
|
|
(0.01
|
)
|
(0.05
|
)
|
(0.84
|
)
|
0.08
|
|
(0.38
|
)
|
(2.33
|
)
|
0.04
|
|
0.31
|
|
Net income (loss)
|
|
$
|
1.56
|
|
$
|
1.34
|
|
$
|
0.54
|
|
$
|
1.29
|
|
$
|
0.90
|
|
$
|
(1.23
|
)
|
$
|
0.92
|
|
$
|
0.93
|
|
Basic average shares outstanding (In thousands)
|
|
125,544
|
|
125,809
|
|
128,453
|
|
130,093
|
|
131,569
|
|
132,910
|
|
134,603
|
|
135,127
|
|
Diluted:
|
|
|
|
|
|
|
|
|
|
|
|
|
|
|
|
|
|
Income from
continuing operations
|
|
$
|
1.54
|
|
$
|
1.36
|
|
$
|
1.34
|
|
$
|
1.19
|
|
$
|
1.25
|
|
$
|
1.07
|
|
$
|
0.86
|
|
$
|
0.61
|
|
(Loss) income
from discontinued operations, net of income taxes
|
|
(0.01
|
)
|
(0.04
|
)
|
(0.81
|
)
|
0.07
|
|
(0.37
|
)
|
(2.27
|
)
|
0.03
|
|
0.30
|
|
Net income (loss)
|
|
$
|
1.53
|
|
$
|
1.32
|
|
$
|
0.53
|
|
$
|
1.26
|
|
$
|
0.88
|
|
$
|
(1.20
|
)
|
$
|
0.89
|
|
$
|
0.91
|
|
Diluted average shares outstanding (In
thousands)
|
|
128,023
|
|
128,379
|
|
131,294
|
|
132,856
|
|
134,300
|
|
135,629
|
|
137,582
|
|
138,283
|
|
Segment profit margins
|
|
|
|
|
|
|
|
|
|
|
|
|
|
|
|
|
|
Bell
|
|
5.0
|
%
|
7.8
|
%
|
8.1
|
%
|
8.8
|
%
|
15.0
|
%
|
13.2
|
%
|
10.6
|
%
|
12.2
|
%
|
Cessna
|
|
17.3
|
|
15.4
|
|
15.2
|
|
13.5
|
|
13.7
|
|
13.1
|
|
13.3
|
|
12.2
|
|
Industrial
|
|
4.0
|
|
3.9
|
|
6.6
|
|
6.1
|
|
2.2
|
|
3.1
|
|
7.0
|
|
6.9
|
|
Finance
|
|
24.5
|
|
25.0
|
|
29.2
|
|
26.9
|
|
27.6
|
|
27.7
|
|
29.9
|
|
23.4
|
|
Segment profit margin
|
|
10.8
|
%
|
10.9
|
%
|
11.6
|
%
|
10.8
|
%
|
11.8
|
%
|
11.2
|
%
|
11.5
|
%
|
11.0
|
%
|
Common stock information
|
|
|
|
|
|
|
|
|
|
|
|
|
|
|
|
|
|
Price range: High
|
|
$
|
98.38
|
|
$
|
93.13
|
|
$
|
98.10
|
|
$
|
94.40
|
|
$
|
80.00
|
|
$
|
78.80
|
|
$
|
78.30
|
|
$
|
80.05
|
|
Low
|
|
$
|
88.19
|
|
$
|
81.10
|
|
$
|
82.51
|
|
$
|
75.76
|
|
$
|
69.00
|
|
$
|
65.85
|
|
$
|
71.11
|
|
$
|
68.61
|
|
Dividends per
share
|
|
$
|
0.3875
|
|
$
|
0.3875
|
|
$
|
0.3875
|
|
$
|
0.3875
|
|
$
|
0.350
|
|
$
|
0.350
|
|
$
|
0.350
|
|
$
|
0.350
|
|
75
Schedule II Valuation and Qualifying Accounts
(In millions)
|
|
2006
|
|
2005
|
|
2004
|
|
Manufacturing Group
|
|
|
|
|
|
|
|
|
|
|
|
|
|
|
|
Allowance for Doubtful Accounts
|
|
|
|
|
|
|
|
Balance at beginning of year
|
|
$
|
38
|
|
$
|
54
|
|
$
|
55
|
|
Charged to costs and
expenses
|
|
4
|
|
16
|
|
16
|
|
Deductions from
reserves*
|
|
(8
|
)
|
(32
|
)
|
(17
|
)
|
Balance at end of year
|
|
$
|
34
|
|
$
|
38
|
|
$
|
54
|
|
|
|
|
|
|
|
|
|
Reserves for Recourse Liability
to Finance Group Continuing Operations**
|
|
|
|
|
|
|
|
Balance at beginning of year
|
|
$
|
40
|
|
$
|
37
|
|
$
|
46
|
|
Charged to costs and
expenses
|
|
|
|
12
|
|
10
|
|
Reclassifications to
other assets
|
|
|
|
|
|
(14
|
)
|
Deductions from
reserves*
|
|
(1
|
)
|
(9
|
)
|
(5
|
)
|
Balance at end of year
|
|
$
|
39
|
|
$
|
40
|
|
$
|
37
|
|
|
|
|
|
|
|
|
|
Inventory FIFO Reserves
|
|
|
|
|
|
|
|
Balance at beginning of year
|
|
$
|
85
|
|
$
|
91
|
|
$
|
100
|
|
Charged to costs and
expenses
|
|
29
|
|
25
|
|
33
|
|
Deductions from
reserves*
|
|
(25
|
)
|
(31
|
)
|
(42
|
)
|
Balance at end of year
|
|
$
|
89
|
|
$
|
85
|
|
$
|
91
|
|
|
|
|
|
|
|
|
|
Finance Group
|
|
|
|
|
|
|
|
|
|
|
|
|
|
|
|
Allowance for Losses on Finance
Receivables
|
|
|
|
|
|
|
|
Balance at beginning of year
|
|
$
|
96
|
|
$
|
99
|
|
$
|
119
|
|
Provision for losses
|
|
26
|
|
29
|
|
58
|
|
Deduction from reserves*
|
|
(29
|
)
|
(32
|
)
|
(78
|
)
|
Balance at end
of year
|
|
$
|
93
|
|
$
|
96
|
|
$
|
99
|
|
* Represents uncollectible
accounts written off (less recoveries), inventory disposals, acquisitions and
translation adjustments
** These reserves exclude discontinued operations liabilities
of $6 million in 2006, $18 million in 2005 and $22 million in 2004. The decline
in these reserves is primarily due to write-offs.
Item 9. Changes in and Disagreements with Accountants
on Accounting and Financial Disclosure
None
Item 9A. Controls and Procedures
Disclosure Controls and Procedures
We have carried out an
evaluation, under the supervision and with the participation of our management,
including our Chairman, President and Chief Executive Officer (our CEO) and
our Executive Vice President and Chief Financial Officer (our CFO), of the
effectiveness of the design and operation of our disclosure controls and
procedures (as defined in Rule 13a-15(e) and 15d-15(e) under the Securities
Exchange Act of 1934, as amended (the Act)) as of the end of the fiscal year
covered by this report. Based upon that evaluation, our CEO and CFO concluded
that our disclosure controls and procedures are effective in providing
reasonable assurance that (a) the information required to be disclosed by us in
the reports that we file or submit under the Act is recorded, processed,
summarized and reported within the time periods specified in the Securities and
Exchange Commissions rules and forms, and (b) such information is accumulated
and communicated to our management, including our CEO and CFO, as appropriate
to allow timely decisions regarding required disclosure.
76
Report of Management See page 33.
Report of Independent Registered
Public Accounting Firm on Internal Control over Financial Reporting See page 34.
Changes in Internal Controls There have been no changes in our internal
control over financial reporting during the fourth quarter of the fiscal year
covered by this report that have materially affected, or are reasonably likely
to materially affect, our internal control over financial reporting.
Item 9B. Other Information
None
PART III
Item 10. Directors and Executive Officers of the
Registrant
The information appearing under Audit Committee, Nominees
for Director, Directors Continuing in Office, Corporate Governance, Code
of Ethics and Section 16(a) Beneficial Ownership Reporting Compliance in the
Proxy Statement for our Annual Meeting of Shareholders to be held on April 25,
2007, is incorporated by reference into this Annual Report on Form 10-K.
Information regarding our executive officers is
contained in Part I of this Annual Report on Form 10-K.
Item 11. Executive Compensation
The information appearing under Compensation of
Directors, Compensation Discussion and Analysis and Executive Compensation
in the Proxy Statement for our Annual Meeting of Shareholders to be held on
April 25, 2007, is incorporated by reference into this Annual Report on Form
10-K.
Item 12. Security Ownership of Certain Beneficial
Owners and Management and Related Stockholder Matters
The information appearing under Security Ownership
of Certain Beneficial Holders, Security Ownership of Management and Equity
Compensation Plan Information in the Proxy Statement for our Annual Meeting of
Shareholders to be held on April 25, 2007, is incorporated by reference into
this Annual Report on Form 10-K.
Item 13. Certain Relationships and Related
Transactions
The information appearing under Director
Independence and Transactions with Management and Others in the Proxy
Statement for our Annual Meeting of Shareholders to be held on April 25, 2007,
is incorporated by reference into this Annual Report on Form 10-K.
77
Item 14. Principal Accountant Fees and Services
The information appearing under Fees to Independent
Auditors in the Proxy Statement for our Annual Meeting of Shareholders to be
held on April 25, 2007, is incorporated by reference into this Annual Report on
Form 10-K.
PART IV
Item 15. Exhibits and Financial Statement Schedules
Financial Statements and Schedules - See Index on
Page 32.
Exhibits
|
|
|
|
|
|
3.1
|
|
Restated
Certificate of Incorporation of Textron as filed January 29, 1998.
Incorporated by reference to Exhibit 3.1 to Textrons Annual Report on Form
10-K for the fiscal year ended January 3, 1998.
|
|
|
|
3.2
|
|
By-Laws of
Textron. Incorporated by reference to Exhibit 3.1 to Textrons Current Report
on Form 8-K filed April 29, 2006.
|
|
|
|
4.1A
|
|
Indenture dated
as of December 9, 1999, between Textron Financial Corporation and SunTrust Bank
(formerly known as Sun Trust Bank, Atlanta) (including form of debt
securities). Incorporated by reference to Exhibit 4.1 to Amendment No. 2 to
Textron Financial Corporations Registration Statement on Form S-3 (No.
333-88509).
|
|
|
|
4.1B
|
|
First Supplemental
Indenture dated November 16, 2006, between Textron Financial Corporation and
U.S. Bank National Association (successor trustee to Sun Trust Bank) to
Indenture dated as of December 9, 1999. Incorporated by reference to Exhibit
4.3 of Textron Financial Corporations Form S-3 (File No. 333-138755).
|
|
|
|
4.1C
|
|
Form of
Medium-Term Note of Textron Financial Corporation. Incorporated by reference
to Exhibit 4.3 to Textron Financial Corporations Current Report on Form 8-K
filed November 17, 2006.
|
|
|
|
4.2A
|
|
Indenture dated
as of November 30, 2001, between Textron Financial Canada Funding Corp. and
SunTrust Bank, guaranteed by Textron Financial Corporation. Incorporated by
reference to Exhibit 4.2 to Amendment No. 1 to Textron Financial
Corporations Registration Statement on Form S-3 (No. 333-108464).
|
|
|
|
4.2B
|
|
First
Supplemental Indenture, dated November 16, 2006, between Textron Financial
Canada Funding Corp., Textron Financial Corporation and U.S. Bank National
Association (successor trustee to Sun Trust Bank) to Indenture dated November
30, 2001. Incorporated by reference to Exhibit 4.4 of Textron Financial
Corporations Form S-3 (File No. 333-138755).
|
|
|
|
4.2C
|
|
Form of
Medium-Term Note of Textron Financial Canada Funding Corp. Incorporated by
reference to Exhibit 4.4 to Textron Financial Corporations Current Report on
Form 8-K filed November 17, 2006.
|
|
|
|
4.3A
|
|
Amended and
Restated Indenture, dated as of May 26, 2005, by and between Textron
Financial Floorplan Master Note Trust and The Bank of New York, as indenture
trustee. Incorporated herein by reference to Exhibit 4.1 of Textron Financial
Corporations Current Report on Form 8-K filed June 1, 2005.
|
|
|
|
4.3B
|
|
Amended and
Restated Series 2001-1 Supplement, dated as of May 26, 2005, to the Amended
and Restated Indenture, dated as of May 26, 2005, by and among Textron
Financial Floorplan Master Note Trust, The Bank of New York, as indenture
trustee, and Textron Financial, as servicer. Incorporated herein by reference
to Exhibit 4.2 of Textron Financial Corporations Current Report on Form 8-K
filed June 1, 2005.
|
|
|
|
4.3C
|
|
Series 2005-A
Supplement, dated as of May 26, 2005, to the Amended and Restated Indenture,
dated as of May 26, 2005, by and among Textron Financial Floorplan Master
Note Trust, The Bank of New York, as indenture trustee, and Textron
Financial, as servicer. Incorporated herein by reference to Exhibit 4.3 of
Textron Financial Corporations Current Report on Form 8-K filed June 1, 2005.
|
78
4.3D
|
|
Series 2006-A
Supplement, dated as of April 19, 2006, to the Amended and Restated
Indenture, dated as of May 26, 2005, by and among Textron Financial Floorplan
Master Note Trust, The Bank of New York, as indenture trustee, and Textron
Financial, as servicer. Incorporated herein by reference to Exhibit 4.1 of
Textron Financial Corporations Current Report on Form 8-K filed April 24,
2006.
|
|
|
|
4.4
|
|
Support
Agreement dated as of May 25, 1994, between Textron Inc. and Textron
Financial Corporation. Incorporated by reference to Exhibit 10.1 to Textron
Financial Corporations Registration Statement on Form 10 (File No. 0-27559).
|
|
|
|
NOTE:
|
|
Instruments
defining the rights of holders of certain issues of long-term debt of Textron
have not been filed as exhibits because the authorized principal amount of
any one of such issues does not exceed 10% of the total assets of Textron and
its subsidiaries on a consolidated basis. Textron agrees to furnish a copy of
each such instrument to the Commission upon request.
|
|
|
|
NOTE:
|
|
Exhibits 10.1
through 10.20 below are management contracts or compensatory plans, contracts
or agreements.
|
|
|
|
10.1A
|
|
Annual Incentive
Compensation Plan for Textron Employees. Incorporated by reference to Exhibit
10.1 to Textrons Annual Report on Form 10-K for the fiscal year ended
December 30, 1995.
|
|
|
|
10.1B
|
|
Amendment to
Annual Incentive Compensation Plan for Textron Employees. Incorporated by
reference to Exhibit 10.1 to Textrons Quarterly Report on Form 10-Q for the
fiscal quarter ended July 3, 1999.
|
|
|
|
10.1C
|
|
Objectives for
Executive Officers Under Annual Incentive Compensation Plan for Textron
Employees.
|
|
|
|
10.2
|
|
Deferred Income
Plan for Textron Key Executives. Incorporated by reference to Exhibit 10.2 to
Textrons Annual Report on Form 10-K for the fiscal year ended January 3,
2004.
|
|
|
|
10.3
|
|
Description of
Textron Spillover Pension Plan. Incorporated by reference to Exhibit 10.1 to
Textrons Quarterly Report on Form 10-Q for the fiscal quarter ended
September 30, 2006.
|
|
|
|
10.4
|
|
Supplemental
Retirement Plan for Textron Key Executives. Incorporated by reference to
Exhibit 10.4 to Textrons Annual Report on Form 10-K for the fiscal year
ended January 3, 2004.
|
|
|
|
10.5
|
|
Survivor Benefit
Plan For Textron Key Executives, as amended. Incorporated by reference to
Exhibit 10.5 to Textrons Annual Report on Form 10-K for the fiscal year
ended January 3, 2004.
|
|
|
|
10.6A
|
|
Textron 1994
Long-Term Incentive Plan (1994 Plan). Incorporated by reference to Exhibit
10 to Textrons Quarterly Report on Form 10-Q for the fiscal quarter ended
July 2, 1994.
|
|
|
|
10.6B
|
|
Amendment to
1994 Plan. Incorporated by reference to Exhibit 10.9B to Textrons Annual
Report on Form 10-K for the fiscal year ended January 2, 1999.
|
|
|
|
10.6C
|
|
Amendment to
1994 Plan. Incorporated by reference to Exhibit 10.6 to Textrons Quarterly
Report on Form 10-Q for the fiscal quarter ended July 3, 1999.
|
|
|
|
10.6D
|
|
Amendment to
1994 Plan. Incorporated by reference to Exhibit 10.8D to Textrons Annual
Report on Form 10-K for the fiscal year ended January 1, 2000.
|
|
|
|
10.7A
|
|
Textron 1999
Long-Term Incentive Plan for Textron Employees (April 26, 2005 Restatement).
Incorporated by reference to Exhibit 10.1 to Textrons Quarterly Report on
Form 10-Q for the fiscal quarter ended April 2, 2005.
|
|
|
|
10.7B
|
|
Form of
Non-Qualified Stock Option Agreement. Incorporated by reference to Exhibit
10.1 to Textrons Quarterly Report on Form 10-Q for the fiscal quarter ended
July 3, 2004.
|
|
|
|
10.7C
|
|
Form of
Incentive Stock Option Agreement. Incorporated by reference to Exhibit 10.2
to Textrons Quarterly Report on Form 10-Q for the fiscal quarter ended July
3, 2004.
|
|
|
|
10.7D
|
|
Form of
Restricted Stock Grant Agreement. Incorporated by reference to Exhibit 10.3
to Textrons Quarterly Report on Form 10-Q for the fiscal quarter ended July
3, 2004.
|
|
|
|
10.8A
|
|
Performance
Share Unit Plan for Textron Employees. Incorporated by reference to Exhibit
10.2 to Textrons Quarterly Report on Form 10-Q for the fiscal quarter ended
April 2, 2005.
|
|
|
|
10.8B
|
|
Performance
Factors for Executive Officers for Performance Share Units.
|
79
10.9
|
|
Form of
Indemnity Agreement between Textron and its directors and executive officers.
Incorporated by reference to Exhibit A to Textrons Proxy Statement for its
Annual Meeting of Shareholders on April 29, 1987.
|
|
|
|
10.10
|
|
Deferred Income
Plan for Non-Employee Directors. Incorporated by reference to Exhibit 10.1 to
Textrons Annual Report on Form 10-K for the fiscal year ended December 28,
2002.
|
|
|
|
10.11A
|
|
Amended and
Restated Employment Agreement between Textron and John D. Butler dated May 4,
2006. Incorporated by reference to Exhibit 10.2 to Textrons Quarterly Report
on Form 10-Q for the fiscal quarter ended April 1, 2006.
|
|
|
|
10.11B
|
|
Restricted Stock
Equivalent Award granted to John D. Butler on January 15, 2002. Incorporated
by reference to Exhibit 10.1 of Textrons Quarterly Report on Form 10-Q for
the fiscal quarter ended March 30, 2002.
|
|
|
|
10.12A
|
|
Employment
Agreement between Textron and Lewis B. Campbell dated July 23, 1998.
Incorporated by reference to Exhibit 10.3 to Textrons Quarterly Report on
Form 10-Q for the fiscal quarter ended October 3, 1998.
|
|
|
|
10.12B
|
|
Amendment dated
May 6, 2005, to Employment Agreement between Textron and Lewis B. Campbell.
Incorporated by reference to Exhibit 10.3 to Textrons Quarterly Report on
Form 10-Q for the fiscal quarter ended April 2, 2005.
|
|
|
|
10.12C
|
|
Second
Amendment, dated May 4, 2006, to Employment Agreement between Textron and
Lewis B. Campbell. Incorporated by reference to Exhibit 10.4 to Textrons
Quarterly Report on Form 10-Q for the fiscal quarter ended April 1, 2006.
|
|
|
|
10.12D
|
|
Retention Award
granted to Lewis B. Campbell on December 14, 1995. Incorporated by reference
to Exhibit 10.16B to Textrons Annual Report on Form 10-K for the fiscal year
ended December 30, 1995.
|
|
|
|
10.12E
|
|
Retention Award
granted to Lewis B. Campbell on June 1, 1999. Incorporated by reference to
Exhibit 10.13C to Textrons Annual Report on Form 10-K for the fiscal year
ended January 1, 2000.
|
|
|
|
10.12F
|
|
Retention Award
granted to Lewis B. Campbell on January 1, 2001, and revision of vesting
schedule for the Retention Award granted on June 1, 1999. Incorporated by
reference to Exhibit 10.14D to Textrons Annual Report on Form 10-K for the
fiscal year ended December 30, 2000.
|
|
|
|
10.12G
|
|
Amendments to
Retention Awards granted to Lewis B. Campbell. Incorporated by reference to
Exhibit 10.14D to Textrons Annual Report on Form 10-K for the fiscal year
ended December 29, 2001.
|
|
|
|
10.13A
|
|
Employment
Agreement between Textron and Ted R. French dated December 21, 2000.
Incorporated by reference to Exhibit 10.15A to Textrons Annual Report on
Form 10-K for the fiscal year ended December 30, 2000.
|
|
|
|
10.13B
|
|
Retention Award
granted to Ted R. French on January 1, 2001. Incorporated by reference to
Exhibit 10.15B to Textrons Annual Report on Form 10-K for the fiscal year
ended December 30, 2000.
|
|
|
|
10.14A
|
|
Amended and
Restated Employment Agreement between Textron and Mary L. Howell dated May 4,
2006. Incorporated by reference to Exhibit 10.1 to Textrons Quarterly Report
on Form 10-Q for the fiscal quarter ended April 1, 2006.
|
|
|
|
10.14B
|
|
Restricted Stock
Equivalent Award granted to Mary L. Howell on January 15, 2002. Incorporated
by reference to Exhibit 10.2 of Textrons Quarterly Report on Form 10-Q for
the fiscal quarter ended March 30, 2002.
|
|
|
|
10.15A
|
|
Amended and
Restated Employment Agreement between Textron and Terrence ODonnell dated
May 4, 2006. Incorporated by reference to Exhibit 10.3 to Textrons Quarterly
Report on Form 10-Q for the fiscal quarter ended April 1, 2006.
|
|
|
|
10.15B
|
|
Restricted Stock
Equivalent Award granted to Terrence ODonnell on January 15, 2002. Incorporated
by reference to Exhibit 10.3 of Textrons Quarterly Report on Form 10-Q for
the fiscal quarter ended March 30, 2002.
|
|
|
|
10.16
|
|
Employment
Agreement between Textron and Kenneth C. Bohlen dated July 18, 2000.
Incorporated by reference to Exhibit 10.2 to Textrons Quarterly Report on
Form 10-Q for the fiscal quarter ended July 1, 2000.
|
|
|
|
10.17
|
|
Director Compensation.
|
|
|
|
10.18
|
|
Director Stock
Awards. Incorporated by reference to Exhibit 10.17 to Textrons Annual Report
on Form 10-K for the fiscal year ended December 28, 2002.
|
80
10.19
|
|
CitationShares
Directors Evaluation Program. Incorporated by reference to Exhibit 10.17 to
Textrons Annual Report on Form 10-K for the fiscal year ended January 1,
2005.
|
|
|
|
10.20
|
|
Amendment to 13
plans to comply with the American Jobs Creation Act of 2004. Incorporated by
reference to Exhibit 10.18 to Textrons Annual Report on Form 10-K for the
fiscal year ended January 1, 2005.
|
|
|
|
10.21A
|
|
5-Year Credit
Agreement, dated as of March 28, 2005, among Textron, the Banks listed
therein, JPMorgan Chase Bank, N.A., as Administrative Agent, and Citibank,
N.A., as Syndication Agent (the 5-Year Credit Agreement). Incorporated by
reference to Exhibit 10.1 to Textrons Current Report on Form 8-K filed March
31, 2005.
|
|
|
|
10.21B
|
|
Amendment No. 1,
dated as of April 21, 2006, to 5-Year Credit Agreement. Incorporated by
reference to Exhibit 10.1 to Textrons Current Report on Form 8-K filed April
25, 2006.
|
|
|
|
10.22A
|
|
364-Day Credit
Agreement dated March 31, 2003, among Textron Inc., the Banks listed therein
and JPMorgan Chase Bank as Administrative Agent (the 364-Day Credit
Agreement). Incorporated by reference to Exhibit 10.3 to Textrons Quarterly
Report on Form 10-Q for the fiscal quarter ended March 29, 2003.
|
|
|
|
10.22B
|
|
Amendment, dated
as of July 28, 2003, to the 364-Day Credit Agreement. Incorporated by
reference to Exhibit 10.19 to Textrons Annual Report on Form 10-K for the
fiscal year ended January 3, 2004.
|
|
|
|
10.22C
|
|
Amendment No. 2,
dated as of March 29, 2004, to the 364-Day Credit Agreement. Incorporated by
reference to Exhibit 10.1 to Textrons Quarterly Report on Form 10-Q for the
fiscal quarter ended April 3, 2004.
|
|
|
|
10.23A
|
|
364-Day Credit
Agreement dated July 28, 2003, among Textron Financial Corporation, the Banks
listed therein, and JPMorgan Chase Bank, as Administrative Agent.
Incorporated by reference to Exhibit 10.1 to Textron Financial Corporations
Current Report on Form 8-K as filed on August 26, 2003.
|
|
|
|
10.23B
|
|
Amendment, dated
as of July 26, 2004, to 364-Day Credit Agreement dated July 28, 2003, among
Textron Financial Corporation, the Banks listed therein, and JPMorgan Chase
Bank, as Administrative Agent. Incorporated by reference to Exhibit 10.1 to
Textron Financial Corporations Quarterly Report on Form 10-Q for the fiscal
quarter ended September 30, 2004.
|
|
|
|
10.23C
|
|
Amendment No. 2,
dated as of July 25, 2005, to the 364-Day Credit Agreement dated as of July
28, 2003, among Textron Financial, the Banks listed therein, and JPMorgan
Chase Bank N.A., as Administrative Agent. Incorporated by reference to
Exhibit 10.2 of Textron Financial Corporations Current Report on Form 8-K
filed July 27, 2005.
|
|
|
|
10.24A
|
|
Five-Year Credit
Agreement dated July 28, 2003 among Textron Financial Corporation, the Banks
listed therein, and JPMorgan Chase Bank, as Administrative Agent.
