0001466593falseFY2021http://fasb.org/us-gaap/2021-01-31#OtherAssetsNoncurrenthttp://fasb.org/us-gaap/2021-01-31#OtherAssetsNoncurrenthttp://fasb.org/us-gaap/2021-01-31#OtherLiabilitiesCurrenthttp://fasb.org/us-gaap/2021-01-31#OtherLiabilitiesCurrenthttp://fasb.org/us-gaap/2021-01-31#OtherLiabilitiesNoncurrenthttp://fasb.org/us-gaap/2021-01-31#OtherLiabilitiesNoncurrentP3Y00014665932021-01-012021-12-3100014665932021-06-30iso4217:USD00014665932022-02-07xbrli:shares00014665932021-12-3100014665932020-12-31iso4217:USDxbrli:shares0001466593ottr:ElectricMember2021-01-012021-12-310001466593ottr:ElectricMember2020-01-012020-12-310001466593ottr:ElectricMember2019-01-012019-12-310001466593ottr:ProductSalesMember2021-01-012021-12-310001466593ottr:ProductSalesMember2020-01-012020-12-310001466593ottr:ProductSalesMember2019-01-012019-12-3100014665932020-01-012020-12-3100014665932019-01-012019-12-310001466593us-gaap:CommonStockMember2018-12-310001466593us-gaap:AdditionalPaidInCapitalMember2018-12-310001466593us-gaap:RetainedEarningsMember2018-12-310001466593us-gaap:AccumulatedOtherComprehensiveIncomeMember2018-12-3100014665932018-12-310001466593us-gaap:CommonStockMember2019-01-012019-12-310001466593us-gaap:AdditionalPaidInCapitalMember2019-01-012019-12-310001466593us-gaap:RetainedEarningsMember2019-01-012019-12-310001466593us-gaap:AccumulatedOtherComprehensiveIncomeMember2019-01-012019-12-310001466593us-gaap:CommonStockMember2019-12-310001466593us-gaap:AdditionalPaidInCapitalMember2019-12-310001466593us-gaap:RetainedEarningsMember2019-12-310001466593us-gaap:AccumulatedOtherComprehensiveIncomeMember2019-12-3100014665932019-12-310001466593us-gaap:CommonStockMember2020-01-012020-12-310001466593us-gaap:AdditionalPaidInCapitalMember2020-01-012020-12-310001466593us-gaap:RetainedEarningsMember2020-01-012020-12-310001466593us-gaap:AccumulatedOtherComprehensiveIncomeMember2020-01-012020-12-310001466593us-gaap:CommonStockMember2020-12-310001466593us-gaap:AdditionalPaidInCapitalMember2020-12-310001466593us-gaap:RetainedEarningsMember2020-12-310001466593us-gaap:AccumulatedOtherComprehensiveIncomeMember2020-12-310001466593us-gaap:CommonStockMember2021-01-012021-12-310001466593us-gaap:AdditionalPaidInCapitalMember2021-01-012021-12-310001466593us-gaap:RetainedEarningsMember2021-01-012021-12-310001466593us-gaap:AccumulatedOtherComprehensiveIncomeMember2021-01-012021-12-310001466593us-gaap:CommonStockMember2021-12-310001466593us-gaap:AdditionalPaidInCapitalMember2021-12-310001466593us-gaap:RetainedEarningsMember2021-12-310001466593us-gaap:AccumulatedOtherComprehensiveIncomeMember2021-12-31ottr:segment0001466593ottr:ElectricPlantMember2021-01-012021-12-310001466593ottr:ElectricPlantMember2020-01-012020-12-310001466593ottr:ElectricPlantMember2019-01-012019-12-310001466593srt:MinimumMemberottr:ElectricPlantMemberus-gaap:EquipmentMember2021-01-012021-12-310001466593ottr:ElectricPlantMembersrt:MaximumMemberus-gaap:EquipmentMember2021-01-012021-12-310001466593srt:MinimumMemberus-gaap:EquipmentMemberottr:NonelectricPlantMember2021-01-012021-12-310001466593srt:MaximumMemberus-gaap:EquipmentMemberottr:NonelectricPlantMember2021-01-012021-12-310001466593srt:MinimumMemberottr:BuildingAndLeaseholdImprovementsMemberottr:NonelectricPlantMember2021-01-012021-12-310001466593ottr:BuildingAndLeaseholdImprovementsMembersrt:MaximumMemberottr:NonelectricPlantMember2021-01-012021-12-31ottr:plantottr:unit0001466593srt:MinimumMember2021-01-012021-12-310001466593srt:MaximumMember2021-01-012021-12-310001466593srt:MinimumMember2021-12-310001466593srt:MaximumMember2021-12-310001466593ottr:OtterTailPowerCompanyMemberottr:CoyoteCreekMiningCompanyLLCCCMCMemberottr:LigniteSalesAgreementMember2021-12-310001466593ottr:OtterTailPowerCompanyMemberottr:CoyoteCreekMiningCompanyLLCCCMCMemberottr:LigniteSalesAgreementMember2021-01-012021-12-31xbrli:pure0001466593us-gaap:OperatingSegmentsMemberottr:ElectricMember2021-01-012021-12-310001466593us-gaap:OperatingSegmentsMemberottr:ElectricMember2020-01-012020-12-310001466593us-gaap:OperatingSegmentsMemberottr:ElectricMember2019-01-012019-12-310001466593us-gaap:OperatingSegmentsMemberottr:ManufacturingMember2021-01-012021-12-310001466593us-gaap:OperatingSegmentsMemberottr:ManufacturingMember2020-01-012020-12-310001466593us-gaap:OperatingSegmentsMemberottr:ManufacturingMember2019-01-012019-12-310001466593us-gaap:OperatingSegmentsMemberottr:PlasticsMember2021-01-012021-12-310001466593us-gaap:OperatingSegmentsMemberottr:PlasticsMember2020-01-012020-12-310001466593us-gaap:OperatingSegmentsMemberottr:PlasticsMember2019-01-012019-12-310001466593us-gaap:CorporateNonSegmentMember2021-01-012021-12-310001466593us-gaap:CorporateNonSegmentMember2020-01-012020-12-310001466593us-gaap:CorporateNonSegmentMember2019-01-012019-12-310001466593us-gaap:OperatingSegmentsMemberottr:ElectricMember2021-12-310001466593us-gaap:OperatingSegmentsMemberottr:ElectricMember2020-12-310001466593us-gaap:OperatingSegmentsMemberottr:ManufacturingMember2021-12-310001466593us-gaap:OperatingSegmentsMemberottr:ManufacturingMember2020-12-310001466593us-gaap:OperatingSegmentsMemberottr:PlasticsMember2021-12-310001466593us-gaap:OperatingSegmentsMemberottr:PlasticsMember2020-12-310001466593us-gaap:CorporateNonSegmentMember2021-12-310001466593us-gaap:CorporateNonSegmentMember2020-12-310001466593ottr:ElectricMemberottr:RetailResidentialMember2021-01-012021-12-310001466593ottr:ElectricMemberottr:RetailResidentialMember2020-01-012020-12-310001466593ottr:ElectricMemberottr:RetailResidentialMember2019-01-012019-12-310001466593ottr:RetailCommercialAndIndustrialMemberottr:ElectricMember2021-01-012021-12-310001466593ottr:RetailCommercialAndIndustrialMemberottr:ElectricMember2020-01-012020-12-310001466593ottr:RetailCommercialAndIndustrialMemberottr:ElectricMember2019-01-012019-12-310001466593ottr:ElectricMemberottr:RetailOtherMember2021-01-012021-12-310001466593ottr:ElectricMemberottr:RetailOtherMember2020-01-012020-12-310001466593ottr:ElectricMemberottr:RetailOtherMember2019-01-012019-12-310001466593ottr:ElectronicProductRetailMemberottr:ElectricMember2021-01-012021-12-310001466593ottr:ElectronicProductRetailMemberottr:ElectricMember2020-01-012020-12-310001466593ottr:ElectronicProductRetailMemberottr:ElectricMember2019-01-012019-12-310001466593ottr:ElectricMemberus-gaap:ElectricTransmissionMember2021-01-012021-12-310001466593ottr:ElectricMemberus-gaap:ElectricTransmissionMember2020-01-012020-12-310001466593ottr:ElectricMemberus-gaap:ElectricTransmissionMember2019-01-012019-12-310001466593ottr:WholesaleMemberottr:ElectricMember2021-01-012021-12-310001466593ottr:WholesaleMemberottr:ElectricMember2020-01-012020-12-310001466593ottr:WholesaleMemberottr:ElectricMember2019-01-012019-12-310001466593ottr:ElectricMemberottr:ElectricProductOtherMember2021-01-012021-12-310001466593ottr:ElectricMemberottr:ElectricProductOtherMember2020-01-012020-12-310001466593ottr:ElectricMemberottr:ElectricProductOtherMember2019-01-012019-12-310001466593ottr:ElectricMember2021-01-012021-12-310001466593ottr:ElectricMember2020-01-012020-12-310001466593ottr:ElectricMember2019-01-012019-12-310001466593ottr:ManufacturingMemberottr:MetalPartsAndToolingMember2021-01-012021-12-310001466593ottr:ManufacturingMemberottr:MetalPartsAndToolingMember2020-01-012020-12-310001466593ottr:ManufacturingMemberottr:MetalPartsAndToolingMember2019-01-012019-12-310001466593ottr:ManufacturingMemberottr:PlasticProductsMember2021-01-012021-12-310001466593ottr:ManufacturingMemberottr:PlasticProductsMember2020-01-012020-12-310001466593ottr:ManufacturingMemberottr:PlasticProductsMember2019-01-012019-12-310001466593ottr:ManufacturingMemberus-gaap:ManufacturedProductOtherMember2021-01-012021-12-310001466593ottr:ManufacturingMemberus-gaap:ManufacturedProductOtherMember2020-01-012020-12-310001466593ottr:ManufacturingMemberus-gaap:ManufacturedProductOtherMember2019-01-012019-12-310001466593ottr:ManufacturingMember2021-01-012021-12-310001466593ottr:ManufacturingMember2020-01-012020-12-310001466593ottr:ManufacturingMember2019-01-012019-12-310001466593ottr:PlasticsMember2021-01-012021-12-310001466593ottr:PlasticsMember2020-01-012020-12-310001466593ottr:PlasticsMember2019-01-012019-12-310001466593ottr:PensionAndOtherPostretirementBenefitPlansMember2021-12-310001466593ottr:PensionAndOtherPostretirementBenefitPlansMember2020-12-310001466593ottr:AlternativeRevenueProgramRidersMember2021-01-012021-12-310001466593ottr:AlternativeRevenueProgramRidersMember2021-12-310001466593ottr:AlternativeRevenueProgramRidersMember2020-12-310001466593ottr:AssetRetirementObligationsMember2021-12-310001466593ottr:AssetRetirementObligationsMember2020-12-310001466593ottr:ISOCostRecoveryTrackersMember2021-01-012021-12-310001466593ottr:ISOCostRecoveryTrackersMember2021-12-310001466593ottr:ISOCostRecoveryTrackersMember2020-12-310001466593ottr:UnrecoveredProjectCostsMember2021-01-012021-12-310001466593ottr:UnrecoveredProjectCostsMember2021-12-310001466593ottr:UnrecoveredProjectCostsMember2020-12-310001466593ottr:DeferredRateCaseExpensesMember2021-12-310001466593ottr:DeferredRateCaseExpensesMember2020-12-310001466593ottr:DebtReacquisitionPremiumsMember2021-01-012021-12-310001466593ottr:DebtReacquisitionPremiumsMember2021-12-310001466593ottr:DebtReacquisitionPremiumsMember2020-12-310001466593ottr:FuelClauseAdjustmentsMember2021-01-012021-12-310001466593ottr:FuelClauseAdjustmentsMember2021-12-310001466593ottr:FuelClauseAdjustmentsMember2020-12-310001466593ottr:OtherRegulatoryAssetsMember2021-12-310001466593ottr:OtherRegulatoryAssetsMember2020-12-310001466593ottr:DeferredIncomeTaxesMember2021-12-310001466593ottr:DeferredIncomeTaxesMember2020-12-310001466593ottr:PlantRemovalObligationsMember2021-12-310001466593ottr:PlantRemovalObligationsMember2020-12-310001466593ottr:FuelClauseAdjustmentMember2021-01-012021-12-310001466593ottr:FuelClauseAdjustmentMember2021-12-310001466593ottr:FuelClauseAdjustmentMember2020-12-310001466593ottr:AlternativeRevenueProgramRidersMember2021-12-310001466593ottr:AlternativeRevenueProgramRidersMember2020-12-310001466593ottr:PensionAndOtherPostretirementBenefitPlansMember2021-01-012021-12-310001466593ottr:PensionAndOtherPostretirementBenefitPlansMember2021-12-310001466593ottr:PensionAndOtherPostretirementBenefitPlansMember2020-12-310001466593ottr:DerivativeLiabilitiesMember2021-01-012021-12-310001466593ottr:DerivativeLiabilitiesMember2021-12-310001466593ottr:DerivativeLiabilitiesMember2020-12-310001466593ottr:OtherRegulatoryLiabilitiesMember2021-12-310001466593ottr:OtherRegulatoryLiabilitiesMember2020-12-310001466593ottr:ElectricPlantMemberus-gaap:ElectricGenerationEquipmentMember2021-12-310001466593ottr:ElectricPlantMemberus-gaap:ElectricGenerationEquipmentMember2020-12-310001466593ottr:TransmissionPlantMemberottr:ElectricPlantMember2021-12-310001466593ottr:TransmissionPlantMemberottr:ElectricPlantMember2020-12-310001466593ottr:ElectricPlantMemberottr:DistributionPlantMember2021-12-310001466593ottr:ElectricPlantMemberottr:DistributionPlantMember2020-12-310001466593ottr:GeneralPlantMemberottr:ElectricPlantMember2021-12-310001466593ottr:GeneralPlantMemberottr:ElectricPlantMember2020-12-310001466593ottr:ElectricPlantMemberottr:ElectricPlantInServiceMember2021-12-310001466593ottr:ElectricPlantMemberottr:ElectricPlantInServiceMember2020-12-310001466593ottr:ElectricPlantMemberus-gaap:ConstructionInProgressMember2021-12-310001466593ottr:ElectricPlantMemberus-gaap:ConstructionInProgressMember2020-12-310001466593ottr:ElectricPlantMember2021-12-310001466593ottr:ElectricPlantMember2020-12-310001466593us-gaap:EquipmentMemberottr:NonelectricPlantMember2021-12-310001466593us-gaap:EquipmentMemberottr:NonelectricPlantMember2020-12-310001466593ottr:BuildingsAndLeaseholdImprovementsMemberottr:NonelectricPlantMember2021-12-310001466593ottr:BuildingsAndLeaseholdImprovementsMemberottr:NonelectricPlantMember2020-12-310001466593us-gaap:LandMemberottr:NonelectricPlantMember2021-12-310001466593us-gaap:LandMemberottr:NonelectricPlantMember2020-12-310001466593ottr:NonelectricOperationsPlantMemberottr:NonelectricPlantMember2021-12-310001466593ottr:NonelectricOperationsPlantMemberottr:NonelectricPlantMember2020-12-310001466593us-gaap:ConstructionInProgressMemberottr:NonelectricPlantMember2021-12-310001466593us-gaap:ConstructionInProgressMemberottr:NonelectricPlantMember2020-12-310001466593ottr:NonelectricPlantMember2021-12-310001466593ottr:NonelectricPlantMember2020-12-310001466593ottr:OtterTailPowerCompanyMemberottr:BigStonePlantMember2021-12-310001466593ottr:BigStonePlantMember2021-12-310001466593ottr:CoyoteStationMemberottr:OtterTailPowerCompanyMember2021-12-310001466593ottr:CoyoteStationMember2021-12-310001466593ottr:BigStoneSouthEllendaleMultiValueProjectMemberottr:OtterTailPowerCompanyMember2021-12-310001466593ottr:BigStoneSouthEllendaleMultiValueProjectMember2021-12-310001466593ottr:OtterTailPowerCompanyMemberottr:FargoProjectMember2021-12-310001466593ottr:FargoProjectMember2021-12-310001466593ottr:BigStoneSouthBrookingsMultiValueProjectMemberottr:OtterTailPowerCompanyMember2021-12-310001466593ottr:BigStoneSouthBrookingsMultiValueProjectMember2021-12-310001466593ottr:BrookingsProjectMemberottr:OtterTailPowerCompanyMember2021-12-310001466593ottr:BrookingsProjectMember2021-12-310001466593ottr:OtterTailPowerCompanyMemberottr:BemidjiProjectMember2021-12-310001466593ottr:BemidjiProjectMember2021-12-310001466593ottr:OtterTailPowerCompanyMemberottr:BigStonePlantMember2020-12-310001466593ottr:BigStonePlantMember2020-12-310001466593ottr:CoyoteStationMemberottr:OtterTailPowerCompanyMember2020-12-310001466593ottr:CoyoteStationMember2020-12-310001466593ottr:BigStoneSouthEllendaleMultiValueProjectMemberottr:OtterTailPowerCompanyMember2020-12-310001466593ottr:BigStoneSouthEllendaleMultiValueProjectMember2020-12-310001466593ottr:OtterTailPowerCompanyMemberottr:FargoProjectMember2020-12-310001466593ottr:FargoProjectMember2020-12-310001466593ottr:BigStoneSouthBrookingsMultiValueProjectMemberottr:OtterTailPowerCompanyMember2020-12-310001466593ottr:BigStoneSouthBrookingsMultiValueProjectMember2020-12-310001466593ottr:BrookingsProjectMemberottr:OtterTailPowerCompanyMember2020-12-310001466593ottr:BrookingsProjectMember2020-12-310001466593ottr:OtterTailPowerCompanyMemberottr:BemidjiProjectMember2020-12-310001466593ottr:BemidjiProjectMember2020-12-310001466593ottr:ManufacturingMember2021-12-310001466593ottr:ManufacturingMember2020-12-310001466593ottr:PlasticsMember2021-12-310001466593ottr:PlasticsMember2020-12-310001466593us-gaap:CustomerRelationshipsMember2021-12-310001466593us-gaap:OtherIntangibleAssetsMember2021-12-310001466593us-gaap:CustomerRelationshipsMember2020-12-310001466593us-gaap:OtherIntangibleAssetsMember2020-12-310001466593srt:ParentCompanyMember2021-12-310001466593ottr:OtterTailPowerCompanyMember2021-12-310001466593srt:ParentCompanyMember2020-12-310001466593ottr:OtterTailPowerCompanyMember2020-12-310001466593ottr:OtterTailCorporationCreditAgreementMember2021-12-310001466593ottr:OtterTailCorporationCreditAgreementMember2020-12-310001466593ottr:OTPCreditAgreementMember2021-12-310001466593ottr:OTPCreditAgreementMember2020-12-310001466593ottr:OtterTailCorporationCreditAgreementMemberus-gaap:RevolvingCreditFacilityMember2021-12-310001466593us-gaap:RevolvingCreditFacilityMemberottr:OTPCreditAgreementMember2021-12-310001466593ottr:OtterTailCorporationCreditAgreementMemberus-gaap:LetterOfCreditMember2021-12-310001466593us-gaap:LetterOfCreditMemberottr:OTPCreditAgreementMember2021-12-310001466593srt:MinimumMemberottr:BenchmarkRateMember2021-01-012021-12-310001466593ottr:BenchmarkRateMembersrt:MaximumMember2021-01-012021-12-310001466593ottr:The355GuaranteedSeniorNotesDueDecember152026Member2021-12-310001466593ottr:The355GuaranteedSeniorNotesDueDecember152026Member2020-12-310001466593ottr:SeniorUnsecuredNotes463SeriesADueDecember12021Member2021-12-310001466593ottr:SeniorUnsecuredNotes463SeriesADueDecember12021Member2020-12-310001466593ottr:SeniorUnsecuredNotes615SeriesBDueAugust202022Member2021-12-310001466593ottr:SeniorUnsecuredNotes615SeriesBDueAugust202022Member2020-12-310001466593ottr:SeniorUnsecuredNotes637SeriesCDueAugust202027Member2021-12-310001466593ottr:SeniorUnsecuredNotes637SeriesCDueAugust202027Member2020-12-310001466593ottr:SeniorUnsecuredNotes468SeriesADueFebruary272029Member2021-12-310001466593ottr:SeniorUnsecuredNotes468SeriesADueFebruary272029Member2020-12-310001466593ottr:SeniorUnsecuredNotes307SeriesADueOctober102029Member2021-12-310001466593ottr:SeniorUnsecuredNotes307SeriesADueOctober102029Member2020-12-310001466593ottr:SeniorUnsecuredNotes307SeriesADueFebruary252030Member2021-12-310001466593ottr:SeniorUnsecuredNotes307SeriesADueFebruary252030Member2020-12-310001466593ottr:SeniorUnsecuredNotes322SeriesBDueAugust202030Member2021-12-310001466593ottr:SeniorUnsecuredNotes322SeriesBDueAugust202030Member2020-12-310001466593ottr:SeniorUnsecuredNotes274SeriesADueNovember292031Member2021-12-310001466593ottr:SeniorUnsecuredNotes274SeriesADueNovember292031Member2020-12-310001466593ottr:SeniorUnsecuredNotes647SeriesDDueAugust202037Member2021-12-310001466593ottr:SeniorUnsecuredNotes647SeriesDDueAugust202037Member2020-12-310001466593ottr:SeniorUnsecuredNotes352SeriesBDueOctober102039Member2021-12-310001466593ottr:SeniorUnsecuredNotes352SeriesBDueOctober102039Member2020-12-310001466593ottr:SeniorUnsecuredNotes362SeriesCDueFebruary252040Member2021-12-310001466593ottr:SeniorUnsecuredNotes362SeriesCDueFebruary252040Member2020-12-310001466593ottr:SeniorUnsecuredNotes547SeriesBDueFebruary272044Member2021-12-310001466593ottr:SeniorUnsecuredNotes547SeriesBDueFebruary272044Member2020-12-310001466593ottr:SeniorUnsecuredNotes407SeriesADueFebruary72048Member2021-12-310001466593ottr:SeniorUnsecuredNotes407SeriesADueFebruary72048Member2020-12-310001466593ottr:SeniorUnsecuredNotes382SeriesCDueOctober102049Member2021-12-310001466593ottr:SeniorUnsecuredNotes382SeriesCDueOctober102049Member2020-12-310001466593ottr:SeniorUnsecuredNotes392SeriesDDueFebruary252050Member2021-12-310001466593ottr:SeniorUnsecuredNotes392SeriesDDueFebruary252050Member2020-12-310001466593ottr:SeniorUnsecuredNotes369SeriesBDueNovember292051Member2021-12-310001466593ottr:SeniorUnsecuredNotes369SeriesBDueNovember292051Member2020-12-310001466593ottr:PartnershipInAssistingCommunityExpansionPaceNote254DueMarch182021Member2021-12-310001466593ottr:PartnershipInAssistingCommunityExpansionPaceNote254DueMarch182021Member2020-12-310001466593us-gaap:SeniorNotesMember2021-06-100001466593us-gaap:SeniorNotesMemberottr:SeniorUnsecuredNotes274SeriesADueNovember292031Member2021-06-100001466593us-gaap:SeniorNotesMemberottr:SeniorUnsecuredNotes369SeriesBDueNovember292051Member2021-06-100001466593us-gaap:SeniorNotesMemberottr:SeniorUnsecuredNotes377SeriesADueMay202052Member2021-06-100001466593us-gaap:SeniorNotesMember2021-01-012021-12-310001466593us-gaap:PensionPlansDefinedBenefitMember2021-01-012021-12-31ottr:year0001466593us-gaap:OtherPostretirementBenefitPlansDefinedBenefitMember2021-01-012021-12-310001466593ottr:DefinedBenefitPlanReturnEnhancementMembersrt:MinimumMemberus-gaap:PensionPlansDefinedBenefitMemberottr:PermittedRange20To60PercentMember2021-12-310001466593ottr:DefinedBenefitPlanReturnEnhancementMemberus-gaap:PensionPlansDefinedBenefitMemberottr:PermittedRange20To60PercentMembersrt:MaximumMember2021-12-310001466593ottr:DefinedBenefitPlanReturnEnhancementMemberus-gaap:PensionPlansDefinedBenefitMember2021-12-310001466593ottr:DefinedBenefitPlanReturnEnhancementMemberus-gaap:PensionPlansDefinedBenefitMember2020-12-310001466593srt:MinimumMemberus-gaap:PensionPlansDefinedBenefitMemberottr:DefinedBenefitPlanRiskManagementMemberottr:PermittedRange40To80PercentMember2021-12-310001466593us-gaap:PensionPlansDefinedBenefitMemberottr:DefinedBenefitPlanRiskManagementMembersrt:MaximumMemberottr:PermittedRange40To80PercentMember2021-12-310001466593us-gaap:PensionPlansDefinedBenefitMemberottr:DefinedBenefitPlanRiskManagementMember2021-12-310001466593us-gaap:PensionPlansDefinedBenefitMemberottr:DefinedBenefitPlanRiskManagementMember2020-12-310001466593srt:MinimumMemberus-gaap:PensionPlansDefinedBenefitMemberottr:DefinedBenefitPlanAlternativesMemberottr:PermittedRange0To20PercentMember2021-12-310001466593us-gaap:PensionPlansDefinedBenefitMemberottr:DefinedBenefitPlanAlternativesMemberottr:PermittedRange0To20PercentMembersrt:MaximumMember2021-12-310001466593us-gaap:PensionPlansDefinedBenefitMemberottr:DefinedBenefitPlanAlternativesMember2021-12-310001466593us-gaap:PensionPlansDefinedBenefitMemberottr:DefinedBenefitPlanAlternativesMember2020-12-310001466593us-gaap:PensionPlansDefinedBenefitMember2021-12-310001466593us-gaap:PensionPlansDefinedBenefitMember2020-12-310001466593us-gaap:DefinedBenefitPlanEquitySecuritiesMemberus-gaap:FairValueInputsLevel1Member2021-12-310001466593us-gaap:DefinedBenefitPlanEquitySecuritiesMemberus-gaap:FairValueInputsLevel2Member2021-12-310001466593us-gaap:DefinedBenefitPlanEquitySecuritiesMemberus-gaap:FairValueInputsLevel3Member2021-12-310001466593us-gaap:DefinedBenefitPlanEquitySecuritiesMember2021-12-310001466593us-gaap:FairValueInputsLevel1Memberus-gaap:FixedIncomeFundsMember2021-12-310001466593us-gaap:FixedIncomeFundsMemberus-gaap:FairValueInputsLevel2Member2021-12-310001466593us-gaap:FairValueInputsLevel3Memberus-gaap:FixedIncomeFundsMember2021-12-310001466593us-gaap:FixedIncomeFundsMember2021-12-310001466593us-gaap:FairValueInputsLevel1Memberottr:DefinedBenefitPlanHybridFundsMember2021-12-310001466593ottr:DefinedBenefitPlanHybridFundsMemberus-gaap:FairValueInputsLevel2Member2021-12-310001466593us-gaap:FairValueInputsLevel3Memberottr:DefinedBenefitPlanHybridFundsMember2021-12-310001466593ottr:DefinedBenefitPlanHybridFundsMember2021-12-310001466593us-gaap:USTreasuryAndGovernmentMemberus-gaap:FairValueInputsLevel1Member2021-12-310001466593us-gaap:USTreasuryAndGovernmentMemberus-gaap:FairValueInputsLevel2Member2021-12-310001466593us-gaap:USTreasuryAndGovernmentMemberus-gaap:FairValueInputsLevel3Member2021-12-310001466593us-gaap:USTreasuryAndGovernmentMember2021-12-310001466593ottr:DefinedBenefitPlanOtherSEIEnergyDebtCollectiveFundMemberus-gaap:FairValueInputsLevel1Member2021-12-310001466593ottr:DefinedBenefitPlanOtherSEIEnergyDebtCollectiveFundMemberus-gaap:FairValueInputsLevel2Member2021-12-310001466593us-gaap:FairValueInputsLevel3Memberottr:DefinedBenefitPlanOtherSEIEnergyDebtCollectiveFundMember2021-12-310001466593us-gaap:FairValueMeasuredAtNetAssetValuePerShareMemberottr:DefinedBenefitPlanOtherSEIEnergyDebtCollectiveFundMember2021-12-310001466593ottr:DefinedBenefitPlanOtherSEIEnergyDebtCollectiveFundMember2021-12-310001466593us-gaap:FairValueInputsLevel1Member2021-12-310001466593us-gaap:FairValueInputsLevel2Member2021-12-310001466593us-gaap:FairValueInputsLevel3Member2021-12-310001466593us-gaap:FairValueMeasuredAtNetAssetValuePerShareMember2021-12-310001466593us-gaap:FairValueInputsLevel1Memberus-gaap:DefinedBenefitPlanCashAndCashEquivalentsMember2020-12-310001466593us-gaap:FairValueInputsLevel2Memberus-gaap:DefinedBenefitPlanCashAndCashEquivalentsMember2020-12-310001466593us-gaap:FairValueInputsLevel3Memberus-gaap:DefinedBenefitPlanCashAndCashEquivalentsMember2020-12-310001466593us-gaap:DefinedBenefitPlanCashAndCashEquivalentsMember2020-12-310001466593us-gaap:DefinedBenefitPlanEquitySecuritiesMemberus-gaap:FairValueInputsLevel1Member2020-12-310001466593us-gaap:DefinedBenefitPlanEquitySecuritiesMemberus-gaap:FairValueInputsLevel2Member2020-12-310001466593us-gaap:DefinedBenefitPlanEquitySecuritiesMemberus-gaap:FairValueInputsLevel3Member2020-12-310001466593us-gaap:DefinedBenefitPlanEquitySecuritiesMember2020-12-310001466593us-gaap:FairValueInputsLevel1Memberus-gaap:FixedIncomeFundsMember2020-12-310001466593us-gaap:FixedIncomeFundsMemberus-gaap:FairValueInputsLevel2Member2020-12-310001466593us-gaap:FairValueInputsLevel3Memberus-gaap:FixedIncomeFundsMember2020-12-310001466593us-gaap:FixedIncomeFundsMember2020-12-310001466593us-gaap:FairValueInputsLevel1Memberottr:DefinedBenefitPlanHybridFundsMember2020-12-310001466593ottr:DefinedBenefitPlanHybridFundsMemberus-gaap:FairValueInputsLevel2Member2020-12-310001466593us-gaap:FairValueInputsLevel3Memberottr:DefinedBenefitPlanHybridFundsMember2020-12-310001466593ottr:DefinedBenefitPlanHybridFundsMember2020-12-310001466593ottr:DefinedBenefitPlanOtherSEIEnergyDebtCollectiveFundMemberus-gaap:FairValueInputsLevel1Member2020-12-310001466593ottr:DefinedBenefitPlanOtherSEIEnergyDebtCollectiveFundMemberus-gaap:FairValueInputsLevel2Member2020-12-310001466593us-gaap:FairValueInputsLevel3Memberottr:DefinedBenefitPlanOtherSEIEnergyDebtCollectiveFundMember2020-12-310001466593us-gaap:FairValueMeasuredAtNetAssetValuePerShareMemberottr:DefinedBenefitPlanOtherSEIEnergyDebtCollectiveFundMember2020-12-310001466593ottr:DefinedBenefitPlanOtherSEIEnergyDebtCollectiveFundMember2020-12-310001466593us-gaap:FairValueInputsLevel1Member2020-12-310001466593us-gaap:FairValueInputsLevel2Member2020-12-310001466593us-gaap:FairValueInputsLevel3Member2020-12-310001466593us-gaap:FairValueMeasuredAtNetAssetValuePerShareMember2020-12-310001466593us-gaap:PensionPlansDefinedBenefitMember2019-12-310001466593ottr:ExecutiveSurvivorAndSupplementalRetirementPlanMember2020-12-310001466593ottr:ExecutiveSurvivorAndSupplementalRetirementPlanMember2019-12-310001466593us-gaap:OtherPostretirementBenefitPlansDefinedBenefitMember2020-12-310001466593us-gaap:OtherPostretirementBenefitPlansDefinedBenefitMember2019-12-310001466593us-gaap:PensionPlansDefinedBenefitMember2020-01-012020-12-310001466593ottr:ExecutiveSurvivorAndSupplementalRetirementPlanMember2021-01-012021-12-310001466593ottr:ExecutiveSurvivorAndSupplementalRetirementPlanMember2020-01-012020-12-310001466593us-gaap:OtherPostretirementBenefitPlansDefinedBenefitMember2020-01-012020-12-310001466593ottr:ExecutiveSurvivorAndSupplementalRetirementPlanMember2021-12-310001466593us-gaap:OtherPostretirementBenefitPlansDefinedBenefitMember2021-12-310001466593us-gaap:PensionPlansDefinedBenefitMemberottr:ParticipantsToAge39Member2021-12-310001466593us-gaap:PensionPlansDefinedBenefitMemberottr:ParticipantsToAge39Member2020-12-310001466593us-gaap:PensionPlansDefinedBenefitMemberottr:ParticipantsAge40To49Member2021-12-310001466593us-gaap:PensionPlansDefinedBenefitMemberottr:ParticipantsAge40To49Member2020-12-310001466593us-gaap:PensionPlansDefinedBenefitMemberottr:ParticipantsAge50AndOlderMember2021-12-310001466593us-gaap:PensionPlansDefinedBenefitMemberottr:ParticipantsAge50AndOlderMember2020-12-310001466593us-gaap:PensionPlansDefinedBenefitMember2019-01-012019-12-310001466593ottr:ExecutiveSurvivorAndSupplementalRetirementPlanMember2019-01-012019-12-310001466593us-gaap:OtherPostretirementBenefitPlansDefinedBenefitMember2019-01-012019-12-310001466593us-gaap:PensionPlansDefinedBenefitMemberottr:ParticipantsToAge39Member2021-01-012021-12-310001466593us-gaap:PensionPlansDefinedBenefitMemberottr:ParticipantsToAge39Member2020-01-012020-12-310001466593us-gaap:PensionPlansDefinedBenefitMemberottr:ParticipantsToAge39Member2019-01-012019-12-310001466593us-gaap:PensionPlansDefinedBenefitMemberottr:ParticipantsAge40To49Member2021-01-012021-12-310001466593us-gaap:PensionPlansDefinedBenefitMemberottr:ParticipantsAge40To49Member2020-01-012020-12-310001466593us-gaap:PensionPlansDefinedBenefitMemberottr:ParticipantsAge40To49Member2019-01-012019-12-310001466593us-gaap:PensionPlansDefinedBenefitMemberottr:ParticipantsAge50AndOlderMember2021-01-012021-12-310001466593us-gaap:PensionPlansDefinedBenefitMemberottr:ParticipantsAge50AndOlderMember2020-01-012020-12-310001466593us-gaap:PensionPlansDefinedBenefitMemberottr:ParticipantsAge50AndOlderMember2019-01-012019-12-310001466593us-gaap:SubsequentEventMember2022-02-012022-02-280001466593us-gaap:DomesticCountryMember2021-12-310001466593us-gaap:DomesticCountryMemberottr:TaxYears2022To2032Member2021-12-310001466593us-gaap:DomesticCountryMemberottr:TaxYears2033To2038Member2021-12-310001466593us-gaap:DomesticCountryMemberottr:TaxYears2039To2043Member2021-12-310001466593us-gaap:StateAndLocalJurisdictionMember2021-12-310001466593us-gaap:StateAndLocalJurisdictionMemberottr:TaxYears2022To2032Member2021-12-310001466593ottr:TaxYears2033To2038Memberus-gaap:StateAndLocalJurisdictionMember2021-12-310001466593us-gaap:StateAndLocalJurisdictionMemberottr:TaxYears2039To2043Member2021-12-310001466593ottr:OtterTailPowerCompanyMemberottr:ConstructionProgramsMember2021-01-012021-12-310001466593ottr:OtterTailPowerCompanyMemberottr:ConstructionProgramsMember2020-01-012020-12-310001466593ottr:OtterTailPowerCompanyMemberottr:ConstructionProgramsMember2019-01-012019-12-310001466593ottr:OtterTailPowerCompanyMemberottr:OTPLandEasementsMember2021-01-012021-12-310001466593ottr:ConstructionProgramAndOtherCommitmentsMembersrt:SubsidiariesMember2021-12-310001466593ottr:CapacityAndEnergyRequirementsMemberottr:OtterTailPowerCompanyMember2021-12-310001466593ottr:CoalPurchaseCommitmentsMemberottr:OtterTailPowerCompanyMember2021-12-310001466593ottr:OtterTailPowerCompanyMember2021-12-310001466593ottr:OtterTailPowerCompanyMemberottr:FederalEnergyRegulatoryCommissionMember2020-12-310001466593ottr:WestmorelandArbitrationMemberus-gaap:PendingLitigationMember2021-01-012021-12-310001466593us-gaap:CumulativePreferredStockMember2021-12-310001466593ottr:CumulativePreferenceSharesMember2021-12-310001466593us-gaap:CumulativePreferredStockMember2020-12-310001466593ottr:SecondShelfRegistrationMember2021-05-032021-05-030001466593ottr:SecondShelfRegistrationMember2021-01-012021-12-310001466593ottr:SecondShelfRegistrationMember2021-12-310001466593srt:MinimumMemberottr:OtterTailPowerCompanyMemberottr:MinnesotaPublicUtilitiesCommissionMember2020-07-152020-07-150001466593ottr:OtterTailPowerCompanyMemberottr:MinnesotaPublicUtilitiesCommissionMembersrt:MaximumMember2020-07-152020-07-150001466593ottr:OtterTailPowerCompanyMember2021-01-012021-12-310001466593ottr:OtterTailPowerCompanyMembersrt:MaximumMember2021-12-310001466593srt:MinimumMemberottr:OtterTailPowerCompanyMemberus-gaap:SubsequentEventMemberottr:MinnesotaPublicUtilitiesCommissionMember2022-01-262022-01-260001466593ottr:OtterTailPowerCompanyMemberus-gaap:SubsequentEventMemberottr:MinnesotaPublicUtilitiesCommissionMembersrt:MaximumMember2022-01-262022-01-260001466593ottr:OtterTailPowerCompanyMemberus-gaap:SubsequentEventMembersrt:MaximumMember2022-01-260001466593us-gaap:AccumulatedDefinedBenefitPlansAdjustmentMember2018-12-310001466593us-gaap:AccumulatedNetUnrealizedInvestmentGainLossMember2018-12-310001466593us-gaap:AccumulatedDefinedBenefitPlansAdjustmentMember2019-01-012019-12-310001466593us-gaap:AccumulatedNetUnrealizedInvestmentGainLossMember2019-01-012019-12-310001466593us-gaap:AccumulatedDefinedBenefitPlansAdjustmentMember2019-12-310001466593us-gaap:AccumulatedNetUnrealizedInvestmentGainLossMember2019-12-310001466593us-gaap:AccumulatedDefinedBenefitPlansAdjustmentMember2020-01-012020-12-310001466593us-gaap:AccumulatedNetUnrealizedInvestmentGainLossMember2020-01-012020-12-310001466593us-gaap:AccumulatedDefinedBenefitPlansAdjustmentMember2020-12-310001466593us-gaap:AccumulatedNetUnrealizedInvestmentGainLossMember2020-12-310001466593us-gaap:AccumulatedDefinedBenefitPlansAdjustmentMember2021-01-012021-12-310001466593us-gaap:AccumulatedNetUnrealizedInvestmentGainLossMember2021-01-012021-12-310001466593us-gaap:AccumulatedDefinedBenefitPlansAdjustmentMember2021-12-310001466593us-gaap:AccumulatedNetUnrealizedInvestmentGainLossMember2021-12-310001466593ottr:The1999EmployeeStockPurchasePlanMember2021-12-310001466593ottr:The1999EmployeeStockPurchasePlanMember2021-01-012021-12-310001466593srt:MinimumMemberottr:The1999EmployeeStockPurchasePlanMember2021-01-012021-12-310001466593ottr:The1999EmployeeStockPurchasePlanMembersrt:MaximumMember2021-01-012021-12-310001466593ottr:The1999EmployeeStockPurchasePlanMember2018-01-012019-06-300001466593ottr:The1999EmployeeStockPurchasePlanMember2019-07-012021-12-310001466593ottr:The1999EmployeeStockPurchasePlanMember2020-01-012020-12-310001466593ottr:The1999EmployeeStockPurchasePlanMember2019-01-012019-12-310001466593ottr:The2014StockIncentivePlanMember2021-12-310001466593ottr:The2014StockIncentivePlanMember2021-01-012021-12-310001466593ottr:The2014StockIncentivePlanMember2020-01-012020-12-310001466593ottr:The2014StockIncentivePlanMember2019-01-012019-12-310001466593us-gaap:RestrictedStockMembersrt:MinimumMember2021-01-012021-12-310001466593us-gaap:RestrictedStockMembersrt:MaximumMember2021-01-012021-12-310001466593us-gaap:RestrictedStockMember2021-01-012021-12-310001466593us-gaap:RestrictedStockMember2020-12-310001466593us-gaap:RestrictedStockMember2021-12-310001466593us-gaap:RestrictedStockMember2020-01-012020-12-310001466593us-gaap:RestrictedStockMember2019-01-012019-12-310001466593us-gaap:PerformanceSharesMember2021-01-012021-12-310001466593srt:MinimumMemberus-gaap:PerformanceSharesMember2021-01-012021-12-310001466593srt:MaximumMemberus-gaap:PerformanceSharesMember2021-01-012021-12-310001466593us-gaap:PerformanceSharesMember2021-12-312021-12-310001466593us-gaap:PerformanceSharesMember2020-12-312020-12-310001466593us-gaap:PerformanceSharesMember2019-12-312019-12-310001466593us-gaap:PerformanceSharesMember2020-12-310001466593us-gaap:PerformanceSharesMember2021-12-310001466593us-gaap:PerformanceSharesMember2020-01-012020-12-310001466593us-gaap:PerformanceSharesMember2019-01-012019-12-310001466593us-gaap:EmployeeStockOptionMember2021-01-012021-12-310001466593us-gaap:EmployeeStockOptionMember2020-01-012020-12-310001466593us-gaap:EmployeeStockOptionMember2019-01-012019-12-310001466593us-gaap:SwapMember2021-12-312021-12-31utr:MWh0001466593us-gaap:SwapMember2021-12-310001466593us-gaap:SwapMember2021-01-012021-12-310001466593us-gaap:FairValueMeasurementsRecurringMemberus-gaap:FairValueInputsLevel1Member2021-12-310001466593us-gaap:FairValueMeasurementsRecurringMemberus-gaap:FairValueInputsLevel2Member2021-12-310001466593us-gaap:FairValueMeasurementsRecurringMemberus-gaap:FairValueInputsLevel3Member2021-12-310001466593us-gaap:FairValueMeasurementsRecurringMemberus-gaap:CorporateDebtSecuritiesMemberus-gaap:FairValueInputsLevel1Member2021-12-310001466593us-gaap:FairValueMeasurementsRecurringMemberus-gaap:CorporateDebtSecuritiesMemberus-gaap:FairValueInputsLevel2Member2021-12-310001466593us-gaap:FairValueMeasurementsRecurringMemberus-gaap:CorporateDebtSecuritiesMemberus-gaap:FairValueInputsLevel3Member2021-12-310001466593us-gaap:FairValueMeasurementsRecurringMemberus-gaap:FairValueInputsLevel1Memberottr:GovernmentBackedAndGovernmentSponsoredEnterprisesDebtSecuritiesMember2021-12-310001466593us-gaap:FairValueMeasurementsRecurringMemberottr:GovernmentBackedAndGovernmentSponsoredEnterprisesDebtSecuritiesMemberus-gaap:FairValueInputsLevel2Member2021-12-310001466593us-gaap:FairValueMeasurementsRecurringMemberus-gaap:FairValueInputsLevel3Memberottr:GovernmentBackedAndGovernmentSponsoredEnterprisesDebtSecuritiesMember2021-12-310001466593us-gaap:FairValueMeasurementsRecurringMemberus-gaap:FairValueInputsLevel1Member2020-12-310001466593us-gaap:FairValueMeasurementsRecurringMemberus-gaap:FairValueInputsLevel2Member2020-12-310001466593us-gaap:FairValueMeasurementsRecurringMemberus-gaap:FairValueInputsLevel3Member2020-12-310001466593us-gaap:FairValueMeasurementsRecurringMemberus-gaap:CorporateDebtSecuritiesMemberus-gaap:FairValueInputsLevel1Member2020-12-310001466593us-gaap:FairValueMeasurementsRecurringMemberus-gaap:CorporateDebtSecuritiesMemberus-gaap:FairValueInputsLevel2Member2020-12-310001466593us-gaap:FairValueMeasurementsRecurringMemberus-gaap:CorporateDebtSecuritiesMemberus-gaap:FairValueInputsLevel3Member2020-12-310001466593us-gaap:FairValueMeasurementsRecurringMemberus-gaap:FairValueInputsLevel1Memberottr:GovernmentBackedAndGovernmentSponsoredEnterprisesDebtSecuritiesMember2020-12-310001466593us-gaap:FairValueMeasurementsRecurringMemberottr:GovernmentBackedAndGovernmentSponsoredEnterprisesDebtSecuritiesMemberus-gaap:FairValueInputsLevel2Member2020-12-310001466593us-gaap:FairValueMeasurementsRecurringMemberus-gaap:FairValueInputsLevel3Memberottr:GovernmentBackedAndGovernmentSponsoredEnterprisesDebtSecuritiesMember2020-12-310001466593us-gaap:CarryingReportedAmountFairValueDisclosureMember2021-12-310001466593us-gaap:EstimateOfFairValueFairValueDisclosureMember2021-12-310001466593us-gaap:CarryingReportedAmountFairValueDisclosureMember2020-12-310001466593us-gaap:EstimateOfFairValueFairValueDisclosureMember2020-12-310001466593srt:ParentCompanyMember2021-01-012021-12-310001466593srt:ParentCompanyMember2020-01-012020-12-310001466593srt:ParentCompanyMember2019-01-012019-12-310001466593srt:ParentCompanyMember2019-12-310001466593srt:ParentCompanyMember2018-12-310001466593ottr:OtterTailPowerCompanyMemberottr:OtterTailCorporationMember2021-12-310001466593ottr:NorthernPipeProductsIncMemberottr:OtterTailCorporationMember2021-12-310001466593ottr:VinyltechCorporationMemberottr:OtterTailCorporationMember2021-12-310001466593ottr:BTDManufacturingIncMemberottr:OtterTailCorporationMember2021-12-310001466593ottr:TOPlasticsIncMemberottr:OtterTailCorporationMember2021-12-310001466593ottr:VaristarCorporationMemberottr:OtterTailCorporationMember2021-12-310001466593ottr:OtterTailAssuranceLimitedMemberottr:OtterTailCorporationMember2021-12-310001466593ottr:OtterTailCorporationMember2021-12-310001466593ottr:OtterTailPowerCompanyMemberottr:OtterTailCorporationMember2020-12-310001466593ottr:NorthernPipeProductsIncMemberottr:OtterTailCorporationMember2020-12-310001466593ottr:VinyltechCorporationMemberottr:OtterTailCorporationMember2020-12-310001466593ottr:BTDManufacturingIncMemberottr:OtterTailCorporationMember2020-12-310001466593ottr:TOPlasticsIncMemberottr:OtterTailCorporationMember2020-12-310001466593ottr:VaristarCorporationMemberottr:OtterTailCorporationMember2020-12-310001466593ottr:OtterTailAssuranceLimitedMemberottr:OtterTailCorporationMember2020-12-310001466593ottr:OtterTailCorporationMember2020-12-310001466593us-gaap:AllowanceForCreditLossMember2020-12-310001466593us-gaap:AllowanceForCreditLossMember2021-01-012021-12-310001466593us-gaap:AllowanceForCreditLossMember2021-12-310001466593us-gaap:AllowanceForCreditLossMember2019-12-310001466593us-gaap:AllowanceForCreditLossMember2020-01-012020-12-310001466593us-gaap:AllowanceForCreditLossMember2018-12-310001466593us-gaap:AllowanceForCreditLossMember2019-01-012019-12-310001466593us-gaap:ValuationAllowanceOfDeferredTaxAssetsMember2020-12-310001466593us-gaap:ValuationAllowanceOfDeferredTaxAssetsMember2021-01-012021-12-310001466593us-gaap:ValuationAllowanceOfDeferredTaxAssetsMember2021-12-310001466593us-gaap:ValuationAllowanceOfDeferredTaxAssetsMember2019-12-310001466593us-gaap:ValuationAllowanceOfDeferredTaxAssetsMember2020-01-012020-12-310001466593us-gaap:ValuationAllowanceOfDeferredTaxAssetsMember2018-12-310001466593us-gaap:ValuationAllowanceOfDeferredTaxAssetsMember2019-01-012019-12-31