Incorporated by reference to Exhibit 10.2 to Textron Financial Corporations
Current Report on Form 8-K as filed on August 26, 2003.
|
|
|
|
10.24B
|
|
Amendment No. 1,
dated as of July 25, 2005, to the Five-Year Credit Agreement dated as of July
28, 2003 among Textron Financial, the Banks listed therein, and JPMorgan
Chase Bank N.A., as Administrative Agent. Incorporated by reference to
Exhibit 10.1 of Textron Financial Corporations Current Report on Form 8-K
filed July 27, 2005.
|
|
|
|
10.24C
|
|
Amendment No. 2,
dated as of April 28, 2006, to the Five-Year Credit Agreement dated as of
July 28, 2003 among Textron Financial, the Banks listed therein, and JPMorgan
Chase Bank N.A., as Administrative Agent. Incorporated by reference to
Exhibit 10.1 of Textron Financial Corporations Current Report on Form 8-K
filed May 1, 2006.
|
|
|
|
10.25
|
|
Master Services
Agreement between Textron Inc. and Computer Sciences Corporation dated
October 27, 2004. Confidential treatment has been requested for portions of
this agreement. Incorporated by reference to Exhibit 10.26 to Textrons
Annual Report on Form 10-K for the fiscal year ended January 1, 2005.
|
|
|
|
12.1
|
|
Computation of
ratio of income to combined fixed charges and preferred stock dividends of
Textron Manufacturing.
|
|
|
|
12.2
|
|
Computation of
ratio of income to combined fixed charges and preferred stock dividends of
Textron including all majority-owned subsidiaries.
|
|
|
|
21
|
|
Certain
subsidiaries of Textron. Other subsidiaries, which considered in the
aggregate do not constitute a significant subsidiary, are omitted from such
list.
|
|
|
|
23
|
|
Consent of
Independent Registered Public Accounting Firm.
|
|
|
|
81
24
|
|
Power of
attorney.
|
|
|
|
31.1
|
|
Certification of
Chief Executive Officer Pursuant to Rule 13a-14(a).
|
|
|
|
31.2
|
|
Certification of
Chief Financial Officer Pursuant to Rule 13a-14(a).
|
|
|
|
32.1
|
|
Certification of
Chief Executive Officer Pursuant to 18 U.S.C. Section 1350.
|
|
|
|
32.2
|
|
Certification of
Chief Financial Officer Pursuant to 18 U.S.C. Section 1350.
|
Signatures
Pursuant to the requirement of Section 13 or 15(d) of
the Securities Exchange Act of 1934, the registrant has duly caused this Annual
Report on Form 10-K to be signed on its behalf by the undersigned, thereunto
duly authorized on this 21st day of February 2007.
|
|
TEXTRON INC.
|
|
|
|
Registrant
|
|
|
|
|
|
|
By:
|
|
/s/ Ted R. French
|
|
|
|
|
Ted R. French
|
|
|
|
Executive Vice
President
|
|
|
|
and Chief
Financial Officer
|
|
|
|
|
|
|
|
82
Pursuant to the requirements of the Securities and
Exchange Act of 1934, this Annual Report on Form 10-K has been signed below on
this 21st day of February 2007, by the following persons on behalf of the
registrant and in the capacities indicated:
Name
|
|
Title
|
|
|
|
/s/ Lewis B. Campbell
|
|
Chairman,
President and Chief Executive Officer,
|
Lewis B. Campbell
|
|
Director
|
|
|
|
*
|
|
|
H. Jesse Arnelle
|
|
Director
|
|
|
|
*
|
|
|
Kathleen M. Bader
|
|
Director
|
|
|
|
*
|
|
|
R. Kerry Clark
|
|
Director
|
|
|
|
*
|
|
|
Ivor J. Evans
|
|
Director
|
|
|
|
*
|
|
|
Lawrence K. Fish
|
|
Director
|
|
|
|
*
|
|
|
Joe T. Ford
|
|
Director
|
|
|
|
*
|
|
|
Paul E. Gagné
|
|
Director
|
|
|
|
*
|
|
|
Dain M. Hancock
|
|
Director
|
|
|
|
*
|
|
|
Lord Powell of Bayswater KCMG
|
|
Director
|
|
|
|
*
|
|
|
Thomas B. Wheeler
|
|
Director
|
|
|
|
/s/ Ted R. French
|
|
Executive Vice
President and
|
Ted R. French
|
|
Chief Financial
Officer
|
|
|
(principal
financial officer)
|
|
|
|
/s/ Richard L. Yates
|
|
Senior Vice
President and Corporate Controller
|
Richard L. Yates
|
|
(principal
accounting officer)
|
*By:
|
/s/ Michael D. Cahn
|
|
|
Michael D. Cahn
|
|
|
Attorney-in-fact
|
|
83
EXHIBIT INDEX
Exhibits
|
|
|
|
|
|
3.1
|
|
Restated
Certificate of Incorporation of Textron as filed January 29, 1998.
Incorporated by reference to Exhibit 3.1 to Textrons Annual Report on Form
10-K for the fiscal year ended January 3, 1998.
|
|
|
|
3.2
|
|
By-Laws of
Textron. Incorporated by reference to Exhibit 3.1 to Textrons Current Report
on Form 8-K filed April 29, 2006.
|
|
|
|
4.1A
|
|
Indenture dated
as of December 9, 1999, between Textron Financial Corporation and SunTrust
Bank (formerly known as Sun Trust Bank, Atlanta) (including form of debt
securities). Incorporated by reference to Exhibit 4.1 to Amendment No. 2 to
Textron Financial Corporations Registration Statement on Form S-3 (No.
333-88509).
|
|
|
|
4.1B
|
|
First
Supplemental Indenture dated November 16, 2006, between Textron Financial
Corporation and U.S. Bank National Association (successor trustee to Sun
Trust Bank) to Indenture dated as of December 9, 1999. Incorporated by
reference to Exhibit 4.3 of Textron Financial Corporations Form S-3 (File
No. 333-138755).
|
|
|
|
4.1C
|
|
Form of
Medium-Term Note of Textron Financial Corporation. Incorporated by reference
to Exhibit 4.3 to Textron Financial Corporations Current Report on Form 8-K
filed November 17, 2006.
|
|
|
|
4.2A
|
|
Indenture dated as
of November 30, 2001, between Textron Financial Canada Funding Corp. and
SunTrust Bank, guaranteed by Textron Financial Corporation. Incorporated by
reference to Exhibit 4.2 to Amendment No. 1 to Textron Financial
Corporations Registration Statement on Form S-3 (No. 333-108464).
|
|
|
|
4.2B
|
|
First
Supplemental Indenture, dated November 16, 2006, between Textron Financial
Canada Funding Corp., Textron Financial Corporation and U.S. Bank National
Association (successor trustee to Sun Trust Bank) to Indenture dated November
30, 2001. Incorporated by reference to Exhibit 4.4 of Textron Financial
Corporations Form S-3 (File No. 333-138755).
|
|
|
|
4.2C
|
|
Form of
Medium-Term Note of Textron Financial Canada Funding Corp. Incorporated by
reference to Exhibit 4.4 to Textron Financial Corporations Current Report on
Form 8-K filed November 17, 2006.
|
|
|
|
4.3A
|
|
Amended and
Restated Indenture, dated as of May 26, 2005, by and between Textron
Financial Floorplan Master Note Trust and The Bank of New York, as indenture
trustee. Incorporated herein by reference to Exhibit 4.1 of Textron Financial
Corporations Current Report on Form 8-K filed June 1, 2005.
|
|
|
|
4.3B
|
|
Amended and
Restated Series 2001-1 Supplement, dated as of May 26, 2005, to the Amended
and Restated Indenture, dated as of May 26, 2005, by and among Textron
Financial Floorplan Master Note Trust, The Bank of New York, as indenture
trustee, and Textron Financial, as servicer. Incorporated herein by reference
to Exhibit 4.2 of Textron Financial Corporations Current Report on Form 8-K
filed June 1, 2005.
|
|
|
|
4.3C
|
|
Series 2005-A
Supplement, dated as of May 26, 2005, to the Amended and Restated Indenture,
dated as of May 26, 2005, by and among Textron Financial Floorplan Master
Note Trust, The Bank of New York, as indenture trustee, and Textron
Financial, as servicer. Incorporated herein by reference to Exhibit 4.3 of
Textron Financial Corporations Current Report on Form 8-K filed June 1, 2005.
|
|
|
|
4.3D
|
|
Series 2006-A
Supplement, dated as of April 19, 2006, to the Amended and Restated
Indenture, dated as of May 26, 2005, by and among Textron Financial Floorplan
Master Note Trust, The Bank of New York, as indenture trustee, and Textron
Financial, as servicer. Incorporated herein by reference to Exhibit 4.1 of
Textron Financial Corporations Current Report on Form 8-K filed April 24,
2006.
|
|
|
|
4.4
|
|
Support
Agreement dated as of May 25, 1994, between Textron Inc. and Textron
Financial Corporation. Incorporated by reference to Exhibit 10.1 to Textron
Financial Corporations Registration Statement on Form 10 (File No. 0-27559).
|
|
|
|
NOTE:
|
|
Instruments
defining the rights of holders of certain issues of long-term debt of Textron
have not been filed as exhibits because the authorized principal amount of
any one of such issues does not exceed 10% of the total assets of Textron and
its subsidiaries on a consolidated basis. Textron agrees to furnish a copy of
each such instrument to the Commission upon request.
|
|
|
|
NOTE:
|
|
Exhibits 10.1
through 10.20 below are management contracts or compensatory plans, contracts
or agreements.
|
|
|
|
10.1A
|
|
Annual Incentive
Compensation Plan for Textron Employees. Incorporated by reference to Exhibit
10.1 to Textrons Annual Report on Form 10-K for the fiscal year ended
December 30, 1995.
|
|
|
|
10.1B
|
|
Amendment to
Annual Incentive Compensation Plan for Textron Employees. Incorporated by
reference to Exhibit 10.1 to Textrons Quarterly Report on Form 10-Q for the
fiscal quarter ended July 3, 1999.
|
|
|
|
10.1C
|
|
Objectives for
Executive Officers Under Annual Incentive Compensation Plan for Textron
Employees.
|
|
|
|
10.2
|
|
Deferred Income
Plan for Textron Key Executives. Incorporated by reference to Exhibit 10.2 to
Textrons Annual Report on Form 10-K for the fiscal year ended January 3,
2004.
|
|
|
|
10.3
|
|
Description of
Textron Spillover Pension Plan. Incorporated by reference to Exhibit 10.1 to
Textrons Quarterly Report on Form 10-Q for the fiscal quarter ended
September 30, 2006.
|
|
|
|
10.4
|
|
Supplemental
Retirement Plan for Textron Key Executives. Incorporated by reference to
Exhibit 10.4 to Textrons Annual Report on Form 10-K for the fiscal year
ended January 3, 2004.
|
|
|
|
10.5
|
|
Survivor Benefit
Plan For Textron Key Executives, as amended. Incorporated by reference to
Exhibit 10.5 to Textrons Annual Report on Form 10-K for the fiscal year
ended January 3, 2004.
|
|
|
|
10.6A
|
|
Textron 1994
Long-Term Incentive Plan (1994 Plan). Incorporated by reference to Exhibit
10 to Textrons Quarterly Report on Form 10-Q for the fiscal quarter ended
July 2, 1994.
|
|
|
|
10.6B
|
|
Amendment to
1994 Plan. Incorporated by reference to Exhibit 10.9B to Textrons Annual
Report on Form 10-K for the fiscal year ended January 2, 1999.
|
|
|
|
10.6C
|
|
Amendment to
1994 Plan. Incorporated by reference to Exhibit 10.6 to Textrons Quarterly
Report on Form 10-Q for the fiscal quarter ended July 3, 1999.
|
|
|
|
10.6D
|
|
Amendment to
1994 Plan. Incorporated by reference to Exhibit 10.8D to Textrons Annual
Report on Form 10-K for the fiscal year ended January 1, 2000.
|
|
|
|
10.7A
|
|
Textron 1999
Long-Term Incentive Plan for Textron Employees (April 26, 2005 Restatement).
Incorporated by reference to Exhibit 10.1 to Textrons Quarterly Report on
Form 10-Q for the fiscal quarter ended April 2, 2005.
|
|
|
|
10.7B
|
|
Form of Non-Qualified
Stock Option Agreement. Incorporated by reference to Exhibit 10.1 to
Textrons Quarterly Report on Form 10-Q for the fiscal quarter ended July 3,
2004.
|
|
|
|
10.7C
|
|
Form of
Incentive Stock Option Agreement. Incorporated by reference to Exhibit 10.2 to
Textrons Quarterly Report on Form 10-Q for the fiscal quarter ended July 3,
2004.
|
|
|
|
10.7D
|
|
Form of
Restricted Stock Grant Agreement. Incorporated by reference to Exhibit 10.3
to Textrons Quarterly Report on Form 10-Q for the fiscal quarter ended July
3, 2004.
|
|
|
|
10.8A
|
|
Performance
Share Unit Plan for Textron Employees. Incorporated by reference to Exhibit
10.2 to Textrons Quarterly Report on Form 10-Q for the fiscal quarter ended
April 2, 2005.
|
|
|
|
10.8B
|
|
Performance
Factors for Executive Officers for Performance Share Units.
|
|
|
|
10.9
|
|
Form of
Indemnity Agreement between Textron and its directors and executive officers.
Incorporated by reference to Exhibit A to Textrons Proxy Statement for its
Annual Meeting of Shareholders on April 29, 1987.
|
|
|
|
10.10
|
|
Deferred Income
Plan for Non-Employee Directors. Incorporated by reference to Exhibit 10.1 to
Textrons Annual Report on Form 10-K for the fiscal year ended December 28,
2002.
|
|
|
|
10.11A
|
|
Amended and
Restated Employment Agreement between Textron and John D. Butler dated May 4,
2006. Incorporated by reference to Exhibit 10.2 to Textrons Quarterly Report
on Form 10-Q for the fiscal quarter ended April 1, 2006.
|
|
|
|
10.11B
|
|
Restricted Stock
Equivalent Award granted to John D. Butler on January 15, 2002. Incorporated
by reference to Exhibit 10.1 of Textrons Quarterly Report on Form 10-Q for
the fiscal quarter ended March 30, 2002.
|
|
|
|
10.12A
|
|
Employment
Agreement between Textron and Lewis B. Campbell dated July 23, 1998.
Incorporated by reference to Exhibit 10.3 to Textrons Quarterly Report on
Form 10-Q for the fiscal quarter ended October 3, 1998.
|
|
|
|
10.12B
|
|
Amendment dated
May 6, 2005, to Employment Agreement between Textron and Lewis B. Campbell.
Incorporated by reference to Exhibit 10.3 to Textrons Quarterly Report on
Form 10-Q for the fiscal quarter ended April 2, 2005.
|
|
|
|
10.12C
|
|
Second
Amendment, dated May 4, 2006, to Employment Agreement between Textron and
Lewis B. Campbell. Incorporated by reference to Exhibit 10.4 to Textrons
Quarterly Report on Form 10-Q for the fiscal quarter ended April 1, 2006.
|
|
|
|
10.12D
|
|
Retention Award
granted to Lewis B. Campbell on December 14, 1995. Incorporated by reference
to Exhibit 10.16B to Textrons Annual Report on Form 10-K for the fiscal year
ended December 30, 1995.
|
|
|
|
10.12E
|
|
Retention Award
granted to Lewis B. Campbell on June 1, 1999. Incorporated by reference to
Exhibit 10.13C to Textrons Annual Report on Form 10-K for the fiscal year
ended January 1, 2000.
|
|
|
|
10.12F
|
|
Retention Award
granted to Lewis B. Campbell on January 1, 2001, and revision of vesting
schedule for the Retention Award granted on June 1, 1999. Incorporated by
reference to Exhibit 10.14D to Textrons Annual Report on Form 10-K for the
fiscal year ended December 30, 2000.
|
|
|
|
10.12G
|
|
Amendments to
Retention Awards granted to Lewis B. Campbell. Incorporated by reference to
Exhibit 10.14D to Textrons Annual Report on Form 10-K for the fiscal year
ended December 29, 2001.
|
|
|
|
10.13A
|
|
Employment Agreement
between Textron and Ted R. French dated December 21, 2000. Incorporated by
reference to Exhibit 10.15A to Textrons Annual Report on Form 10-K for the
fiscal year ended December 30, 2000.
|
|
|
|
10.13B
|
|
Retention Award
granted to Ted R. French on January 1, 2001. Incorporated by reference to
Exhibit 10.15B to Textrons Annual Report on Form 10-K for the fiscal year
ended December 30, 2000.
|
|
|
|
10.14A
|
|
Amended and
Restated Employment Agreement between Textron and Mary L. Howell dated May 4,
2006. Incorporated by reference to Exhibit 10.1 to Textrons Quarterly Report
on Form 10-Q for the fiscal quarter ended April 1, 2006.
|
|
|
|
10.14B
|
|
Restricted Stock
Equivalent Award granted to Mary L. Howell on January 15, 2002. Incorporated
by reference to Exhibit 10.2 of Textrons Quarterly Report on Form 10-Q for
the fiscal quarter ended March 30, 2002.
|
|
|
|
10.15A
|
|
Amended and
Restated Employment Agreement between Textron and Terrence ODonnell dated
May 4, 2006. Incorporated by reference to Exhibit 10.3 to Textrons Quarterly
Report on Form 10-Q for the fiscal quarter ended April 1, 2006.
|
|
|
|
10.15B
|
|
Restricted Stock
Equivalent Award granted to Terrence ODonnell on January 15, 2002.
Incorporated by reference to Exhibit 10.3 of Textrons Quarterly Report on Form
10-Q for the fiscal quarter ended March 30, 2002.
|
|
|
|
10.16
|
|
Employment
Agreement between Textron and Kenneth C. Bohlen dated July 18, 2000.
Incorporated by reference to Exhibit 10.2 to Textrons Quarterly Report on
Form 10-Q for the fiscal quarter ended July 1, 2000.
|
|
|
|
10.17
|
|
Director Compensation.
|
|
|
|
10.18
|
|
Director Stock
Awards. Incorporated by reference to Exhibit 10.17 to Textrons Annual Report
on Form 10-K for the fiscal year ended December 28, 2002.
|
|
|
|
10.19
|
|
CitationShares
Directors Evaluation Program. Incorporated by reference to Exhibit 10.17 to
Textrons Annual Report on Form 10-K for the fiscal year ended January 1,
2005.
|
|
|
|
10.20
|
|
Amendment to 13
plans to comply with the American Jobs Creation Act of 2004. Incorporated by
reference to Exhibit 10.18 to Textrons Annual Report on Form 10-K for the
fiscal year ended January 1, 2005.
|
|
|
|
10.21A
|
|
5-Year Credit
Agreement, dated as of March 28, 2005, among Textron, the Banks listed
therein, JPMorgan Chase Bank, N.A., as Administrative Agent, and Citibank,
N.A., as Syndication Agent (the 5-Year Credit Agreement). Incorporated by
reference to Exhibit 10.1 to Textrons Current Report on Form 8-K filed March
31, 2005.
|
|
|
|
10.21B
|
|
Amendment No. 1,
dated as of April 21, 2006, to 5-Year Credit Agreement. Incorporated by
reference to Exhibit 10.1 to Textrons Current Report on Form 8-K filed April
25, 2006.
|
|
|
|
10.22A
|
|
364-Day Credit
Agreement dated March 31, 2003, among Textron Inc., the Banks listed therein
and JPMorgan Chase Bank as Administrative Agent (the 364-Day Credit
Agreement). Incorporated by reference to Exhibit 10.3 to Textrons Quarterly
Report on Form 10-Q for the fiscal quarter ended March 29, 2003.
|
|
|
|
10.22B
|
|
Amendment, dated
as of July 28, 2003, to the 364-Day Credit Agreement. Incorporated by
reference to Exhibit 10.19 to Textrons Annual Report on Form 10-K for the
fiscal year ended January 3, 2004.
|
|
|
|
10.22C
|
|
Amendment No. 2,
dated as of March 29, 2004, to the 364-Day Credit Agreement. Incorporated by
reference to Exhibit 10.1 to Textrons Quarterly Report on Form 10-Q for the
fiscal quarter ended April 3, 2004.
|
|
|
|
10.23A
|
|
364-Day Credit
Agreement dated July 28, 2003, among Textron Financial Corporation, the Banks
listed therein, and JPMorgan Chase Bank, as Administrative Agent.
Incorporated by reference to Exhibit 10.1 to Textron Financial Corporations
Current Report on Form 8-K as filed on August 26, 2003.
|
|
|
|
10.23B
|
|
Amendment, dated
as of July 26, 2004, to 364-Day Credit Agreement dated July 28, 2003, among
Textron Financial Corporation, the Banks listed therein, and JPMorgan Chase
Bank, as Administrative Agent. Incorporated by reference to Exhibit 10.1 to
Textron Financial Corporations Quarterly Report on Form 10-Q for the fiscal
quarter ended September 30, 2004.
|
|
|
|
10.23C
|
|
Amendment No. 2,
dated as of July 25, 2005, to the 364-Day Credit Agreement dated as of July
28, 2003, among Textron Financial, the Banks listed therein, and JPMorgan
Chase Bank N.A., as Administrative Agent. Incorporated by reference to
Exhibit 10.2 of Textron Financial Corporations Current Report on Form 8-K
filed July 27, 2005.
|
|
|
|
10.24A
|
|
Five-Year Credit
Agreement dated July 28, 2003 among Textron Financial Corporation, the Banks
listed therein, and JPMorgan Chase Bank, as Administrative Agent.
Incorporated by reference to Exhibit 10.2 to Textron Financial Corporations
Current Report on Form 8-K as filed on August 26, 2003.
|
|
|
|
10.24B
|
|
Amendment No. 1,
dated as of July 25, 2005, to the Five-Year Credit Agreement dated as of July
28, 2003 among Textron Financial, the Banks listed therein, and JPMorgan
Chase Bank N.A., as Administrative Agent. Incorporated by reference to
Exhibit 10.1 of Textron Financial Corporations Current Report on Form 8-K
filed July 27, 2005.
|
|
|
|
10.24C
|
|
Amendment No. 2,
dated as of April 28, 2006, to the Five-Year Credit Agreement dated as of
July 28, 2003 among Textron Financial, the Banks listed therein, and JPMorgan
Chase Bank N.A., as Administrative Agent. Incorporated by reference to
Exhibit 10.1 of Textron Financial Corporations Current Report on Form 8-K
filed May 1, 2006.
|
|
|
|
10.25
|
|
Master Services
Agreement between Textron Inc. and Computer Sciences Corporation dated
October 27, 2004. Confidential treatment has been requested for portions of
this agreement. Incorporated by reference to Exhibit 10.26 to Textrons
Annual Report on Form 10-K for the fiscal year ended January 1, 2005.
|
|
|
|
12.1
|
|
Computation of
ratio of income to combined fixed charges and preferred stock dividends of
Textron Manufacturing.
|
|
|
|
12.2
|
|
Computation of
ratio of income to combined fixed charges and preferred stock dividends of
Textron including all majority-owned subsidiaries.
|
|
|
|
21
|
|
Certain
subsidiaries of Textron. Other subsidiaries, which considered in the
aggregate do not constitute a significant subsidiary, are omitted from such
list.
|
|
|
|
23
|
|
Consent of
Independent Registered Public Accounting Firm.
|
|
|
|
24
|
|
Power of
attorney.
|
|
|
|
31.1
|
|
Certification of
Chief Executive Officer Pursuant to Rule 13a-14(a).
|
|
|
|
31.2
|
|
Certification of
Chief Financial Officer Pursuant to Rule 13a-14(a).
|
|
|
|
32.1
|
|
Certification of
Chief Executive Officer Pursuant to 18 U.S.C. Section 1350.
|
|
|
|
32.2
|
|
Certification of
Chief Financial Officer Pursuant to 18 U.S.C. Section 1350.
|
EX-10.1C
2
a07-4686_1ex10d1c.htm
EX-10.1C
Exhibit 10.1C
Objectives for Executive Officers
Under
Annual Incentive Compensation Plan for
Textron Employees
Under the Textron Annual Incentive Compensation Plan,
target annual incentive payments are recommended by the Organization and
Compensation Committee (the Committee) of the Board of Directors and approved
by the full Board. The targets for Executive Officers can range from 50%
to 100% of the Executive Officers base salary. The amount actually paid
generally can range from zero, if the threshold level of actual performance
relating to target performance objectives is not achieved, to no more than
twice the target award level.
The target performance objectives for Executive
Officers are set by the Board of Directors, and generally include such targets
as achieving earnings per share and specified leadership initiatives, including
financial goals and strategic and business initiatives such as six sigma,
customer growth, talent development, supply chain information technology and
compliance goals. The Board of Directors
can also provide for a potential multiplier based on return on invested
capital.
EX-10.8B
3
a07-4686_1ex10d8b.htm
EX-10.8B
Exhibit 10.8B
Performance Factors for Executive
Officers for Performance Share Units
Under the Performance Share Unit Plan for Textron
Employees, participants are awarded a number of performance share units that
are payable in cash at the end of the respective three-year performance
cycle. The payout is determined by multiplying the number of performance
share units earned by the then current market value of Textron common stock at
the end of the performance period. The number of performance share units earned
by Executive Officers at the end of the three-year performance cycle is
determined by the Board of Directors upon the recommendation of the
Organization and Compensation Committee (the Committee), and are based on
factors for each cycle determined by the Board of Directors. Such factors generally include Cumlative
earnings per share, average return on invested capital and accomplishment of
leadership initiatives such as strategic direction, company grownt, talen
development, enterprise management and portfolio management. The Board of Directors can also provide for
additional payout based on return on invested capital (ROIC).