UNITED STATES
SECURITIES AND EXCHANGE COMMISSION
Washington, D.C. 20549
FORM 10-K
(Mark One)
☒ Annual Report pursuant to Section 13 or 15(d) of the Securities Exchange Act of 1934
For the fiscal year ended December 31, 2021 or
☐ Transition Report pursuant to Section 13 or 15(d) of the Securities Exchange Act of 1934
Commission File Number 0-53713
OTTER TAIL CORPORATION
(Exact name of registrant as specified in its charter)
| | | | | |
Minnesota (State or other jurisdiction of incorporation or organization) | 27-0383995 (I.R.S. Employer Identification No.) |
| |
215 South Cascade Street, Box 496, Fergus Falls, Minnesota (Address of principal executive offices) | 56538-0496 (Zip Code) |
Registrant's telephone number, including area code: 866-410-8780
Securities registered pursuant to Section 12(b) of the Act:
| | | | | | | | |
Title of each class | Trading Symbol(s) | Name of each exchange on which registered |
Common Shares, par value $5.00 per share | OTTR | The Nasdaq Stock Market LLC |
Securities registered pursuant to Section 12(g) of the Act: None
Indicate by check mark if the registrant is a well-known seasoned issuer, as defined in Rule 405 of the Securities Act. Yes ☑ No ☐
Indicate by check mark if the registrant is not required to file reports pursuant to Section 13 or Section 15(d) of the Act. Yes ☐ No ☑
Indicate by check mark whether the registrant (1) has filed all reports required to be filed by Section 13 or 15(d) of the Securities Exchange Act of 1934 during the preceding 12 months (or for such shorter period that the registrant was required to file such reports), and (2) has been subject to such filing requirements for the past 90 days. Yes ☑ No ☐
Indicate by check mark whether the registrant has submitted electronically every Interactive Data File required to be submitted pursuant to Rule 405 of Regulation S-T during the preceding 12 months (or for such shorter period that the registrant was required to submit such files). Yes ☑ No ☐
Indicate by check mark whether the registrant is a large accelerated filer, an accelerated filer, a non-accelerated filer or a smaller reporting company. See the definitions of “large accelerated filer,” “accelerated filer,” “smaller reporting company” and “emerging growth company” in Rule 12b-2 of the Exchange Act. (Check one):
| | | | | | | | | | | | | | | | | |
| Large Accelerated Filer ☑ | | Accelerated Filer ☐ | | |
| Non-Accelerated Filer ☐ | | Smaller Reporting Company ☐ | | Emerging Growth Company ☐ |
If an emerging growth company, indicate by check mark if the registrant has elected not to use the extended transition period for complying with any new or revised financial accounting standards provided pursuant to Section 13(a) of the Exchange Act ☐
Indicate by check mark whether the registrant has filed a report on and attestation to its management's assessment of the effectiveness of its internal control over financial reporting under Section 404(b) of the Sarbanes-Oxley Act (15 U.S.C. 7262(b)) by the registered public accounting firm that prepared or issued
its audit report. ☑
Indicate by check mark whether the registrant is a shell company (as defined in Rule 12b-2 of the Exchange Act). Yes ☐ No ☑
As of June 30, 2021, the aggregate market value of common stock held by non-affiliates was 1,948,379,911.
Indicate the number of shares outstanding of each of the registrant's classes of common stock, as of the latest practicable date: 41,605,742 Common Shares ($5 par value) as of February 7, 2022.
DOCUMENTS INCORPORATED BY REFERENCE
The Registrant's definitive Proxy Statement for its 2022 Annual Meeting of Shareholders is incorporated by reference into Part III of this Form 10-K.
| | | | | | | | |
| Description | Page |
| | |
| | |
| | |
| | |
| | |
ITEM 1. | | |
ITEM 1A. | | |
ITEM 1B. | | |
ITEM 2. | | |
ITEM 3. | | |
ITEM 3A. | | |
ITEM 4. | | |
| | |
ITEM 5. | | |
| | |
ITEM 7. | | |
ITEM 7A. | | |
ITEM 8. | | |
| | |
| | |
| | |
| | |
| | |
| | |
| | |
| | |
ITEM 9. | | |
ITEM 9A. | | |
ITEM 9B. | | |
ITEM 9C. | | |
| | |
ITEM 10. | | |
ITEM 11. | | |
ITEM 12. | | |
ITEM 13. | | |
ITEM 14. | | |
| | |
ITEM 15. | | |
ITEM 16. | | |
| | |
The following abbreviations or acronyms are used in the text. | | | | | | | | | | | | | | |
ACE | Affordable Clean Energy | | kwh | kilowatt-hour |
AFUDC | Allowance for Funds Used During Construction | | LIBOR | London Interbank Offered Rate |
ARO | Asset Retirement Obligation | | LSA | Lignite Sales Agreement |
ARP | Alternative Revenue Program | | Merricourt | Merricourt Wind Energy Center |
Astoria | Astoria Station | | MISO | Midcontinent Independent System Operator, Inc. |
BTD | BTD Manufacturing, Inc. | | MPUC | Minnesota Public Utilities Commission |
CCMC | Coyote Creek Mining Company, L.L.C. | | NAV | Net Asset Value |
CDD | Cooling Degree Day | | NDDEQ | North Dakota Department of Environmental Quality |
CIP | Conservation Improvement Program | | NDPSC | North Dakota Public Service Commission |
CO2 | carbon dioxide | | NERC | North American Electric Reliability Corporation |
COSO | Committee of Sponsoring Organizations of the Treadway Commission | | Northern Pipe | Northern Pipe Products, Inc. |
ECR | Environmental Cost Recovery Rider | | OSHA | Occupational Safety and Health Administration |
EEI | Edison Electric Institute | | OTC | Otter Tail Corporation |
EEP | Energy Efficiency Plan | | OTP | Otter Tail Power Company |
EPA | Environmental Protection Agency | | PACE | Partnership in Assisting Community Expansion |
ERISA | Employee Retirement Income Security Act of 1974 | | PIR | Phase-in Rider |
ESSRP | Executive Survivor and Supplemental Retirement Plan | | PTCs | Production tax credits |
ETS | Emergency Temporary Standard | | PVC | Polyvinyl chloride |
EUIC | Electric Utility Infrastructure Cost Recovery Rider | | RHR | Regional Haze Rule |
FCA | Fuel Clause Adjustment | | ROE | Return on equity |
FERC | Federal Energy Regulatory Commission | | RRR | Renewable Resource Rider |
GCR | Generation Cost Recovery Rider | | SDPUC | South Dakota Public Utilities Commission |
GHG | Greenhouse Gas | | SEC | Securities and Exchange Commission |
HDD | Heating Degree Day | | SRECs | Solar renewable energy credits |
ISO | Independent System Operator | | T.O. Plastics | T.O. Plastics, Inc. |
IRP | Integrated Resource Plan | | TCR | Transmission Cost Recovery Rider |
kV | kiloVolt | | Varistar | Varistar Corporation |
kW | kiloWatt | | Vinyltech | Vinyltech Corporation |
| | | | |
| | | | | | | | |
WHERE TO FIND MORE INFORMATION | | |
We make available free of charge at our website (www.ottertail.com) our annual reports on Form 10-K, quarterly reports on Form 10-Q, current reports on Form 8-K, proxy and information statements, Forms 3, 4 and 5 filed on behalf of directors and executive officers and any amendments to these reports filed or furnished pursuant to Section 13(a) or 15(d) of the Securities Exchange Act of 1934, as soon as reasonably practicable after such material is electronically filed with or furnished to the Securities and Exchange Commission (SEC). These reports are also available on the SEC's website (www.sec.gov). Information on our and the SEC's websites is not deemed to be incorporated by reference into this report on Form 10-K. | | |
FORWARD-LOOKING INFORMATION |
This report on Form 10-K contains forward-looking statements within the meaning of the Private Securities Litigation Reform Act of 1995 (the Act). When used in this Form 10-K and in future filings by the Company with the SEC, in the Company’s press releases and in oral statements, words such as “anticipate,” “believe,” “could,” “estimate,” “expect,” "goal," “intend,” “may,” “outlook,” “plan,” “possible,” “potential,” "probable," "projected," “should,” "target," “will,” “would” or similar expressions are intended to identify forward-looking statements within the meaning of the Act. Such statements are based on current expectations and assumptions and entail various risks and uncertainties that could cause actual results to differ materially from those expressed in such forward-looking statements. Such risks and uncertainties include the various factors set forth in Item 1A. Risk Factors of this report on Form 10-K and in our other SEC filings.
PART I
Otter Tail Corporation (OTC) has interests in diversified operations that include an electric utility and manufacturing and plastic pipe businesses with corporate offices located in Fergus Falls, Minnesota and Fargo, North Dakota.
We classify our five operating companies into three reportable segments consistent with our business strategy and management structure. The following table depicts our three segments and the subsidiary entities included within each segment:
| | | | | | | | | | | | | | |
ELECTRIC SEGMENT | | MANUFACTURING SEGMENT | | PLASTICS SEGMENT |
Otter Tail Power Company (OTP) | | BTD Manufacturing, Inc. (BTD) | | Northern Pipe Products, Inc. (Northern Pipe) |
| | T.O. Plastics, Inc. (T.O. Plastics) | | Vinyltech Corporation (Vinyltech) |
Electric includes the generation, purchase, transmission, distribution and sale of electric energy in western Minnesota, eastern North Dakota and northeastern South Dakota. OTP, our largest operating subsidiary and primary business since 1907, serves more than 133,000 customers in more than 400 communities across a predominantly rural and agricultural service territory.
Manufacturing consists of businesses in the following manufacturing activities: contract machining; metal parts stamping, fabrication and painting; and production of plastic thermoformed horticultural containers, life science and industrial packaging, material handling components and extruded raw material stock. These businesses have manufacturing facilities in Georgia, Illinois and Minnesota and sell products primarily in the United States.
Plastics consists of businesses producing polyvinyl chloride (PVC) pipe at plants in North Dakota and Arizona. The PVC pipe is sold primarily in the western half of the United States and Canada.
Throughout the remainder of this report, we use the terms "Company", "us", "our", or "we" to refer to OTC and its subsidiaries collectively. We will also refer to our Electric, Manufacturing and Plastics segments and our individual subsidiaries as indicated above.
INVESTMENT AND GROWTH STRATEGY
We maintain a moderate risk profile by investing in rate base growth opportunities in our Electric segment and organic growth opportunities in our Manufacturing and Plastics segments. This strategy and risk profile are designed to provide a more predictable earnings stream, maintain our credit quality and preserve our ability to fund our dividend payments. Our goal is to deliver annual growth in earnings per share between five and seven percent over the next several years, using 2020 diluted earnings per share as the base for measurement. We expect our earnings growth to come from rate base investments in our Electric segment and from existing capacities and planned investments within our Manufacturing and Plastics segments.
We will continue to review our business portfolio to identify additional opportunities to improve our risk profile, enhance our credit metrics and generate additional sources of cash to support the organic growth opportunities in our electric utility and manufacturing and plastics segments. We will also evaluate opportunities to allocate capital to potential acquisitions within our Manufacturing and Plastics segments. We are a committed long-term owner and do not acquire companies in pursuit of short-term gains. However, we will divest businesses which no longer fit into our strategy and risk profile over the long term.
We maintain a set of criteria used in evaluating the strategic fit of our operating businesses. The operating company should:
•Maintain a minimum level of net earnings and a return on invested capital in excess of the Company’s weighted average cost of capital,
•Have a strategic differentiation from competitors and a sustainable cost advantage,
•Operate within a stable and growing industry and be able to quickly adapt to changing economic cycles, and
•Have a strong management team committed to operational and commercial excellence.
Over time, we expect our Electric segment will provide approximately 70% of our overall earnings and our Manufacturing and Plastics segments will collectively provide approximately 30% of our overall earnings and continue to be a fundamental part of our strategy.
Our actual mix of earnings for the years ended December 31, 2021, 2020, 2019 was as follows:
Our 2021 earnings mix was impacted by significantly higher earnings in our Plastics segment as unique supply and demand conditions during the year in the PVC pipe industry led to earnings levels not previously experienced. We expect our earnings mix to return back to our targeted mix of 70% from the Electric segment and 30% from the Manufacturing and Plastics segments over the long term as these industry conditions subside.
HUMAN CAPITAL
Our employees are a critical resource and an integral part of our success. We strive to provide an environment of opportunity and accountability where people are valued and empowered to do their best work. We are focused on the health and safety of our employees and creating a culture of inclusion, excellence and learning. Our human capital management efforts include monitoring various metrics and objectives associated with i) employee safety, ii) workforce stability, iii) management and workforce demographics, including gender, racial and ethnic diversity, iv) leadership development and succession planning and v) productivity. We have established the following programs in furtherance of these efforts:
Safety - Safety is one of our core values. In managing our business, we focus on the safety of our employees and have implemented safety programs and management practices to promote a culture of safety. Safety is also a metric used and evaluated in determining annual incentive compensation. We continually monitor the Occupational Safety and Health Administration (OSHA) Total Recordable Incident Rate (number of work-related injuries per 100 employees for a one-year period) and Lost Time Incident Rate (number of employees who lost time due to work-related injuries per 100 employees for a one-year period). New cases are reported and evaluated for corrective action during monthly safety meetings attended by safety professionals at all locations. Our 2021 Total Recordable Incident Rate was 1.86, compared to 1.42 in 2020 and our Lost Time Incident Rate was 0.57, compared to 0.55 in 2020. In both 2021 and 2020 these rates were favorable to the rates of our peers.
Leadership Development and Training Programs - We extend leadership development throughout the organization to build enterprise-wide understanding of our culture, strategy and processes. Annual succession planning, individual development planning, mentoring, and supervisory and leadership development programs all play a role in ensuring a capable leadership team now and in the future. Our skill progression and technical training programs help to retain a stable and skilled workforce.
Workforce Stability - Retaining and developing our employees is an important factor in our continued success and growth. We regularly evaluate our employee retention and turnover rates.
Employee Engagement - To enhance productivity and employee engagement, and to help our companies continue to be places where our employees choose to work and thrive, we have undertaken a multi-year series of employee engagement surveys. We use the feedback to help shape the future of our organization.
Code of Business Ethics - We communicate annually to all employees on our code of business ethics to reinforce our commitment to compliance with laws, regulations and values that guide who we are and how we do business.
Across our operating companies and including our corporate team as of December 31, 2021, we employed 2,487 full-time employees:
| | | | | |
Segment/Organization | Employees |
| |
Electric Segment | |
OTP (1) | 721 | |
Manufacturing Segment | |
BTD | 1,364 | |
T.O. Plastics | 182 | |
Segment Total | 1,546 | |
Plastics Segment | |
Northern Pipe | 104 | |
Vinyltech | 78 | |
Segment Total | 182 | |
Corporate | 38 | |
Total | 2,487 | |
(1) Includes all full-time employees of Otter Tail Power Company, including employees working at jointly-owned facilities. Labor costs associated with employees working at jointly-owned facilities are allocated to each of the co-owners based on their ownership interest. | |
At December 31, 2021, 358 employees of OTP are represented by local unions of the International Brotherhood of Electrical Workers under two separate collective bargaining agreements expiring on August 31, 2023 and October 31, 2023. OTP has not experienced any strike, work stoppage or strike vote, and considers its present relations with employees to be good. None of the employees of our other operating companies are represented by local unions.