Failure to attain a minimum EPS performance level (70%
of target) will result in the failure to earn any performance share units
related to the EPS portion of the award. Attainment between the minimum
and maximum EPS targets will result in earning a portion of the performance
share units related to the EPS portion of the award as defined by a
pre-established mathematical formula. The Committee may determine an award less
than that determined by the formula but may not determine an award more than
that derived by the formula.
With respect to the ROIC target, if enterprise-wide
ROIC averages 100 basis points or more above the WACC (weighted average cost of
capital) over the performance period, then this portion of the award will be
earned. If the difference between ROIC and WACC is between 0% and 1%,
then a pro rata portion of this amount is earned. In addition, participants
have an opportunity to earn up to an additional 30% for achieving ROIC stretch
targets.
Performance share units related to one or more
leadership initiatives will be earned only as determined by the Committee and
may not exceed more than 100% of the value of such units.
EX-10.17
4
a07-4686_1ex10d17.htm
EX-10.17
Exhibit 10.17
Director Compensation
For their service on the Board, non-employee directors
are paid an annual retainer of $110,000, plus $1,500 for each meeting of the
Board attended. Non-employee directors who serve on the Executive Committee or
one of the standing committees, other than the Audit Committee, receive $1,500
for each committee meeting attended, and the chairman of each such standing
committee receives an additional $5,000 per year. Non-employee directors who
serve on the Audit Committee receive $2,500 for each committee meeting
attended, and the chairman of the Audit Committee receives an additional
$15,000 per year.
Textron maintains a deferred income plan for
non-employee directors under which they may defer all or part of their cash
compensation until retirement from the Board. Deferrals are made either into an
interest bearing account which bears interest at the greater of 8% or the Moodys
Corporate Bond Yield Index rate, or into an account consisting of Textron stock
units, which are equivalent in value to Textron common stock. Directors must
defer a minimum of $65,000 of their annual retainer into the stock unit account.
At the end of each calendar quarter, Textron contributes to the stock unit
account an additional amount equal to 10% of the amount deferred by the
director into this account during the quarter in excess of the minimum deferral
amount. One half of this additional amount vests on December 31 of the year in
which payment was deferred and one half on the next December 31. Textron also
credits dividend equivalents to the stock unit account. In addition, once a
year, on April 30, Textron contributes to the stock unit account an amount
equal to 20% of the then current annual retainer for each director who is
serving as a director on the date of Textrons annual meeting of shareholders
and has been a director for more than three months.
Each non-employee director received 1,000 restricted
shares of Textron common stock upon joining the Board. Except in the case of
the directors death or disability, or a change in control of Textron, the
director may not sell or transfer the shares until he or she has completed all
of his or her successive terms as a director and at least five years of Board
service.
Employee directors do not receive fees or other
compensation for their service on the Board or its Committees, but, if
otherwise eligible, can participate in the Textron Charitable Trust Program
described below. Each member of the Board is reimbursed for expenses incurred
in connection with each Board or committee meeting attended.
Textron sponsors a program under which it contributes
up to $1,000,000 to the Textron Charitable Trust on behalf of each director
upon his or her death, and the trust donates 50% of that amount in accordance
with the directors recommendation among up to five charitable organizations.
Payment of the contributions ultimately are recovered from life insurance
policies that Textron maintains on the lives of directors for this
purpose. The directors do not receive any
direct financial benefit from this program since the insurance proceeds and
charitable deductions accrue solely to Textron.
The program was closed to new participants in 2004.
Non-employee directors also participate in the
CitationShares Directors Evaluation Program established by Textron to provide
ongoing evaluation of the performance of the CitationShares fractional ownership
program, a joint venture between Cessna Aircraft Company, a wholly-owned
subsidiary of Textron, and TAG Aviation USA. Under the program, Textron
purchased a one-eighth ownership share of two Cessna Citation aircraft from
CitationShares entitling it to a fixed number of hours of usage of the aircraft
during the year, and makes ten hours of flight time per calendar year available
for personal use to the non-employee directors. Following each flight, a
participating director is expected to complete an evaluation of his or her
travel experience to assist Textron in ensuring that CitationShares maintains
its customer service focus. The aircraft also are utilized by Textron for
travel by executives and directors to and from Board meetings and other
Board-related activities. Directors are not charged for their participation in
the program or use of the aircraft.
However, directors pay tax on the imputed income attributable to their
personal use of the aircraft and the program requires participating directors
to reimburse Textron for its cost per hour of flight time to the extent their
personal use of the aircraft exceeds ten hours of flight time per calendar
year. Textron absorbs the cost of the ownership shares to the extent the
aircraft are not fully utilized.
Non-employee directors are also eligible to receive
grants of options to purchase Textron common stock under the Textrons Long-Term
Incentive Plans.
EX-12.1
5
a07-4686_1ex12d1.htm
EX-12.1
EXHIBIT
12.1
TEXTRON
INC.
MANUFACTURING GROUP
COMPUTATION
OF RATIO OF INCOME TO COMBINED FIXED
CHARGES AND PREFERRED STOCK DIVIDENDS
(Unaudited)
(In millions
except ratios)
|
|
Year
|
|
|
|
2006
|
|
2005
|
|
2004
|
|
2003
|
|
2002
|
|
Fixed charges:
|
|
|
|
|
|
|
|
|
|
|
|
Interest expense
|
|
$
|
101
|
|
$
|
96
|
|
$
|
100
|
|
$
|
101
|
|
$
|
130
|
|
Distributions on
preferred securities of subsidiary trusts, net of income taxes
|
|
|
|
|
|
|
|
13
|
|
26
|
|
Estimated
interest portion of rents
|
|
27
|
|
27
|
|
27
|
|
26
|
|
19
|
|
|
|
|
|
|
|
|
|
|
|
|
|
Total fixed
charges
|
|
$
|
128
|
|
$
|
123
|
|
$
|
127
|
|
$
|
140
|
|
$
|
175
|
|
|
|
|
|
|
|
|
|
|
|
|
|
Income:
|
|
|
|
|
|
|
|
|
|
|
|
Income from
continuing operations before income taxes and distributions on preferred
securities of subsidiary trusts
|
|
$
|
975
|
|
$
|
739
|
|
$
|
540
|
|
$
|
424
|
|
$
|
524
|
|
Fixed charges*
|
|
128
|
|
123
|
|
127
|
|
127
|
|
149
|
|
Eliminate equity
in undistributed pretax income of finance subsidiary
|
|
(130
|
)
|
(71
|
)
|
(69
|
)
|
(10
|
)
|
(65
|
)
|
|
|
|
|
|
|
|
|
|
|
|
|
Adjusted income
|
|
$
|
973
|
|
$
|
791
|
|
$
|
598
|
|
$
|
541
|
|
$
|
608
|
|
|
|
|
|
|
|
|
|
|
|
|
|
Ratio of income to fixed charges
|
|
7.60
|
|
6.43
|
|
4.71
|
|
3.86
|
|
3.47
|
|
*Adjusted to
exclude distributions on preferred securities of subsidiary trusts, net of
income taxes.
EX-12.2
6
a07-4686_1ex12d2.htm
EX-12.2
EXHIBIT
12.2
TEXTRON
INC. INCLUDING ALL MAJORITY-OWNED SUBSIDIARIES
COMPUTATION
OF RATIO OF INCOME TO COMBINED FIXED
CHARGES AND PREFERRED STOCK DIVIDENDS
(Unaudited)
(In millions
except ratios)
|
|
Year
|
|
|
|
2006
|
|
2005
|
|
2004
|
|
2003
|
|
2002
|
|
Fixed charges:
|
|
|
|
|
|
|
|
|
|
|
|
Interest expense
|
|
$
|
452
|
|
$
|
314
|
|
$
|
253
|
|
$
|
273
|
|
$
|
319
|
|
Distributions on
preferred securities of subsidiary trusts, net of income taxes
|
|
|
|
|
|
|
|
13
|
|
26
|
|
Estimated
interest portion of rents
|
|
30
|
|
30
|
|
30
|
|
29
|
|
22
|
|
|
|
|
|
|
|
|
|
|
|
|
|
Total fixed
charges
|
|
$
|
482
|
|
$
|
344
|
|
$
|
283
|
|
$
|
315
|
|
$
|
367
|
|
|
|
|
|
|
|
|
|
|
|
|
|
Income:
|
|
|
|
|
|
|
|
|
|
|
|
Income from
continuing operations before income taxes and distributions on preferred securities
of subsidiary trusts
|
|
$
|
975
|
|
$
|
739
|
|
$
|
540
|
|
$
|
424
|
|
$
|
524
|
|
Fixed charges*
|
|
482
|
|
344
|
|
283
|
|
302
|
|
341
|
|
|
|
|
|
|
|
|
|
|
|
|
|
Adjusted income
|
|
$
|
1,457
|
|
$
|
1,083
|
|
$
|
823
|
|
$
|
726
|
|
$
|
865
|
|
|
|
|
|
|
|
|
|
|
|
|
|
Ratio of income to fixed charges
|
|
3.02
|
|
3.15
|
|
2.91
|
|
2.30
|
|
2.36
|
|
*Adjusted to
exclude distributions on preferred securities of subsidiary trusts, net of
income taxes.
EX-21
7
a07-4686_1ex21.htm
EX-21
Exhibit 21
Certain Subsidiaries of
Textron
(Unless indicated otherwise, all entities listed are
wholly-owned.)
Name
|
|
Jurisdiction
|
TEXTRON INC.
|
|
Delaware
|
Aktiebolaget
Benzlers
|
|
Sweden
|
Benzler
Antriebstechnik Ges.mbH
|
|
Austria
|
Benzler
Antriebstechnik GmbH
|
|
Germany
|
Benzler
S.P.R.L./B.V.B.A. (50%; 50% - Benzler-TBA
B.V.)
|
|
Belgium
|
Benzler-TBA B.V.
|
|
Netherlands
|
Benzler
Transmission A.S.
|
|
Denmark
|
OY Benzler AB
|
|
Finland
|
Avco Corporation
|
|
Delaware
|
ARS Two Inc.
|
|
Delaware
|
Avco Rhode
Island (2002) Inc.
|
|
Delaware
|
Christine Realty
Co., Inc.
|
|
Pennsylvania
|
Ocean
Acquisition LLC
|
|
Delaware
|
AIS Acquisition
Corp.
|
|
Delaware
|
AIS Holding
Company, LLC
|
|
Delaware
|
AIS Holding
Company, LLP (99%; 1% - AIS Holding Company, LLC)
|
|
Texas
|
AIS GP, LLC
|
|
Texas
|
Overwatch
Systems, Ltd. (99% and Limited Partner; 1% and General
Partner AIS GP, LLC)
|
|
Texas
|
Overwatch MRI
Research, Inc.
|
|
Delaware
|
Overwatch
Systems of Virginia, Inc.
|
|
Virginia
|
Medical
Numerics, Inc.
|
|
Virginia
|
Visual Learning
Systems, Inc.
|
|
Montana
|
Textron Pacific
Limited
|
|
Australia
|
Textron Systems
Corporation
|
|
Delaware
|
Textron Systems
Childrens Center, Inc. (not-for-profit)
|
|
Massachusetts
|
Textron Systems
Rhode Island (2001) Inc.
|
|
Delaware
|
Bell Aircraft
Services Company
|
|
Delaware
|
Edwards &
Associates, Inc.
|
|
Tennessee
|
Aeronautical
Accessories, Inc.
|
|
Tennessee
|
Aeronautical
Accessories Rhode Island (2001) Inc.
|
|
Delaware
|
Aeronautical
Rotor Blades, Inc.
|
|
Tennessee
|
Edwards &
Associates Rhode Island (2002) Inc.
|
|
Delaware
|
Bell Helicopter Textron
Inc.
|
|
Delaware
|
BHT Energy
Company
|
|
Delaware
|
Bell Aerospace
Services Inc.
|
|
Delaware
|
Bell/Agusta
Aerospace Company LLC (60%; 40% - Agusta US,
Inc.)
|
|
Delaware
|
Bell Helicopter
Rhode Island Inc.
|
|
Delaware
|
Bell Helicopter
Services Inc.
|
|
Delaware
|
Bell Helicopter
Asia (Pte) Ltd.
|
|
Singapore
|
Bell Helicopter
do Brasil Ltda. (99.99%; 0.01% - Bell Helicopter Textron
Inc.)
|
|
Brazil
|
Bell Helicopter
India Inc.
|
|
Delaware
|
Bell Helicopter
Korea Inc.
|
|
Delaware
|
Bell Technical
Services Inc.
|
|
Delaware
|
Cadillac Gage
Textron Inc.
|
|
Michigan
|
Cessna Aircraft
Company
|
|
Kansas
|
Cessna Aircraft
Rhode Island Inc.
|
|
Delaware
|
CitationShares
Holding, L.L.C. (86.1%; 13.9% - TAG Aviation USA, Inc.)
|
|
Delaware
|
CitationShares
Charter, L.L.C.
|
|
Delaware
|
CitationShares
Management, L.L.C.
|
|
Delaware
|
CitationShares
Sales, Inc.
|
|
Delaware
|
Cone Drive
Operations Inc.
|
|
Delaware
|
David Brown
(Delaware) Holdings Corp.
|
|
Delaware
|
Union Pump
Company
|
|
Michigan
|
Union Pump
Canada Limited (93%; 7% - David Brown Engineering
Limited)
|
|
New Brunswick
|
1
Name
|
|
Jurisdiction
|
TEXTRON INC. (continued from prior page)
|
|
|
Greenlee Textron Inc.
|
|
Delaware
|
Greenlee Plumbing Inc.
|
|
Delaware
|
HR Textron Inc.
|
|
Delaware
|
Kautex Inc.
|
|
Delaware
|
McCord Corporation
|
|
Michigan
|
Kautex of Georgia Inc.
|
|
Massachusetts
|
Textron Holdco Inc.
|
|
Rhode Island
|
MAAG Pump Systems Textron Inc.
|
|
North Carolina
|
Opto Acquisition Inc.
|
|
Ontario
|
Opto-Electronics Inc.
|
|
Ontario
|
Textron Asia
Inc.
|
|
Delaware
|
Textron Atlantic
Inc.
|
|
Delaware
|
David Brown
(Thailand) Ltd.
|
|
Thailand
|
Elektrotechnische
Spezialerzeugnisse Handels Vermietungs und Verpachtungs GmbH
|
|
Germany
|
E-Z-GO Canada
Limited
|
|
Canadian Federal
|
Jacobsen E-Z-GO Textron B.V. (liquidation in process)
|
|
Netherlands
|
Kautex Textron India Pvt. Ltd. (99%; 1% - Kautex
Textron Verwaltungs-GmbH; liquidation in progress)
|
|
India
|
Klauke
Handelsgesellschaft m.b.H.
|
|
Austria
|
MAAG Textron
Holding A.G.
|
|
Switzerland
|
MAAG Pump
Systems Textron A.G.
|
|
Switzerland
|
Textron
Acquisition Limited
|
|
England
|
David Brown
Group plc
|
|
England
|
David Brown Benzlers A/S (90.9%; 9.1% -
Aktiebolaget Benzlers)
|
|
Norway
|
David Brown
Engineering Ltd.
|
|
England
|
David Brown
Defence Equipment Ltd.
|
|
England
|
David Brown
France Engrenages S.A.S.
|
|
France
|
David Brown Group Australian Partners (95%; 5% -
David Brown Group plc)
|
|
Australia
|
David Brown Corporation of Australia Pty. Ltd. (99.9%;
0.1% - David Brown Engineering Ltd.)
|
|
Australia
|
David Brown
Engineering & Hydraulics Pty. Ltd.
|
|
Australia
|
David Brown Gear
Industries Australia Pty. Ltd.
|
|
Australia
|
David Brown Gear
Industries Limited
|
|
Australia
|
David Brown
Hydraulics Ltd.
|
|
England
|
David Brown
Radicon Ltd.
|
|
England
|
David Brown Sadi
S.A.
|
|
Belgium
|
David Brown
Special Products Ltd.
|
|
England
|
David Brown
Transmissions France S.A.
|
|
France
|
David Brown
Union Pumps Ltd.
|
|
England
|
David Brown
Vehicle Products Ltd.
|
|
England
|
David Brown Gear
Industries (Pty) Ltd.
|
|
South Africa
|
David Brown
Hydraulics Danmark A/s
|
|
Denmark
|
David Brown
Hydraulics (Deutschland) GmbH
|
|
Germany
|
David Brown
Hydraulics Finland Oy
|
|
Finland
|
David Brown
Hydraulics Italia S.r.l.
|
|
Italy
|
David Brown
Investments Ltd.
|
|
England
|
David Brown
Pension Trustee Ltd.
|
|
England
|
Hygate
Transmissions Ltd.
|
|
England
|
2
Name
|
|
Jurisdiction
|
TEXTRON INC.
|
|
|
Textron Atlantic Inc.
|
|
|
Textron Acquisition Limited (continued from prior
page)
|
|
|
Ransomes
Investment Corporation
|
|
Delaware
|
Ransomes America
Corporation
|
|
Delaware
|
Cushman Inc.
|
|
Delaware
|
Ransomes Inc.
|
|
Wisconsin
|
Ransomes Rhode
Island Inc.
|
|
Delaware
|
STE Holding Inc.
|
|
Wisconsin
|
Ransomes plc
|
|
England
|
Ransomes Jacobsen
Limited
|
|
England
|
Ransomes
Overseas Services Limited
|
|
England
|
Ransomes
Pensions Trustee Company Limited
|
|
England
|
Ransomes
Property Developments Limited
|
|
England
|
Ransomes Sims
& Jeffries Limited
|
|
England
|
Textron Golf & Turf plc (99.9%; 1 share -Textron
Atlantic Inc.)
|
|
England
|
Textron Limited
|
|
England
|
Kautex Textron (UK) Limited
|
|
England
|
Textron Global Technology Center Private Limited (99.9%; 1
share Textron Inc.)
|
|
India
|
Textron Industrial S.r.l. (85%; 15% - Textron
International Inc.)
|
|
Italy
|
Textron International Holding, S.L.
|
|
Spain
|
Bell Helicopter Supply Center N.V.
|
|
Netherlands
|
Bell Helicopter Textron Canada Limited/Limitée
|
|
Canada
|
Bell Helicopter Canada International Inc.
|
|
Canada
|
Kautex Textron Iberica S.L.
|
|
Spain
|
Kautex Textron Argentina S.R.L. (99.9%; 1 share
Textron International Holding, S.L.; Liquidation in progress)
|
|
Argentina
|
Kautex Textron do Brasil Ltda. (99.9%; 1 share -
Textron International Holding, S.L.)
|
|
Brazil
|
Kautex Textron Portugal Produtos Plasticos, Ldas.
|
|
Portugal
|
MAAG-Textron Italia S.r.l. (90%; 10% - Textron
France E.U.R.L.)
|
|
Italy
|
Textron Capital B.V.
|
|
Netherlands
|
Textron France Holding S.A.R.L. (99.9%; 1 share
Textron France E.U.R.L.)
|
|
France
|
Cessna Citation European Service Center S.A.S. (99.9%; 1
share Textron France E.U.R.L.)
|
|
France
|
MAAG Pump Systems Textron S.A.R.L.
|
|
France
|
Textron France E.U.R.L.
|
|
France
|
Jacobsen E-Z-GO Textron S.r.l. (99%; 1% - Textron
International Holding, S.L.; liquidation in process)
|
|
Italy
|
Ransomes Jacobsen S.A.S.
|
|
France
|
Textron Atlantic Holding GmbH
|
|
Germany
|
Textron Holding
GmbH
|
|
Germany
|
Textron
Deutschland Beteiligungs-GmbH
|
|
Germany
|
Gustav Klauke GmbH (94.9%; 5.1% -
Textron International Holding, S.L.)
|
|
Germany
|
Gustav Klauke France S.A.R.L.
|
|
France
|
Kautex Textron Verwaltungs-GmbH (94.8%; 5.2% - Textron
International Holding, S.L.)
|
|
Germany
|
Kautex Textron CVS Limited
|
|
England
|
Kautex Textron GmbH & Co. K.G. (98.656778%; 0.671611% -
Textron Holding GmbH; 0.671611% - Textron Deutschland Beteiligungs-GmbH)
|
|
Germany
|
Kautex Corporation
|
|
Nova Scotia
|
Kautex
Textron Benelux B.V.B.A. (99.9%; 1 share - Kautex
Textron Iberica S.L.)
|
|
Belgium
|
Kautex Textron Bohemia spol. s.r.o.
|
|
Czech Republic
|
Kautex
Textron Italia S.r.l. (95%; 5% - Kautex
Textron Iberica S.L.)
|
|
Italy
|
3
Name
|
|
Jurisdiction
|
TEXTRON INC.
|
|
|
Textron Atlantic
Inc.
|
|
|
Textron
International Holding, S.L.
|
|
|
Textron France
Holding S.A.R.L.
|
|
|
Textron France
E.U.R.L.
|
|
|
Textron Atlantic
Holding GmbH
|
|
|
Textron Holding
GmbH
|
|
|
Textron
Deutschland Beteiligungs-GmbH
|
|
|
Kautex Textron
Verwaltungs-GmbH
|
|
|
Kautex Textron GmbH & Co. K.G. (continued from prior
page)
|
|
|
Kautex Lanbao (Changchun) Plastics Products Company, Limited (55%; 45% - Lanbao Technology Information Co., Ltd.)
|
|
PRC
|
Kautex Shanghai GmbH
|
|
Germany
|
Kautex (Guangzhou) Plastic Technology Co., Ltd.
|
|
PRC
|
Kautex (Shanghai) Plastic Products Co. Ltd.
|
|
PRC
|
Kautex (Shanghai) Plastic Technology Co., Ltd.
|
|
PRC
|
Kautex Textron de Mexico, S. de R.L. de C.V. (99.9%;
0.1% - Textron International Holding, S.L.)
|
|
Mexico
|
Kautex Textron Management Services Company de Puebla, S. de R.L. de
C.V. (98%; 2% - Kautex Textron GmbH & Co. K.G.)
|
|
Mexico
|
Kautex Textron Japan GmbH
|
|
Germany
|
Kautex Japan KK
|
|
Japan
|
MAAG Pump Systems Textron GmbH
|
|
Germany
|
Textron China Holdings S.R.L. (99%; 1% - Textron
International Holding, S.L.)
|
|
Barbados
|
Textron Trading
(Shanghai) Co., Ltd.
|
|
PRC
|
Textron Poland
Sp. z o.o.
|
|
Poland
|
Textron China
Inc.
|
|
Delaware
|
Textron
Communications Inc.
|
|
Delaware
|
Textron Far East
Pte. Ltd.
|
|
Singapore
|
Textron
Fastening Systems Inc.
|
|
Delaware
|
Avdel Cherry
Textron Inc.
|
|
New York
|
Ring Screw
Textron Inc.
|
|
Michigan
|
Textron
Fastening Systems Mississippi Inc.
|
|
Delaware
|
Textron
Financial Corporation
|
|
Delaware
|
Cessna Finance
Corporation
|
|
Kansas
|
Textron Financial
Canada Limited
|
|
Ontario
|
Textron
Financial Investment Corporation
|
|
Rhode Island
|
Textron Fluid
and Power Inc.
|
|
Delaware
|
Textron Global
Services Inc.
|
|
Delaware
|
Textron
International Inc.
|
|
Delaware
|
Textron IPMP
Inc.
|
|
Delaware
|
Textron
Innovations Inc.
|
|
Delaware
|
Textron
Management Services Inc.
|
|
Delaware
|
Textron Marine
Services Company
|
|
Delaware
|
Textron
Providence Inc.
|
|
Rhode Island
|
Textron Realty
Corporation
|
|
Delaware
|
Textron Rhode
Island Inc.
|
|
Delaware
|
TRAK
International, Inc.
|
|
Delaware
|
Turbine Engine
Components Textron (Newington Operations) Inc.
|
|
Connecticut
|
Westminster
Insurance Company
|
|
Vermont
|
4
EX-23
8
a07-4686_1ex23.htm
EX-23
Exhibit 23
Consent of Independent Registered Public Accounting
Firm
We consent to the incorporation by reference in the
following Registration Statements: Form
S-8 No. 333-101183 pertaining to the Textron Savings Plan, Form S-8 No.
333-101180 pertaining to the 1999 Long-Term Incentive Plan, Form S-8 No.
333-105100 related to the 1999 Long-term Incentive Plan, Form S-8 No. 333-78145
pertaining to the 1999 Long Term Incentive Plan, Form S-8 No. 333-124723
pertaining to the 1999 Long Term Incentive Plan, Form S-8 No. 333-50931
pertaining to the Textron Canada Savings Plan, Form S-8 No. 33-57025 pertaining
to the 1994 Long Term Incentive Plan, Form S-3 No. 333-113313 pertaining to the
$2 Billion Shelf Registration of Textron Inc. of our reports dated February 14,
2007, with respect to the consolidated financial statements and schedule of
Textron Inc., Textron Inc. managements assessment of the effectiveness of
internal control over financial reporting, and the effectiveness of internal
control over financial reporting of Textron Inc., included in the Annual Report
(Form 10-K) for the year ended December 30, 2006.
|
/s/ ERNST & YOUNG LLP
|
|
|
|
Boston, Massachusetts
|
|
February 20, 2007
|
|
EX-24
9
a07-4686_1ex24.htm
EX-24
Exhibit 24
POWER OF ATTORNEY
The
undersigned, Textron Inc. (Textron) a Delaware corporation, and the
undersigned directors and officers of Textron, do hereby constitute and appoint
Terrence ODonnell, Arnold M. Friedman, Michael D. Cahn and Ann T. Willaman,
and each of them, with full powers of substitution, their true and lawful
attorneys and agents to do or cause to be done any and all acts and things and
to execute and deliver any and all instruments and documents which said
attorneys and agents, or any of them, may deem necessary or advisable in order
to enable Textron to comply with the Securities and Exchange Act of 1934, as
amended, and any requirements of the Securities and Exchange Commission in
respect thereof, in connection with the filing of Textrons Annual Report on
Form 10-K for the fiscal year ended December 30, 2006, including specifically,
but without limitation, power and authority to sign the names of the
undersigned directors and officers in the capacities indicated below and to
sign the names of such officers on behalf of Textron to such Annual Report
filed with the Securities and Exchange Commission, to any and all amendments to
such Annual Report, to any instruments or documents or other writings in which
the original or copies thereof are to be filed as a part of or in connection
with such Annual Report or amendments thereto, and to file or cause to be filed
the same with the Securities and Exchange Commission; and each of the
undersigned hereby ratifies and confirms all that such attorneys and agents,
and each of them, shall do or cause to be done hereunder and such attorneys and
agents, and each of them, shall have, and may exercise, all of the powers
hereby conferred.
IN WITNESS WHEREOF, Textron has caused this Power of
Attorney to be executed and delivered in its name and on its behalf by the
undersigned duly authorized officer and its corporate seal affixed, and each of
the undersigned has signed his or her name thereto, as of the 16th day of
February, 2007.
|
TEXTRON INC.
|
|
|
|
|
|
By:
|
/s/ Lewis B. Campbell
|
|
|
|
Lewis B. Campbell
|
|
|
Chairman, President and Chief
|
|
|
Executive Officer
|
ATTEST:
|
|
|
|
|
|
/s/ Frederick K. Butler
|
|
|
Frederick K. Butler
|
|
Vice President and Secretary
|
|
|
|
|
|
|
/s/ Lewis B. Campbell
|
|
/s/ Paul E. Gagné
|
|
Lewis B. Campbell
|
Paul E. Gagné
|
Chairman, President and Chief Executive
|
Director
|
Officer, Director
|
|
|
|
|
|
/s/ H. Jesse Arnelle
|
|
/s/ Dain M. Hancock
|
|
H. Jesse Arnelle
|
Dain M. Hancock
|
Director
|
Director
|
|
|
|
|
/s/ Kathleen M. Bader
|
|
/s/ Lord Powell of Bayswater KCMG
|
|
Kathleen M. Bader
|
Lord Powell of Bayswater KCMG
|
Director
|
Director
|
|
|
|
|
/s/ R. Kerry Clark
|
|
/s/ Thomas B. Wheeler
|
|
R. Kerry Clark
|
Thomas B. Wheeler
|
Director
|
Director
|
|
|
|
|
/s/ Ivor J. Evans
|
|
/s/ Ted R. French
|
|
Ivor J. Evans
|
Ted R. French
|
Director
|
Executive Vice President
|
|
and Chief Financial Officer
|
|
(principal financial officer)
|
|
|
/s/ Lawrence K. Fish
|
|
|
Lawrence K. Fish
|
/s/ Richard L. Yates
|
|
Director
|
Richard L. Yates
|
|
Senior Vice President and Corporate Controller
|
|
(principal accounting officer)
|
/s/ Joe T. Ford
|
|
|
Joe T. Ford
|
|
Director
|
|
|
|
|
|
|
|
|
|
|
|
|
|
|
EX-31.1
10
a07-4686_1ex31d1.htm
EX-31.1
Exhibit 31.1
Certification
of Chief Executive Officer Pursuant to Section 302 of the Sarbanes-Oxley Act of
2002
I, Lewis B. Campbell, Chairman, President and Chief Executive Officer
of Textron Inc. certify that:
1. I have
reviewed this annual report on Form 10-K of Textron Inc.;
2. Based on my
knowledge, this report does not contain any untrue statement of a material fact
or omit to state a material fact necessary to make the statements made, in
light of the circumstances under which such statements were made, not
misleading with respect to the period covered by this report;
3. Based on my
knowledge, the financial statements, and other financial information included
in this report, fairly present in all material respects the financial
condition, results of operations and cash flows of the registrant as of, and
for, the periods presented in this report;
4. The
registrants other certifying officer and I are responsible for establishing
and maintaining disclosure controls and procedures (as defined in Exchange Act
Rules 13a-15(e) and 15d-15(e)) and internal control over financial reporting
(as defined in Exchange Act Rules 13a-15(f) and 15d-15(f)) for the registrant
and have:
a) designed
such disclosure controls and procedures, or caused such disclosure controls and
procedures to be designed under our supervision, to ensure that material
information relating to the registrant, including its consolidated
subsidiaries, is made known to us by others within those entities, particularly
during the period in which this report is being prepared;
b) designed
such internal control over financial reporting, or caused such internal control
over financial reporting to be designed under our supervision, to provide
reasonable assurance regarding the reliability of financial reporting and the
preparation of financial statements for external purposes in accordance with
generally accepted accounting principles;
c) evaluated
the effectiveness of the registrants disclosure controls and procedures and
presented in this report our conclusions about the effectiveness of the
disclosure controls and procedures, as of the end of the period covered by this
report based on such evaluation; and
d) disclosed in
this report any change in the registrants internal control over financial
reporting that occurred during the registrants most recent fiscal quarter (the
registrants fourth fiscal quarter in the case of an annual report) that has
materially affected, or is reasonably likely to materially affect, the
registrants internal control over financial reporting; and
5. The
registrants other certifying officer and I have disclosed, based on our most
recent evaluation of internal control over financial reporting, to the
registrants auditors and the audit committee of the registrants board of directors
(or persons performing the equivalent functions):
a) all
significant deficiencies and material weaknesses in the design or operation of
internal control over financial reporting which are reasonably likely to
adversely affect the registrants ability to record, process, summarize and
report financial information; and
b) any fraud,
whether or not material, that involves management or other employees who have a
significant role in the registrants internal control over financial reporting.
Date: February 21, 2007
|
/s/Lewis B. Campbell
|
|
Lewis B. Campbell
|
|
Chairman,
President and Chief Executive
Officer
|
EX-31.2
11
a07-4686_1ex31d2.htm
EX-31.2
Exhibit 31.2
Certification
of Chief Financial Officer Pursuant to Section 302 of the Sarbanes-Oxley Act of
2002
I, Ted R. French, Executive Vice President and Chief Financial Officer
of Textron Inc. certify that:
1. I have
reviewed this annual report on Form 10-K of Textron Inc.;
2. Based on my
knowledge, this report does not contain any untrue statement of a material fact
or omit to state a material fact necessary to make the statements made, in
light of the circumstances under which such statements were made, not
misleading with respect to the period covered by this report;
3. Based on my
knowledge, the financial statements, and other financial information included
in this report, fairly present in all material respects the financial
condition, results of operations and cash flows of the registrant as of, and
for, the periods presented in this report;
4. The
registrants other certifying officer and I are responsible for establishing
and maintaining disclosure controls and procedures (as defined in Exchange Act
Rules 13a-15(e) and 15d-15(e)) and internal control over financial reporting
(as defined in Exchange Act Rules 13a-15(f) and 15d-15(f)) for the registrant
and have:
a) designed
such disclosure controls and procedures, or caused such disclosure controls and
procedures to be designed under our supervision, to ensure that material
information relating to the registrant, including its consolidated
subsidiaries, is made known to us by others within those entities, particularly
during the period in which this report is being prepared;
b) designed
such internal control over financial reporting, or caused such internal control
over financial reporting to be designed under our supervision, to provide
reasonable assurance regarding the reliability of financial reporting and the
preparation of financial statements for external purposes in accordance with
generally accepted accounting principles;
c) evaluated
the effectiveness of the registrants disclosure controls and procedures and
presented in this report our conclusions about the effectiveness of the
disclosure controls and procedures, as of the end of the period covered by this
report based on such evaluation; and
d) disclosed in
this report any change in the registrants internal control over financial
reporting that occurred during the registrants most recent fiscal quarter (the
registrants fourth fiscal quarter in the case of an annual report) that has
materially affected, or is reasonably likely to materially affect, the
registrants internal control over financial reporting; and
5. The
registrants other certifying officer and I have disclosed, based on our most
recent evaluation of internal control over financial reporting, to the
registrants auditors and the audit committee of the registrants board of directors
(or persons performing the equivalent functions):
a) all
significant deficiencies and material weaknesses in the design or operation of
internal control over financial reporting which are reasonably likely to
adversely affect the registrants ability to record, process, summarize and
report financial information; and
b) any fraud,
whether or not material, that involves management or other employees who have a
significant role in the registrants internal control over financial reporting.
Date: February 21, 2007
|
/s/Ted R. French
|
|
Ted R. French
|
|
Executive
Vice President and Chief
Financial Officer
|
EX-32.1
12
a07-4686_1ex32d1.htm
EX-32.1
Exhibit
32.1
TEXTRON
INC.
CERTIFICATION
PURSUANT TO
18 U.S.C. SECTION 1350,
AS ADOPTED PURSUANT TO
SECTION 906 OF THE SARBANES-OXLEY ACT OF 2002
In connection with the Annual Report of Textron Inc.
(the Company) on Form 10-K for the period ended December 30, 2006 as filed
with the Securities and Exchange Commission on the Date hereof (the Report),
I, Lewis B. Campbell, Chairman, President and Chief Executive Officer of the
Company, certify, pursuant to 18 U.S.C. Section 1350, as adopted pursuant to
Section 906 of the Sarbanes-Oxley Act of 2002, that to my knowledge:
(1) The Report fully
complies with the requirements of section 13(a) or 15(d) of the Securities
Exchange Act of 1934; and
(2) The information
contained in the Report fairly presents, in all material respects, the
financial condition and results of operations of the Company.
Date: February 21, 2007
|
/s/ Lewis B. Campbell
|
|
Lewis B. Campbell
|
|
Chairman,
President and Chief Executive
Officer
|
EX-32.2
13
a07-4686_1ex32d2.htm
EX-32.2
Exhibit
32.2
TEXTRON
INC.
CERTIFICATION PURSUANT TO
18 U.S.C. SECTION 1350,
AS ADOPTED PURSUANT TO
SECTION 906 OF THE
SARBANES-OXLEY ACT OF 2002
In connection with the Annual Report of Textron Inc.
(the Company) on Form 10-K for the period ended December 30, 2006 as filed
with the Securities and Exchange Commission on the Date hereof (the Report),
I, Ted R. French, Executive Vice President and Chief Financial Officer of the
Company, certify, pursuant to 18 U.S.C. Section 1350, as adopted pursuant to
Section 906 of the Sarbanes-Oxley Act of 2002, that to my knowledge:
(1) The Report fully
complies with the requirements of section 13(a) or 15(d) of the Securities
Exchange Act of 1934; and
(2) The information
contained in the Report fairly presents, in all material respects, the
financial condition and results of operations of the Company.
Date: February 21, 2007
|
/s/Ted R. French
|
|
Ted R. French
|
|
Executive
Vice President and Chief
Financial Officer
|
GRAPHIC
14
g46861bci001.jpg
GRAPHIC
begin 644 g46861bci001.jpg
M_]C_X``02D9)1@`!`0$`8`!@``#_VP!#``H'!P@'!@H("`@+"@H+#A@0#@T-
M#AT5%A$8(Q\E)"(?(B$F*S7J#A(6&AXB)BI*3E)66EYB9FJ*CI*6FIZBIJK*SM+6VM[BYNL+#Q,7&
MQ\C)RM+3U-76U]C9VN'BX^3EYN?HZ>KQ\O/T]?;W^/GZ_\0`'P$``P$!`0$!
M`0$!`0````````$"`P0%!@<("0H+_\0`M1$``@$"!`0#!`<%!`0``0)W``$"
M`Q$$!2$Q!A)!40=A<1,B,H$(%$*1H;'!"2,S4O`58G+1"A8D-.$E\1<8&1HF
M)R@I*C4V-S@Y.D-$149'2$E*4U155E=865IC9&5F9VAI:G-T=79W>'EZ@H.$
MA8:'B(F*DI.4E9:7F)F:HJ.DI::GJ*FJLK.TM;:WN+FZPL/$Q<;'R,G*TM/4
MU=;7V-G:XN/DY>;GZ.GJ\O/T]?;W^/GZ_]H`#`,!``(1`Q$`/P#V6BL7Q)?:
M;I\%K+J#WF9KA;>&.TFD1G=SC&$89Z9Y]#CDX,$O]@PV]M?W_E7:[XF%]<
MG*\?,<-\JC(R3@#(S5)1ZLEN71?U]QT-%?9??_P#
M1HK._L*S_P">U_\`^#&X_P#BZ/["L_\`GM?_`/@QN/\`XNBT._X?\$+S[+[_
M`/@&C16=_85G_P`]K_\`\&-Q_P#%T?V%9_\`/:__`/!C\`Q=%H=_P_X(7G
MV7W_`/`-&BL[^PK/_GM?_P#@QN/_`(NC^PK/_GM?_P#@QN/_`(NBT._X?\$+
MS[+[_P#@&C16=_85G_SVO_\`P8W'_P`71_85G_SVO_\`P8W'_P`71:'?\/\`
M@A>?9??_`,`T:*SO["L_^>U__P"#&X_^+H_L*S_Y[7__`(,;C_XNBT._X?\`
M!"\^R^__`(!HT5G?V%9_\]K_`/\`!C?9??_P``T:*SO["L_P#GM?\`_@QN/_BZ/["L_P#GM?\`_@QN/_BZ+0[_
M`(?\$+S[+[_^`:-%9W]A6?\`SVO_`/P8W'_Q=']A6?\`SVO_`/P8W'_Q=%H=
M_P`/^"%Y]E]__`-&BL[^PK/_`)[7_P#X,;C_`.+H_L*S_P">U_\`^#&X_P#B
MZ+0[_A_P0O/LOO\`^`:-%9W]A6?_`#VO_P#P8W'_`,71_85G_P`]K_\`\&-Q
M_P#%T6AW_#_@A>?9??\`\`T:*SO["L_^>U__`.#&X_\`BZ/["L_^>U__`.#&
MX_\`BZ+0[_A_P0O/LOO_`.`:-%9W]A6?_/:__P#!CU_P#^#&X_^+H_L*S_`.>U
M_P#^#&X_^+HM#O\`A_P0O/LOO_X!HT5G?V%9_P#/:_\`_!CU__P"#&X_^+HM#O^'_``0O/LOO_P"`:-%9W]A6?_/:_P#_``8W
M'_Q=']A6?_/:_P#_``8W'_Q=%H=_P_X(7GV7W_\``-&BL[^PK/\`Y[7_`/X,
M;C_XNC^PK/\`Y[7_`/X,;C_XNBT._P"'_!"\^R^__@&C16=_85G_`,]K_P#\
M&-Q_\71_85G_`,]K_P#\&-Q_\71:'?\`#_@A>?9??_P#1HK._L*S_P">U_\`
M^#&X_P#BZ/["L_\`GM?_`/@QN/\`XNBT._X?\$+S[+[_`/@&C16=_85G_P`]
MK_\`\&-Q_P#%T?V%9_\`/:__`/!C\`Q=%H=_P_X(7GV7W_`/`-&BL[^PK/
M_GM?_P#@QN/_`(NK5K:1V<1CB:9E+;LRS/*?S8DXXZ4GR]&-.75$]%4M7U2#
M1=+FU"Y21XH=NX1@%CE@O&2.YKF?^%HZ'_SZW_\`W[3_`.+JX4:E17BKF,X!
MQ-SIJ*X_2/%]ZVDVCW]I'),;"WN))5FQO>9VC08VC!+`9[#)ZXYGNO&,UJT\
M1TQ&GLX9YKQ1<_+&(A&S;3M^8E95(R%]#CJ`#J:*YWQ3K$FDKIM]&7:)'GED
MB5MOFJEK,X4_BH_$41>)[B>Z>PBTU#J".V831PIQ(BAQ
MEHST##U/`!-)J$.J266GVEYIK:B)(-FH2VQB!8_+E`'9?E8YSCLN,6QGN%MXX[2.-VE=S@##J>F">,=^IP*@EN8(;>VN'\3W_E7:[XF
M$,)RO'S'$7RJ,C).`,C-4DGU)<\5J:/#=V^EPQ7TA>==V26W$+N)4%NY"X!/*095O+@'Z&+(^E/E7?
M\_\`(7,^S_#_`#-:BL[^S+S_`*#M_P#]\6__`,:H_LR\_P"@[?\`_?%O_P#&
MJ.5=_P`_\@YGV?X?YFC16=_9EY_T';__`+XM_P#XU1_9EY_T';__`+XM_P#X
MU1RKO^?^0?\`0=O_`/OB
MW_\`C5'*N_Y_Y!S/L_P_S-&BL[^S+S_H.W__`'Q;_P#QJC^S+S_H.W__`'Q;
M_P#QJCE7?\_\@YGV?X?YFC16=_9EY_T';_\`[XM__C5']F7G_0=O_P#OBW_^
M-4?]!V__P"^+?\`^-4?V9>?]!V__P"^
M+?\`^-4?\`0=O_`/OBW_\`C5']F7G_`$';
M_P#[XM__`(U1RKO^?^0?]!V__`.^+?_XU1_9EY_T';_\`
M[XM__C5'*N_Y_P"0?]!V_P#^^+?_`.-4?V9>?]!V
M_P#^^+?_`.-4?]
M!V__`.^+?_XU1RKO^?\`D',^S_#_`#-&BL[^S+S_`*#M_P#]\6__`,:H_LR\
M_P"@[?\`_?%O_P#&J.5=_P`_\@YGV?X?YFC16=_9EY_T';__`+XM_P#XU1_9
MEY_T';__`+XM_P#XU1RKO^?^0L-J-H/U(`'
MZ&IK7X<:1:2>9%(I+=S73%L[Y0@(]OE51C\.]34<+6@OSN5352
M]YM_A;_,?<6\%W`T%S#'-$V-TN#B.R\1?;-7O+#[)L%LLA#^9EOD;;\RX^7=U7DY`)XJ2A+;PGI]M;-
M`)+AU^SQVZ%F&42-V>/&`.5+<$Y^Z,Y.21_"EC*D_G37$LES;3V\TS,H:02[
M=S'"@;L(H&```.E)H7B"?5!:B[LDM7O;,7D`CG,H,?RY#$JN&&]>.1[\5+#X
MA26WGNGT^\AM8BP6=_+VRD/LPH#ELD],@4`2:MH-IK-K';732JD:R*OEL`
M$\1ZC^ZY_'%12>&K5KJ6ZBN+FWN)7W&6)EW`>6D9494C!$:Y[Y&013)?%=E!
M`))H+F-U\PS0E5WP+'MWLV&QA=RG@G.1C-7-1U:+3;BQCE"B.[E=&E9PJQ!8
MGD+'VPGZT`6+2T6SB,222-&,!%2RT^TO)['41)!LU"6VNK<%C\N4`=U^5CG..RXQSD:OC#4=1TS3K2;3W
M2)7OH(KF=DW^5$S@$[>_)`_'\0_4-3U.VTNUNX$LYB8@\NQBRS.=NV.+D?>)
M.&.<8'!SQ2<>J):ET?\`7WG+M+;;2+6^@@A@EBF>VFU9)A/(DZ29C)?"#"N.
M0N2PR!C-=%H&K:38Z2D-QK%@LK2RS,INXSMWR,^W(..-V/PJ"_U_6+.1H?*@
M:1MA/DVTEQ]D!8#:ZHV78KN/R[>GTSOZ;<_:].AG-Q'<%UYDCB,:DYP?E8DK
MCH03D$4[P[?C_P``5I]U]W_!(/\`A(M#_P"@S8?^!2?XT?\`"1:'_P!!FP_\
M"D_QK1HHO#M^/_`"T^Z^[_@F=_PD6A_]!FP_\"D_QH_X2+0_^@S8?^!2?XUH
MT47AV_'_`(`6GW7W?\$SO^$BT/\`Z#-A_P"!2?XT?\)%H?\`T&;#_P`"D_QK
M1HHO#M^/_`"T^Z^[_@F=_P`)%H?_`$&;#_P*3_&C_A(M#_Z#-A_X%)_C6C11
M>';\?^`%I]U]W_!,[_A(M#_Z#-A_X%)_C1_PD6A_]!FP_P#`I/\`&M&BB\.W
MX_\``"T^Z^[_`()G?\)%H?\`T&;#_P`"D_QH_P"$BT/_`*#-A_X%)_C6C11>
M';\?^`%I]U]W_!,[_A(M#_Z#-A_X%)_C1_PD6A_]!FP_\"D_QK1HHO#M^/\`
MP`M/NON_X)G?\)%H?_09L/\`P*3_`!H_X2+0_P#H,V'_`(%)_C6C11>';\?^
M`%I]U]W_``3._P"$BT/_`*#-A_X%)_C1_P`)%H?_`$&;#_P*3_&M&BB\.WX_
M\`+3[K[O^"9W_"1:'_T&;#_P*3_&C_A(M#_Z#-A_X%)_C6C11>';\?\`@!:?
M=?=_P3._X2+0_P#H,V'_`(%)_C1_PD6A_P#09L/_``*3_&M&BB\.WX_\`+3[
MK[O^"9W_``D6A_\`09L/_`I/\:/^$BT/_H,V'_@4G^-:-%%X=OQ_X`6GW7W?
M\$SO^$BT/_H,V'_@4G^-'_"1:'_T&;#_`,"D_P`:T:*+P[?C_P``+3[K[O\`
M@F=_PD6A_P#09L/_``*3_&C_`(2+0_\`H,V'_@4G^-:-%%X=OQ_X`6GW7W?\
M$SO^$BT/_H,V'_@4G^-'_"1:'_T&;#_P*3_&M&BB\.WX_P#`"T^Z^[_@F=_P
MD6A_]!FP_P#`I/\`&C_A(M#_`.@S8?\`@4G^-:-%%X=OQ_X`6GW7W?\`!,[_
M`(2+0_\`H,V'_@4G^-'_``D6A_\`09L/_`I/\:T:*+P[?C_P`M/NON_X)G?\
M)%H?_09L/_`I/\:/^$BT/_H,V'_@4G^-:-%%X=OQ_P"`%I]U]W_!,[_A(M#_
M`.@S8?\`@4G^-'_"1:'_`-!FP_\``I/\:T:*+P[?C_P`M/NON_X)G?\`"1:'
M_P!!FP_\"D_QH_X2+0_^@S8?^!2?XUHT47AV_'_@!:?=?=_P3._X2+0_^@S8
M?^!2?XT?\)%H?_09L/\`P*3_`!K1HHO#M^/_```M/NON_P""9W_"1:'_`-!F
MP_\``I/\:/\`A(M#_P"@S8?^!2?XUHT47AV_'_@!:?=?=_P3._X2+0_^@S8?
M^!2?XT?\)%H?_09L/_`I/\:NO<0Q_?FC7M\S`54EUS2(/];JMFF>1NN%&?UI
MI)[)_P!?(3+?#\>
M=VKVIQ_=?=_*JDGC_P`,QDC^T2Q!Q\L+G^E6J4GM!_U\C-U8K>:_KYFE_P`)
M%H?_`$&;#_P*3_&C_A(M#_Z#-A_X%)_C7/GQU=:BQ30-"NKSG`ED&U!^7]2*
M3^R_&NL#_3M5ATN)AS':C+C\1_\`%5?L$OCT^?Z6(]NW\&OR_5NQT#>)-"12
MQUFQP/2X0G\@:PM0^)6BVA*VJS7CCNB[5_,\_I4UG\/M%@E\Z\,^H3$Y+7$G
M!/T&,_CFNBM;.ULHA%:V\4"#^&-`H_2E>A%Z7?X%6Q$EJTOQ.#_X2W7=8R+>
M]T?2(6Z/-=(S_P`S_P"@BG)H6AWCB77?&,>H.#G8+M%0>W4_IBO0:*?UA+X%
M;T_SM?!FE`?8KG28F'1_M",_P#WT3FM+_A(M#_Z#-A_
MX%)_C6C16+DI.[O]_P#P#=1E%65ON_X)G?\`"1:'_P!!FP_\"D_QH_X2+0_^
M@S8?^!2?XUHT4KP[?C_P!VGW7W?\$SO^$BT/_H,V'_@4G^-6K6]M;Z(RV=S#
M<1AMI>*0.`?3([\BIZ*3Y>B&E+JS)\4Z%_PDOAVZTC[3]F^T;/WNS?MVNK=,
MC/W<=:\\_P"%&?\`4Q_^27_VRO6:*DH\F_X49_U,?_DE_P#;*ZSP-X&_X0O[
M=_Q,OMOVSR_^6'E[-N[_`&CG.[]*ZVB@#G=0T^_N-:6:&RCCE6>(QZA$P7$`
M*EXY!G+D_.`,8^8'@CG/L-%U:TU*&1+>:,L6&HS>K:11SL
M\S2$$*,J"2<*#G@<>E8DGAFYERK-'*IR,G`V,,O@_.>
MW-=K4$5[:3W$MO#=0R30G$L:2`LGU`Y'XT`?>'M4N7O[R*S99-6ANK=X7D
M3-N)4A17;!P0!#DA23\W&:TO&&BWNJ:;!;V,0E:-+A2"P7[UM+&O7_:=1^-=
M+10!QYT34;76KF^2Q^T0.[(D"N@R&MX4W\D#`,;`]\$X!Z',T_PEJUM!''<6
MSW&+=`8FEB$.?LJ0%6XWM@@G&=N`"/FKT"66.%-\LBQKD+N9@!DG`'XD@?C3
MZ`,KPY83Z7HZ6%PN7@=E\W.?/R<^8>^6SDY[Y^M:M,CECF4M%(L@#%258'!!
MP1]0013Z`.?\7VD%W96GGI<#R+N*>.>&2)/+=6&!^\=02V2!UY[=*KRV$Q%@
M+/3M9L%T^(Q0I`]HR[2`.0[-SA<9Z\GGDU'\0UA.EZ;),K'R]4MV4D9B!W8/
MF_[&"?QQZU#JLVE-I6C6UVXTJ>>U_P!&6ZG"BTX3+9;K(N0%[\GMG%)I="7%
MOK^1+::9?65N8(1XB"[BZ_O+$%7)R6)!&\GG._<#G/7!&I8S2Z?:);6^@:B$
M4L/;9MI\R[?G_F+E?\WY?Y$W]IWG_0"O\`_ONW
M_P#CM']IWG_0"O\`_ONW_P#CM:-%',NWY_YARON_P_R,[^T[S_H!7_\`WW;_
M`/QVC^T[S_H!7_\`WW;_`/QVM&BCF7;\_P#,.5]W^'^1G?VG>?\`0"O_`/ON
MW_\`CM']IWG_`$`K_P#[[M__`([6C11S+M^?^8?]`*__P"^
M[?\`^.T?VG>?]`*__P"^[?\`^.UHT4?]`*_P#^
M^[?_`..T?VG>?]`*_P#^^[?_`..UHT4?\`0"O_`/ONW_\`CM:-%',NWY_YARON_P`/\C._M.\_Z`5_
M_P!]V_\`\=H_M.\_Z`5__P!]V_\`\=K1HHYEV_/_`##E?=_A_D9W]IWG_0"O
M_P#ONW_^.T?VG>?]`*__`.^[?_X[6C11S+M^?^8'G'K@X_D:W5&=
MKN*2\]/U,'6A>RDV_+7]#H?[3O/^@%?_`/?=O_\`':S+_P`;V.F$B\L[F-AU
M02V[,/\`@(D)JE_PB&MZISKOB.9D(^:"U&U?Z#_QVM+3_!/A_3R&2P69Q_'.