The demographics of our workforce, including our Board of Directors, as of December 31, 2021 was as follows: | | | | | | | | | | | |
| % Female | | % Racially and Ethnically Diverse |
| | | |
Board of Directors(1) | 20 | % | | 10 | % |
CEO Direct Reports | 33 | % | | — | % |
Management | 22 | % | | 4 | % |
Non-Management Employees | 17 | % | | 19 | % |
| | | |
(1) Includes the new director appointed to our Board effective January 1, 2022. | | | |
| | | | | |
ELECTRIC | Contribution to Operating Revenues: 40% (2021), 50% (2020), 50% (2019) |
OTP, headquartered in Fergus Falls, Minnesota, is a vertically integrated, regulated utility with generation, transmission and distribution facilities to serve its more than 133,000 residential, industrial and commercial customers in a service area encompassing approximately 70,000 square miles of western Minnesota, eastern North Dakota and northeastern South Dakota.
CUSTOMERS
Our service territory is predominantly rural and agricultural and includes over 400 communities, most of which have populations of less than 10,000. While our customer base includes relatively few large customers, sales to commercial and industrial customers are significant, with one industrial customer accounting for 10% of segment operating revenues for the year ended December 31, 2021.
The following charts summarize our retail electric revenues by state and by customer segment for the years ended December 31, 2021 and 2020:
In addition to retail revenue, our Electric segment also generates operating revenues from the transmission of electricity for others over the transmission assets we wholly or jointly own with other transmission service providers, and from the sale of electricity we generate and sell into the wholesale electricity market.
COMPETITIVE CONDITIONS
Retail electric sales are made to customers in assigned service territories. As a result, most retail customers do not have the ability to choose their electric supplier. Competition is present in some areas from municipally owned systems, rural electric cooperatives and, in certain respects, from on-site generators and co-generators. Electricity also competes with other forms of energy.
Competition also arises from customers supplying their own power through distributed generation, which is the generation of electricity on-site or close to where it is needed in small facilities designed to meet local needs. Distributed energy resources can include combined heat and power, solar photovoltaic, wind, battery storage, thermal storage and demand-response technologies.
The degree of competition may vary from time to time depending on relative costs and supplies of other forms of energy and advances in technology. Irrespective of the competitive environment, we are focused on providing value to our customers and ensuring our retail rates remain among the lowest in the region and in the nation.
The following table presents our average retail rate per kilowatt-hour (kwh) by customer class and in total for the years ended December 31, 2021 and 2020:
| | | | | | | | | | | |
Revenue per kwh | 2021 | | 2020 |
| | | |
Residential | 10.90 | ¢ | | 10.05 | ¢ |
Commercial & Industrial | 7.52 | ¢ | | 7.40 | ¢ |
Total Retail | 8.47 | ¢ | | 8.15 | ¢ |
Wholesale electricity markets are competitive under the Federal Energy Regulatory Commission (FERC) open access transmission tariffs, which require utilities to provide nondiscriminatory access to all wholesale users. In addition, the FERC has established a competitive process for the construction and operation of certain new electric transmission facilities whereby electric transmission providers, including the Midcontinent Independent System Operator, Inc. (MISO), of which OTP is a member, are required to remove from their tariffs a federal right of first refusal to construct transmission facilities selected in a regional transmission plan for purposes of cost allocation. The FERC is contemplating potential reforms for electric regional transmission planning, cost allocation and generator interconnection processes. While the ultimate regulatory outcome is uncertain at this time, changes to the regulatory framework could impact future transmission investments.
Franchises
OTP has franchises to operate as an electric utility in substantially all of the incorporated municipalities it serves. Franchise rights generally require periodic renewal. No franchises are required to serve unincorporated communities in any of the three states OTP serves.
GENERATION AND PURCHASED POWER
OTP primarily relies on company-owned generation, supplemented by purchase power agreements, to supply the energy to meet our customer needs. Wholesale market purchases and sales of electricity are used as necessary to balance supply and demand. Our mix of owned generation and wholesale market energy purchases to meet customer demand are impacted by wholesale energy prices and the relative cost of each energy source.
As of December 31, 2021, OTP’s wholly or jointly owned plants and facilities, as well as in place purchased power agreements, and their dependable kilowatt (kW) capacity were: | | | | | | | | |
| | Capacity / Purchased Power in kW |
| | |
Owned Generation: | | |
Baseload Plants | | |
Big Stone Plant(1) | | 257,700 | |
Coyote Station(2) | | 149,100 | |
Total Baseload Plants | | 406,800 | |
Combustion Turbine and Small Diesel Units | | |
Astoria Station | | 249,700 | |
All Other | | 102,800 | |
Total Combustion Turbine and Small Diesel Units | | 352,500 | |
Owned Wind Facilities (rated at nameplate) | | |
Merricourt Wind Energy Center | | 150,000 | |
Luverne Wind Farm | | 49,500 | |
Ashtabula Wind Center | | 48,000 | |
Langdon Wind Center | | 40,500 | |
Total Owned Wind Facilities | | 288,000 | |
Hydroelectric Facilities | | 2,600 | |
Total Owned Generation Capacity | | 1,049,900 | |
Purchased Power Agreements: | |
Purchased Wind Power (rated at nameplate and greater than 2,000 kW) | |
Ashtabula Wind III | | 62,400 | |
Edgeley | | 21,000 | |
Langdon | | 19,500 | |
Total Purchased Wind | | 102,900 | |
Total Generating Capacity | | 1,152,800 | |
(1) Reflects OTP's 53.9% ownership percentage of jointly-owned facility | | |
(2) Reflects OTP's 35.0% ownership percentage of jointly-owned facility | | |
The following charts summarize the percentage of our generating capacity by source, including owned and jointly-owned facilities and through power purchase arrangements, as of December 31, 2021 and 2020:
Under MISO requirements, OTP is required to have sufficient capacity through wholly or jointly-owned generating capacity or purchased power agreements to meet its monthly weather-normalized forecast demand, plus a reserve obligation. OTP met its obligation for the 2020-2021 planning year and anticipates meeting this obligation prospectively.
The following charts summarize the percentage of retail kilowatt-hours (kwh) sold by source during the years ended December 31, 2021 and 2020:
Capacity Retirements and Additions
Hoot Lake Plant, our 142-megawatt coal-fired power plant in Fergus Falls, Minnesota was retired in mid-2021.
As part of our investment plan to meet our future energy needs, we have the following significant projects at various stages of planning and construction or that have been recently completed:
Merricourt Wind Energy Center (Merricourt) is a 150-megawatt wind farm located in southeastern North Dakota. Construction of the wind farm commenced in 2019 and the facility was placed into commercial operation in December 2020, with a total cost of approximately $260 million.
Astoria Station Natural Gas Plant (Astoria) is a 245-megawatt simple cycle natural gas combustion turbine generation facility near Astoria, South Dakota. Construction commenced in 2019 and the facility was placed into commercial operation in February 2021, with a total cost of approximately $160 million.
Hoot Lake Solar is a 49-megawatt solar farm under development on land on and around our Hoot Lake Plant in Fergus Falls, Minnesota, with an anticipated cost of approximately $60 million. We anticipate the facility will be in commercial operation by the end of 2023.
ENERGY TRANSITION
Otter Tail Power is committed to transitioning to a lower-carbon and increasingly clean energy future, while maintaining low cost and reliable electricity to serve our customers. We have developed the following goals in the furtherance of our efforts to support the energy transition:
Provide 30% of energy generated from renewable resources to our customers by 2023.
Reduce carbon emissions from owned generation resources by 50% by 2025 from 2005 levels.
Reduce carbon emissions from owned generation resources by 97% by 2050 from 2005 levels.
To date, we have undertaken numerous initiatives to reduce our carbon footprint and mitigate greenhouse gas emissions in the process of generating electricity for our customers. Our initiatives include increasing the efficiency of our plants, adding renewable energy to our resource mix and sponsoring energy conservation programs.
From 2005 through 2021, we have reduced our carbon dioxide emissions approximately 39% and increased the amount of renewable generation resources we own or contract through purchase power agreements by approximately 370 megawatts. Our future resource plans to deliver low-cost, reliable and increasingly clean energy to our customers include the addition of 49 megawatts of solar energy from Hoot Lake Solar in 2023 along with the resource additions as outlined in our Integrated Resource Plan, including the addition of 150 megawatts of solar generation and 100 megawatts of wind generation by 2027. Our resource plan also proposes to withdraw from Coyote Station, our jointly owned coal-fired generation facility by the end of 2028.
The following chart depicts our energy resource mix in 2005 and 2021 and the projected mix in 2025 and 2030 if our preferred plan within our Integrated Resource Plan is approved in each of the jurisdictions in which we operate. The amounts include energy generated from owned resources, procured through purchase power agreements and energy purchased in the wholesale market:
RESOURCE MATERIALS
Coal is the principal fuel burned at our jointly-owned Big Stone and Coyote Station generating plants. Coyote Station, a mine-mouth facility, burns North Dakota lignite coal. Big Stone Plant burns western subbituminous coal transported by rail. We source coal for our coal-fired power plants through requirements contracts which do not include minimum purchase requirements but do require all coal necessary for the operation of the respective plant to be purchased from the counterparty. Our coal supply contracts for our Big Stone Plant and Coyote Station have expiration dates in 2022 and 2040, respectively.
The supply agreement between the Coyote Station owners, including OTP, and the coal supplier includes provisions requiring the Coyote Station owners to purchase the membership interests and pay off or assume loan and lease obligations of the coal supplier, as well as complete mine closing and post-mining reclamation, in the event of certain early termination events and at the expiration of the coal supply agreement in 2040. See Note 1 to our consolidated financial statements included in this report on Form 10-K for additional information.
Coal is transported to our non-mine-mouth facility, Big Stone Plant, by rail and is provided under a common carrier rate which includes a mileage-based fuel surcharge.
We purchase natural gas for use at our combustion turbine facilities based on anticipated short-term resource needs. We procure natural gas from multiple vendors at spot prices in a liquid market primarily under firm delivery contracts.
TRANSMISSION AND DISTRIBUTION
Our transmission and distribution assets deliver energy from energy generation sources to our customers. In addition, we earn revenue from the transmission of electricity over our wholly or jointly owned transmission assets for others under approved rate tariffs. As of December 31, 2021, we were the sole or joint owner of over 9,000 miles of transmission and distribution lines.
Midcontinent Independent System Operator, Inc. (MISO)
MISO is an independent, non-profit organization that operates the transmission facilities owned by other entities, including OTP, within its regional jurisdiction and administers energy and generation capacity markets. MISO has operational control of our transmission facilities above 100 kiloVolts (kV). MISO seeks to optimize the efficiency of the interconnected system, provide solutions to regional planning needs and minimize risk to reliability through its security coordination, long-term regional planning, market monitoring, scheduling and tariff administration functions.
SEASONALITY
Electricity demand is affected by seasonal weather differences, with peak demand occurring in the summer and winter months. As a result, our Electric segment operating results regularly fluctuate on a seasonal basis. In addition, fluctuations in electricity demand within the same season but between years can impact our operating results. We monitor the level of heating and cooling degree days in a period to assess the impact of weather-related effects on our operating results between periods.
PUBLIC UTILITY REGULATION
OTP is subject to regulation of rates and other matters in each of the three states in which it operates and by the federal government for, among other matters, the interstate transmission of electricity. OTP operates under approved retail electric tariff rates in all three states it serves. Tariff rates are designed to recover plant investments, a return on those investments and operating costs. In addition to determining rate tariffs, state regulatory commissions also authorize return on equity (ROE), capital structure and depreciation rates of our plant investments. Decisions by our regulators significantly impact our operating results, financial position and cash flows.
Below is a summary of the regulatory agencies with jurisdiction of electric rates over OTP covered by each regulatory agency:
| | | | | | | | | | |
Regulatory | | | | |
Agency | | | | Areas of Regulation |
| | | | |
Minnesota Public Utilities Commission (MPUC)
| | | | Retail rates, issuance of securities, depreciation rates, capital structure, public utility services, construction of major facilities, establishment of exclusive assigned service areas, contracts with subsidiaries and other affiliated interests and other matters. Selection or designation of sites for new generating plants (50,000 kW or more) and routes for transmission lines (100 kV or more). Review and approval of fifteen-year Integrated Resource Plan. |
North Dakota Public Service Commission (NDPSC) | | | | Retail rates, certain issuances of securities, construction of major utility facilities and other matters. Approval of site and routes for new electric generating facilities (500 kW or more for wind generating facilities; 50,000 kW for non-wind generating facilities) and high voltage transmission lines (115 kV or more). Review and approval of ten-year facility plan and Integrated Resource Plan. |
South Dakota Public Utilities Commission (SDPUC) | | | | Retail rates, public utility services, construction of major facilities, establishment of assigned service areas and other matters. Approval of sites and routes for new electric generating facilities (100,000 kW or more) and most transmission lines (115 kV or more). |
Federal Energy Regulatory Commission (FERC) | | | | Wholesale electricity sales, transmission and sale of electric energy in interstate commerce, interconnection of facilities, hydroelectric licensing and accounting policies and practices. Compliance with North American Electric Reliability Corporation (NERC) reliability standards, including standards on cybersecurity and protection of critical infrastructure. |
In addition to base rates, which are established through periodic rate case proceedings within each state jurisdiction, there are other mechanisms for recovery of plant investments, including a return on investment and operating expenses, between rate cases. The following table summarizes these recovery mechanisms:
| | | | | | | | | | | | | | |
Recovery Mechanism | | Jurisdiction(s) | | Additional Information |
| | | | |
Fuel Clause Adjustment (FCA) | | MN, ND, SD | | Provides for periodic billing adjustments for changes in prudently incurred costs of fuel and purchased power. In North and South Dakota, fuel and purchased power costs are generally adjusted on a monthly basis with over or under collections from the previous month applied to the next monthly billing. In Minnesota, fuel and purchased power costs are estimated on an annual basis and the accumulated difference between actual and estimated cost per kwh are refunded or recovered, subject to regulatory approval, in subsequent periods. |
Transmission Cost Recovery Rider (TCR) | | MN, ND, SD | | Provides for recovery of costs outside of a general rate case for investments in new or modified electric transmission or distribution assets. |
Environmental Cost Recovery Rider (ECR) | | MN, ND, SD | | Provides for recovery of costs outside of a general rate case for investments in certain environmental improvement projects. |
Renewable Resource Rider (RRR) | | MN, ND | | Provides for recovery of costs outside of a general rate case for investments in certain new renewable energy projects. |
Conservation Improvement Program (CIP) | | MN | | Under Minnesota law, OTP is required to invest at least 1.5% of its gross operating revenues on energy conservation improvements. Recovery of these costs outside of a general rate case occurs through the CIP rider. |
Electric Utility Infrastructure Costs Rider (EUIC) | | MN | | Provides for recovery of costs for investments made to replace or modify existing infrastructure if the replacement or modification conserves energy or uses energy more efficiently. |
Generation Cost Recovery Rider (GCR) | | ND | | Provides for the recovery of costs outside of a general rate case for investments in new generation facilities. |
Energy Efficiency Plan (EEP) | | SD | | Provides for the recovery of costs from energy efficiency investments. |
Phase-In Rider (PIR) | | SD | | Provides for the recovery of costs outside of a general rate case for investments in new generation facilities. |
Renewable Energy Standard
Minnesota has a renewable energy standard requiring utilities to generate or procure sufficient renewable generation such that the following percentages of total retail electric sales to Minnesota customers come from qualifying renewable sources: 17% by 2016; 20% by 2020 and 25% by 2025. We met the current renewable sources requirements with a combination of owned renewable generation and purchases from renewable generation sources. Minnesota law also requires 1.5% of total Minnesota electric sales by public utilities to be supplied by solar energy. For a public utility with between 50,000 and 200,000 retail electric customers, such as OTP, at least 10% of the 1.5% requirement must be met by solar energy generated by or procured from solar photovoltaic devices with a nameplate capacity of 40 kWs or less. OTP plans to purchase Solar Renewable Energy Credits (SRECs) to meet its obligations until its Hoot Lake Solar and other solar projects are complete and operational. OTP plans to purchase SRECs to meet its 2021 obligation, for which compliance will be measured as of April 30, 2022.
Under certain circumstances and after consideration of costs and reliability issues, the MPUC may modify or delay implementation of the standards. We are evaluating potential options for maintaining compliance and meeting the solar energy standard beyond 2021.
Integrated Resource Plan (IRP)
Under Minnesota law, utilities are required to submit for approval by the MPUC a 15-year advance IRP. An IRP is a set of resource options a utility could use to meet the service needs of its customers over the forecast period, including an explanation of the utility’s supply and demand circumstances, and the extent to which each resource option would be used to meet those service needs. The MPUC’s findings of fact and conclusions regarding IRPs are considered to be prima facie evidence, subject to rebuttal, in future rate reviews and other proceedings. Typically, IRPs are submitted every two years.
In 2021, the North Dakota Legislative Assembly enacted a provision requiring investor-owned electric utilities to submit an IRP to the NDPSC and granted the NDPSC the authority to adopt rules and regulations for the preparation and submission of integrated resource plans. To date, the NDPSC has not established any formal rules and regulations.
On September 1, 2021, OTP filed its 2022 IRP concurrently with regulators in the three states where OTP operates, Minnesota, North Dakota and South Dakota. The 2022 IRP includes OTP’s preferred plan for meeting customers’ anticipated capacity and energy needs while maintaining system reliability and low electric service rates.
The components of OTP's preferred plan include:
•the addition of dual fuel capability at our Astoria Station natural gas plant, allowing for the plant to burn fuel oil in addition to natural gas;
•the addition of 150 megawatts of solar generation in 2025;
•the addition of 100 megawatts of wind generation in 2027;
•the commencement of the process of withdrawing from our 35 percent ownership interest in Coyote Station, a jointly owned, coal-fired generation plant, by December 31, 2028; and
•the addition of 50 megawatts of solar generation in 2033.
The 2022 IRP includes requests for approval of certain activities planned to commence within the next five years, which include the addition of dual fuel capacity at our Astoria Station natural gas plant, the addition of 150 megawatts of solar generation and commencement of the withdrawal from our ownership interest in Coyote Station. Although the 2022 IRP includes planned actions beyond 2026, regulators will not act upon or approve planned actions in periods beyond 2026 as part of our 2022 IRP filing.
The preferred plan proposes to, subject to regulatory approval, create a regulatory asset as a vehicle to recover costs related to a future withdrawal from Coyote Station, including the net book value of the plant on the withdrawal date, anticipated decommissioning costs and any required costs incurred as a result of an early termination of the existing lignite sales agreement, under which Coyote Station acquires all of its lignite coal from a nearby mine. As part of the filing, OTP developed an estimate of the reasonably foreseeable costs of withdrawing from Coyote Station at the end of 2028 of $68.5 million. These costs may differ from actual results due to the uncertainty and timing of future events associated with the terms and conditions of a withdrawal.
Capital Structure Petition
Minnesota law requires an annual filing of a capital structure petition with the MPUC. In this filing the MPUC reviews and approves OTP's capital structure. Once approved, OTP may issue securities without further petition or approval, provided the issuance is consistent with the purposes and amounts set forth in the approved petition. OTP’s current capital structure approved by the MPUC on January 26, 2022, allows for an equity-to-total-capitalization ratio between 48.0% and 58.7%, with total capitalization not to exceed $1.7 billion.
ENVIRONMENTAL REGULATION
OTP is subject to stringent federal and state environmental standards and regulations regarding, among other things, air, water and solid waste pollution. OTP's facilities have been designed, constructed and, as necessary, updated to operate in compliance with applicable environmental regulations. However, new or amended laws and regulations or changes in interpretations of current laws and regulations may require additional pollution control equipment or emission reduction measures and there can be no assurance that our facilities will remain economic to operate. Prudent expenditures incurred to comply with environmental regulations are eligible to be recovered in rates granted by regulators in jurisdictions in which we operate; however, there can be no assurance that future costs will be granted recovery. Alternatively, additional pollution control equipment or other emission reduction measures may prove to be uneconomic with the potential to lead to the exiting of a facility earlier than originally planned. As it relates to our jointly owned facilities, we may determine it is necessary to transfer, sell or otherwise divest of our ownership, or the ownership group may determine the early closure of a facility is necessary.
For the five-year period ended December 31, 2021, OTP invested approximately $13.3 million, including $0.9 million in 2021, in environmental control facilities. Our construction budgets for the next five years include an approximately $6.0 million of capital investments in environmental control equipment. The timing and amount of our expenditures may change as the regulatory environment changes.
Among current regulatory requirements, the Regional Haze Rule (RHR) could have the most significant impact on our operating results, financial condition and liquidity.
The Environmental Protection Agency (EPA) adopted the RHR in 1999 as an effort to improve visibility in national parks and wilderness areas. The RHR requires states, in coordination with the EPA and other governmental agencies, to develop and implement plans to work towards achieving natural visibility conditions by the year 2064. The second RHR implementation period covers the years 2018-2028. States are required to submit a state implementation plan to assess reasonable progress with the RHR and determine what additional emission reductions are appropriate, if any.
Coyote Station, OTP's co-owned coal-fired power plant in North Dakota is subject to assessment in the second implementation period under the North Dakota state implementation plan. In September 2021, the North Dakota Department of Environmental Quality (NDDEQ) made public a draft of its state implementation plan. The plan concluded it is not reasonable to require additional emission controls during this planning period. Following a consultation and public comment period and any subsequent modifications to the plan, the NDDEQ will submit its state implementation plan to the EPA for approval. In January 2022, the EPA provided preliminary comments on the North Dakota state implementation plan in which it expressed disagreement with the NDDEQ's recommendation to forgo additional emission controls. See Note 13 to our consolidated financial statements included in the report on Form 10-K for additional information.
Climate Change and Greenhouse Gas Regulation
Global climate change presents a significant energy and environmental policy challenge. Combustion of fossil fuels for the generation of electricity is a considerable source of carbon dioxide (CO2) emissions, which is the primary greenhouse gas (GHG) emitted by our utility operations. The federal government and many states are pursuing climate policies to regulate GHG emissions as part of a broad based effort to limit global warming.
In February 2021, the U.S. rejoined the United Nations Framework Convention on Climate Change (the Paris Agreement), which is a legally binding international treaty on climate change adopted by over 190 countries. The goal of the Paris Agreement is to limit global temperature increase to well below 2° Celsius compared to pre-industrial levels and to pursue efforts to limit the temperature increase to 1.5° Celsius. The Biden Administration has announced the goal of reducing greenhouse gas emissions by 50 to 52 percent from 2005 levels in 2030 and to reach 100 percent carbon pollution-free electricity by 2035 as part of the U.S. plan to achieve the goals under the Paris Agreement.
The implementation of climate change programs, such as the Paris Agreement, and federal or state regulations targeting GHG emissions may have a significant impact on our utility business. Specific regulatory measures to address climate change continue to evolve. In January 2021, the EPA's Affordable Clean Energy Rule (ACE Rule), which required states to develop plans for GHG emissions from coal-fired power plants, was vacated by the U.S. Court of Appeals for the District of Columbia Circuit. In October 2021, the U.S. Supreme Court agreed to hear a consolidated challenge to the Court of Appeals decision. The Supreme Court's decision, expected in mid-2022, could significantly impact the legal authority of the EPA to regulate CO2 and other greenhouse gas emissions.
While the future financial impact of any current, proposed or pending litigation or regulation of GHG or other emissions is unknown at this time, any capital or operating costs incurred for additional pollution control equipment or emission reduction measures could materially adversely impact our future operating results, financial position and liquidity unless such costs could be recovered through related rates and/or future market prices for energy.
| | | | | |
MANUFACTURING | Contribution to Operating Revenues: 28% (2021), 27% (2020), 30% (2019) |
Manufacturing consists of businesses engaged in the following activities: contract machining, metal parts stamping, fabrication and painting, and production of plastic thermoformed horticultural containers, life science and industrial packaging, and material handling components and extruded raw material stock. The following is a brief description of each of these businesses:
BTD Manufacturing, Inc. (BTD), with headquarters located in Detroit Lakes, Minnesota, provides metal fabrication services for custom machine parts and metal components through metal stamping, tool and die, machining, tube bending, welding and assembly in its facilities in Detroit Lakes and Lakeville, Minnesota, Washington, Illinois and Dawsonville, Georgia.
T.O. Plastics, Inc. (T.O. Plastics), with facilities in Otsego and Clearwater, Minnesota, manufactures extruded and thermoformed plastic products, including custom parts for customers in several industries and its own line of horticulture containers. Examples of products produced include clamshell packing, blister packs, returnable pallets and handling trays for shipping and storing odd-shaped or difficult-to-handle parts.
CUSTOMERS
Our metal fabrication business primarily serves Midwestern and Southeastern U.S. manufacturers in the recreational vehicle, lawn and garden, agricultural, construction, and industrial and energy equipment end markets. Our plastic products business serves primarily U.S. customers in the horticulture, medical and life sciences, industrial, recreational and electronics industries. The principal method of production distribution is by direct shipment to our customers through direct customer pick-up or common carrier ground transportation.
No single customer or product of our manufacturing businesses accounted for 10% or more of our consolidated operating revenue in 2021. However, the top three customers combined to account for 46% of our 2021 Manufacturing segment operating revenue.
COMPETITIVE CONDITIONS
The various markets in which we compete are characterized by intense competition from both foreign and domestic manufacturers. These markets have many established manufacturers with broader product lines, greater distribution capabilities, greater capital resources, excess capacity, labor advantages and larger marketing, research and development staffs and facilities than our own.
We believe the principal competitive factors in our Manufacturing segment are product performance, quality, price, technical innovation, cost effectiveness, customer service and breadth of product line. We intend to continue to compete based on high-performance products, innovative production technologies, cost-effective manufacturing techniques, close customer relations and support, and increasing product offerings.
RESOURCE MATERIALS
We use raw materials in the products we manufacture, including, among others, steel, aluminum, and polystyrene and other plastics resins. Managing price volatility and ensuring raw material availability are important aspects of our business. We attempt to pass increases in the costs of
these raw materials on to our customers. Increases in the costs of raw materials that cannot be passed on to customers could have a negative effect on profit margins. Additionally, a certain amount of residual material (scrap) is a by-product of the manufacturing and production processes. Declines in commodity prices for these scrap materials due to weakened demand or excess supply can negatively impact the profitability of our Manufacturing segment as it reduces their ability to mitigate the cost associated with excess material.
ENVIRONMENTAL REGULATION
Our manufacturing businesses are subject to environmental, health and safety laws and regulations, including those governing discharges to air and water, the management and disposal of hazardous substances, the cleanup of contaminated sites and health and safety matters.
| | | | | |
PLASTICS | Contribution to Operating Revenues: 32% (2021), 23% (2020), 20% (2019) |
Plastics consists of businesses producing PVC pipe at plants in North Dakota and Arizona. The following is a brief description of these businesses:
Northern Pipe Products, Inc. (Northern Pipe), located in Fargo, North Dakota, manufactures and sells PVC pipe for municipal water, rural water, wastewater, storm drainage systems and other uses in the northern, midwestern, south-central and western regions of the United States as well as central and western Canada.
Vinyltech Corporation (Vinyltech), located in Phoenix, Arizona, manufactures and sells PVC pipe for municipal water, wastewater, water reclamation systems and other uses in the western, northwest and south-central regions of the United States.
PVC pipe is manufactured through a process known as extrusion. During this process, PVC compound (a dry powder-like substance) is introduced into an extrusion machine, where it is heated to a molten state and then forced through a sizing apparatus to produce the pipe. The newly extruded pipe is pulled through a series of water-cooling tanks, marked to identify the type of pipe and cut to finished lengths.
CUSTOMERS
PVC pipe products are marketed through a combination of independent sales representatives, company salespersons and customer service representatives. Customers for our PVC pipe products consist primarily of wholesalers and distributors and the principal method for distribution of our products is by common carrier ground transportation. No single customer of the PVC pipe companies accounted for 10% or more of our consolidated operating revenues in 2021. However, two customers, both of which are distributors of PCV pipe, combined to account for 50% of our 2021 Plastics segment operating revenue.
COMPETITIVE CONDITIONS
The plastic pipe industry is fragmented and competitive due to the number of producers, the small number of raw material suppliers and the fungible nature of the product. Due to shipping costs, competition is usually regional, instead of national, in scope. The principal factors of competition are price, customer service and product performance. We compete not only against other plastic pipe manufacturers, but also ductile iron, high-density polyethylene, steel and concrete pipe producers. Pricing pressure will continue to affect our operating margins in the future.
We will continue to compete based on our high-quality products, cost-effective production techniques and close customer relations and support.
RESOURCE MATERIALS
PVC resins are acquired in bulk and shipped to our facilities by rail. There are four vendors from which we can source our PVC resin requirements. In 2021 we sourced all of our PVC resin needs from two vendors. The supply of PVC resin may also be limited primarily due to manufacturing capacity and the limited availability of raw material components. Most U.S. resin production plants are located in the Gulf Coast region. These plants are subject to the risk of damage and production shutdowns because of exposure to hurricanes or other extreme weather events that occur in this part of the United States. The loss of a key vendor, or any interruption or delay in the supply of PVC resin could disrupt the ability of the Plastics segment to manufacture products, cause customers to cancel orders or result in increased expenses for obtaining PVC resin from alternative sources, if such sources were available. We believe we have good relationships with our key raw material vendors.
Due to the commodity nature of PVC resin and PVC pipe and the dynamic supply and demand factors worldwide, historically the markets for both PVC resin and PVC pipe have been very cyclical with significant fluctuations in prices and gross margins.
In addition to PVC resin, we use certain other materials, such as tin stabilizer, gaskets and lumber, in the process of manufacturing and shipping our PVC pipe products. We generally source these materials from a limited number of suppliers, and supply chain constraints or disruptions related to these materials could disrupt our ability to manufacture or ship products and could result in increased costs.
SEASONALITY
Demand for our PVC pipe products can be impacted by seasonal weather differences, with generally lower sales volumes realized in the first quarter of the year when cold temperatures and frozen ground across the northern portion of our footprint can delay or prevent construction activity.
RISK FACTORS AND CAUTIONARY STATEMENTS
Our businesses are subject to various risks and uncertainties. Any of the risks described below or elsewhere in this report on Form 10-K or in our other SEC filings could materially adversely affect our business, operating results, financial condition and liquidity. Additional risks and uncertainties we are not presently aware of or that we currently consider immaterial may also affect our business, operating results, financial condition and liquidity.
Oversight of Risk and Related Processes
A key accountability of the Board of Directors is the oversight of material risk. Management and the Board of Directors have responsibility for overseeing the identification and mitigation of significant and emerging risks. Management identifies and analyzes risks to determine the impact and other attributes such as timing, likelihood and management control. Identification and analysis occur formally through an assessment of significant and emerging risks conducted by senior management, the financial disclosure process, and internal auditing and compliance with financial and operational controls. Management also identifies and analyzes risk through development of goals and key performance indicators, which include risk identification to determine barriers to implementing our strategy. We promote a culture of compliance, including tone at the top. The process for risk mitigation includes adherence to our code of business ethics and compliance policies, operation of formal risk management structures and overall business management to mitigate the risks inherent in the implementation of strategy. We manage and further mitigate risks through formal risk management structures, including a management executive risk committee and services such as internal audit/business risk management and legal. Management communicates regularly with our Board of Directors and key stakeholders regarding risk. Senior management presents and communicates a periodic risk assessment to our Board of Directors which provides information on the risks management believes are material, including the earnings impact, timing, likelihood and management control. The Board of Directors approaches oversight, management and mitigation of risk as an integral and continuous part of its governance of OTC. The Board of Directors regularly reviews management’s top risk assessment and analyzes areas of existing and future risks and opportunities. Finally, the Board of Directors conducts an annual strategy session where our future plans and initiatives are reviewed.
OPERATIONAL RISKS
The economic effects of the coronavirus (COVID-19) pandemic and measures taken to reduce and slow the spread of the virus could adversely impact our business.
The outbreak and global spread of COVID-19, which was declared a pandemic by the World Health Organization in March 2020, continues to have widespread and unpredictable impacts on society, economies, financial markets and businesses everywhere. The COVID-19 pandemic has impacted our business operations, including our employees, customers, construction contractors, suppliers and vendors, and there is substantial uncertainty in the nature and degree of the continued effects over time. In 2021, our business was impacted by supply chain disruptions and labor shortages resulting from the pandemic, and the associated costs and inflation related thereto. The extent to which COVID-19 impacts our business going forward is highly uncertain and will depend on future developments including the efficacy of vaccines, the spread of COVID-19 variants and the extent of federal, state and local government responses, including potential vaccine or testing mandates.
On November 5, 2021, OSHA issued an Emergency Temporary Standard (“ETS”) requiring that most employers with at least 100 employees ensure that their employees are fully vaccinated for COVID-19 or require their employees to obtain a negative COVID-19 test at least once a week. On January 13, 2022, the US Supreme Court granted emergency relief to stay the implementation of the OSHA ETS and on January 26, 2022, OSHA withdrew its ETS. Despite withdrawing the ETS as an enforceable standard, OSHA emphasized that the ETS will continue to serve as its proposal for a permanent standard. Additionally, on September 9, 2021, President Biden issued an executive order requiring employees of certain federal contractors and covered subcontractors to be vaccinated, with no weekly testing option, unless they have an approved disability or religious exemption. Currently, the mandate set forth by the executive order has been halted as several states are challenging its legality and the matter remains in litigation. If these mandates are upheld in federal court and become effective, we expect one, or both, of these new regulations will apply to at least some, and possibly all, of our businesses which could require us to mandate COVID-19 vaccination of our workforce or have our unvaccinated employees undergo required weekly COVID-19 testing, or some combination thereof, which could be difficult and costly. Further, additional vaccine and testing mandates may be announced in jurisdictions in which we operate our business, and there could be potential actions by certain states that are in conflict with the federal mandates, the impacts of which remain uncertain. Requirements to mandate COVID-19 vaccination of our workforce or requirements of our unvaccinated employees to be tested could result in labor disruptions, employee attrition and difficulty securing future labor needs.
We continue to monitor developments involving our workforce, customers, construction contractors, suppliers and vendors and take steps to mitigate against additional impacts, but given the unprecedented and evolving nature of these circumstances, we cannot predict the full extent of the impact that COVID-19 will have on our operating results, financial condition and liquidity.
Our strategy includes large capital investments, which are subject to risks.
Our business strategy includes major capital investments at our existing companies. Our capital investment program planned for the next five years includes Electric segment investments in renewable generation, transmission asset additions and upgrades, and technology and infrastructure projects, and Manufacturing and Plastics segments investments in facilities, equipment and machinery. These capital projects are planned years in advance of their in-service dates and are subject to various risks including: obtaining necessary permits, licenses and approvals in a timely manner; adverse changes in regulatory treatment or public policy; changes in commodity pricing, equipment and construction costs; technology changes; delivery delays of critical materials and components; delays caused by construction accidents, injuries or public health crises; adverse weather conditions; unforeseen product defects; limited access to capital; and other adverse conditions. Capital investments in our Electric segment are
subject to regulatory approval and are at risk of not being granted timely or full recovery of our investments. The inability to complete capital projects on budget and in a timely manner could adversely impact our operating results and financial condition.
Our acquisition or divestiture strategies are subject to risk and could adversely impact our financial position and operating results.
As part of our business strategy, we continually assess our mix of businesses and potential strategic acquisitions or divestitures. This investment strategy is subject to various risks including the ability to identify appropriate acquisition candidates or successfully negotiate and finance any acquisitions. In addition, difficulties in integrating the operations, services, products and personnel of the acquired business, and the potential loss of key employees, customers and suppliers of the acquired business could adversely impact our financial condition and operating results.
The sale of any of our businesses may result in the recognition of a loss if the business is sold for less than its book value and may expose us to risk arising from indemnification obligations that arose out of the conduct of the business prior to the sale. These obligations may include warranty and environmental obligations or the recoverability of certain assets sold as part of the transaction. Unforeseen costs related to these obligations could impact our operating results.
Weather impacts, including normal seasonal fluctuation and extreme weather events, could adversely affect our operating results.
Our Electric segment business is seasonal and weather patterns can have a material impact on our financial performance. Demand for electricity is normally greater in the winter and summer months. Unusually mild summers and winters could have an adverse effect on our financial condition and results of operations. Weather can also have a significant impact on our Plastics segment businesses as most U.S. PVC resin production plants are located in the Gulf Coast region, which is prone to seasonal hurricane activity and other extreme weather events. Our access to PVC resin may be impacted by the volume and magnitude of hurricane and storm activity in this region. In addition, our Plastics segment businesses can be affected by weather prohibiting or delaying construction projects at any time of the year in any geography, but specifically times of the year when frozen ground and cold temperatures in many parts of the country can delay construction projects, all of which can result in reduced customer demand.
Our businesses are located in areas that could be subject to natural disasters such as severe snow and ice storms, tornadoes, flooding and fires. These factors could result in interruption of our business and damage to our facilities. An extreme weather event within our utility service area could directly affect our capital assets, causing disruption in service to customers and result in repair or replacement costs, due to downed wires and poles or damage to other operating equipment.
In addition to variations in seasonal weather patterns, more widespread climate change may also create physical and financial risk to our businesses. Physical risks of climate change, such as more frequent or more extreme weather events, changes in temperature and precipitation patterns, changes to ground and surface water availability and other phenomena, could affect some or all of our operations. Severe weather or other natural disasters related to climate change could be destructive and result in increased costs and disruptions in our operations. Extreme weather conditions, such as uncommonly long periods of high or low ambient temperature, generally require more utility system backup, adding to costs and contributing to increased system stress on our utility infrastructure, which could cause service interruptions.
The loss of, or significant reduction in revenue from, any of our key customers could have an adverse effect on our operating results.
While no single customer provided more than 10% of our consolidated operating revenue, each of our segments have customers which accounted for over 10% of the segment’s operating revenues. In 2021, one customer accounted for 10% of Electric segment revenue, three customers combined to account for 46% of Manufacturing segment operating revenue and two customers combined to account for 50% of Plastics segment operating revenue. The loss of any one of these customers or a significant decline in sales to these customers, would have a significant negative impact on the segment's financial condition and operating results, and could have a significant negative impact on the Company’s consolidated financial condition and operating results.
We are subject to counterparty credit risk.
We extend credit to our customers in the ordinary course of business in each of our operating segments. Our customers' ability to pay depends on a variety of factors including macroeconomic conditions, local economic conditions, including unemployment rates, and industry conditions in which our commercial and industrial customers operate. Increased customer delinquencies and bad debts could adversely impact our operating results and liquidity.
A cyber incident, security breach or system failure could adversely affect our business and operating results.
The operation of our business is dependent on the secure function of our computer hardware and software systems. Furthermore, all our businesses require us to collect and maintain sensitive customer data, as well as confidential employee and shareholder information, which is subject to electronic theft or loss. We also use third-party vendors to electronically process certain of our business transactions. Information systems, both ours and those of third parties, are vulnerable to security breaches by computer hackers and cyber terrorists and the negligent or intentional breach of established controls and procedures or mismanagement of confidential information by employees. We may also be impacted by attacks and data security breaches of financial institutions, merchants or third-party processors. While we regularly conduct cybersecurity assessments, we cannot be certain our information security systems and protocols and those of our vendors and other third parties are sufficient to withstand a cyber-attack or other security breach.
A major cyber incident could result in significant expenses to investigate and repair security breaches or system damage and could lead to litigation, fines, other remedial action, heightened regulatory scrutiny and damage to our reputation. For example, we may be subject to liability under various federal, state and international data protection laws. These laws are subject to change and expansion and may require additional operational changes to comply.
The misappropriation, corruption or loss of personally identifiable information and other confidential data could lead to significant monetary damages, regulatory enforcement actions and breach notification and mitigation expenses, such as credit monitoring, and result in reputational
damage affecting relations with shareholders, customers and regulators. In addition to property and casualty insurance, which may cover restoration of data, certain physical damage or third-party injuries, we have cybersecurity insurance related to a breach event. However, damage and claims arising from such incidents may not be covered or may exceed the amount of any available insurance.
The inability to attract and retain a qualified workforce could have an adverse effect on our operations.
The success of our business is heavily dependent on the leadership of our executive officers and key employees for implementation of our strategy. In addition, all of our businesses rely on technical employees who possess certain specialized knowledge and skills. The inability to attract and maintain a skilled and stable workforce may negatively affect our ability to service our customers, manufacture products or successfully manage our business and achieve our objectives. Competition for employees, including skilled workers, is high and can lead to increased labor expenses, decreased productivity and potentially lost business opportunities. Our ability to maintain productivity, relationships with customers, competitive costs and quality services is limited by the ability to employ the necessary skilled personnel and could negatively affect our operating results, financial condition and liquidity.
FINANCIAL RISKS
We are subject to capital market and interest rate risks.
We rely on access to debt and equity capital markets as a source of liquidity to fund our investment initiatives, including rate base growth investments in our Electric segment and opportunities for investment, including acquisitions, in our Manufacturing and Plastics segments. Capital markets are impacted by global and domestic economic conditions, monetary policy, commodity prices, geopolitical events and other factors. If we are unable to access capital on acceptable terms and at reasonable costs, our ability to implement our business plans may be adversely affected. In addition, higher market interest rates on outstanding variable-rate, short-term indebtedness could also impact our operating results.
A decrease in our credit rating could increase our borrowing costs and result in additional contractual costs.
We rely on our investment grade credit ratings to provide acceptable costs for accessing the capital markets. A downgrade of our credit ratings could result in higher borrowing costs thereby negatively impacting our operating results and limiting our ability to access capital markets, which may negatively impact our ability to implement our business plans. In addition, OTP is a party to contracts that require the posting of collateral or settlement of applicable contracts if credit ratings fall below certain levels.
Our pension and other postretirement benefit plans are subject to investment and interest rate risks.
The financial obligations and related costs of our pension and other postretirement benefit plans are affected by numerous factors. Assumptions related to future costs, investment returns, actuarial estimates and interest rates have a significant effect on our funding obligations and the cost recognized for these plans. If our pension plan assets do not achieve our estimated long-term rate of return or if our other estimates prove to be inaccurate, our operating results, financial condition and liquidity may be adversely impacted. In addition, our funding requirements could be impacted by changes to the Pension Protection Act.
We rely on our subsidiaries to provide sufficient earnings and cash flows to allow us to meet our financial obligations and pay dividends to our shareholders.
OTC is a holding company with no significant operations of its own. The primary source of funds for payment of our financial obligations and dividends to our shareholders is from cash provided by our subsidiary companies. Our ability to meet our financial obligations and pay dividends on our common stock principally depends on the earnings, cash flows, capital requirements and general financial positions of our subsidiary companies. In addition, OTP is subject to federal and state regulations which may restrict its ability to pay dividends. Finally, we are also reliant on our subsidiary companies to maintain compliance with financial covenants under our various short- and long-term debt agreements. Our debt agreements include restrictions on the payment of cash dividends upon an event of default.