M?,_0\?I1:C'XM?2_YM_H*]>7PZ>MOR2_4S5^(D=YG^R]#U&\QUP@X/\`P'=3
ME\5>)9QF'PA.F1QYDI'\U%=:B)&@1%"J.@48`IU3[2FMH?BRU3JO>?W)?\$X
M]]8\=2#]QX-9?];?ZDG.?W:6_])17?T57
MUE](Q^X7U5=9R^\\^7PUK;_\?-]XBE]=LT*\?C.:&\&+.,7-OXBF!'.;FVY_
M-S7H-%'UNH+ZI3\SA(_!>DI][P[J\G^]/1]+C^[X+E/&/F^SM_.6K44%K!_J?!T
MD??Y([4?^U*WJ*AUI/?\W_F6J*6WY+_(S1J5TH`70+\`=`'M_P#X[2_VG>?]
M`*__`.^[?_X[6C14?\`0"O_`/ONW_\`CM']IWG_
M`$`K_P#[[M__`([6C11S+M^?^8BDVGT&DUU*VH33V]E)+;1^;*N-J;2<\CL/:
ML;^V-<_Z!O\`Y`?_`!KHJ*DHYW^V-<_Z!O\`Y`?_`!K1TF\OKOS?MMMY.W;L
M^1ESG.>OX5HT4`]BO-1UW6X$2%;6/4K:X:7>?-W1Q0.%5=N.=H&[=W/%9M
MOXH\0SV%MF.<27C1.'46^]0T4LA"@MM"YC7!1TC56D.YV"
M@%C@#)]>`!^%5SI6G&"2`Z?:F&5_,>,PKM9O[Q&.3[T`9'AC4=1U6._N;N4!
MD>-(X$"E(R8(G.&`RWS.>2*X9B,@@$F-,#&/;GGM6LK1KI+MK6$W$
M:E$F,8WJIZ@'J!6=>>%])NWMS]AMHTBG,TB+`FV;Y'7##'(_>,?K]:`,W4+R
M:_\`!D,]Q@R?VA;QE@,!PMXBAOQ"@_C6$>L(Z*;W(O)9HPQB3%LJWJ0!AQ
MSA')^;(R![Y[8VT#0K`T,9B3;M0J-HVD%<#V(!'IBHVTZQ="C6=NRLKJ08EP
M0QRPZ=">3ZF@#A-+UG5+.Z%I;%Y85OY&DF_=+'-YE[)&=Q8@YP,@(#RPSQ72
M>'M3O+_4]1M[FZCDCM&V0[4VF9=S?O/PQLXXRC'N`-9-,T^,PE+&V4P$M$5B
M4>63U*\<9[XJ6.UMX2AB@B0QIL0J@&U?0>@X'%`&1XHOK;3[:U>ZN[J$37,<
M,45M%'(TLC,-O#JW0C/&.G+;E&TX!FW
M-M&T>1ELG^[FM*WL[FY@2:/7-357&0)((8V_%6B!'XBL&[OM)GM[J:YN[>YD
MEO1)Y<&J1PR"-/E0JP<>F[&X?>/.>*U-'UO3[?2X8K[7;!YUW9)O$8A=Q*@M
MGDA<`GN1FJM4[?@3>G_-^/\`P2]_9EY_T';_`/[XM_\`XU1_9EY_T';_`/[X
MM_\`XU1_PD6A_P#09L/_``*3_&C_`(2+0_\`H,V'_@4G^-%JG;\`O3_F_'_@
MA_9EY_T';_\`[XM__C5']F7G_0=O_P#OBW_^-4?\)%H?_09L/_`I/\:/^$BT
M/_H,V'_@4G^-%JG;\`O3_F_'_@A_9EY_T';_`/[XM_\`XU1_9EY_T';_`/[X
MM_\`XU1_PD6A_P#09L/_``*3_&C_`(2+0_\`H,V'_@4G^-%JG;\`O3_F_'_@
MA_9EY_T';_\`[XM__C5']F7G_0=O_P#OBW_^-4?\)%H?_09L/_`I/\:/^$BT
M/_H,V'_@4G^-%JG;\`O3_F_'_@A_9EY_T';_`/[XM_\`XU1_9EY_T';_`/[X
MM_\`XU1_PD6A_P#09L/_``*3_&C_`(2+0_\`H,V'_@4G^-%JG;\`O3_F_'_@
MA_9EY_T';_\`[XM__C5']F7G_0=O_P#OBW_^-4?\)%H?_09L/_`I/\:/^$BT
M/_H,V'_@4G^-%JG;\`O3_F_'_@A_9EY_T';_`/[XM_\`XU1_9EY_T';_`/[X
MM_\`XU1_PD6A_P#09L/_``*3_&C_`(2+0_\`H,V'_@4G^-%JG;\`O3_F_'_@
MA_9EY_T';_\`[XM__C5']F7G_0=O_P#OBW_^-4?\)%H?_09L/_`I/\:/^$BT
M/_H,V'_@4G^-%JG;\`O3_F_'_@A_9EY_T';_`/[XM_\`XU1_9EY_T';_`/[X
MM_\`XU1_PD6A_P#09L/_``*3_&C_`(2+0_\`H,V'_@4G^-%JG;\`O3_F_'_@
MA_9EY_T';_\`[XM__C5']F7G_0=O_P#OBW_^-4?\)%H?_09L/_`I/\:/^$BT
M/_H,V'_@4G^-%JG;\`O3_F_'_@A_9EY_T';_`/[XM_\`XU1_9EY_T';_`/[X
MM_\`XU1_PD6A_P#09L/_``*3_&C_`(2+0_\`H,V'_@4G^-%JG;\`O3_F_'_@
MA_9EY_T';_\`[XM__C5']F7G_0=O_P#OBW_^-4?\)%H?_09L/_`I/\:/^$BT
M/_H,V'_@4G^-%JG;\`O3_F_'_@A_9EY_T';_`/[XM_\`XU1_9EY_T';_`/[X
MM_\`XU2'Q'H8!)UFPX]+E/\`&LB_^(F@665BFDNW':%./S.!^5.,*LG91_`F
M4Z45=R_'_@FQ_9EY_P!!V_\`^^+?_P"-4?V9=_\`0>O_`/OBW_\`C5<'NJ
MZJ=NG1Z;81DD>9>7:9'X$C^1I/[.CU09U[QW;R*1\T-M1=^+[E7'5%6W=OR$1-8C^*K^]?\`0=O_`/OBW_\`
MC5'_``D6A_\`09L/_`I/\:/^$BT/_H,V'_@4G^-%JG;\`O3_`)OQ_P""']F7
MG_0=O_\`OBW_`/C5']F7G_0=O_\`OBW_`/C5'_"1:'_T&;#_`,"D_P`:/^$B
MT/\`Z#-A_P"!2?XT6J=OP"]/^;\?^"']F7G_`$';_P#[XM__`(U1_9EY_P!!
MV_\`^^+?_P"-4?\`"1:'_P!!FP_\"D_QH_X2+0_^@S8?^!2?XT6J=OP"]/\`
MF_'_`((?V9>?]!V__P"^+?\`^-4?V9>?]!V__P"^+?\`^-4?\)%H?_09L/\`
MP*3_`!H_X2+0_P#H,V'_`(%)_C1:IV_`+T_YOQ_X(?V9>?\`0=O_`/OBW_\`
MC5']F7G_`$';_P#[XM__`(U1_P`)%H?_`$&;#_P*3_&C_A(M#_Z#-A_X%)_C
M1:IV_`+T_P";\?\`@A_9EY_T';__`+XM_P#XU1_9EY_T';__`+XM_P#XU1_P
MD6A_]!FP_P#`I/\`&C_A(M#_`.@S8?\`@4G^-%JG;\`O3_F_'_@A_9EY_P!!
MV_\`^^+?_P"-4?V9>?\`0=O_`/OBW_\`C5'_``D6A_\`09L/_`I/\:/^$BT/
M_H,V'_@4G^-%JG;\`O3_`)OQ_P""']F7G_0=O_\`OBW_`/C5']F7G_0=O_\`
MOBW_`/C5'_"1:'_T&;#_`,"D_P`:/^$BT/\`Z#-A_P"!2?XT6J=OP"]/^;\?
M^"']F7G_`$';_P#[XM__`(U1_9EY_P!!V_\`^^+?_P"-4?\`"1:'_P!!FP_\
M"D_QH_X2+0_^@S8?^!2?XT6J=OP"]/\`F_'_`((?V9>?]!V__P"^+?\`^-4?
MV9>?]!V__P"^+?\`^-4?\)%H?_09L/\`P*3_`!H_X2+0_P#H,V'_`(%)_C1:
MIV_`+T_YOQ_X(?V9>?\`0=O_`/OBW_\`C56K6"2WB*2W
M2^C_`!)Z***S-`HHHH`****`"BBB@`HHHH`****`"BBB@#`\8:CJ.F:=:3:>
MZ1*]]!%>W2AX`VF
MVNG)X?U&*WM'A>)4EM^/*964?\`0"O_`/ONW_\`
MCM'(_P"F@YUY_?]`*__`.^[?_X[1_:=Y_T`K_\`[[M__CM'(_Z:#G7G
M]S-&BL[^T[S_`*`5_P#]]V__`,=H_M.\_P"@%?\`_?=O_P#':.1_TT'.O/[F
M:-%9W]IWG_0"O_\`ONW_`/CM']IWG_0"O_\`ONW_`/CM'(_Z:#G7G]S-&BL[
M^T[S_H!7_P#WW;__`!V@ZI=@9.A7_P#W\M__`([1R/\`IH.=>?W,T:*YJ]\<
MZ?I^1JU=(S>(
MI)V;.RHKB;C5O'MZFZRT.*T0]-[J7'_?3#^54_["\3:ASK-SK#@_>BMG@5?_
M`$:!^E4L.OM22^=R'B.D8-_*QVE[K6EZ=Q>7]O"?[KR#=^76L*X^(NC+)Y5E
M'=7\IZ+#$1G\\']*JV7A32;+!/A74;AP,;IYH&S^'F@?I6];7#6<8CM?#-U`
M@_AC^S*/TDI\M*/G\TO\Q<]67E\F_P#(Q1KWC#4_^0=X>2SC)_UEXW('K@[?
MY&C_`(1KQ3J0_P")KXD,*$Y,=HN./3(V_P!:Z#^T[S_H!7__`'W;_P#QVC^T
M[S_H!7__`'W;_P#QVCVC7P)+[G^8>S3^.3?WK\K&/:_#S0H6\RY6>]D)R6GE
M/)_#'ZUOV>F6&G+MLK."W!Z^7&%)^I[U!_:=Y_T`K_\`[[M__CM']IWG_0"O
M_P#ONW_^.U$Y5)_%+\32$:4/AC;Y&C16=_:=Y_T`K_\`[[M__CM']IWG_0"O
M_P#ONW_^.UGR/^FC3G7G]S-&BL[^T[S_`*`5_P#]]V__`,=H_M.\_P"@%?\`
M_?=O_P#':.1_TT'.O/[F:-%9W]IWG_0"O_\`ONW_`/CM']IWG_0"O_\`ONW_
M`/CM'(_Z:#G7G]S-&BL[^T[S_H!7_P#WW;__`!VC^T[S_H!7_P#WW;__`!VC
MD?\`30?]`*_P#^^[?_`..T?VG>?]`*_P#^^[?_`..T?W,T:*SO[3O/^@%?_P#?=O\`_':/[3O/^@%?_P#?=O\`_':.1_TT'.O/
M[F:-%9W]IWG_`$`K_P#[[M__`([1_:=Y_P!`*_\`^^[?_P".TV&/_(M'(_Z:#G7G]S-B
MBN=F\:Z?;J&FC\H'@%[VT&?SFJL_Q%T1,Y9>/2]M3_*6CD?]-!SKS^YG5T5Q
MK_%#P_&`6\TY_NS0-_*2JLGQA\,Q.4:.^)']V-&'YAL4?W,[RBN`
M/QF\,#_ECJ!_[8K_`/%4T_&CPR/^774C](4_^+J>5E)W/0:*\[E^+D/?&MYA;#PW;6V3UGD+X'TRM(9Z;17EQG^)NHL/]-@LT
M/406VX_JI_G33X+\7Z@Q:_\`$6IR!OX$D\M?RW8_2@#TZ>ZM[9=UQ/'$OK(X
M4?K6/<^./"UH"9=>LCCJ(Y1(?R7-<&/A:$+/-I]Y>NW)9[I,G_QX5H6O@:"W
M0+_PC#\?WEMY3^;2U2BV2Y)?\,:5S\7/"D/$$MU=MG`6&W()_P"^L56D^)M_
M/C^S/!VJ7`;H\P,:C\0I'ZU?MM%EMD")I6HHH&,1?9T'_HVK*::BG+:'JLA_
MVIK?^DE/D?\`30N=>?W,P9/%?CV[?;;Z/I5@AZM<7*N1^`?/Z579_'%VQ-WX
MNL;)#T2TMRY'X[!_.NM2V@3IX8OC_O2PG_VK5A)!']SPO<@^H^S9_P#1E'(_
MZ:#G7])G!?\`"-/=$_VGXOUR^+'[L/R+^18^_:N[\(Z7::/H26=D+D1+(S?Z
M207R3D]`*LKJ-THPN@7P'L]O_P#':MVL\EQ$7EM)K5@V-DI0D^_RLPQ^/:DX
MM#4D_P#AB>BBBI*"BBB@`HHHH`****`"BBB@`HHHH`****`.3^(:PG2]-DF5
MCY>J6[*2,Q`[L'S?]C!/XX]:=J<"3>&]"G6WN+0Q75B5MS,_[L&6,%7&?FP.
M/FSCVJ]XHOK;3[:U>ZN[J$37,<,45M%'(TLC,-O#JW0C/&.G7
M`/T,61]*?*N_Y_Y"YGV?X?YFM16=_9EY_P!!V_\`^^+?_P"-4?V9>?\`0=O_
M`/OBW_\`C5'*N_Y_Y!S/L_P_S+LMQ#`5$TT<>[[N]@,_2H6U/3T)#7ULI'4&
M51_6L?5_!L&NK$-1U74)O)SY?^I7;G&>D8]!7,7OPDD;FPU]H_\`9FM@WZ@C
M^56HTK>])_)$.56_NQ7S?_`9VY\1Z&HR=9L/PN4/]:C;Q5H"==7M.?24'^5>
M:GX=>,--+M`-*U)>PGJHOO!TNT'#-:11R_\`LC?SJDJ'
M=DWQ%ME^)Z@WC+PZI(.K0<>F3_2JY\?^&`,C4B?802?_`!-><0^*/#T,WE:A
M8WEI(O4265MQ^'DDUO:?KW@^;_4ZJT!?C_CUM$S^<0-5RX?N_P"OD1?$=E_7
MS.E;XA^&UQB[D;Z0M_45$WQ)\/!L![EAZB+_`.O1;'29D'DZ[.%[8MK?'Z18
MK0BMXG(,7B2XSVPML#_Z*H_<=OQ_X`_W_P#2_P#MC*3XF:3+GR;#49".PB4_
MR:G_`/"P8F4&+0M4<>OE#_&MP:;=,,C7K\CU"6__`,:I?[,O/^@[?_\`?%O_
M`/&J+T>WXO\`R$E7ZO\`!?YF$?'%V6Q'X6U1@>G[LY/Z4Q?&&OS96+P;>`]C
M([*/U05T']F7G_0=O_\`OBW_`/C5']F7G_0=O_\`OBW_`/C5'-2_E7WL.6M_
M,_NB<_N\>ZH/E2RTF,GO\S@?^/?TH_X0.>_.=;\07MX"<^6AVJ/P.1^@KH/[
M,O/^@[?_`/?%O_\`&J/[,O/^@[?_`/?%O_\`&J/;-?"TO1?\`/8I_$F_5_I>
MQ3LO!?AZQP4TV.1A_%-F3]#Q6U'%'"@2)%11T51@51_LR\_Z#M__`-\6_P#\
M:IKV%Q&,OXAO5'^TMN/_`&E64FY?%*_WFT4H:1C;[O\`,TZ*PY&CC^]XINOP
M%N?Y156DOX4^[XBU)_\`=A@_K%4\J[_G_D5S/M^7^9TM%R'G;:V^/\`V8']*EHL]4Z0_@X-1MK>FKUNU_`$_P`A7GL'@SX@2$>=K6FP)_LQAS_Z
M+_K5G_A6>NW1'VSQA*J@\K;V^S/XAA_*@9VC>(=-'29F^B'_``JK/XQT>WSY
MDY7'J5'\S7-CX0Z?,NV]UW5IP1@CS5`/Y@TY?@SX8'6?46^LR?\`Q-"28GH:
M4WQ+\.19_P!,1OI(I_D36=-\7_#\9(0/(0>P8?\`LM7+?X7>'[8`1F5L#'[R
M*"3_`-"C-:=MX0M+(8M;EX/^N5I:K_*&JY5W_/\`R)YGV?X?YG++\8(+EREA
MHE[/+C!N?&WEG_IC&0/TVTG_"
MN_$LDFZ;X@:D5/W@F]?_`&IBNQ_LR\_Z#M__`-\6_P#\:H_LR\_Z#M__`-\6
M_P#\:HY5W_/_`"#F?;\O\SD/^%87[C$WC35I!V^9OZL::?A':R,3<>(M5E##
M#?O!S^>:['^S+S_H.W__`'Q;_P#QJC^S+S_H.W__`'Q;_P#QJCE7?\_\@YGV
M?X?YG&Q_!?P\@(>[OY/?\`0=O_`/OB
MW_\`C5']F7G_`$';_P#[XM__`(U1RKO^?^0PK/\`[,O/^@[?_P#?%O\`_&J/
M[,O/^@[?_P#?%O\`_&J.5=_S_P`@YG_*_P`/\S1HK._LR\_Z#M__`-\6_P#\
M:H_LR\_Z#M__`-\6_P#\:HY5W_/_`"#F?9_A_F:-%9W]F7G_`$';_P#[XM__
M`(U1_9EY_P!!V_\`^^+?_P"-4?]!V__`.^+?_XU1RKO^?\`D',^S_#_`#-&BL[^S+S_`*#M_P#]\6__
M`,:JU:P26\126[FNF+9WRA`1[?*JC'X=Z3274:;?0GHHHJ2@HHHH`****`"B
MBB@`HHHH`****`"BBB@#E?'\@73+!0]N&&H028DF6.0*KC+1DG&X9&2>`":;
M?:G:W>A:=!/K6F3WL5Q:2W#)=1JI*2HTA&3[$U=\8:CJ.F:=:3:>Z1*]]!%<
MSLF_RHF<`G;WY('X_B-BREDFL8)96A:1XU9F@8M&21U4GJ/2J3CU1+4NC_K[
MSSZ18#,KC4K$BQN))H_]-B_TD->)<8'S<$*F/FQR?3FNFT#5M)L=)2&XUBP6
M5I99F4W<9V[Y&?;D''&['X5#>:QK=I)>!9;6XCBFCA62'3Y7*,QRV460E\(1
MTQR?:M[3;G[7IT,YN([@NO,D<1C4G.#\K$E<=""<@BG>';\?^`*T^Z^[_@D'
M_"1:'_T&;#_P*3_&C_A(M#_Z#-A_X%)_C6C11>';\?\`@!:?=?=_P3._X2+0
M_P#H,V'_`(%)_C1_PD6A_P#09L/_``*3_&M&BB\.WX_\`+3[K[O^"9W_``D6
MA_\`09L/_`I/\:/^$BT/_H,V'_@4G^-:-%%X=OQ_X`6GW7W?\$RIM:\.W*;)
M]3TR5?[KSQL/U-8=[HGPYOU(F315W=3#.D1_-"*[&BB\.WX_\`+3[_A_P3S*
MY\!>`VD\RQ\1?8'[>5?QD?KD_K5"7PM<6@;^S/B+8R]U2ZE7\!G1[>\
M,PF4_P`A^M>R447CV_K[@M+O^'_!/,[+XJ64H7?J0C)X"W%N01]2H(_6MN#Q
MY;2+G[;I;_2[13^1;-=->:3INHJ5OM/MKD'J)H5?^8K!O/AKX1O'WOI"1-_T
MQD>,?D#C]*DLJS^.[=`2=3TF)?:Y5S^08_RK(N/B7IJE@VOA\'I!;.?U*C^=
M=+:?#OPE9C$>B0/WS,6E_P#0B:V;71]+L5"VFFVEN!T$4"K_`"%(#RN7XE6<
MH)CCUBZST#!4'Z,U0IXJU&\3=9Z%:HS#(-YJ<8_,$H:]FHJDX]42U+I_7XGD
M2R>)[I/DU3PIIY/-I[[')#ZA'@_GD_K5^V\'_#2V(8S6,S#O+J&?TW
M8_2N_HHO#M^/_`"T^_X?\$YBUMO`5FP:W708V'1@82P_'K6HFO:!$NV/5M.1
M?1;B,#^=:=%%X=OQ_P"`%I]U]W_!,[_A(M#_`.@S8?\`@4G^-'_"1:'_`-!F
MP_\``I/\:T:*+P[?C_P`M/NON_X)G?\`"1:'_P!!FP_\"D_QH_X2+0_^@S8?
M^!2?XUHT47AV_'_@!:?=?=_P3._X2+0_^@S8?^!2?XT?\)%H?_09L/\`P*3_
M`!K1HHO#M^/_```M/NON_P""9W_"1:'_`-!FP_\``I/\:/\`A(M#_P"@S8?^
M!2?XUHT47AV_'_@!:?=?=_P3._X2+0_^@S8?^!2?XT?\)%H?_09L/_`I/\:T
M:*+P[?C_`,`+3[K[O^"9W_"1:'_T&;#_`,"D_P`:/^$BT/\`Z#-A_P"!2?XU
MHT47AV_'_@!:?=?=_P`$SO\`A(M#_P"@S8?^!2?XT?\`"1:'_P!!FP_\"D_Q
MK1HHO#M^/_`"T^Z^[_@F=_PD6A_]!FP_\"D_QH_X2+0_^@S8?^!2?XUHT47A
MV_'_`(`6GW7W?\$SO^$BT/\`Z#-A_P"!2?XT?\)%H?\`T&;#_P`"D_QK1HHO
M#M^/_`"T^Z^[_@F=_P`)%H?_`$&;#_P*3_&C_A(M#_Z#-A_X%)_C6C11>';\
M?^`%I]U]W_!,[_A(M#_Z#-A_X%)_C1_PD6A_]!FP_P#`I/\`&M&BB\.WX_\`
M`"T^Z^[_`()G?\)%H?\`T&;#_P`"D_QH_P"$BT/_`*#-A_X%)_C6C11>';\?
M^`%I]U]W_!,[_A(M#_Z#-A_X%)_C1_PD6A_]!FP_\"D_QK1HHO#M^/\`P`M/
MNON_X)G?\)%H?_09L/\`P*3_`!H_X2+0_P#H,V'_`(%)_C6C11>';\?^`%I]
MU]W_``3._P"$BT/_`*#-A_X%)_C1_P`)%H?_`$&;#_P*3_&M&BB\.WX_\`+3
M[K[O^"9W_"1:'_T&;#_P*3_&C_A(M#_Z#-A_X%)_C6C11>';\?\`@!:?=?=_
MP3._X2+0_P#H,V'_`(%)_C1_PD6A_P#09L/_``*3_&M&BB\.WX_\`+3[K[O^
M"9W_``D6A_\`09L/_`I/\:M6M[:WT1EL[F&XC#;2\4@<`^F1WY%3T4GR]$-*
M75A1114E!1110`4444`%%%%`!1110`4444`%%%%`'/\`B^T@N[*T\]+@>1=Q
M3QSPR1)Y;JPP/WCJ"6R0.O/;I5FSN);"SAL[;P]?QPP1K'&HD@X4#`'^MK*^
M(:PG2]-DF5CY>J6[*2,Q`[L'S?\`8P3^./6M_1B#HMB5M9+4&W3$$C%FB^4?