Changes in tax laws could materially affect our financial condition and operating results.
Our provision for income taxes and tax obligations are impacted by various tax laws and regulations, including the availability of various tax credits, IRS tax policies such as tax normalization and, at times, the ability to carryforward net operating losses and tax credits. Changes in tax laws, regulations and interpretations could have an adverse effect on our financial condition and operating results. Tax law changes that reduce or eliminate production or investment tax credits may impact the economics of constructing certain electric generation resources, which may adversely impact our planned investments.
A significant impairment of our goodwill would negatively impact our financial position and operating results.
As of December 31, 2021, we had $37.6 million of goodwill recorded on our consolidated balance sheet. We have recorded goodwill for businesses in our Manufacturing and Plastics segments. Goodwill is tested for impairment annually or whenever events or changes in circumstances indicate impairment may have occurred. The goodwill impairment test requires us to estimate the fair value of the businesses being tested. Estimating the fair value of a business unit requires significant judgments and estimates, including estimates of future operating results and cash flows, among others. These estimates can be affected by numerous factors, including changes in economic, industry or market conditions, changes in business operations, changes in competition or changes in technologies. Any changes in key assumptions or material differences between actual and forecasted financial performance could affect our fair value estimates and lead to a goodwill impairment charge that could adversely affect our financial condition and operating results, as well as impact compliance with financing agreement covenants.
ELECTRIC SEGMENT RISKS
General economic and industry conditions impact our business.
Several factors, many of which are beyond our control, may contribute to reduced demand for energy from our customers or increase the cost of providing energy to our customers. These risks include economic growth or decline in our service areas, demographic changes in our customer base and changes in customer demand or load growth due to, among other items, proliferation of distributed generation, energy efficiency initiatives
and technological advancements. In addition, customer demand could be impacted by increased competition in our service territories or the loss of a service territory or franchise. Other risks include increased transmission or interconnection costs, generation curtailment and changes in the manner in which wholesale power is purchased and sold. A decrease in revenues or an increase in expenses related to our electric operations could negatively impact our financial condition, operating results and liquidity.
Our utility business is significantly impacted by government legislation and regulation.
OTP is subject to federal and state legislation and comprehensive regulation by federal and state regulatory agencies, including the public utility commissions in each of the three states in which OTP operates, and by the FERC. State utility commissions regulate, among other matters, the establishment of assigned service areas, the siting and construction of major facilities, the capital structure of the utility business and the allowed rates to charge customers for providing energy and utility service. Each state utility commission operates independent of one another; therefore, OTP is subject to and must adhere to the decisions of each independent state commission. The FERC regulates, among other matters, wholesale energy transactions, hydroelectric licensing, transmission and sale of electric energy in interstate commerce and the interconnection of electric facilities.
Our financial condition, operating results and liquidity are significantly impacted by and dependent upon our ability to recover the cost of providing utility service and earning a return on our utility capital investments. There is no assurance that each state utility commission will judge our utility costs to have been prudently incurred or that rates will produce full recovery of such costs. In addition, there could be changes in the federal or state regulatory framework that would impair our ability to recover utility costs historically collected from our customers. In addition, inflationary cost pressures could increase the cost of constructing our utility assets and operating our utility business. Rising fuel costs could increase the cost of providing energy to our customers. In each instance, there can be no assurance that our state regulatory commissions will authorize recovery of these rising costs. In addition to the recovery of our utility costs, our profitability is impacted by the authorized return on equity, which can be impacted by macroeconomic factors such as interest rates. There can be no assurance that our state utility commissions or the FERC will authorize an acceptable rate of return.
An adverse decision by one or more regulatory authorities concerning the level or method of determining electric utility rates, the authorized returns on equity, recoverability of fuel, purchase power and other costs, the allocation of costs between jurisdictions, approval of depreciation rates, implementation of enforceable federal reliability standards or other regulatory matters, permitted business activities, such as ownership or operation of nonelectric businesses, or any prolonged delay in rendering a decision in a rate or other proceeding could adversely impact our financial condition, operating results and liquidity.
Our generating facilities are subject to risks that could result in early closure or a sale of our interest.
Changes in operational or economic factors, environmental regulation or risks of litigation could result in the early closure of, or the sale of our interest in, a generating facility. In the event of an early closure, a significant asset impairment charge could be required and we would be obligated to pay for costs of closure for our share of the generating facility, including costs associated with decommissioning, remediation, reclamation and restoration of the property, and any costs of terminating contracts associated with the generating facility, such as coal supply arrangements. In the event of a sale of our interest in a generating facility, we may not be able to negotiate the sale on favorable terms, which could result in the recognition of a loss on the sale and other potential liabilities. There can be no assurance that we would be authorized by any or all of our state utility commissions to recover any costs or losses associated with the early closure of or sale of our interest in a generating facility.
The loss of a major generating facility would require OTP to identify and receive approval for other sources of generation for its customers, if available, and expose it to higher purchased power costs. In addition, OTP may not be able to obtain timely regulatory approval for new generation resources to replace closed facilities.
In September 2021, our IRP filed in the three jurisdictions in which we operate outlined our plan to withdraw from our 35 percent ownership interest in Coyote Station, a jointly owned coal fired generation plant, by December 31, 2028. We will seek to recover all costs related to the future withdrawal from Coyote Station, however, there can be no assurance that we will be granted recovery of any or all such costs. A full or partial denial of recovery of the costs of withdrawal could significantly impact our operating results, financial condition and liquidity.
Federal and state environmental regulation could require us to incur substantial capital expenditures and increased operating costs or make it no longer economically viable to operate some of our facilities.
We are subject to federal, state and local environmental laws and regulations relating to air quality, water quality, waste management, natural resources and health safety. These laws and regulations regulate the modification and operation of existing facilities, the construction and operation of new facilities and the proper storage, handling, cleanup and disposal of hazardous waste and toxic substances. Compliance with these legal requirements requires us to commit significant resources and funds toward environmental monitoring, installation and operation of pollution control equipment, payment of emission fees and securing environmental permits. Obtaining environmental permits can entail significant expense and cause substantial construction delays. Failure to comply with environmental laws and regulations, even if caused by factors beyond our control, may result in civil or criminal liabilities, penalties and fines.
Coyote Station, one of OTP's jointly owned coal fired power plant, is subject to assessment under the second implementation period of RHR as part of the state of North Dakota's state implementation plan. We cannot predict with certainty the impact the state implementation plan may have on our business until the plan has been approved or otherwise acted on by the EPA. However, significant emission control investments could be required. Alternatively, investments in emission control equipment may prove to be uneconomic and result in an early closure of, or the sale of our interest in, Coyote Station.
Existing environmental laws or regulations may be revised, and new laws or regulations may be adopted or become applicable to us. The multiple jurisdictions that govern our electric utility business may not agree as to the appropriate resource mix, which may lead to costs to comply with one jurisdiction that are not recoverable across all jurisdictions served by the same assets. Revised or additional regulations, which result in increased
compliance costs or additional operating restrictions, particularly if those costs are not fully recoverable from customers, could have a material effect on our operating results and make it no longer economically viable to operate some of our facilities.
Legislation, regulation, litigation or other actions related to climate change and greenhouse gas emissions could materially impact us.
Current and future federal, state, regional and international regulations to address global climate change and reduce GHG emissions, including measures such as mandated levels of renewable generation, mandatory reductions in CO2 emission levels, taxes on CO2 emissions or cap-and-trade regimes, could require us to incur significant costs, which could negatively impact our financial condition, operating results and liquidity if such costs cannot be recovered through rates granted by ratemaking authorities or through increased market prices for electricity.
In 2021, the Biden Administration introduced new targets aimed at reducing economy-wide net GHG emissions by 50 to 52 percent from 2005 levels by 2030. In addition, the Administration set a goal to reach 100 percent carbon pollution-free electricity by 2035. To achieve these targets the Administration may implement new regulations targeting GHG emissions from existing fossil fuel-fired power plants. While the precise nature and implications of any new regulations are uncertain, such regulations could impose substantial costs on and impact the operations of our utility business, which may materially impact our financial condition, operating results and liquidity.
In addition to complying with legislation and regulation, we could be subject to litigation related to climate change. Costs of such litigation could be significant, and an adverse outcome could require substantial capital expenditures, changes in operations and possible payment of penalties or damages which could affect our operating results and liquidity if the costs are not recoverable in rates or covered by insurance.
To the extent investors view climate change, fossil fuel combustion and GHG emissions as a financial risk, our stock price or our ability to access capital markets on favorable terms and conditions could be adversely impacted.
Violations of extensive legal and regulatory compliance requirements could have a negative impact on our business and results of operations.
We are subject to an extensive legal and regulatory framework imposed under federal and state laws and regulatory agencies, including the FERC and the NERC. We could be subject to potential financial penalties for compliance violations. Our transmission systems and electric generation facilities are subject to the NERC mandatory reliability standards, including cybersecurity standards. If a serious reliability incident did occur, it could have a material effect on our operations or financial results. Some states have the authority to impose substantial penalties in the event of non-compliance. We attempt to mitigate the risk of regulatory penalties through formal training. However, there is no guarantee our compliance program will be sufficient to ensure against violations.
In addition, energy policy initiatives at the state or federal level could increase incentives for distributed generation or authorize municipal utility formation or acquisition of service territory, or local initiatives could introduce generation or distribution requirements that could change the current integrated utility model.
These laws and regulations significantly influence our operations and may affect our ability to recover costs from our customers. We are required to have numerous permits, licenses, approvals and certificates from the agencies and other organizations that regulate our business. We believe we have obtained the necessary approvals for our existing operations and that our business is conducted in accordance with applicable laws and regulatory requirements; however, we are unable to predict the impact on our operating results from the future regulatory activities of any of these agencies and other organizations. Changes in regulations or the imposition of additional regulations could have a material adverse impact on our results of operations.
Our transmission and generation facilities could be vulnerable to cyber and physical attack.
OTP owns electric transmission and generation facilities subject to mandatory and enforceable standards advanced by the NERC. These bulk electric system facilities provide the framework for the electrical infrastructure of OTP’s service territory and interconnected systems, the operation of which is dependent on information technology systems. Further, the information systems that operate OTP’s electric system are interconnected to external networks. Parties that wish to disrupt the U.S. bulk power system or OTP’s operations could view OTP’s computer systems, software or networks as attractive targets for cyber-attack.
In addition, OTP’s generation and transmission facilities are spread throughout a large service territory. These facilities could be subject to physical attack or vandalism that could disrupt OTP’s operations or conceivably the regional or U.S. bulk power system.
OTP is subject to mandatory cybersecurity and physical security regulatory requirements. OTP implements the NERC standards for operating its transmission and generation assets and stays abreast of best practices within business and the utility industry to protect its computers and computer-controlled systems from outside attack. We rely on industry accepted security measures and technology to securely maintain confidential and proprietary information necessary for the operation of our systems. In an effort to reduce the likelihood and severity of cyber intrusions, we have cybersecurity processes and controls and disaster recovery plans designed to protect and preserve the confidentiality, integrity and availability of data and systems. We also take prudent and reasonable steps to protect the physical security of our generation and transmission facilities. However, all these measures and technology may not adequately prevent security breaches, ransomware attacks or other cyber-attacks or enable us to recover effectively from such a breach or attack. Any significant interruption or failure of our information systems or any significant breach of security due to cyber-attacks, hacking or internal security breaches or physical attack of our generation or transmission facilities could adversely affect our business and results of operations.
Our generating facilities are subject to operational risks that could result in unscheduled plant outages and increased costs.
The operation of electric generating facilities involves many risks, including facility shutdowns due to equipment or process failures; labor disputes; operator error; catastrophic events such as fires, explosions and floods; the dependence on a specific fuel source; and the risk of performance below expected levels of output or efficiency. We could be subject to costs associated with any unexpected failure to produce or deliver power, including failures caused by a breakdown or forced outage, as well as damages to facilities.
We rely on a limited number of suppliers to provide coal and coal transportation to our facilities. A failure to perform by any of these counterparties may arise due to liquidity challenges or insolvency, operational deficiencies or other circumstances such as severe weather or natural disasters, which could impact our ability to provide service to our customers or require us to seek alternative sources for these products and services, if available, which could lead to increased costs adversely impacting our operating results.
Joint ownership of coal-fired generation facilities could impact our ability to manage changing regulations and economic conditions.
We own our coal-fired generation facilities jointly with other co-owners with varying ownership interests in such facilities. Our ability to make determinations on our integrated resource plan in order to best navigate changing environmental regulations and economic conditions may be impacted by our rights and obligations under the co-ownership agreements and related agreements and our ability to reconcile a divergence in the interests of OTP and the co-owners of these generation facilities. Such a divergence could impair our ability to effectively manage these changing conditions to meet our strategic objectives and could adversely impact our financial condition, operating results and liquidity.
We are subject to risks associated with energy markets.
Our electric business is subject to the risks associated with energy markets, including market supply and changing energy prices. If we are faced with shortages in market supply, we may be unable to fulfill our contractual obligations to our retail, wholesale and other customers at previously anticipated costs. This could force us to obtain alternative energy or fuel supplies at higher costs or suffer increased liability for unfulfilled contractual obligations. Any significantly higher than expected energy or fuel costs could negatively affect our financial performance.
MANUFACTURING SEGMENT RISKS
The price and availability of raw materials could adversely impact our operating results.
The companies in our Manufacturing segment use a variety of raw materials in the products they manufacture including, among others, steel, aluminum, and polystyrene and other plastics resins. The price and availability of the raw materials used in our manufacturing process are based on global supply and demand conditions, which can create volatile pricing and supply disruptions as conditions change. Federal trade policies, including imposed tariffs, can also impact prices for these raw materials. If we are unable to pass cost increases on to our customers or are unable to procure adequate or timely raw material inputs for use in our manufacturing processes, our operating results could be negatively impacted.
Additionally, a certain amount of residual material (scrap) is a by-product of the manufacturing and production processes used by our manufacturing companies. Declines in commodity prices for these scrap materials due to weakened demand or excess supply can negatively impact the profitability of our manufacturing companies as it reduces their ability to mitigate the cost associated with excess material.
Competition from foreign and domestic manufacturers could affect the revenues and earnings of our manufacturing businesses.
Our manufacturing businesses are subject to intense competition from foreign and domestic manufacturers, many of whom have broader product lines, greater distribution capabilities, greater capital resources, larger marketing, research and development personnel and facilities, and other capabilities. Our ability to compete on product performance, competitive pricing, technological innovation and customer service is critical to our ongoing success. If we are unable to compete in these and potentially other areas, our business and operating results could be adversely impacted.
Economic conditions in the end markets in which our customers operate could have an adverse impact on our operating results and liquidity.
Our manufacturing businesses derive a large amount of their revenues from customers in the following industry sectors: recreational vehicle/powersports, lawn and garden, construction, agriculture, energy and horticultural. Factors affecting any of these industries in general could adversely affect our operating results as growth in our operating revenues is largely dependent on the growth of our customers’ businesses in their respective industries. These factors include:
•seasonality of demand for our customers’ products, which may cause our manufacturing capacity to be underutilized for periods of time;
•our customers’ failure to successfully market their products, gain or retain widespread commercial acceptance of their products or compete effectively in their industries;
•loss of market share for our customers’ products, which may lead our customers to reduce or discontinue purchasing our products and components and to reduce prices, thereby exerting pricing pressure on us;
•economic conditions in the markets in which our customers operate; in particular, the United States, including recessionary periods such as a global economic downturn;
•our customers’ decision to bring the production of components in-house that has traditionally been outsourced to us; and
•product design changes or manufacturing process changes that may reduce or eliminate demand for the components we supply.
We expect future sales will continue to depend on the success of our customers. If economic conditions or demand for our customers’ products deteriorate, we may experience a material adverse effect on our business, operating results and financial condition.
Our business may be adversely affected if we are not able to maintain our workforce and manufacturing, engineering and technological expertise.
The markets for our manufacturing businesses are characterized by changing technology and evolving process development. The continued success of our businesses will depend on our ability to:
•hire, retain and expand our workforce, including qualified engineering and trade-skilled personnel;
•maintain technological leadership in our industry;
•implement new and expand on current robotics, automation and tooling technologies; and
•anticipate or respond to changes in manufacturing processes in a cost-effective and timely manner.
We may be unable to develop the capabilities required by our customers in the future. The emergence of new technologies, industry standards or customer requirements may render our equipment, inventory or processes obsolete or noncompetitive. We may be required to acquire new technologies and equipment to remain competitive. The acquisition and implementation of new technologies and equipment may require us to incur significant expense and capital investment, which could reduce our margins and affect our operating results. When we establish or acquire new facilities, we may not be able to maintain or develop our manufacturing, engineering and technological expertise due to a lack of trained personnel, effective training of new staff or technical difficulties with machinery. Failure to anticipate and adapt to customers’ changing technological needs and requirements, to hire and retain a sufficient number of engineers and trade-skilled personnel, and to maintain manufacturing, engineering and technological expertise may have a material adverse effect on our businesses and operating results.
Our manufacturing operations are subject to environmental, health and safety laws and regulations that could result in liabilities to us.
Our manufacturing operations, which include painting and coating processes, are subject to environmental, health and safety laws and regulations, including those governing discharges to air and water, the management and disposal of hazardous substances, the cleanup of contaminated sites and health and safety matters. We could be required to incur material costs, including cleanup costs, civil and criminal fines, penalties and third-party claims for cost recovery, property damage or personal injury as a result of violations of or liabilities under such laws and regulations. The ultimate cost of remediating contaminated sites, if any, is difficult to accurately predict and could exceed estimates. In addition, as environmental, health and safety laws and regulations have become more strict, we could incur additional costs complying with requirements that are promulgated in the future.
PLASTICS SEGMENT RISKS
Changes in PVC resin prices could negatively affect our plastics business.
The PVC pipe industry is highly sensitive to commodity raw material pricing volatility. Historically, when resin prices are rising or stable, margins and sales volume have been higher and when resin prices are falling, sales volumes and margins have been lower. Changes in PVC resin prices can negatively affect PVC pipe prices, profit margins on PVC pipe sales and the value of our finished goods inventory.
Our plastics operations are highly dependent on a limited number of vendors and a limited supply of PVC resin and other materials.
We rely on a limited number of vendors to supply the PVC resin used in our plastics business. In 2021 we sourced all of our PVC resin needs from two vendors. In addition, the supply of PVC resin may be limited primarily due to manufacturing capacity and the limited availability of raw material components. Most U.S. resin production plants are located in the Gulf Coast region. This could increase the risk of a shortage of resin in the event of a hurricane, other extreme weather events and other natural disasters in that region. The loss of a key vendor or any interruption or delay in the availability or supply of PVC resin could disrupt our ability to deliver our plastic products, cause customers to cancel orders or require us to incur additional expenses to obtain PVC resin from alternative sources, if such sources are available.
Although PVC resin is the most significant raw material input in our PVC pipe manufacturing process, we do use certain other materials, such as stabilizers, gaskets and others, in the process of manufacturing and shipping our PVC pipe products. We generally source these materials from a limited number of suppliers and any significant supply chain constraints or disruptions related to these materials could also disrupt our ability to manufacture or ship products and could result in increased costs.
We compete against many other manufacturers of PVC pipe and manufacturers of alternative products. Customers may not distinguish our products from those of our competitors.
The plastic pipe industry is fragmented and competitive due to the number of producers and the fungible nature of the product. We compete not only against other plastic pipe manufacturers, but also against ductile iron, steel and concrete pipe manufacturers. Due to shipping costs, competition is usually regional instead of national in scope and the principal areas of competition are a combination of price, service, warranty and product performance. Our inability to compete effectively in each of these areas and to distinguish our plastic pipe products from competing products may adversely affect the financial performance of our plastics business.
External factors beyond our control could cause fluctuations in demand for our PVC pipe products and changes in our prices and margins, which could adversely impact our operating results.
Our PVC pipe products, sold through distributors and wholesalers, are primarily used in municipal and rural water projects, wastewater projects, storm drainage systems and reclamation systems. External factors beyond our control can cause volatility in raw material prices, demand for our products, prices of our product and volumes and deterioration in operating margins. These factors can magnify the impact of economic cycles on our business and results of operations. Examples of external factors include:
•general economic conditions including housing and construction markets which can be cyclical;
•increases in interest rates;
•severe weather and natural disasters;
•governmental regulation in the United States;
•funding shortages for municipal water and wastewater projects can also adversely impact demand for our products; and
•pandemics and other public health threats.
GENERAL RISK FACTORS
Economic conditions could negatively impact our businesses.
Our businesses are affected by local, national and worldwide economic conditions, including the impact of inflation, tightening of credit in financial markets, economic recessions or other changes in economic conditions. Our businesses may be adversely affected by decreases in the general level of economic activity, such as decreases in business and consumer spending. A decline in the level of economic activity and uncertainty regarding
energy and commodity prices could adversely affect our results of operations and our future growth. Inflationary pressures may lead to rising material and commodity costs and increased labor costs. Our operating results and liquidity would be adversely impacted if we were unable to recover these increased costs from our customers. Tightening of credit in financial markets could adversely affect the ability of customers to finance purchases of our goods and services, resulting in decreased orders, cancelled or deferred orders, slower payment cycles, and increased bad debt and customer bankruptcies.
If we are unable to achieve the organic growth we expect, our financial performance may be adversely affected.