M*2>21TYJDTNA+BWU_(RV2Y^S210Z=K-N[SM/YT4UMN#,2<8+E2.<8(/0=^:L
M6,TNGVB6UOH&HA%+'+26Y+,Q+,3^]ZDDD_6N3`AMX;B*%;"ZBEFCDO[N"U\J
M2-#VS;3YEV_/_,7
M*_YG^'^1-_:=Y_T`K_\`[[M__CM']IWG_0"O_P#ONW_^.UHT4?]`*__P"^[?\`^.T?VG>?]`*__P"^[?\`^.UHT4?]`*_P#^^[?_`..T?VG>?]`*_P#^^[?_`..UHT4?\`0"O_`/ONW_\`CM:-%',NWY_Y
MARON_P`/\C._M.\_Z`5__P!]V_\`\=H_M.\_Z`5__P!]V_\`\=K1HHYEV_/_
M`##E?=_A_D9W]IWG_0"O_P#ONW_^.T?VG>?]`*__`.^[?_X[6C11S+M^?^8<
MK[O\/\C._M.\_P"@%?\`_?=O_P#':/[3O/\`H!7_`/WW;_\`QVM&BCF7;\_\
MPY7W?X?Y&=_:=Y_T`K__`+[M_P#X[1_:=Y_T`K__`+[M_P#X[6C11S+M^?\`
MF'*^[_#_`",[^T[S_H!7_P#WW;__`!VC^T[S_H!7_P#WW;__`!VM&BCF7;\_
M\PY7W?X?Y&=_:=Y_T`K_`/[[M_\`X[1_:=Y_T`K_`/[[M_\`X[6C11S+M^?^
M8?]`*__`.^[?_X[1_:=Y_T`K_\`[[M__CM:-%',NWY_
MYARON_P_R,[^T[S_`*`5_P#]]V__`,=H_M.\_P"@%?\`_?=O_P#':T:*.9=O
MS_S#E?=_A_D9W]IWG_0"O_\`ONW_`/CM']IWG_0"O_\`ONW_`/CM:-%',NWY
M_P"8?\`0"O_`/ONW_\`CM']IWG_`$`K_P#[[M__`([6C11S
M+M^?^8?]`*__P"^[?\`^.T?VG>?]`*__P"^[?\`^.UHT4?]`*_P#^^[?_`..T?VG>?]`*_P#^^[?_`..UHT4<
MR[?G_F'*^[_#_(SO[3O/^@%?_P#?=O\`_':M6L\EQ$7EM)K5@V-DI0D^_P`K
M,,?CVJ>BDVGT&DUU"BBBI*"BBB@`HHHH`****`"BBB@`HHHH`****`,/Q1?6
MVGVUJ]U=W4(FN8X8HK:*.1I9&8;>'5NA&>,=.YQ4UM:37=M%W##4(),23+'(%5QEHR3C<,C)/`!-:.GZ_IR:=;)
M?Z[ILEVL2B=TN4"L^/F(YZ9S6D>>VB_`SER7U?XE-]1MHTD8^)-48(P4!+2-
MC(20OR`0Y<9.,KD5H6]GG_-^/_!+W]F7G_0=O_P#OBW_^-4?V9>?]!V__`.^+
M?_XU1_PD6A_]!FP_\"D_QH_X2+0_^@S8?^!2?XT6J=OP"]/^;\?^"']F7G_0
M=O\`_OBW_P#C5']F7G_0=O\`_OBW_P#C5'_"1:'_`-!FP_\``I/\:/\`A(M#
M_P"@S8?^!2?XT6J=OP"]/^;\?^"']F7G_0=O_P#OBW_^-4?V9>?]!V__`.^+
M?_XU1_PD6A_]!FP_\"D_QH_X2+0_^@S8?^!2?XT6J=OP"]/^;\?^"']F7G_0
M=O\`_OBW_P#C5']F7G_0=O\`_OBW_P#C5'_"1:'_`-!FP_\``I/\:/\`A(M#
M_P"@S8?^!2?XT6J=OP"]/^;\?^"']F7G_0=O_P#OBW_^-4?V9>?]!V__`.^+
M?_XU1_PD6A_]!FP_\"D_QH_X2+0_^@S8?^!2?XT6J=OP"]/^;\?^"']F7G_0
M=O\`_OBW_P#C5']F7G_0=O\`_OBW_P#C5'_"1:'_`-!FP_\``I/\:/\`A(M#
M_P"@S8?^!2?XT6J=OP"]/^;\?^"']F7G_0=O_P#OBW_^-4?V9>?]!V__`.^+
M?_XU1_PD6A_]!FP_\"D_QH_X2+0_^@S8?^!2?XT6J=OP"]/^;\?^"']F7G_0
M=O\`_OBW_P#C5']F7G_0=O\`_OBW_P#C5'_"1:'_`-!FP_\``I/\:/\`A(M#
M_P"@S8?^!2?XT6J=OP"]/^;\?^"']F7G_0=O_P#OBW_^-4?V9>?]!V__`.^+
M?_XU1_PD6A_]!FP_\"D_QH_X2+0_^@S8?^!2?XT6J=OP"]/^;\?^"']F7G_0
M=O\`_OBW_P#C5']F7G_0=O\`_OBW_P#C5'_"1:'_`-!FP_\``I/\:/\`A(M#
M_P"@S8?^!2?XT6J=OP"]/^;\?^"']F7G_0=O_P#OBW_^-4?V9>?]!V__`.^+
M?_XU1_PD6A_]!FP_\"D_QH_X2+0_^@S8?^!2?XT6J=OP"]/^;\?^"']F7G_0
M=O\`_OBW_P#C5']F7G_0=O\`_OBW_P#C5'_"1:'_`-!FP_\``I/\:/\`A(M#
M_P"@S8?^!2?XT6J=OP"]/^;\?^"']F7G_0=O_P#OBW_^-4?V9>?]!V__`.^+
M?_XU1_PD6A_]!FP_\"D_QH_X2+0_^@S8?^!2?XT6J=OP"]/^;\?^"']F7G_0
M=O\`_OBW_P#C5']F7G_0=O\`_OBW_P#C5'_"1:'_`-!FP_\``I/\:/\`A(M#
M_P"@S8?^!2?XT6J=OP"]/^;\?^"']F7G_0=O_P#OBW_^-4?V9>?]!V__`.^+
M?_XU1_PD6A_]!FP_\"D_QH_X2+0_^@S8?^!2?XT6J=OP"]/^;\?^"']F7G_0
M=O\`_OBW_P#C5']F7G_0=O\`_OBW_P#C5'_"1:'_`-!FP_\``I/\:/\`A(M#
M_P"@S8?^!2?XT6J=OP"]/^;\?^"']F7G_0=O_P#OBW_^-4?V9>?]!V__`.^+
M?_XU1_PD6A_]!FP_\"D_QH_X2+0_^@S8?^!2?XT6J=OP"]/^;\?^"']F7G_0
M=O\`_OBW_P#C5']F7G_0=O\`_OBW_P#C5'_"1:'_`-!FP_\``I/\:/\`A(M#
M_P"@S8?^!2?XT6J=OP"]/^;\?^"']F7G_0=O_P#OBW_^-4?V9>?]!V__`.^+
M?_XU1_PD6A_]!FP_\"D_QH_X2+0_^@S8?^!2?XT6J=OP"]/^;\?^"']F7G_0
M=O\`_OBW_P#C5']F7G_0=O\`_OBW_P#C5'_"1:'_`-!FP_\``I/\:/\`A(M#
M_P"@S8?^!2?XT6J=OP"]/^;\?^"']F7G_0=O_P#OBW_^-4?V9>?]!V__`.^+
M?_XU1_PD6A_]!FP_\"D_QH_X2+0_^@S8?^!2?XT6J=OP"]/^;\?^"']F7G_0
M=O\`_OBW_P#C5']F7G_0=O\`_OBW_P#C5'_"1:'_`-!FP_\``I/\:/\`A(M#
M_P"@S8?^!2?XT6J=OP"]/^;\?^"']F7G_0=O_P#OBW_^-4?V9>?]!V__`.^+
M?_XU1_PD6A_]!FP_\"D_QH_X2+0_^@S8?^!2?XT6J=OP"]/^;\?^"']F7G_0
M=O\`_OBW_P#C5']F7G_0=O\`_OBW_P#C5'_"1:'_`-!FP_\``I/\:/\`A(M#
M_P"@S8?^!2?XT6J=OP"]/^;\?^"']F7G_0=O_P#OBW_^-4?V9>?]!V__`.^+
M?_XU1_PD6A_]!FP_\"D_QH_X2+0_^@S8?^!2?XT6J=OP"]/^;\?^"']F7G_0
M=O\`_OBW_P#C5']F7G_0=O\`_OBW_P#C5'_"1:'_`-!FP_\``I/\:/\`A(M#
M_P"@S8?^!2?XT6J=OP"]/^;\?^"']F7G_0=O_P#OBW_^-4?V9>?]!V__`.^+
M?_XU1_PD6A_]!FP_\"D_QH_X2+0_^@S8?^!2?XT6J=OP"]/^;\?^"']F7G_0
M=O\`_OBW_P#C5']F7G_0=O\`_OBW_P#C5'_"1:'_`-!FP_\``I/\:/\`A(M#
M_P"@S8?^!2?XT6J=OP"]/^;\?^"']F7G_0=O_P#OBW_^-4?V9>?]!V__`.^+
M?_XU1_PD6A_]!FP_\"D_QH_X2+0_^@S8?^!2?XT6J=OP"]/^;\?^"']F7G_0
M=O\`_OBW_P#C56K6"2WB*2W2^C_$GHHHK,T"BBB@`HHH
MH`****`"BBB@`HHHH`****`"BBB@`HHHH`****`*U]J%MIT(FNI"BLVU0J,[
M,<$X`4$G@$_0$]J@_MW3//:'[6FY8O-+8.S;MW?>QC.T@XSG!STJ/7S>BUA6
MRL9+IGDVR-$T8DB0J-V><8/,WWA2^NX;JQM;4VEM+OFA+.N$W6
M8MUB(!/(/<9&`.30!U$/B'29Y;:%+U!-=.R10NI61B`2?D(!&`.I`[>HK2KF
M(M)U"6\MKV2V:(OK!O)(G=28H_LS1#D$@\@'C/WJZ>@`HHHH`****`"BBB@"
M"\O8+"#SKAF5<[0%1G9CZ!5!)/T%5EUW2WGBA2\1C-%YJ,`=C+MW?>QMSM!.
M,YQSTINNM>K9)]@LWN93*`3$8]\2D'+KO(&[L.>^><8/,W?A6\NHVL;2U>SM
M)?WL;/(O[@?8VMQ'@,?F!(.1D=>:`.D'B72#$DOVLA7==TP23QFY^:W#%_D;!VG:VTX^8@D`AZ>;2IX)8)`;0J\(B
M\M9TD(!#[MTFP$E@`.G8DUX?#NK":3=;!5U"XBGD8R+_`*-LO);@AN>25D`&
MW(SGMS0!U>GZK8ZHKM93B4)@GY2N0>C#(&5/9AP>QJY6#X?LK^"_O;F[M?LJ
MSQQ`QF;S7%ZMJ-)GNM/EB'VAK3^[;>ZD+CDX!SN
MQQSD`N'Q#I>)3]H8^40,+"Y+\X^0`9DYX^7-3C5[!GLT%RA:^+"W7G,FU2Q^
MF`#G/TZURL6@:I#<:+99F_L",Q;!*F;S(V[ERV.`,_-MYS]:=9>%M7M]:T
MO4)+B&2.*ZEE>)HR7MT=9B5#;\-\TF.%_N]0M`':4444`%%%%`!1110`4444
M`17%Q%:0//.^R-!DG!/Z#K5+_A(-+V0O]I)$Y(4B-_EPVT[^/DPWR_-CGCK4
MVKM=)IDS65H+NX&TQQ';R=PY^8@<=<9'3J*YF;0KQ[6YCMK&ZB&IV9MI3-+%
MO@^3+)Y?G?
MO596'!\P<%E/4]@#UVF17<&E6D5_,)KM(46:0='<`9/YT`6J***`"BBB@`HH
MHH`*RQXCTDVSW"W19%8+\L3EFSD@JH&6!`)!`((!/0&M-ONGC/'3UKD(;+4Y
M'M-5?0YHKZVG5Y;E36.H6VI0&:UD+H&*G
GRAPHIC
15
g46861bci002.jpg
GRAPHIC
begin 644 g46861bci002.jpg
M_]C_X``02D9)1@`!`0$`8`!@``#_VP!#``H'!P@'!@H("`@+"@H+#A@0#@T-
M#AT5%A$8(Q\E)"(?(B$F*S7J#A(6&AXB)BI*3E)66EYB9FJ*CI*6FIZBIJK*SM+6VM[BYNL+#Q,7&
MQ\C)RM+3U-76U]C9VN'BX^3EYN?HZ>KQ\O/T]?;W^/GZ_\0`'P$``P$!`0$!
M`0$!`0````````$"`P0%!@<("0H+_\0`M1$``@$"!`0#!`<%!`0``0)W``$"
M`Q$$!2$Q!A)!40=A<1,B,H$(%$*1H;'!"2,S4O`58G+1"A8D-.$E\1<8&1HF
M)R@I*C4V-S@Y.D-$149'2$E*4U155E=865IC9&5F9VAI:G-T=79W>'EZ@H.$
MA8:'B(F*DI.4E9:7F)F:HJ.DI::GJ*FJLK.TM;:WN+FZPL/$Q<;'R,G*TM/4
MU=;7V-G:XN/DY>;GZ.GJ\O/T]?;W^/GZ_]H`#`,!``(1`Q$`/P#V6BBB@`HH
MHH`****`"BBB@`HHHH`****`#IR:*Y?XAD#PA=[KAH1YV$`CM;6207T/FQ8,3;=ZY&`2IP20,C')P*Z_39&FTNTE:V^RL\*,8,8\
MHE1\OX=/PH`S[^Y@36HK%_$-Q:7-RF^*V18<8!"]6C)Y)XR>3G'2JHOK8S11
M#Q/J!:61HE(MXBH82&/#-Y.%RX*C)&X],U6UK3=0G\=Z==VEDC0&T,<\[`,K
M*)HV9'!Z87+)MY+?[(-)9Z=?6LUOI\FC2?8$NY9]]N8=O_'U(\0;+@A5!5\*
M"?\`0=O_`/OBW_\`C5']F7G_`$';_P#[XM__`(U6C11SO^D@
MY%Y_>S._LR\_Z#M__P!\6_\`\:H_LR\_Z#M__P!\6_\`\:K1HHYW_20*W*LIX((,7(I_\`9EY_T';_`/[XM_\`XU4NL?\`
M(%OO^O>3_P!!->68KHHTW43=[?)&51J#Z_>ST[^S+S_H.W__`'Q;_P#QJC^S
M+S_H.W__`'Q;_P#QJO,<5Z_2K0=*VM[^2"FU.^_WL**I7%]$*W';?\`0"O_`/ON
MW_\`CM']IWG_`$`K_P#[[M__`([1R/\`IH.=>?W,T:*SO[3O/^@%?_\`?=O_
M`/':/[3O/^@%?_\`?=O_`/':.1_TT'.O/[F97BW6;_2;[1_L]Q!;VLTLHN))
M4+_=C9E!`Y"9!+,/NX!)QFF/J6JSWD]@UT+1Y-6^RQR0A7,,8M!,,;EP22.<
M@_>('04[7;>VU06]WJ?A[42M@7D!66`94H5=6Q+DJ1U7O@`Y&0'[M)
MUETG4O\`2)A-(R.J-O"!-P99`5^50O!&1GU.:5&(?#K7<=R=(U+?$5*#S!L&
MT`+\GF[<#:"!C`.2,$DUU/\`:=Y_T`K_`/[[M_\`X[1*E..Z!58O;\F2ZO\`
M\@:]_P"O>3_T$UY?BO0=3U&[;2KM3HE\@,#@L7@P/E//$E>=^;)_SZR_FG_Q
M5=F%BU%G/7DFU_DQ^*]:>4?
M9XO+,(/RN1(DB'VPR9XZ\9.!@H/"]DMPDRS7``F,TB97;,WG-,H;Y1QQV/0GL":YBWUL?V[97
MS&WAM[218Q'->;IGB_>AY(B5R]O^\5MQ(^6#...`#TJBN6TIK/\`X36Z6TV;
MO)F^T,C$R,_F)CS@0"N.1'URNX@XZ]30!3U?_D#7W_7O)_Z":\MVUZGJW_('
MO?\`KWD_]!->88KT,)\+.6ONB/;7KU>2XKUJIQGV?F.AU*FJ_P#((O?^O=__
M`$$UYKBO2]4_Y!-Y_P!<'_\`037F^*>%^%A6W0S%>JUY;BO4JG%]!T.H45C7
MZ^&FUJ*SO[>P?4+I-ZB:%6=P"%Y)'T`SUQQTI+O3O#-E)!'<:58(UPX2/_0U
M(R2`,D+@9)`R<XKC?^$YU3_GA:?]\-_\570ZIH&C1Z3>.FD6*LL#E66V0$':>1Q7G/V.
MV_Y]XO\`O@5V8>G3DG?4YZTZB:M_7X'2_P#"^QVW_
M`#[Q?]\"O4/^$=T/_H#6'_@*G^%3B84XVMH.C.H[W_K\";5?^01>_P#7O)_Z
M":\TQ7>:EH&BII=VZ:18JRPN0PMD!!VGVK@/L-I_SZP_]^Q5X7EL[,5;FNM/
MZ^X?BO5J\F^PVG_/K#_W[%>D?\([H?\`T!K#_P`!4_PI8KETNPH\VNGX_P#`
M)]4_Y!5Y_P!<'_\`037G6VNVU#0-%33;ITTBQ5EA<@BV0$'!]JX7^S[/_GT@
M_P"_8_PHPW+9V8ZO-=:?U]Q)MKT^O+/[/L_^?2#_`+]C_"O0O^$=T/\`Z`UA
M_P"`J?X4L3RZ784>;73\?^`8NL:?J4GCW3;VRLU,0M#'-<$`J5$T;%'STP,L
MFWDM[`T>*M(U34=3@GM%N#Y4(%LT)B"1R^:LA,V_DIF.(_)D_*WJ,]717"=0
M4444`5-6_P"0/>_]>\G_`*":\SVUZ9JO_((O/^N#_P#H)KS?;7?A?A9S5MT1
M[:]7KRS;7J=3B^@Z'4JZG_R"KS_K@_\`Z":\ZVUZ-J7_`""[O_K@_P#Z":\^
MVT8;9A6W1%MKT^O-=M>E4L5T'1ZE;4O^07=_]<7_`/037`8KO]1_Y!EU_P!<
M7_\`037![:,-LPJ[H9BO2*\ZVUZ+2Q/0=+J4KB+56G8VU[9QQ<;5DM&=AQW(
MD&>?:H_(US_H(V'_`(`O_P#':PM:U.>T^(&FP'49([5[09@B`(5VG1`T@/56
MR$!&2#D\#)J77KR\AUYY0)OL>G6L=T_E7)B)R[[P$P1*=J`;3_>X()!KFYW_
M`$D:_FUP?E7G_/>#_OR?\`XJO3=2_Y!=W_`-<'
M_P#037GVVNS#2=F858*Z_P`V4_*O/^>\'_?D_P#Q5>B^1KG_`$$;#_P!?_X[
M7#;:]*I8F;T"E!:_YLQK^'6O[.N=^H6)7R7R!9."1@]_-KB?*O?^?B#_`+\'
M_P"+KT;4?^0;=?\`7%_Y&N%VT8>3LQU8*_\`P64_*O?^?B#_`+\'_P"+KOO(
MUS_H(V'_`(`O_P#':XW;7H=+$2>@4H+7_-F/?0ZU_9]QNU"P*^4V0+)P2,'_
M`*:UQOE7_P#S\6__`'X;_P"+KT*__P"0=<_]5?
M_P#/Q;_]^&_^+KN?(US_`*"-A_X`O_\`':Y/;7>TL1-Z#IP6O^;*LNFV4^H0
M:A+;1O=6Z,D4K#)0-C./R'/U]3EUSI]E>2PRW5G!/)`VZ)Y8@QC/JI(X/`Z5
M%<7US#.T<>DWEPHQB2-X0K<=MS@_I4?]IWG_`$`K_P#[[M__`([7+R/^FC7G
M7])FC16=_:=Y_P!`*_\`^^[?_P".T?VG>?\`0"O_`/ONW_\`CM/D?]-!SKS^
MYEC4?^09=?\`7%__`$$UP>VNMOM2NVL+A3H=^H,3#)>#`X/_`$TKCOM$W_0/
MN/\`OJ/_`.*KKP\6DS&I-7_X#)-M>BUYM]HF_P"@?]]1__`!5=Q_:=Y_T`
MK_\`[[M__CM+$1;M_F%*:U_R99O_`/D'7/\`UQ?^1KB=M=->ZE=M8W`.AWZ@
MQ,,EX,#C_KI7)_:9_P#H'7/_`'U'_P#%T4(M)A4FK_\``9-MKOJ\[^TS_P#0
M.N?^^H__`(NNS_M.\_Z`5_\`]]V__P`=I5XMV_S'3FM?\F6K[_D'W/\`UR;^
M1KC-M='>:E=M93@Z'?J#&W)>#`X_ZZ5ROVJ?_H&W/_?47_Q=%"+2?^85)J__
M``&3[:[JO/OM4_\`T#;G_OJ+_P"+KL/[3O/^@%?_`/?=O_\`':5>+=O\PIS6
MO^3*-_KUY:>,+'1TMH?LUS;-+YLLFTR,'52J=B54EB.X],UF32S916\:
M22W-U#&X;.$B:5$9OK\Z@>YSS@TW4/#5OJ/B"UU>:>4?9XO+,(/RN1(DB'VP
MR9XZ\9.!@V-4T+3=8,+WEK$\L$B21RF-2Z[7#X!(.`2N".X)KD.@T:***`*]
M_P#\@^Y_ZY-_(UQFVNTO?^/"X_ZY-_(UR&VNJALS*IN1;:[NN)VUVU*OT"GU
M(+W_`(\+C_KDW\C7(;:["\_X\I_^N;?RKE-M%'9A/HFA5G<`A>21]`,]<<=*CNK/PM9WD-I/I=BDLQ`7%D"HR
M=J[F"X7)X&2,G@9-8VCW_K[QWEV_'_@&[16=_P`([H?_`$!K#_P%3_"C_A'=
M#_Z`UA_X"I_A3M#O^'_!"\^R^_\`X!;O/^/*?_KFW\JY7;6U<^'M$6UE*Z/8
M`A&P1;)QQ]*Y_P#L;3/^@=:_]^5_PK>ERV>O]?>9SY^WX_\``)MM=A7$_P!C
M:9_T#K7_`+\K_A72_P#".Z'_`-`:P_\``5/\**W+IK_7WA#G[?C_`,`MW?\`
MQYS_`/7-OY5S&VM>Y\/:(+:4KH]@"$."+9../I6#_8VF?]`VT_[\+_A12Y;;
M_P!?>$^?M^/_``"?;76UQ?\`8VF?]`VT_P"_"_X5T?\`PCNA_P#0&L/_``%3
M_"E5Y=-?Z^\<.?M^/_`+EU_QZ3?]P!"'!%LGI]*P
MO[&TO_H&VG_?A?\`"G2Y;;_U]X2<^WX_\`L8KJJXW^QM+_Z!MI_WX7_"NA_X
M1W0_^@-8?^`J?X4JO+IK_7WA!S[?C_P#%UC3]2D\>Z;>V5FIB%H8YK@@%2HF
MC8H^>F!EDV\EO8&M'5$NI]9M83IDTUB#'))-$8N9%?*A]SAMJ$!_E!))'H0=
MJBN8V"BBB@"*Y_X]9?\`<;^5<_MKH;C_`(]I?]P_RK#VUM3>A$B+;72US^VN
M@HJ]`B17/_'K+_N'^58&VN@N/^/>7_\JQ-M%/8)$6VNDK`VUOTJG0(D=Q_
MQ[2_[A_E6#MK>G_X]Y/]P_RK%VTZ>P2(]M=%6#MK>I5.@XE*XBU5IV-M>V<<
M7&U9+1G8<=R)!GGVJ/R-<_Z"-A_X`O\`_':T:*CG?])"Y%_39G>1KG_01L/_
M``!?_P".T>1KG_01L/\`P!?_`..UHT4^=_TD'(O/[V9-RNJPVLLMSJVFPPJI
M+R/9LJJ.Y),V!6<-YQCQ)I!S#]H'[CK%_?\`]=]WWZ5LZSY_]ER&ULEO9U9&
MCA;;]X."&^8J#M(W8R/N]17*R>']4?RO)MKA`FH1ZDYE:+=(`@#P':^,LP9O
M[HW4U4DMOR0>SC_39K)9WDJ0/'K>FNES_J66U)$O&?E_>\\`GCL*T?(US_H(
MV'_@"_\`\=K!@\.ZJNM:1J4DJ-%!S7]-F8]OK31L&U+3PI!R?L+\#_O[67%OG,`A\2:1(;DL(=D&?-*
M_>"_ON<=\=*Z&\!-C.!;?:28V_<9`\WC[N3QSTYXYKE(]*U2:Y-PUA/'+?3V
MDDYD>(+"89@['"NW#(%4`9/RC=C.:%4DO^&0>S7]-EL)*WEX\1:2?.D,4>+<
M_.XZJ/WW)'IUK5\C7/\`H(V'_@"__P`=KEM'\/:SIZ6)^RO'<1S1(94N0%2-
M([:.3`22O=4.I)_\,@]FOZ;,Q[?6C&P;4M/"D')^POT_P"_
MM9<6^/NY/'
M/3GCFN4CTK5)KDW#6$\S7]-EQ8YF$97Q!I1$LABCQ;GYW&1KG_01L/_``!?_P".
MUQ]CX7UFTM[=S;,)XHS%&$F7$<@AM425QN`9`UNQQR<%?E!SCT&AU)/_`(9!
M[-?TV%%%%9EA1110`4444`%07EW'96YF<,W(543[SL3@*,]R34]9VIVUQ/=Z
M9)`NY8+II)`6P`/)D4$^HW,O'T/:@!;+6]/OYC;QW$:7(:0"W=U$A".4+A>F[GC/;-84WAK5OMINXI[9Y#*[`2.P";C-\W"_,
M0)8QM.`?+'(/-1KX3URHX3:2+Y17,]S"@8-;2"-\C`)**X(]1AA^(-6*H:5:20"YN)D\N6[G,K1YSL`544?
M]\HN<<9)Z]:OT`%%%%`!1110`4444`%%%%`!1110`4444`%%%%`!1110`444
$4`?_V3\_
`
end
GRAPHIC
16
g46861bci003.jpg
GRAPHIC
begin 644 g46861bci003.jpg
M_]C_X``02D9)1@`!`0$`8`!@``#_VP!#``H'!P@'!@H("`@+"@H+#A@0#@T-
M#AT5%A$8(Q\E)"(?(B$F*S7J#A(6&AXB)BI*3E)66EYB9FJ*CI*6FIZBIJK*SM+6VM[BYNL+#Q,7&
MQ\C)RM+3U-76U]C9VN'BX^3EYN?HZ>KQ\O/T]?;W^/GZ_\0`'P$``P$!`0$!