We expect much of our growth in the next few years will come from major capital investment at existing companies. To achieve the organic growth we expect, we must have access to the capital markets, be successful with capital expansion programs related to organic growth, develop new products and services, expand our markets and increase efficiencies in our businesses. Competitive and economic factors could adversely affect our ability to do this. If we are unable to achieve and sustain consistent organic growth, we will be less likely to meet our earnings growth targets, which may adversely affect the market price of our common shares.
| | | | | | | | | | | |
ITEM 1B. | UNRESOLVED STAFF COMMENTS | | |
None.
The following provides a summary of our properties which are material to our operations, by segment, as of December 31, 2021.
ELECTRIC SEGMENT
The following reflects our wholly or jointly owned material electric generation facilities as of December 31, 2021:
| | | | | | | | | | | | | | |
Description | Location | Year Placed in Service | Fuel Type | Capacity - kW (Nameplate Rating) |
| | | | |
Big Stone Plant(1) | Big Stone City, SD | 1975 | Subbituminous Coal | 223,146 | |
Coyote Station(2) | Beulah, ND | 1981 | Lignite Coal | 144,900 | |
Jamestown Combustion Turbine | Jamestown, ND | 1975 | Natural Gas/Oil | 48,108 | |
Lake Preston Combustion Turbine | Lake Preston, SD | 1978 | Natural Gas/Oil | 24,100 | |
Solway Combustion Turbine | Solway, MN | 2003 | Natural Gas/Oil | 44,500 | |
Astoria Station | Astoria, SD | 2021 | Natural Gas | 245,000 | |
Langdon Wind Center | Langdon, ND | 2007 | Wind | 40,500 | |
Ashtabula Wind Center | Barnes County, ND | 2008 | Wind | 48,000 | |
Luverne Wind Farm | Griggs and Steele Counties, ND | 2009 | Wind | 49,500 | |
Merricourt Wind Energy Center | McIntosh and Dickey Counties, ND | 2020 | Wind | 150,000 | |
| | | | |
(1)OTP holds a 53.9% joint ownership interest in this jointly owned facility. The nameplate capacity indicated reflects OTP's ownership percentage. |
(2)OTP holds a 35.0% joint ownership interest in this jointly owned facility. The nameplate capacity indicated reflects OTP's ownership percentage. |
In addition to our generation facilities, we wholly or jointly own transmission and distribution lines as of December 31, 2021 as follows: | | | | | |
| Miles |
| |
Transmission | |
345 kV(3) | 875 | |
230 kV(4) | 484 | |
115 kV | 960 | |
Less than 115 kV | 4,028 | |
Distribution | |
Less than 115 kV | 2,660 | |
| |
(3) As of December 31, 2021, OTP held a 14.2% ownership interest of 242 miles, a 4.8% ownership interest of 250 miles, and a 50.0% ownership interest of 234 miles of the 345 kV transmission lines, with the remaining miles being wholly-owned. |
(4) As of December 31, 2021, OTP held a 14.8% ownership interest of 70 miles of the 230 kV transmission lines, with the remaining miles being wholly-owned. |
MANUFACTURING AND PLASTICS SEGMENTS
The following reflects the material properties of our Manufacturing and Plastic segments as of December 31, 2021:
| | | | | | | | | | | |
Segment/Location | Owned/Leased | Facility Type/Use | Approximate Square Feet |
| | | |
Manufacturing Segment | | | |
Washington, IL | Leased | Office/Manufacturing/Warehouse | 217,508 | |
Detroit Lakes, MN | Owned | Office/Manufacturing/Warehouse | 353,812 | |
Lakeville, MN | Leased | Office/Manufacturing/Warehouse | 413,000 | |
Dawsonville, GA | Owned | Office/Manufacturing/Warehouse | 172,000 | |
Buford, GA | Leased | Warehouse | 71,357 | |
Clearwater, MN | Owned | Office/Manufacturing/Warehouse | 203,840 | |
Otsego, MN | Leased | Manufacturing/Warehouse | 86,400 | |
Plastics Segment | | | |
Fargo, ND | Owned | Office/Manufacturing/Warehouse | 122,441 | |
Fargo, ND | Leased | Warehouse | 239,580 | |
Phoenix, AZ | Owned | Office/Manufacturing/Warehouse | 86,066 | |
| | | |
We believe the facilities described above are adequate for our present business.
| | | | | | | | |
ITEM 3A. | INFORMATION ABOUT OUR EXECUTIVE OFFICERS | |
Set forth below is a summary of the principal occupations and business experience during the past five years of the executive officers as defined by rules of the SEC. Each of the executive officers has been employed by the Company for more than five years in an executive or management position either with the Company or its wholly owned subsidiary, Otter Tail Power Company.
| | | | | | | | |
Name and Age | Date Elected to Office | Current Position |
| | |
Charles S. MacFarlane (57) | 04/13/15 | President and Chief Executive Officer |
Kevin G. Moug (62) | 04/09/01 | Chief Financial Officer and Senior Vice President |
Timothy J. Rogelstad (55) | 04/14/14 | Senior Vice President, Electric Platform |
John S. Abbott (63) | 02/11/15 | Senior Vice President, Manufacturing Platform |
Jennifer O. Smestad (51) | 01/01/18 | Vice President, General Counsel and Corporate Secretary |
| | |
Chuck MacFarlane has served as the Company’s President and Chief Executive Officer and as a member of the Company’s board of directors since April 13, 2015.
Kevin Moug has served as Chief Financial Officer and Senior Vice President of the Company since April 9, 2001.
Timothy Rogelstad has served as President of OTP and Senior Vice President, Electric Platform of the Company since April 14, 2014.
John Abbott has served as Senior Vice President, Manufacturing Platform, since February 5, 2015.
Jennifer Smestad was appointed to the position of Vice President, General Counsel and Corporate Secretary of the Company, effective January 1, 2018. Ms. Smestad joined the Company on May 14, 2001 as an Associate General Counsel and has served in various legal capacities of increasing responsibility at the Company and at OTP. She most recently served as General Counsel for OTP from March 1, 2013 to the present.
The term of office for each of the executive officers is one year and any executive officer elected may be removed by the vote of the board of directors at any time during the term. There are no family relationships between any of the executive officers or directors.
| | | | | | | | | | | |
ITEM 4. | MINE SAFETY DISCLOSURES | | |
Not Applicable.
PART II
| | | | | |
ITEM 5. | MARKET FOR THE REGISTRANT'S COMMON EQUITY, RELATED STOCKHOLDER MATTERS AND ISSUER PURCHASES OF EQUITY SECURITIES |
Our common stock is traded on the Nasdaq Global Select Market under the Nasdaq symbol “OTTR”. As of December 31, 2021, there were approximately 12,038 holders of record of our common stock.
We do not have a publicly announced stock repurchase program and we did not repurchase any equity securities during the year ended December 31, 2021.
PERFORMANCE GRAPH COMPARISON OF FIVE-YEAR CUMULATIVE TOTAL RETURN
This graph compares the cumulative total shareholder return on our common shares for the last five years with the cumulative return of The Nasdaq Stock Market Index and the Edison Electric Institute (EEI) Index over the same period (assuming the investment of $100 in each vehicle on December 31, 2016, and reinvestment of all dividends).
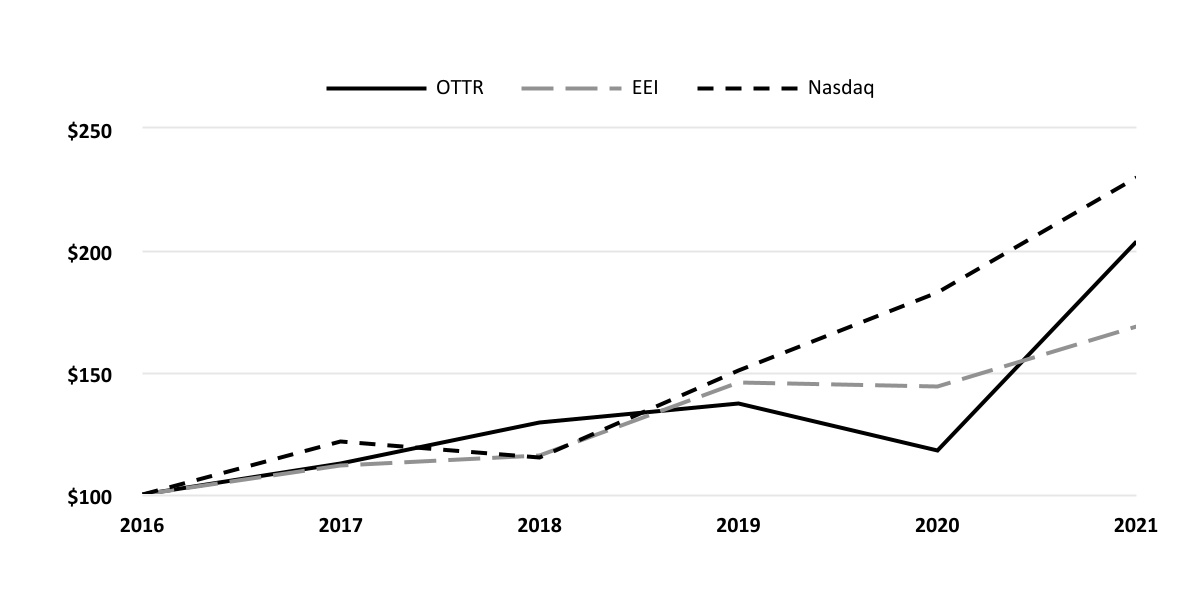
| | | | | | | | | | | | | | | | | | | | | | | | | | | | | | | | | | | |
| 2016 | | 2017 | | 2018 | | 2019 | | 2020 | | 2021 |
| | | | | | | | | | | |
OTTR | $ | 100.00 | | | $ | 112.35 | | | $ | 129.14 | | | $ | 137.12 | | | $ | 117.96 | | | $ | 203.57 | |
EEI | $ | 100.00 | | | $ | 111.72 | | | $ | 115.82 | | | $ | 145.69 | | | $ | 144.00 | | | $ | 168.64 | |
Nasdaq | $ | 100.00 | | | $ | 121.38 | | | $ | 114.77 | | | $ | 150.55 | | | $ | 182.57 | | | $ | 229.84 | |
| | | | | | | | | | | |
| | | | | |
ITEM 7. | MANAGEMENT'S DISCUSSION AND ANALYSIS OF FINANCIAL CONDITION AND RESULTS OF OPERATIONS |
You should read the following discussion and analysis of our financial condition and results of operations together with our financial statements and the related notes appearing under Item 8 of this Form 10-K. Otter Tail Corporation (OTC) and its subsidiaries form a diverse group of businesses with operations classified into three segments: Electric, Manufacturing and Plastics. Our Electric business is a vertically integrated, regulated utility with generation, transmission and distribution facilities to serve our customers in western Minnesota, eastern North Dakota and northeastern South Dakota. Our Manufacturing segment provides metal fabrication for custom machine parts and metal components and manufactures extruded and thermoformed plastic products. Our Plastics segment manufactures PVC pipe for use in, among other applications, municipal and rural water, wastewater and water reclamation projects.
Our strategy includes investing in rate base growth opportunities in our Electric segment and capitalizing on organic growth opportunities in our Manufacturing and Plastics segments. Investments in our Electric segment are expected to produce increased earnings and cash flow potential and lower our overall risk, create a more predictable earnings stream, improve our credit quality and preserve our ability to fund our dividend. Our Electric segment is complemented by our Manufacturing and Plastics segment businesses, which we expect to contribute to earnings growth by capitalizing on market expansion opportunities and increasing utilization of existing capacities and planned investments to create additional capacity and increased efficiencies. Collectively, our mix of businesses is expected to contribute to the achievement of our targeted annual growth in earnings per share of five to seven percent over the next several years, using 2020 as the base for measurement.
In 2021, all of our businesses were able to effectively manage through the challenges resulting from the COVID-19 pandemic and other marketplace challenges, including supply chain disruptions and rapidly escalating costs for certain raw material components used in our manufacturing processes. We continue to remain focused on maintaining the health and safety of our employees, customers and communities and ensuring continued electrical reliability and continuous delivery of our products to our customers.
2021 FINANCIAL RESULTS
Our Electric segment produced earnings growth of 8.5% in 2021, driven by returns on our recent rate base investments. Our Merricourt wind farm and Astoria Station natural gas plant, which collectively constitute a $420 million investment, were completed and placed in service in the fourth quarter of 2020 and the first quarter of 2021, respectively. Recovery of these investments and associated operating costs through either rate riders or interim rates provided under our Minnesota rate case led to increasing operating revenues and net income.
Our Manufacturing segment produced earnings growth in 2021 of 55.6%, as strong end market demand across most of the markets we serve led to increased sales volumes. Higher production volumes to meet customer demand led to improved leveraging of fixed manufacturing costs which, along with increased prices, led to improved gross profit levels. Our Manufacturing segment was impacted in 2021 by steel supply constraints and a significant increase in steel prices, as further discussed below.
Our Plastics segment produced earnings of $97.8 million in 2021, compared to $27.6 million in 2020. The unprecedented level of earnings in 2021 resulted from extraordinary industry supply and demand dynamics. As further described below, supply shortages of resin, the primary raw material used in the manufacturing of PVC pipe, coupled with robust end market demand for PVC pipe led to a rapid escalation in PVC pipe prices and gross margins. Our ability to manage through these supply disruptions and to deliver products to our customers allowed us to capitalize on these unique industry conditions.
Collectively in 2021, our businesses generated net income of $176.8 million, or $4.23 per diluted share, an increase of 84.4% from $95.9 million, or $2.34 per diluted share, in 2020. In 2021, we paid an annual dividend of $1.56 per share, or $64.9 million, completing our 83rd consecutive year of dividend payments to our shareholders.
Our earnings mix in 2021 was 41% from our Electric segment and 59% from the combination of our Manufacturing and Plastics segments net of unallocated corporate costs. Electric segment earnings as a percentage of our total earnings were less than our long-term estimate of 70% due to the unique market conditions that occurred in our Plastics segment. We expect our earnings mix to return back to our expected 70% from our Electric segment and 30% from our Manufacturing and Plastics segments over the long term as the conditions within the Plastics' industry subside.
RESOURCE MATERIAL AVAILABILITY AND PRICING
Supply shortages and the cost of steel and resin, two key material inputs to our Manufacturing and Plastics segments, respectively, significantly impacted our operating results in 2021.
Steel supply shortages arose in 2021 following steel mill capacity reductions in 2020 in response to lower demand due to COVID-19. Production and availability of steel began to improve late in 2021 after steel mill facilities increased production capacities in response to strong market demand for steel products. The combination of supply shortages and strong end user demand led to significantly increased steel prices. The increase in steel prices led to increased sale prices for our products at BTD, our metal fabrication business within our Manufacturing segment, as we passed along material cost increases to our customers. Limited steel availability also heightened the complexity in managing our business, including effective management of our production and shipping schedules. Steel costs began to recede late in 2021, but we anticipate steel prices will remain elevated relative to historic norms through at least the first half of 2022.
PVC resin is the primary material input of the PVC pipe manufactured by our Plastics segment businesses. Resin supply disruptions initially arose as a result of production plant shutdowns due to abnormally low temperatures and ice storms in the Gulf Coast region of the United States in the first quarter of 2021 and were exacerbated by hurricane activity in the third quarter of the year. These supply disruptions, along with robust domestic and global demand for PVC resin led to significantly increased resin prices.
Limited PVC resin resulted in reduced manufacturing of PVC pipe and low pipe inventories across the industry. The combination of constrained PVC resin supply and the resulting low PVC pipe inventories along with significantly increased PVC resin costs and robust demand for PVC pipe led to rapidly increasing sale prices for PVC pipe, with the increase in sale prices outpacing the increase in PVC resin costs, leading to expanding gross profit margins and a significant increase in earnings in our Plastics segment. We anticipate these market dynamics will continue through the first quarter of 2022 but begin to subside thereafter.
The marketplace dynamics impacting both our Manufacturing and Plastics segments are fluid and subject to change which may impact our operating results prospectively.
COVID-19
We continue to monitor the progression of COVID-19 and its impact on our business. As this pandemic continues, we are following the directives and advice of government leaders and medical professionals and have adopted practices to help curtail the spread of the virus and mitigate its impact on our employees, customers, vendors and other business partners, and communities in which we live and work.
While the impact of COVID-19 and the resulting macroeconomic conditions did not materially impact our operating results in 2021, uncertainty remains regarding the magnitude and duration of the pandemic and the resulting potential future financial effects. Increased infection rates and any future responses to mitigate the spread of the virus, including any potential vaccination mandates that would apply to our employees, could impact our business and our financial results in future periods.
OSHA has issued an ETS requiring all employers with at least 100 employees to ensure their employees are fully vaccinated or require weekly testing for unvaccinated employees, and President Biden has issued an executive order, which requires employees of certain federal contractors
and covered subcontractors to be vaccinated, with no weekly testing option, unless they have an approved disability or religious exemption. OSHA has withdrawn its ETS, however, they have emphasized that the ETS will continue to serve as its proposal for a permanent standard. Currently, the mandate set forth by the President's executive order has been halted as several states are challenging its legality and the matter remains in litigation. If these mandates are upheld in federal court and become effective, we expect one, or both, of these new regulations will apply to at least some, and possibly all, of our businesses which could require us to mandate COVID-19 vaccination of our workforce or have our unvaccinated employees undergo required weekly COVID-19 testing, or some combination thereof, which could be difficult and costly. Further, additional vaccine and testing mandates may be announced in jurisdictions in which we operate our business, and there could be potential actions by certain states that are in conflict with the federal mandates, the impacts of which remain uncertain. Requirements to mandate COVID-19 vaccination of our workforce or requirements of our unvaccinated employees to be tested could result in labor disruptions, employee attrition and difficulty securing future labor needs.
We continue to monitor developments involving our workforce, customers, construction contractors, suppliers and vendors and the financial effects on our business. However, due to the unprecedented and evolving nature of this pandemic, we cannot predict the full extent of the impact COVID-19 will have on our operating results, financial condition and liquidity.
| | | | | |
FINANCIAL AND OTHER METRICS | |
Heating Degree Days (HDDs) is a measure of how much (in degrees), and for how long (in days), the outside air temperature was below a certain normalized level. This measure is commonly used in calculations relating to the energy consumption required to heat buildings.
Cooling Degree Days (CDDs) is a measure of how much (in degrees), and for how long (in days), the outside air temperature was above a certain normalized level. This measure is commonly used in calculations relating to the energy consumption required to cool buildings.
Otter Tail Power Company (OTP) generally bases its forecasted kilowatt-hour (kwh) sales and rates on expected consumption under a normal level of HDDs and CDDs over a given period of time in its service territory. Increased or decreased levels of consumption for certain customer classifications are attributed to deviation from the norms and are a significant factor influencing consumption of electricity across our service territory. We present HDDs and CDDs to provide an indication of the impact of weather on kwh sales, revenues and earnings relative to forecast and on period-to-period results.
Utility Rate Base is the value of property on which a public utility is permitted to earn a specified rate of return in accordance with rules set by a regulatory agency. In general, rate base consists of the value of property used by the utility in providing service. Rate base can also include: cash, working capital, materials and supplies, deductions for accumulated provisions for depreciation, contributions in aid of construction, customer advances for construction, accumulated deferred income taxes, and accumulated deferred investment tax credits, dependent on the method that is used in the calculation, which can vary from jurisdiction to jurisdiction. We present actual and forecasted levels of utility rate base to provide an indication of expected investments on which we expect to earn future returns.
For a comparison of fiscal year 2020 to 2019, see Part II, Item 7 “Management’s Discussion and Analysis of Financial Condition and Results of Operations” in our report on Form 10-K for the fiscal year ended December 31, 2020, filed with the SEC on February 19, 2021 and incorporated by reference into this report on Form 10-K. Provided below is a summary and discussion of our operating results on a consolidated basis followed by a discussion of the operating results of each of our segments, Electric, Manufacturing and Plastics. Intersegment transactions were not material in 2021 or 2020 and amounted to less than $0.1 million of operating revenues and operating expenses for each year. In addition to the segment results, we provide an overview of our Corporate costs. Our Corporate costs do not constitute a reportable segment but rather consist of unallocated general corporate expenses, such as corporate staff and overhead costs, the results of our captive insurance company and other items excluded from the measurement of segment performance. Corporate costs are added to operating segment totals to reconcile to totals on our consolidated statements of income.
CONSOLIDATED RESULTS
The following table summarizes our consolidated results of operations for the years ended December 31, 2021 and 2020:
| | | | | | | | | | | | | | | | | | | | | | | |
(in thousands) | 2021 | | 2020 | | $ change | | % change |
| | | | | | | |
Operating Revenues | $ | 1,196,844 | | | $ | 890,107 | | | $ | 306,737 | | | 34.5 | % |
Operating Expenses | 947,136 | | | 742,221 | | | 204,915 | | | 27.6 | |
Operating Income | 249,708 | | | 147,886 | | | 101,822 | | | 68.9 | |
Interest Charges | 37,771 | | | 34,447 | | | 3,324 | | | 9.6 | |
Nonservice Cost Components of Postretirement Benefits | 2,016 | | | 3,437 | | | (1,421) | | | (41.3) | |
Other Income | 2,900 | | | 6,055 | | | (3,155) | | | (52.1) | |
Income Before Income Taxes | 212,821 | | | 116,057 | | | 96,764 | | | 83.4 | |
Income Tax Expense | 36,052 | | | 20,206 | | | 15,846 | | | 78.4 | |
Net Income | $ | 176,769 | | | $ | 95,851 | | | $ | 80,918 | | | 84.4 | % |
Operating Revenues increased $306.7 million on a consolidated basis in 2021. Each operating segment contributed to the growth in operating revenues. Electric segment operating revenue increased 7.7% primarily due to increased retail, transmission and wholesale revenues. Manufacturing segment operating revenues increased 40.8% mainly as a result of higher material input costs, primarily steel, which are passed
through to customers, and increased volumes due to strong end market demand. Plastics segment operating revenues increased 85.3% primarily due to unique supply and demand dynamics resulting from resin supply constraints coupled with robust demand for PVC pipe leading to rapid and significant increases in sale prices of PVC pipe. See our segment disclosures below for additional discussion of items impacting operating revenues.