M`0$!`0````````$"`P0%!@<("0H+_\0`M1$``@$"!`0#!`<%!`0``0)W``$"
M`Q$$!2$Q!A)!40=A<1,B,H$(%$*1H;'!"2,S4O`58G+1"A8D-.$E\1<8&1HF
M)R@I*C4V-S@Y.D-$149'2$E*4U155E=865IC9&5F9VAI:G-T=79W>'EZ@H.$
MA8:'B(F*DI.4E9:7F)F:HJ.DI::GJ*FJLK.TM;:WN+FZPL/$Q<;'R,G*TM/4
MU=;7V-G:XN/DY>;GZ.GJ\O/T]?;W^/GZ_]H`#`,!``(1`Q$`/P#U3^T[S_H!
M7_\`WW;_`/QVC^T[S_H!7_\`WW;_`/QVL+QOJ5QINH:*\>HRVT&^X>>.$`NR
MK"S;\'AD3DLO?(P"<55T[5=2MO#]W=S";[;=Z5)?0*UP9E#JN3\I`\LY=1L!
M(PO0$-F^9=OS_P`R.5_S/\/\CI_[3O/^@%?_`/?=O_\`':/[3O/^@%?_`/?=
MO_\`':Y&&ZNX/$&HVL=]=O;Z9>6$=ION'?>L[H)@Q)_><$XW9VYXQQ7?T?]`*__`.^[?_X[1_:=Y_T`K_\`[[M__CM:-%',NWY_
MYARON_P_R,[^T[S_`*`5_P#]]V__`,=H_M.\_P"@%?\`_?=O_P#':T:*.9=O
MS_S#E?=_A_D9W]IWG_0"O_\`ONW_`/CM']IWG_0"O_\`ONW_`/CM:-%',NWY
M_P"8?:=X
MEUFYTTSWUY*HM99I+YK"*+=;HKN/^6@(>/"\,F6.UAR0:.9=OS_S#E?=_A_D
M=A_:=Y_T`K__`+[M_P#X[1_:=Y_T`K__`+[M_P#X[6=XI\0C2)].M(KN"WFN
M+J$R>:R@F'S45P,]R&_`!CQBK7ARYOKB"\CO[A9Y;>Y\K>(]A^XA8;<`@;F;
M;D9*[3DYR3F7;\_\PY7W?X?Y$_\`:=Y_T`K_`/[[M_\`X[16C11S+M^?^8VLDZ;#<-<1:?:QS._
MF-(L*AF?!&XG&`&<[_,G:9W;
M:OS%VY/&!SV`%>?;:[KP.,:--_U\-_Z"M:UZ,(0O%&=*I*4K-G1T445P'48-
M_:^$],EMHKVPTR![IRD(>V3YB!D]N``.IXY'K1:V?A>\BGEBTBT$4!.^273_
M`"UXSD@LH##@\C(JCXUT_4KN^T6?3+(3S0RS+YN`?+W1,`'#<>6QX8]<`!>2
M*;!I&IR:5JFF_9+BU@OK4VZ)-="<12E)=\@);/EG,8`GG:O)J^>?,!\H-FCGGW#V<.R,[
M_A'=#_Z`UA_X"I_A1_PCNA_]`:P_\!4_PK1HHYY]P]G#LC._X1W0_P#H#6'_
M`("I_A1_PCNA_P#0&L/_``%3_"M&BCGGW#V<.R,[_A'=#_Z`UA_X"I_A1_PC
MNA_]`:P_\!4_PK1HHYY]P]G#LC._X1W0_P#H#6'_`("I_A1_PCNA_P#0&L/_
M``%3_"M&BCGGW#V<.R,[_A'=#_Z`UA_X"I_A7G6IV%I'JMXB6D*JL[A56,``
M;CQ7JU>9ZJ/^)O>_]?$G_H1KKPLY-N[,*T(V6AF?8[;_`)]HO^^!78>$-%TJ
MYTJ5[C3+.9A.0&D@5CC:O'(KF,5VO@OC2)?^O@_^@K6V(DU3T9G2A'FV-#_A
M'=#_`.@-8?\`@*G^%%:-%>=SS[G7[.'9!16=Y&N?]!&P_P#`%_\`X[1Y&N?]
M!&P_\`7_`/CM'*N_Y_Y!S/L_P_S-&BL[R-<_Z"-A_P"`+_\`QVCR-<_Z"-A_
MX`O_`/':.5=_S_R#F?9_A_F:-%9WD:Y_T$;#_P``7_\`CM'D:Y_T$;#_`,`7
M_P#CM'*N_P"?^09YQ*_(<,-F"H8E>H(%=)<6.KW5O+;SWNG212
MH4D1K!\,I&"#^^]*R+#P2VG1VRPW-FSVZQCS'MILRE,;#(!,`Y7`VY&%_A`H
MY5W_`#_R#F?\K_#_`#%UR\U*QNKZ>WU2Y%O"L*,AAB<(\LJK^[`3<65:GL]-U6PMEMK:^L$C7)`-G(Q))))),Q)
M))))/)))HY5W_/\`R#F?\K_#_,V*\WU0?\3>\_Z[O_Z$:[?R-<_Z"-A_X`O_
M`/':X+48K[^T[K?<6Y;SGR1`P!.X]M]=6&23>IC6D[+3\O\`,BVUVG@X8TF7
M_KN?_05KA_+O/^>\/_?D_P#Q5=9X5AU8Z9)Y%[9HOG'(>T9CG:O<2"ML0ER;
MF=)OFV_(ZNBL[R-<_P"@C8?^`+__`!VBO/Y5W_/_`".KF?9_A_F87C?4KC3=
M0T5X]1EMH-]P\\<(!=E6%FWX/#(G)9>^1@$XJ$:[J#77BF=/M2/;Z>)+2WF@
M=`C*9P"`P&=VU6R.O3G;QU5[IECJ+V[WMK'.;67S8?,&=CX(SC\?SP>H%2/9
MVLEP+A[:)IEQB0H"PP&`YZ\!W'_`F]34%G#0W5W!X@U&UCOKM[?3+RPCM-]P
M[[UG=!,&)/[S@G&[.W/&.*[^J4.C:7;FW,&FVD1M=Q@V0*OE;OO;<#Y<]\=:
MNT`%%%U62:7RXB4"EBS`$J.>.#GCIS@`Z.BL&Y\
M3K';:5)!;(9=2A\](;F<0MMPF5!((,F9%`7C//(Q4^@ZY+K(=I+(VRF&.>)A
M)OW1ONVYX&UQLY7G&1R:`->O+-77_B=7W_7Q)_Z$:]3KS#5E_P")Q>_]?$G_
M`*$:[,)\3.>OLC/VUW?@<8T6;_KX;_T%:XG;7<>"1C1Y?^OAO_05K?%/]V94
M5[YT5>>ZF/\`B:W?_7=__0C7H50#R\?*
MJ(6;KU/3`[\^F"@\0>5_:K7EG);QZ;$9]Q.XR1@R#.,<$^4Q`YX93WP+O#M^
M/_`(M/NON_X)8_MVS_YXW_\`X+KC_P"(H_MVS_YXW_\`X+KC_P"(K*A\6SG4
M);&XTU(Y;.:"&]V7!81&8J(MGR#?DL,YVXP>O?IJ+P[?C_P`M/NON_X)G?V[
M9_\`/&__`/!=\`Q%<>^D2/JVI7RZA=C[9>2&6\VR1L58>4YP0<'M324MD_Z^0FY+=K^OF8VI(NJ*
MAFN;E7$+V[F/1;D#RI!'Y@4?PMNCRK9.T'C-+XD
M3QY5-V&?Y3OD.X[GXS@<#%:O_"6:'_S^_P#D)_\`"K]CJ%KJ4!FLY?,C5MI.
MTCG`/<>XIN%E=Q?]?(2;>TE_7S*_]NV?_/&__P#!=?:E>1/JEVX2?
M#3N1FWD!^\>Q'%>I5YSJB_\`$VO/^N[_`/H1KHPSC=V1G64K+7\/^"97VF+^
MY-_WX?\`PKKO">JVUOI$FZJ:YS;79>#QC29?^NY_]!6ML
M0X\FIG24N;?^OO+O]NV?_/&__P#!=;60'J>Q6
MO1JX;4!_Q,KK_KL_\S7/AW&[T_K[C6HIVW_#_@F5]LA_YYW'_@/)_P#$UTWA
MO5[:#3Y%:*]),I/R6,S#H.X0UC8KJ/#`QILG_78_R%:UW'DV(IJ7-O\`U]Y8
M_MVS_P">-_\`^"ZX_P#B**T:*XKP[?C_`,`Z+3[K[O\`@G/^*?#<_B)].6.\
M$$5M*[2J5W<-&RAU])%)RIS@$YYP`5C\-SM'?QWFH).NH1B"XVV_EF1`CKN.
M&QYAW+EP,$(`%';?HJ"SF8?"4XU"6^N-2226\F@FO=EN5$IA(,03YSLP5&<[
ML\]*Z:BB@`KR_5U_XG-[_P!?$G_H1KU"O-=53.KWG_7P_P#Z$:[,)\3,*^R,
MW97<^"!C1IO^OAO_`$%:XW97:^#!C2)?^O@_^@K6^)?[LRHKWCH*\^U(?\32
M[_Z[O_Z$:]!K@M17_B9W7_79_P#T(US8;=FU79%';77^$AC2Y?\`KN?_`$%:
MY7;76>%1C3)/^NQ_]!6M<0_<(I_$;5<5?C_B8W/_`%U;^9KM:XV^'_$PN/\`
MKJW\S6%#=FE38J;:Z;PV,:=)_P!=3_(5SNVNC\.C&GO_`-=3_(5K6^`FGN:U
M%%%<1N8-_:^$],EMHKVPTR![IRD(>V3YB!D]N``.IXY'K26EOX3O5G:#3K`B
MW&Z0O9!,+SAAN494[6PPR#@X/%4O&NGZE=WVBSZ99">:&69?-P#Y>Z)@`X;C
MRV/#'K@`+R13DLM0U+2-4@N=*GLKO4;8VNYVA,<*;)`BKL#;B2&./3K,/,VT*^G%"AXP'R@V9R,;L;LC&
M?9P[(SO^$=T/\`Z`UA_P"`J?X5PFHZ99)J5TJ6=NJK,X`$0``R:],K@=27
M_B9W7_79_P#T(UTX:IK4IP
MML9/]EV/_/E;_P#?I?\`"NC\/:%I$U@[3:792,)2,O;H3C`]JR]M=)X<&-/D
M_P"NI_D*TK3ER;D0IQOL2_\`".Z'_P!`:P_\!4_PKEKS2--6]G5=/M0HD8`"
M%<#GZ5W5#_39_^NC?SK&C.5WJ7.G#L97]DZ?_`,^%M_WY7_"MW0]"TB6R
M=I=*LG;S",M;H3T'M5';6_H0Q9/_`-=#_(5I5G+EW)A3C?87_A'=#_Z`UA_X
M"I_A16C17+SS[FWLX=D%%9WD:Y_T$;#_`,`7_P#CM'D:Y_T$;#_P!?\`^.T<
MJ[_G_D',^S_#_,T:*SO(US_H(V'_`(`O_P#':/(US_H(V'_@"_\`\=HY5W_/
M_(.9]G^'^9HUQ&H)G4;D_P#39_YFNF\C7/\`H(V'_@"__P`=KE;R#4OML^ZZ
MM2?,;)%LP'7_`*Z5O023>OYF=23MM^7^9'Y==/X9&-.D'_38_P`A7+>1J/\`
MS]6W_@,W_P`76]H4&L?8G\J^LE'F'AK-V/0?]-16M9)QW(@W?;\O\SHZY&]7
M_3KC_KJW\ZW?(US_`*"-A_X`O_\`':YNZ@U/[7-NN[0GS&R1:L.__72L:*2;
MU_,TG)]OR_S#970^'QBQ?_KJ?Y"N9\C4O^?NU_\``9O_`(Y6UH\&L?9&\N^L
ME'F'AK-SV'_345I52Y=R82=]OR_S.@KF+M?],G_ZZ-_.M;R-<_Z"-A_X`O\`
M_':P+F#5?M4N;RT)WG)%JP[_`/72LJ25WK^94Y/M^7^8_;6YH@Q9O_UT/\A7
M-^1JG_/W:?\`@*W_`,&1.2R]\C`)Q5AKW4+73?%(-1M8[Z[>WTR\L([3?<.^]9W03!B3^\X)
MQNSMSQCBN_JE#HVEVYMS!IMI$;7<8-D"KY6[[VW`^7/?'6KM`!7+7B9O9^/^
M6C?SKJ:YVY3-U,?]MOYUM2>K(F4MGM6[H8Q9/_UT/\A67Y=:^D#;:L/]L_R%
M75?NDQ6I?KG+I?\`2YO^NC?SKHZP;A?])E_WS_.LZ6Y4BKMK9T<8M&_ZZ'^0
MK,V5JZ6,6S?[Y_D*NH_=%'-__P""
MZX_^(H_MVS_YXW__`(+KC_XBM&BKO#M^/_`(M/NON_X)G?V[9_\`/&__`/!=
M\`Q%']NV?_`#QO_P#P77'_`,16C11>';\?^`%I]U]W_!,[^W;/_GC?_P#@
MNN/_`(BLN:_B>9V%M?D%B1_Q+Y_7_WODE@$LGE.(5`5H
MX;B5HQQRH\J)2>3DR8*\;7&45T_'_@"<9OK^'_!+OVV/_GUO_P#P`G_^(J]8
MZO;00E7@OP2V?^0?/Z#_`&*YW6O%&KZ=I][9;T1;8`Z69@E,:M\JDX
M*@G+Y&X#H#QW:L'0,,X89&00?R/2FYQ:M;\?^`"C)=?P_P""9_\`;MG_`,\;
M_P#\%UQ_\169+J$33.PMK\@L2/\`B7S_`/Q%=)7,ZQ?:E;ZDXL[Z1H_-BBEC
M2%-ELDA1=VX@DR`L6QG:%ZKT)2E%=/Q_X`.,WU_#_@B?;H_^?6__`/!?/_\`
M$5>LM7MH82KP7X);/_(/G_\`B*YU==UV>.1(KIEF6_ETR/S1&BN%0LMQG8>6
M("]-N6X!.*ZO1+I[O2T>1Y'DCDDAD:4J6+QNR-RJJ",J<'`XQP*;G%K;\?\`
M@`HR77\/^")_;MG_`,\;_P#\%UQ_\169+J,33.PMK\@L2/\`B7S_`/Q%=)7,
MZQ?:E;ZDXL[Z1H_-BBEC2%-ELDA1=VX@DR`L6QG:%ZKT)2E%=/Q_X`.,WU_#
M_@A]OC_Y]K__`,`)_P#XBKMEJ]M#"5>"_!+9_P"0?/\`_$5S?_"2:TJEEDED
M==3;2E1D0!UP<7)(3@DX']SGI76:#@`Z444`252DT;2I;N2[DTRT>XE79),T"EW7&,%L9(QQCTHHH`=_96G
M?]`^U_U/D?ZE?]7_`'.GW?;I4\$$-M`D%O$D,48VI'&H55'H`.E%%`$E%%%`
#'__9
`
end
GRAPHIC
17
g46861bci004.jpg
GRAPHIC
begin 644 g46861bci004.jpg
M_]C_X``02D9)1@`!`0$`8`!@``#_VP!#``H'!P@'!@H("`@+"@H+#A@0#@T-
M#AT5%A$8(Q\E)"(?(B$F*S7J#A(6&AXB)BI*3E)66EYB9FJ*CI*6FIZBIJK*SM+6VM[BYNL+#Q,7&
MQ\C)RM+3U-76U]C9VN'BX^3EYN?HZ>KQ\O/T]?;W^/GZ_\0`'P$``P$!`0$!
M`0$!`0````````$"`P0%!@<("0H+_\0`M1$``@$"!`0#!`<%!`0``0)W``$"
M`Q$$!2$Q!A)!40=A<1,B,H$(%$*1H;'!"2,S4O`58G+1"A8D-.$E\1<8&1HF
M)R@I*C4V-S@Y.D-$149'2$E*4U155E=865IC9&5F9VAI:G-T=79W>'EZ@H.$
MA8:'B(F*DI.4E9:7F)F:HJ.DI::GJ*FJLK.TM;:WN+FZPL/$Q<;'R,G*TM/4
MU=;7V-G:XN/DY>;GZ.GJ\O/T]?;W^/GZ_]H`#`,!``(1`Q$`/P#U3_A(M#_Z
M#-A_X%)_C1_PD6A_]!FP_P#`I/\`&J.HZ_>6?BZRTB.UB-O<6S2^9))L:5PZ
M@I'G@E5)8CN#VQS-9:EJ.H:#)=100PW?VF:$++]V-4G:/+8/)"KD@$9(X(SQ
M=X=OQ_X!%I]U]W_!+'_"1:'_`-!FP_\``I/\:/\`A(M#_P"@S8?^!2?XUS:^
M-+^*UFOIX+=[>W>6`K&A4S,ENUP)5.X@(R*N%()&[[QQ72:/>75R+RWO3$]Q
M97'DR/"A1'RB2`A221PX'4\@T7AV_'_@!:?=?=_P0_X2+0_^@S8?^!2?XT?\
M)%H?_09L/_`I/\:T:*+P[?C_`,`+3[K[O^"9W_"1:'_T&;#_`,"D_P`:/^$B
MT/\`Z#-A_P"!2?XUHT47AV_'_@!:?=?=_P`$SO\`A(M#_P"@S8?^!2?XT?\`
M"1:'_P!!FP_\"D_QK1HHO#M^/_`"T^Z^[_@F=_PD6A_]!FP_\"D_QH_X2+0_
M^@S8?^!2?XUHT47AV_'_`(`6GW7W?\$SO^$BT/\`Z#-A_P"!2?XT?\)%H?\`
MT&;#_P`"D_QK1HHO#M^/_`"T^Z^[_@F=_P`)%H?_`$&;#_P*3_&C_A(M#_Z#
M-A_X%)_C7`^''$WA\QI1WR)RU\1^\4C*2="R@]"A/7%=CK`6;7
M-#DCNW_=WTD31H5*JQMICD\9W`8]N>E%X=OQ_P"`%I]U]W_!+O\`PD6A_P#0
M9L/_``*3_&C_`(2+0_\`H,V'_@4G^-<1J2O!HL*X-W-Y^J16HD*AOM7VD^5*
M,X7>"&P!\WS'`QNQZ11>';\?^`%I]U]W_!,;4/#5OJ/B"UU>:>4?9XO+,(/R
MN1(DB'VPR9XZ\9.!@ESX=6>R>P2_N(;65II)50(69Y)A+U*D;0=Z[2""K$'-
M;-%0681\*6DSN;V[NKQ9%;S$E\M1([(8RYV(OS>6=G&!C'&>:T=-TY-.AD43
MRW$LTADEGFV[Y&P!D[0!PJJ.!T`JY10`4444`%%<9XKE6+Q?X?+37+$WD2K!
M&".JR@NIS@CD;^#\NWIGG'TJSL]5@CL9[&WECN#;0-,Z(_F7`65[B3U1V2-<
M[L,,C(!XH`]+HKEM`DMXO%NK6]LZO'*FYE1RS1R)(^XR@@;"?,`3KE(A@X`K
MJ:`"BBB@`HHHH`YCQ5J%SHJ6B::Z6RRM*SA(UPS$@D\CJ2Q)]2:YQ/$^LQEB
MEV%+MN8B%/F.,9/'H!^5;GCP9^P?]M/_`&6N0VUZ="$'33:..K*2F[,Z?P]X
MAU6^URWMKFZ\R)]VY?+49PI/4#U%=M7G/A48\26O_`__`$!J]&KEQ45&:LNA
MM1;<=3._LR[SC^WK_P#[XM__`(U1_9EY_P!!V_\`^^+?_P"-5S7B"40_$C2O
MWETQ>SV+'&Q7RR9D&]."'/\`?7LBY["GAXH?"$EK-=_P!)%\B\_O9T7]F7G_0=O_\`OBW_`/C5']F7G_0=O_\`OBW_
M`/C5>>1><(+TV7_'_P"?>?8/)QYG]G_9I?)VXY\OS-N.V[%=OX6^R^1?_P!G
M>3_9OVO_`$/R,>7L\N/=MQQCS/,_'-'._P"D@Y%Y_>RY_9EY_P!!V_\`^^+?
M_P"-4?V9>?\`0=O_`/OBW_\`C5:-%'._Z2#D7G][.3\133Z.]H[ZA>W3%F:,
ML+<&-@,9'[D\X%!CQ):_P#`_P#T!J]&KGQ%H3M%?@;4ES1NV_O9RNJZQ;Z-
MJ/V&\\0:HKBU:ZD98(&6.,,%!;$76ZXS!%X-U(3Q2"[6W22YCEN(Q=N/-ZD+@\_._
MZ2->1>?WLU]/9M4>\6UU_46^Q7)MI&,=O@N%5CC]WT&['U!J[_9EY_T';_\`
M[XM__C55O#FA2:"+Z)KR2YBFG5XC+MW[1%&GS;57YLH?P`/4FMJCG?\`20_5+J?._'F+$,?=Z;4%AM1@N7_@L888FF68Q
MH944JKE1N53@D`^AVC/T'I08HS*LI13(JE5;'(!QD?C@?D*H_P!IWG_0"O\`
M_ONW_P#CM']IWG_0"O\`_ONW_P#CM?]`*_P#^^[?_
M`..T?VG>?]`*_P#^^[?_`..T?W,P_'0S]A_[:?\`LMNV[KI]Q*1N^1&CR?E/JP'ZUW']IWG_`$`K_P#[
M[M__`([7+BHMS7IW-J,TH_\``9@^/1G[!_VT_P#9:X_%=-XSO+B;[%OTNZ@Q
MYF/,:(Y^[TVN:YCS9/\`GUE_-/\`XJNO#IJFC"K)<[_R-GPH/^*DM/\`@?\`
MZ`U>CUYEX;N9H]?MG6PN)2-WR(T>3\I]6`_6N\_M.\_Z`5__`-]V_P#\=KEQ
M46YKT[F]":4?^`S'\:C/V+_MI_[+7+8K>\6WMQ-]DWZ5=PXWXWM$<_=_NN:Y
MWSY?^?*?\T_^*K>@FJ:,JDES/_(V/#(_XJ"V_P"!_P#H!KOJ\Z\/W4T>MV[K
MIUS(1N^56CR?E/JX%=I_:=Y_T`K_`/[[M_\`X[7/B8MS7^9M2FN7_@,HW^O7
MEIXPL='2VA^S7-LTOFRR;3(P=5*IV)526([CTQS=\0:D^D:/+>(T*,LD:;YO
M]7'OD5-[+RS"#\KD2)(A]L,F>.O&3
M@8.AJ%C'J5FUM*[Q@LCJ\9&Y'1@RL,@CAE!Y!''(-<9T')1>-KT6],3W%E<>3(\*%$?*)
M("%))'#@=3R#5"/P9IJ;U>2XEBE\QY8G*A999%9'E.U0=Q5V'!"X/`%:FFZ<
MFG0R*)Y;B6:0R2SS;=\C8`R=H`X55'`Z`4`7****`.6\:C/V+_MI_P"RURV*
MZOQD,_8_^!_^RUS&VO3H?PTO..E3W6C^';*VDN;C2+!8XQEB+16/T`"Y)]`.36-H=_P`/^"5>
M?9??_P``UZ*YJ)_!DT@1;&P!V,Y+V.Q5V@EE)*@!@%)*'Y@`3CBK=CIOAO4K
M?S[;2+(IN*D26(C92.Q5E!'XCN*+0[_A_P`$+S[+[_\`@&U16=_PCNA_]`:P
M_P#`5/\`"C_A'=#_`.@-8?\`@*G^%%H=_P`/^"%Y]E]__`,OQ@,_8_\`@?\`
M[+7-8K:\4:+I<'V7R--M(MV_.R!5ST]!6#_9UE_SYP?]^U_PKOH\O(M3FJ:4G.VWX_P#`,GQD,_8_^!_^RUS&VMWQ3HVE
MV_V7R--M(MV_.R!5S]WT%<__`&=9?\^D'_?L5T4>7V:,JG-S/3^ON-?PX,:]
M;?\``O\`T$UW5>?:%I6GRZS`DMA;2(=V5:%2#\I[8KL/^$=T/_H#6'_@*G^%
M<^(Y>??^OO-:7/R[?C_P#-\6#/V3_@?_`++7.[:U_$NBZ5!]F\G3+./=OSL@
M49Z>@K#_`+,L?^?*W_[]+_A6]'EY%J1/FYMOZ^XUM`&-:M_^!?\`H)KM*X/1
M=)TZ75H4DT^U=#NRK0J0?E/M75_\([H?_0&L/_`5/\*Y\1R\V_\`7WFE-SMM
M^/\`P#%UC3]2D\>Z;>V5FIB%H8YK@@%2HFC8H^>F!EDV\EO8&M?Q%8RZAH[P
M0J[NLT,NR-]C,$E1R%;(PQ"D`Y'..1UK4HKE-S@9/#>MWMI=6Y6>
M:56\M6M'MXXF(8LS@%26Y!P>2:ZK1(+A6O[RYMGM7OKKSA`[*6C`CCCY*DCG
MR\\'O6I10`4444`<]XK&?LO_``/_`-EKGL5T?B@9^R_\#_I6#MKOHOW$<\_B
M+F@C_B+1G[)_P/\`]EKG
M=M=+XJ&?LO\`P/\`]EKGMIKHH_`C*?Q%WP^N-;M_^!?^@FNTKC]"7&LP?\"_
M]!-=A7/B/B-*6Q@^)QG[+_P/^E8&VN@\2C/V;_@?]*P\5M2^!$3^(MZ&,:O!
M_P`"_P#03775RFBC_B;0_P#`O_0375UA7^(TI[&=_9EWG']O7_\`WQ;_`/QJ
MC^S+S_H.W_\`WQ;_`/QJN;UZ80?$K227N9"]GL$2.4"9G0;E[.3_`!KQA%SV
M%=+K;7@TF9;""6:>3"8A9%=5)PS*6(&0,D9/4"L^=_TD/D7G][$_LR\_Z#M_
M_P!\6_\`\:H_LR\_Z#M__P!\6_\`\:KSJS:X.AVYMD9=6^Q`0!,&;[*-..TC
M'.PS\C_:QWKN?"WV7R+_`/L[R?[-^U_Z'Y&/+V>7'NVXXQYGF?CFCG?])!R+
MS^]ES^S+S_H.W_\`WQ;_`/QJC^S+S_H.W_\`WQ;_`/QJM&BCG?\`202YW??2'CIZ1BL7
M['-_T$+G_OF/_P"(KJ?$@S]F_P"!?TK$VUM2F^1&E/K._M.\_P"@%?\`_?=O_P#':/[3O/\`H!7_`/WW;_\`
MQVLN1_TT7SKS^YFC16=_:=Y_T`K_`/[[M_\`X[1_:=Y_T`K_`/[[M_\`X[1R
M/^F@YUY_IC=]YX>>GI(:S/M=Q_T"KO_`+ZB
M_P#BZZJ<7RHRE-7_`.`S3TD8U*+\?Y&NDKDM.O;E+^-AI%XQ&>`\.>A]9*W/
M[3O/^@%?_P#?=O\`_':RJQ;E_P`%%0FK?\!E?Q`,_9_^!?TK&VU=UF_NI/)W
M:->IC=]YX>>GI(:S/M5Q_P!`NZ_[ZB_^+K6G%\J(E-7_`.`S3TA<:G#_`,"_
M]!-=+7(:;>W*7\;#2;QB,\!H_NG\G.C7J8W?>>#GIZ25F_;+C_H%7?_`'U%
M_P#%UK3B^5?YDRDK_P#`9IZ4N-1B_'^1KHJY/3[ZY6^C(TB\8C/`>'/0^LE;
M?]IWG_0"O_\`ONW_`/CM958MR_X**A-6_P"`RC?Z]>6GC"QT=+:'[-?D!3-G8H)`+$`C.!DXR,XQD9S6=J
M'AJWU'Q!:ZO-/*/L\7EF$'Y7(D21#[89,\=>,G`P;NJZW>6`K&A4S,ENUP)5.X@(R*
MN%()&[[QQ72:/>75R+RWO3$]Q97'DR/"A1'RB2`A221PX'4\@U3/A2TF=S>W
M=U>+(K>8DOEJ)'9#&7.Q%^;RSLXP,8XSS6CING)IT,BB>6XEFD,DL\VW?(V`
M,G:`.%51P.@%`%RBBB@#,UD9\G_@7]*R]M:VK#/E?C_2L[;73!^Z9RW)=-&+
M^/\`'^1K=K&L%Q>Q_C_(ULUE4W*CL9>M#/D_\"_I67MK7U89\K_@7]*SMM:T
MW[I,MR335Q?Q_C_(UO5BZ>N+V/\`'^1K:K*KN5'8S=8&?)_X%_2LS;6KJHSY
M7X_TK/Q6D/A)EN2:<,7T?X_R-;E8]@/],C_'^1K8K.IN5'8**SO^$=T/_H#6
M'_@*G^%'_".Z'_T!K#_P%3_"E:'?\/\`@BO/LOO_`.`:-%9W_".Z'_T!K#_P
M%3_"C_A'=#_Z`UA_X"I_A1:'?\/^"%Y]E]__``#1HK._X1W0_P#H#6'_`("I
M_A1_PCNA_P#0&L/_``%3_"BT._X?\$+S[+[_`/@#M3&?*_'^E4=M5-S09EE\I`PZ_<7:=V`"3DC`YYZ52:[T>"]BLKGPMIR7'V@0SB-$98
M\F``J2@W1@8PW)P,VI12M_7YDM3?1??_`,`W[)<7:?C_`"K6KF]%@\/Z
MVMY)#H-BD5O<>4CFWC/FKL1PXXZ$."/;![XK3_X1W0_^@-8?^`J?X4I.#>_]
M?>-'9_#WB-C);>'[!+5D+PR-;J&?#;3E2@&,]U+>^#Q6]_P`([H?_`$!K#_P%
M3_"IDX-[_P!?>-7"Q^2T
M+VZB,QNK9W9W*6&1@'!'055/A*QDECFN+BYN)A-YLDDC+F8YC(#`*!@&"+H`
M?DY)RV=VB@"AI>BV&C&Z&GVZ6Z7,HE:.-%5%.Q5PH`&!\N?J3ZU?HKEK[Q#=
M17$4]M(KH]X\,=L<*)`C>006P2N9Y$Y[!1ZG(!MZIIG]J0PQ_;+BU,,HE5X`
MA)(!P"'5@1DYZ=0#VJB?"ED)Y;B&YNH)WF\Y)49H)^?@C"
MXBN/$UQ%9V,D6GQ23W2L[1FY*J%#HGRML.XEI%P"!G/:J=]XGG$5O(6%E(HW
MS(LBR(460DD$KDAHX)L'C`))&1P`;6G:%;Z;.LD<\\JQQM%!'*P80(Q!95.,
MX)5>"3C:`,`8K3KCX/%=QI^GR27P:[-HJ_:YF8)M(4HVQ53GYXI"03QZ]%&C
M8^(+ZYOXK2XTN*#+.LL@NMR@KG(0E!O(Q\P^7'4;@#@`T=4TS^U(88_MEQ:F
M&42J\`0DD`X!#JP(R<].H![51/A2R$\MQ#LM(E#6K2>7
M&KI!$VW;`KL&<+@`_,P!.2>G&!Q6K110`4444`%%%%`!1110`4444`%9L.@Z
M?&\<%5//H*C/AS26B2)K3DO.9
MFM26(((\U]I)+$DKG&[YV^;&<,1G!Q3)/#6F9D=(Y8VE+[BL[XS(Q+D`G`8[
?V&X#(#$`@444`:RJ%4*H`4#``'`I:**`"BBB@#__V3\_
`
end
GRAPHIC
18
g46861bei001.jpg
GRAPHIC
begin 644 g46861bei001.jpg
M_]C_X``02D9)1@`!`0$`8`!@``#_VP!#``H'!P@'!@H("`@+"@H+#A@0#@T-
M#AT5%A$8(Q\E)"(?(B$F*S7J#A(6&AXB)BI*3E)66EYB9FJ*CI*6FIZBIJK*SM+6VM[BYNL+#Q,7&
MQ\C)RM+3U-76U]C9VN'BX^3EYN?HZ>KQ\O/T]?;W^/GZ_\0`'P$``P$!`0$!
M`0$!`0````````$"`P0%!@<("0H+_\0`M1$``@$"!`0#!`<%!`0``0)W``$"
M`Q$$!2$Q!A)!40=A<1,B,H$(%$*1H;'!"2,S4O`58G+1"A8D-.$E\1<8&1HF
M)R@I*C4V-S@Y.D-$149'2$E*4U155E=865IC9&5F9VAI:G-T=79W>'EZ@H.$
MA8:'B(F*DI.4E9:7F)F:HJ.DI::GJ*FJLK.TM;:WN+FZPL/$Q<;'R,G*TM/4
MU=;7V-G:XN/DY>;GZ.GJ\O/T]?;W^/GZ_]H`#`,!``(1`Q$`/P#V6BBB@`HH
MHH`****`"BBB@`HHJ&YNX+2/S)Y%1??O]*$K@345S=YXH8Y6TBP/[[_X5D7&
MH7ESGSKB1@>V<#\AQ6\:$GOH9NHEL=K)>6L)Q+<1(1V9P*A&K6#2*BW*EF.`
M!SDUP]3V/_'_`&__`%U7^=:_5TEN1[1G2KXLT`N4.J6ZD$@[FVX/XU?MM1L;
MW_CUO()_^N4@;^5>#WO_`!_7'_75OYFH.AR*[/[.BUI(\W^TI)V<3Z(ZT5X?
MI_BO7-,(^SZA*4'\$IWK^1Z?A78Z/\4(I"(M7M?*/_/:#)7\5ZC\,URU,#5A
MJM3JIX^C/1Z'?T57L[ZUU"W6XLYTGB;HR'(JQ7$U;1GQ_P"/^W_ZZK_.D]AK<\[O?^/ZX_ZZM_,U!4][
M_P`?UQ_UU;^9J"O7CLCYR7Q,****9)>TO6+_`$:Y%Q8W#1-GYEZJ_L1WKU/P
MMXUM-?46\X6VO@.8R?E?W4_TZ_7K7CU.1WC=9(V*.IRK*<$'U%J/D<\>5=)>LL9@8@,`QR5Y#*002.:C\5VEQ=:1$UM$TSVM[;7)B
M3[SK'*KL!ZG`.!6#KMSK6I1VFHP6\`(<_O&(`X(
M&&(P*`.P?4+*.ZAM9+R!+B=2T,32J'D`ZE1G)'TJ$:WI),X&J69^S.J3?Z0G
M[IB<`-SP22``>YKB[;3+O27T9(]/O+F[-K90RB>V#Q.(W.2S*2(9(P2V2V&X
M`R>E:33;MM/_`+.M=)NWM8&ME7[5:D30?Z7$S1!\8E3:"VX9P$Y8YX`.\.N:
M0-/;4#JMD+-6V&Y-PGEALXQNSC.>*O`AE#*001D$=ZX#48+^#Q!JD2:7<"VN
MKW?#=Q6AE,3_`&2)%*#!`W%I`7(*C:0>O'3>%@UEX*TA+J-X'MM/A25)$*LC
M*@#`@^A!H`FUS4_L-OY<1_?R#Y?]D>MW^*KPW0N(@EW+&YDWG:2%'`X#$8QEAS]!34I;A9&315B^2%+MU@QY8`Q
MM.0#CG!^N:KULG=&85/8_P#'_;_]=5_G4%3V/_'_`&__`%U7^=)[#6YYW>_\
M?UQ_UU;^9J"I[W_C^N/^NK?S-05Z\=D?.2^)A5O2[./4-1AM9KN*TCD)W32D
M!4`!/?'I^=5*TM".GKJ!.HS/;J(R89E4MY4HY5B`.1[4IMJ+:'32^)DE\47]_;
MWLZ69_>1PY8+/(JA5RH[9`//88KBC*N_^&]/+U_X!WRAAUV^_P!?/T_X)@WD
M#Z1J?E0W!,]N5RZ#&R0=0/H>,^U>N>$/$:>(=*#R%5NX<+.@]>S#V/\`C7G.
MNWNCW6D1BS\DW!DC;"P%9%'ED/O0J-98>M9/W6>N^(=7ET73H[BWM%NYI;F&WCB:7RP6D<(,M@X
M&3Z56M/%$']G7-SJIKGV\-:Q%:0W%A93Z=!!J9N8-.M)8/.@C
M:W,;;2^8LEV9B,XPQP_\?UQ_UU;^9J"O7CLCYR7Q,****9(4444`%%%%`'KW
MP\U8ZCX<6WD;,MFWE'_=_A_3C\*ZJO*?AE?&W\0R6A;"W41`'JR\C]-U>K5\
M[BZ?)6=NNI]+@ZGM**;Z:!1117*=84444`%%%%`!1110`=!7`WDGFWD\G]Z1
MC^IKOJ\[-=6&W9C5Z!111768A1110`4444`%3V/_`!_V_P#UU7^=05:TV*26
M_AV(6V.&8^@!Y)I2V8UN><7O_']]=6_F:@K5U?0]2M)I;F6T#N7(K*KUH23CHSYVI%QDTT%%%%40%%%%`!1110!K>%K@VOBC3I!QFX5,^
M@;Y?ZU[E7@6DDC6+(C@BXC_]"%>^*_%GMY8_P,#%>+^!K0W?BVS&,K$6D8^F`COU6$_U;
M]!1Y(!TGDZ:@ENUWS$9CM_ZMZ#VZFL:ZNIKR61I)&
M+NQRS$Y)-(JL[A%!+,<`#N:TC&VK(QVW@/2=.CDN-4LXKB(L/*V2L&"]"=K8!/;K79U0T73ETO
M28+0`;D7+D=V/)_6K]>+6GSS;/3I04()(****R-`HHHH`****`"BBB@`HHHH
M`Y/Q#IQM;G[3&O[J4\X[-W_/_&LN""2XE\N)I]!7=W-O'=0/#*N58
M8-<-X@^T:?(=/CC,5N0#O'6;W)]O3M7=1FY+EZG/4CRZ@;I%D-EI\\22,")+
MN1P@^BD]![]34'_".W0<*9[8;@FUA(2&W$A0,#O@^U9UM&DMU%'(P1&N:UIM2E?7YA;W*0P/*%#D*RJJ<`C([#D8K=J47:)DFGN94]M);"/S,!G!
M.WN!DCG\JL6#"TBGU)\?Z,,1`C[TI^[^7+?A5ZZ.GW=A)=L(UE9"5_>_.K!P
M%7;GIL[X_&LK6W^SI!I:G_4#?-CO*W7\A@?G51?/H3+W=3))+$LQ))Y)-)11
M74GXT@(J*ZW5]3NX6MK8O$VJ&8M@1JPMU88$
M7(P:EN-:CM=;EM'$C/&88PT"+F4J3O4C@88G'X=*P]K*VQK[-=SC:*WM6TR1
MX?-@DA^SVT;%(@3DJ'VNXXQC>3WSC%8-:QDI*Z(E%Q=@KK?!&B&XN?[3G3]U
M"<1`_P`3>OX?S^E8V@Z'-K=Z(ERD*]>I6UO%:6\=O`@2.-=JJ.P
MKEQ5;E7(MS>A2N^9DM%%%>6=X4444`%%%%`!1110`445Y@U[=Q:;XFU)DUQY
MK674!%<-?N+0!7=54()000.!A1C'!'6@#T^BN1G\2ZO%J5RRK9?8;;6(=.:,
MQOYKB01?-NW8!!E)^Z<@8XZU1/C;54BO8\:=-<1"S>-XDD\I1-<>4R%B?WFT
M9^=<`GMP10!WE5-1TZWU.U:WN%R#RK#JI]17,V_B36[B^?1$^P?VG'A/M1<>.!;>((=-GDLH)5FM[:>R9]TYDF"G*'."J[U
MSP<\\C'+3:=T)JYB:KH]UI,^R9K3V\-U"T,\:R(W56&:
MY+5?!LB%I=-;>O7RG/(^A_QKT*6)3TEN61BSNQ9F/4D]36MK.ZQL[?3"I20_O[@'^\?NC\!^I-8U==/7
MWCFJ/H%%%%:F84^&5X)DFC.UXV#*<9P1R*910!HW.O:E=RQ2SSJSPR"1&\I`
M0PZ'@<_C547EP+TWOF?Z07+E]H^\>^,8_P`_E!4UM:7%Y,(;:%Y7/\*+G_\`
M54\L8K8=Y-DHU*\6Q^Q"7$&",;!G!.2-V,XSSC-7-"\.W>MS?(#';J?GF(X'
ML/4UOZ+X$P5FU9O<0(?_`$(_X?G79111P1+%$BI&@PJJ,`"N*KBHQNJ>YU4Z
M#EK,@T_3[;3+1+:UC"(OYD^I]35JL+Q)<3P7WAY89I(UFU01R!&(#KY$QVGU
M&0#CV%8%OXXU2VT>TU34X;.2*\T>;4$CMT9"C1!"5)+'(;S!V&,=Z\YMMW9V
MI6.\HKB+76]9T^XU47LL-Q<#6;&U(4,(D25(%;8I8E?ODXSU.>:D;Q=JS6MI
M<"&S@AEGNTDGG5_*S%.8TC+`_(S*,[VR,@\<\(#LZ*X:/6==L'UV7[3;7).O
M06=LDJ/MB600@_QGC#C@8^;<>TA1QBE#X#TZ&-8_ME](B100J'=.
M(X91+$OW>@(QZD$YR>:Z:B@#$E\*VKW,]W!>7=K51TR2I_+']:IOX,UU3A;17]UE4?S(KTZBMUC*B,GA
MH'F*>#-<8_-:K'_O2J?Y$U=M_A_J+D>?07$D[RNT3KR'2-'CY4_*1$G^T#G!%;]%`&3H'ART\.6\L-I+/(LOEY,S*2`
0D21*!@#^%%_'-:U%%`'_V3\_
`
end
GRAPHIC
19
g46861bei002.jpg
GRAPHIC
begin 644 g46861bei002.jpg
M_]C_X``02D9)1@`!`0$`8`!@``#_VP!#``H'!P@'!@H("`@+"@H+#A@0#@T-
M#AT5%A$8(Q\E)"(?(B$F*S7J#A(6&AXB)BI*3E)66EYB9FJ*CI*6FIZBIJK*SM+6VM[BYNL+#Q,7&
MQ\C)RM+3U-76U]C9VN'BX^3EYN?HZ>KQ\O/T]?;W^/GZ_\0`'P$``P$!`0$!
M`0$!`0````````$"`P0%!@<("0H+_\0`M1$``@$"!`0#!`<%!`0``0)W``$"
M`Q$$!2$Q!A)!40=A<1,B,H$(%$*1H;'!"2,S4O`58G+1"A8D-.$E\1<8&1HF
M)R@I*C4V-S@Y.D-$149'2$E*4U155E=865IC9&5F9VAI:G-T=79W>'EZ@H.$
MA8:'B(F*DI.4E9:7F)F:HJ.DI::GJ*FJLK.TM;:WN+FZPL/$Q<;'R,G*TM/4
MU=;7V-G:XN/DY>;GZ.GJ\O/T]?;W^/GZ_]H`#`,!``(1`Q$`/P#V6BBB@`HH
MHH`****`"BBB@`HHHH`***K76H6MDN9YE4_W1R3^%-)O8-BS17.W/BGJ+:W_
M`.!.?Z5G2Z]J,I_U^P>B+BME0FS-U(H[.BN%2^NWF3='\9'>N-UC6=4@
MUV\$6HW2*LS!5$S8`SZ9K:G@W-VN85L4J23:/;**\4MO&OB*U(VZD[@?PR*&
M'\JWM/\`BE>QD+J%E%,N>6B.T_D:J6`JK;4RAF%&6^AZ;16#I'C/1=8*QQ7(
MAF/_`"RF^4_AV-;U<4H2@[25CNC.,U>+N%%%%24%%%%`!1110`4444`%%%%`
M!1110`4444`%%%%`!1110`4444`%,EEC@C,DKA$7J33+JZBL[=IIFPJ_K[5Q
MVI:I/J,N7.V(?=C!X'O]:UITW-^1$I*)H:CXCDE)CLOW:?\`/0]3]/2L-F9V
M+,Q9CU).2:2BNZ,%%61@VWN%%%%42/B_UT?^^/YUP^O?\AZ^_P"N[?SKN(O]
M='_OC^=I0HHHKN/)"NFT#QUJ>C,L4SF
M\M1UCD/S*/8US.:,U$Z<:BM)7-*=2=-WB['N^C:[8:[:"XLI@V/OH>&0^A%:
M->!:9JEYI%XMW8S&*1?R8>A'<5[#X8\3VWB.QWIB.YC`$T/H?4>U>)B<(Z7O
M1U1[V%QBK>[+21N4445PG<%%%%`!1110`4444`%%%%`!1110`4444`%%%%`!
M37=8T+N0%49)/:G5S_B74"JBRC/+?-)].PJX1M5I];U&YU!=0FN2URJ[5?:/E'3`&,"N%8677L>B\7'I??^NN
MYKZ]H\KP&ZMI(/LEM%^[B5CNV;BI?IC!;/?IBL;2=5N=&U".]M'VR(>1V8=P
M:4ZQ?G31IQN#]F`QLVC.,YQG&<9YQFJ5=4(-1<9ZG)4J)S4X:,]YT;5K?6]+
MBOK<_*X^9>ZMW!KS_P`16\Y\4:_J,5G&1826DK7WG$26R*JL^Q,?-E0>XZU2
M^'_B`Z5JXLYWQ;79"\]%?L?QZ5Z+<^%=&O-3?49[5GN)2ID_?N$?:,#<@.TX
MP.HKP,31]C4MTZ'T&&KJM3YNO4X[7/%5Y?6^L00_:FMFCN[8I]E(CB"1L1)Y
MN.22.F>XXKHO!;LXUDLQ8_;QU.?^6$5:4_AO2+F:XEFM-QN4:.4>8P4AAAB%
MS@$CC(YJW9Z?::?YWV6$1>?)YDF"3N;:%SS[*!^%.ES"H];!111729!1110`4444`/B_P!='_OC^=6=_2-2:UD\+3Q#=J5Y;V(_N,V^3Z;5_QJ)5(QW9I"E.?PHQ%8
MJP920P.01V->X>%M6&L^'[:[)S)MV2?[PX->:);Z%9$>5:S7[@_?N6V(?^`C
M^M=CX'U=KF2>Q>.&)44-$D,84`=_Z5YV-?M(72V/5P,)4IV;W.QHHHKQSUPH
MHHH`****`"BBB@`HHK&7Q/9MJ?V/R+@1&;[.MV4'DM+_`'`,T`;-
M%4_[6TWR;B;[?;>7:G;._FC$1]&/:E?5=.C6W9[^W5;H@0$RC$I/]WU_"@"W
M15)-9TN2]:R34;5KE=VZ$2KO&WKQG/'>I++4;'4D=[&\@N51MK&&0,%/H<4`
M8GBJ3,MO$.P)-<_6UXH_Y"48_P"F0_F:SK>PDN(#,'B1`VW,C[OO^N[?SKN(O\`71_[X_G6+K/AD0ZQYR56+33[R_?99VLLYSCY$)`^I[5OI
M_8UG_P`>FF_:''_+6\;=G_@`X_G3KC5;ZYC$3W!6(#`CC`1/R'%=+JM_"OO.
M..%7VG]Q3C\,&(;M2U"WM./]6A\V3Z87@?G5J)-$LO\`46#WD@Z27;?+_P!\
M#^M5:*S;E+=G1&G".R_4NS:O?31^4)O)BQCRX%$:_D*I=R>YZFM+_A']0$%K
M*\8C^UR^5$CG#$XSD^@J9O#5XMVD'GVY5XS()@Y*8!P>V>O'2H4X+9F_+)F/
M6WX/N#!XEM@.!*&0_B,_TK-N+":UC+S;5(E:+;GDE>I^E3:&VS7+,@X_?**)
MVE!BC=21ZY15._U.#3IK*.97)O;@6\>T9PQ5FY]L*:6#5=.NI98K>^MY9(03
M(J2@E`"0<^G((_"O"/5+=%9-EXFTG4+NXM[>[C<0&)?-#KY;M)NVJISR?E/%
M6FUC3$\C=J%L/M#E()=N+^&);2Y-M(TLBJ
M-XYXYZ'G'T-2P^(]*DC5Y+V"`/.T,7FRH/,93CY>>?YT`:E%4].U*#4XYW@5
MP+>XDMWWC'S(VTX]N*N4`%<=IRZMIZRZ%!I\OF->S3&[=/W/E.S."K?WLMC'
M7BNQHH`\TT_0]3^PN^I)?2-:PPQL+:S$3+(C[MZY)\TCGM@@U/<6.H_8+.Y_
MLF47BI)%`B6F895\S[BCN+*!5\ZV\E4=2X9%7L!D8SG/TKLJ
M*`.6\4*?[0B;L8\?J?\`&H](G1(%1KJ&-!-NDCE4?,N.QJ[XJB)CMYNRDJ?Q
M_P#U5S==]-8GO5A6[D%O@QYXP14N+&[R^ES;F_Y]ICAQ]#T:LJ6*2&1HI4:-UZJPP16D9*6
MQFXM;FU%/;7.@V%I=7>TB^8R:`,D;LYW,>#N4=\L3FLO04,FO62
MCJ90:SZW_!5L9_$<3XXA5GS^G]:F2Y*]E\Y/*E
MA#Q.K7!<)(/X.,,&Z<=Z]+HH`X+^RKM]2:-].F*KXD^TLQB^1HC&^7/#;AW=C*S*A8_<0@Y![YXKU"B@#G_!MO<6^EW?
MVFWD@:2^GD595*L5+<'!]:Z"BB@`HHHH`****`"BBB@"AK5M]JTR50,LHW+^
M%<57H9&1@UQ.JV9L;^2/'R$[D^AKKP\MXF-1=2E111748A1110`4444`%0:U
MS>1,/XK=#_.IZBU@?\>C>L&/R)IKXD*6QFT445L9!T.1UJZ+\3QB'4(1=Q#@
M,3B1/HW^-4J*EI,:9-+H@G4R:7-]I'4PMQ*OX=_PK*961BK*58'!!&"*T%8J
MP9201T(."*N-?17BB/4X//P,"=/EE7\?XOQIJ4EOJ)Q3VT,*N\^']AY=E/?,
M.9FV(?8?_7KFCX?EN9%_LV9;J-V`]'CS_>7^HKTRPLX["QAM8Q\L2!?K7/BJ
MJY.5=36A3?-=EBBBBO,.T****`"BBB@`HHHH`****`"BBB@`HHHH`*S-6B';Z?X5T=%7";@[HF44]SSP@@D'@CL
M:2NRU'1+:_RX'E3?WU[_`%%:/>61):/>G]].17;"K&1A*#10HHHK4@*2^
M!;1U/]RX_FM+2W(SHT_^S*A_I1U0=#'HHHKQA1^
M-=7I/A""V*S7[">0C3W"Q8@LX6DV)U(49_.K@`4````=`*S_$%O-=>'=1M[=#)-+:R)&@
MZLQ4X%>;5JRJ/4[(0449]EXJ>46[:CIKZ;'YX
MXXI;G2]:L[J"ZMM/=Q'8644C1JC2)M,F_P`L$XWC
N\\=^Y`6#-NL8`[
M[]PQZ8)H`[.PU*RU2$S6-RD\:L5+(>A%6JYGP?I]];->W5^UUOG$2!;B../&
MP$<*G&.>O?%=-0`4444`%%%%`!1110`4444`%%%%`!1110`4444`%%%%`%.Y
MTFQNB3+;KN/\2\&LZ7PM`V3%<.GLP!%;M%6JDELR7%,YEO"LX^[
-----END PRIVACY-ENHANCED MESSAGE-----