Operating Expenses increased $204.9 million in 2021. Electric segment operating expenses increased 10.1% primarily due to increased production fuel and purchased power costs along with incremental operating costs and depreciation expense rising from our recent rate base investments. Operating expenses in our Manufacturing segment increased 40.2%, driven by increased cost of products sold, which resulted from higher material input costs and increased sales volumes, and increased other operating expenses. Operating expenses in our Plastics segment increased 47.8% primarily due to higher costs of products sold from higher resin inputs costs. See our segment disclosures below for additional discussion of items impacting operating expenses.
Interest Charges increased $3.3 million in 2021 due to a $40.0 million long-term debt issuance in August 2020, a higher level of short-term debt borrowings outstanding in 2021 and a lower level of capitalized interest due to the completion and placement in service of Astoria Station in the first quarter of 2021. The increase in our short- and long-term debt borrowings were largely used to finance the rate base investments in our Electric segment.
Nonservice Cost Components of Postretirement Benefits decreased $1.4 million in 2021 mostly due to a decrease in nonservice costs of our postretirement healthcare plan reflecting the effect of plan amendments adopted in 2020 and 2019.
Other Income decreased $3.2 million in 2021 due to a reduction of allowance for equity funds used during construction (AFUDC) on Electric segment investments, mainly for the Minnesota share of Astoria Station. Astoria Station was placed into service, and the recognition of AFUDC discontinued, in the first quarter of 2021.
Income Tax Expense increased $15.8 million in 2021 primarily due to an increase in income before income taxes, but partially offset by an increase in production tax credits generated from our Merricourt wind farm, which was placed in service in the fourth quarter of 2020. Our effective tax rate was 16.9% in 2021 and 17.4% in 2020. See Note 12 to our consolidated financial statements included in the report on Form 10-K for additional information regarding factors impacting our effective tax rate. ELECTRIC SEGMENT RESULTS
The following table summarizes the operating results of our Electric segment for the years ended December 31, 2021 and 2020:
| | | | | | | | | | | | | | | | | | | | | | | |
(in thousands) | 2021 | | 2020 | | $ change | | % change |
| | | | | | | |
Retail Sales Revenue | $ | 405,484 | | | $ | 389,522 | | | $ | 15,962 | | | 4.1 | % |
Transmission Services Revenues | 48,835 | | | 44,001 | | | 4,834 | | | 11.0 | |
Wholesale Revenues | 17,936 | | | 4,857 | | | 13,079 | | | 269.3 | |
Other Electric Revenues | 8,066 | | | 7,750 | | | 316 | | | 4.1 | |
Total Operating Revenue | 480,321 | | | 446,130 | | | 34,191 | | | 7.7 | |
Production Fuel | 59,327 | | | 46,296 | | | 13,031 | | | 28.1 | |
Purchased Power | 65,409 | | | 61,698 | | | 3,711 | | | 6.0 | |
Operating and Maintenance Expenses | 159,669 | | | 150,848 | | | 8,821 | | | 5.8 | |
Depreciation and Amortization | 71,343 | | | 63,171 | | | 8,172 | | | 12.9 | |
Property Taxes | 17,609 | | | 17,034 | | | 575 | | | 3.4 | |
Operating Income | $ | 106,964 | | | $ | 107,083 | | | $ | (119) | | | (0.1) | % |
| | | | | | | |
Electric kilowatt-hour (kwh) Sales (in thousands) | | | | | | | |
Retail kwh Sales | 4,789,879 | | | 4,776,687 | | | 13,192 | | | 0.3 | % |
Wholesale kwh Sales | 420,044 | | | 236,528 | | | 183,516 | | | 77.6 | |
Heating Degree Days | 5,794 | | | 6,174 | | | (380) | | | (6.2) | |
Cooling Degree Days | 704 | | | 534 | | | 170 | | | 31.8 | |
| | | | | | | |
Our Electric segment operating results are impacted by fluctuations in weather conditions and the resulting demand for electricity for heating and cooling. The following table presents heating and cooling degree days as a percent of normal for the years ended December 31, 2021 and 2020:
| | | | | | | | | | | |
| 2021 | | 2020 |
| | | |
Heating Degree Days | 91.3 | % | | 97.2 | % |
Cooling Degree Days | 151.7 | % | | 116.3 | % |
| | | |
The following table summarizes the estimated effect on diluted earnings per share of the difference in retail kwh sales under actual weather conditions and expected retail kwh sales under normal weather conditions for the years ended December 31, 2021 and 2020, and between years:
| | | | | | | | | | | | | | | | | |
| 2021 vs Normal | | 2021 vs 2020 | | 2020 vs Normal |
| | | | | |
Effect on Diluted Earnings Per Share | $ | 0.01 | | | $ | 0.01 | | | $ | — | |
| | | | | |
Retail Revenues increased $16.0 million primarily due to the following:
•An $8.1 million increase in fuel recovery revenues primarily resulting from increased production fuel and purchase power costs, both of which were impacted by increasing natural gas prices throughout most of 2021. Partially offsetting this increase are credits provided to retail customers from increased margins recognized on wholesale sales.
•A $6.6 million increase in rider revenues in our North Dakota and South Dakota jurisdictions primarily to recover our investments in and costs to operate Merricourt and Astoria Station.
•A $5.0 million increase in new retail revenues from an interim rate increase in Minnesota, net of estimated refunds.
These increases in retail revenue were partially offset by the impact of reduced demand, exclusive of the impact of weather, from residential customers, and net of the effect of a change in customer usage mix. In addition, retail revenue in 2020 benefited from the recognition of $2.6 million of Minnesota transmission rider revenue resulting from a favorable judicial decision regarding the state jurisdictional treatment of federally approved transmission projects.
Transmission Services Revenues increased $4.8 million primarily due to increased recovery of higher transmission costs and increased transmission investment along with increased generator interconnection revenues.
Wholesale Revenues increased $13.1 million as a result of a 77.6% increase in wholesale sales volumes and a 107.9% increase in wholesale prices driven by increased fuel costs and market demand for wholesale energy, which serves to drive up spot market prices for electricity.
Production Fuel costs increased $13.0 million as a result of a 16.9% increase in kwhs generated from our fuel-burning plants, largely driven by output from Astoria Station after energy generation commenced in April of 2021.
Purchased Power costs increased $3.7 million due to a 27.9% increase in the cost per kwh purchased in 2021. This increase was partially offset by a 17.1% decrease in the volume of purchased power in 2021 as our recent generation additions provide additional generation resources to serve customer demand and market conditions led to operating our facilities at higher capacity factors in lieu of purchasing power at higher market prices.
Operating and Maintenance Expense increased $8.8 million mainly due to:
•A $5.2 million increase in operating and maintenance costs for Merricourt and Astoria Station as these facilities were placed in service in the fourth quarter of 2020 and the first quarter of 2021, respectively.
•A $4.0 million increase in Big Stone plant maintenance costs arising from our planned facility outage, which began in the third quarter and was completed in the fourth quarter of 2021.
•Other additional costs including a $2.2 million increase in transmission tariff expenses and increases in information technology services, insurance costs and increased vegetative maintenance costs.
These expense increases were partially offset by, among other items, a $3.0 million reduction in bad debt expense as customer collections have improved from 2020, which were negatively impacted by the economic effects of COVID-19, along with lower operating costs following the closure of Hoot Lake Plant in May 2021.
Depreciation and Amortization expense increased $8.2 million primarily due to Merricourt and Astoria Station being placed in service in the fourth quarter of 2020 and the first quarter of 2021, respectively.
MANUFACTURING SEGMENT RESULTS
The following table summarizes operating results of our Manufacturing segment for the years ended December 31, 2021 and 2020:
| | | | | | | | | | | | | | | | | | | | | | | |
(in thousands) | 2021 | | 2020 | | $ change | | % change |
| | | | | | | |
Operating Revenues | $ | 336,294 | | | $ | 238,769 | | | $ | 97,525 | | | 40.8 | % |
Cost of Products Sold | 259,581 | | | 180,432 | | | 79,149 | | | 43.9 | |
Other Operating Expenses | 37,163 | | | 27,301 | | | 9,862 | | | 36.1 | |
Depreciation and Amortization | 15,436 | | | 14,933 | | | 503 | | | 3.4 | |
Operating Income | $ | 24,114 | | | $ | 16,103 | | | $ | 8,011 | | | 49.7 | % |
Operating Revenues increased $97.5 million primarily due to the following:
•At BTD, operating revenues increased $91.3 million. Parts revenue increased $78.4 million, primarily due to a 31.2% increase in material costs, which are passed through to customers, as steel prices increased significantly from the previous year. Steel prices increased during the year as steel mill production did not match customer demand as mill capacity recovered from shutdowns in 2020 resulting from the COVID-19 pandemic. Sales volumes increased 6.8% in 2021 from increased and robust end market demand across most markets served. Demand in 2020 was impacted by COVID-19 after certain customers implemented temporary plant shutdowns in response to the pandemic. A $7.3 million increase in scrap revenues, with $5.9 million due to higher scrap metal prices and $1.4 million attributable to higher volumes, also contributed to the increase in operating revenues.
•At T.O. Plastics, revenues increased $6.2 million, primarily due to a 12.5% increase in sales volumes as well as 5.6% increase in sale prices. Increases in horticultural product sales volumes due to strong customer demand during the year were partially offset by decreases in sales to other end market customers. Sales volumes in 2020 were impacted by the COVID-19 pandemic, as certain end markets experienced reduced demand.
Cost of Products Sold increased $79.1 million due to the following:
•Cost of products sold at BTD increased $76.6 million as a result of both increased material costs and higher sales volumes. Increased gross profit margins resulting from a higher leveraging of fixed costs due to increased sales volumes were partially offset by lower productivity and increased labor and freight costs. The lower level of productivity during the year was primarily the result of increased staffing levels to meet higher business volumes and the time required for new employees to achieve peak productivity.
•Cost of products sold at T.O. Plastics increased $3.2 million primarily due to increased sales volumes. Gross profit margins increased as a result of a higher leveraging of fixed costs due to increased sales volumes and better pricing spreads.
Other Operating Expenses increased $9.9 million due to increased staffing levels and associated recruitment costs, travel costs, incentive based compensation and other costs resulting from higher business volumes.
PLASTICS SEGMENT RESULTS
The following table summarizes operating results for our Plastics segment for the years ended December 31, 2021 and 2020:
| | | | | | | | | | | | | | | | | | | | | | | |
(in thousands) | 2021 | | 2020 | | $ change | | % change |
| | | | | | | |
Operating Revenues | $ | 380,229 | | | $ | 205,249 | | | $ | 174,980 | | | 85.3 | % |
Cost of Products Sold | 228,789 | | | 148,835 | | | 79,954 | | | 53.7 | |
Other Operating Expenses | 14,326 | | | 14,987 | | | (661) | | | (4.4) | |
Depreciation and Amortization | 4,354 | | | 3,604 | | | 750 | | | 20.8 | |
Operating Income | $ | 132,760 | | | $ | 37,823 | | | $ | 94,937 | | | 251.0 | % |
Operating Revenues increased $175.0 million primarily due to unique supply and demand dynamics during the year. The average price per pound of PVC pipe sold in 2021 increased 82.1% compared to 2020, which exceeded the 65.5% increase in the cost of PVC resin and other input materials. The increase in sale prices was largely due to the combination of PVC resin supply constraints, which limited PVC pipe manufacturing output and led to extremely low inventory levels, and strong demand for PVC pipe products. Resin supply was negatively impacted during the year by production disruptions caused by extreme weather events in the Gulf Coast region of the U.S. in the first and third quarters of the year. Pounds of pipe sold in 2021 increased 1.7% compared to the previous year.
Cost of Products Sold increased $80.0 million primarily due to the increase in the cost per pound of PVC pipe sold largely due to higher material input costs.
Other Operating Expenses decreased $0.7 million. In 2020, our Plastics businesses made a $2.0 million contribution commitment to OTC’s charitable foundation, and no such contribution commitment was made in 2021. The decrease in foundation contributions was partially offset by an increase in variable costs associated with the increased financial results in 2021.
CORPORATE COSTS
The following table summarizes Corporate results of operations for the years ended December 31, 2021 and 2020:
| | | | | | | | | | | | | | | | | | | | | | | |
(in thousands) | 2021 | | 2020 | | $ change | | % change |
| | | | | | | |
Other Operating Expenses | $ | 13,905 | | | $ | 12,794 | | | $ | 1,111 | | | 8.7 | % |
Depreciation and Amortization | 225 | | | 329 | | | (104) | | | (31.6) | |
Operating Loss | $ | 14,130 | | | $ | 13,123 | | | $ | 1,007 | | | 7.7 | % |
Other Operating Expenses increased $1.1 million primarily due to increased labor and benefit costs as well as a $3.0 million contribution commitment to OTC’s charitable foundation in 2021, compared to a $2.5 million commitment in the previous year.
The following provides a summary of our current general rates and a summary of recent rate case filings and rate rider filings that have or are expected to have a material impact on our operating results, financial position or cash flows.
GENERAL RATES
The following includes a summary of electric base rates as determined in OTP's most recent general rate case in each state:
| | | | | | | | | | | | | | | | | |
| | Revenue | | Allowed | |
| Implementation | Requirement | Return on | Return | Equity |
Jurisdiction | Date | (in millions) | Rate Base | on Equity | Ratio |
| | | | | |
Minnesota | 06/01/19 | $ | 198.6 | | 7.51 | % | 9.41 | % | 52.50 | % |
North Dakota | 02/01/19 | 153.1 | | 7.64 | | 9.77 | | 52.50 | |
South Dakota(1) | 08/01/19 | 35.5 | | 7.09 | | 8.75 | | 52.92 | |
| | | | | |
(1) Includes an earnings sharing mechanism to share with South Dakota customers any weather-normalized earnings above the authorized ROE of 8.75%. The mechanism requires annual customer refunds of 50% of any weather-normalized revenue creating earnings in excess of the authorized ROE up to a maximum of 9.50% and 100% refunds revenue creating earnings above 9.50%. | |
Minnesota Rate Case: On November 2, 2020, OTP filed a request with the MPUC for an increase in revenue recoverable through base rates in Minnesota. In its filing, OTP requested a net increase in annual revenue of approximately $14.5 million, or 6.77%, based on an allowed rate of return on rate base of 7.59% and an allowed rate of return on equity of 10.20% on an equity ratio of 52.5% of total capital. Through this proceeding, OTP has proposed changes to the mechanism of cost recovery, with some costs moving from riders into base rates and fuel, purchased power, and conservation program costs moving out of base rates and into riders. The filing also included a revenue decoupling mechanism proposal. Such mechanisms are designed to separate a utility's revenue from changes in energy sales. The decoupling mechanism uses a tracker balance through which authorized customer margins are subject to a true-up mechanism to maintain or cap a given level of revenues.
On December 3, 2020, the MPUC approved an interim annual rate increase of $6.9 million, or 3.2%, effective January 1, 2021. This approval was provided after an alternative recovery proposal was submitted by OTP, which, among other changes, requested the extension of depreciable lives of certain wind-related assets and deferred certain cost recovery decisions to the final rate determination. In the aggregate, this alternative recovery proposal reduced operating costs and delayed recovery of certain other costs by approximately $7.0 million to lessen the interim rate impact on customers.
In a filing submitted to the MPUC on April 30, 2021, OTP lowered its requested net annual revenue increase from its initial request of $14.5 million to $8.2 million, primarily due to a reduction in operating costs from amounts included in its November 2020 filing. The cost reductions include, among other items, lower depreciation expense on our wind generation assets due to the extension of depreciable lives from 25 to 35 years and a reduction in postretirement benefit costs.
On February 1, 2022, the MPUC issued its written order. The key provisions of the order include a revenue requirement of $209.0 million based on a return on rate base of 7.18%, including an allowed return on equity of 9.48% on an equity ratio of 52.5%. The order also authorizes recovery, over a five-year period, of our remaining Hoot Lake Plant net asset and approves the requested decoupling mechanism for most residential and commercial customer rate groups, with a cap of 4% of annual base revenues. Following the submission of certain compliance filings and a comment period on such filings, we expect final rates will be implemented in mid-2022.
RATE RIDERS
The following table includes a summary of pending and recently concluded rate rider proceedings:
| | | | | | | | | | | | | | | | | | | | | | | | | | | | | | | | | | | | | | |
Recovery | | | | | | Filing | | Amount | | Effective | | |
Mechanism | | Jurisdiction | | Status | | Date | | (in millions) | | Date | | Notes |
| | | | | | | | | | | | |
RRR - 2019 | | MN | | Approved | | 06/21/19 | | $ | 12.5 | | | 01/01/20 | | Includes return on Merricourt construction costs. |
TCR - 2018 | | MN | | Approved | | 05/07/20 | | 10.3 | | | 01/21/20 | | See below for additional details. |
CIP - 2021 | | MN | | Approved | | 04/01/21 | | 9.4 | | | 12/01/21 | | Includes recovery of energy conservation improvement costs as well as a demand side management financial incentive. |
CIP - 2020 | | MN | | Approved | | 05/01/20 | | 8.2 | | | 10/01/20 | | Includes recovery of energy conservation improvement costs as well as a demand side management financial incentive. |
TCR - 2021 | | MN | | Requested | | 11/23/21 | | 7.2 | | | 07/01/22 | | Includes recovery of two new transmission projects. |
RRR - 2021 | | MN | | Requested | | 12/06/21 | | 2.7 | | | 07/01/22 | | Includes return on Hoot Lake Solar construction costs and costs associated with the acquisition of the Ashtabula III wind farm. |
EUIC - 2021 | | MN | | Requested | | 06/07/21 | | 1.3 | | | 01/01/22 | | Includes recovery of new infrastructure costs, including advanced metering, outage management and demand response systems. |
RRR - 2021 | | ND | | Approved | | 03/07/21 | | 11.8 | | | 04/01/21 | | Includes recovery of Merricourt investment and operating costs. |
GCR - 2020 | | ND | | Approved | | 06/10/20 | | 6.2 | | | 07/01/20 | | Includes return on Astoria Station construction costs. |
TCR - 2021 | | ND | | Approved | | 09/15/21 | | 6.1 | | | 01/01/22 | | Includes recovery of three new transmission projects/programs. |
RRR - 2020 | | ND | | Approved | | 03/18/20 | | 5.8 | | | 04/01/20 | | Includes return on Merricourt construction costs. |
TCR - 2020 | | ND | | Approved | | 08/31/20 | | 5.7 | | | 01/21/20 | | Includes recovery of seven new transmission assets. |
TCR - 2020 | | ND | | Approved | | 11/18/20 | | 5.6 | | | 01/01/21 | | Includes recovery of eight new transmission projects. |
GCR - 2021 | | ND | | Approved | | 03/01/21 | | 5.2 | | | 07/01/21 | | Includes recovery of Astoria Station, net of anticipated savings associated with the retirement of Hoot Lake Plant. |
TCR - 2020 | | SD | | Approved | | 01/29/20 | | 2.3 | | | 03/02/20 | | Annual update to transmission cost recovery rider. |
TCR - 2021 | | SD | | Requested | | 10/29/21 | | 2.2 | | | 03/01/22 | | Annual update to transmission cost recovery rider. |
TCR - 2021 | | SD | | Approved | | 02/19/21 | | 2.2 | | | 03/01/21 | | Includes recovery of two new transmission projects. |
PIR - 2020 | | SD | | Approved | | 05/31/20 | | 1.6 | | | 09/01/20 | | Includes return on Merricourt and Astoria Station construction costs. |
| | | | | | | | | | | | |
Minnesota TCR: On May 1, 2017, the MPUC ordered OTP to include in the TCR rider retail rate base the Minnesota jurisdictional share of OTP's investments in certain transmission assets and all revenues received from other utilities under MISO's tariffed rates as a credit in its TCR revenue requirement calculations. The order had the effect of diverting interstate wholesale revenues that have been approved by the FERC to offset the FERC-approved expenses, effectively reducing OTP's recovery of FERC-approved expense levels.
On August 18, 2017, OTP filed an appeal of the MPUC order with the Minnesota Court of Appeals to contest the portion of the order requiring OTP to jurisdictionally allocate costs of the FERC transmission projects in the TCR rider. On June 11, 2018, the Minnesota Court of Appeals reversed the MPUC's order. On July 11, 2018, the MPUC filed a petition for review of the decision to the Minnesota Supreme Court, which granted review of the appellate court decision. The Minnesota Supreme Court issued its opinion on April 22, 2020, concluding the MPUC lacked authority to amend an existing TCR rider approved under Minnesota state law to include the costs and revenues associated with these transmission projects and affirming the decision of the Minnesota Court of Appeals.
On October 22, 2020, the MPUC approved OTP's request for a Minnesota TCR rider update with the exclusion of these transmission projects. In addition, the MPUC approved the inclusion of three new projects previously requested in the Minnesota TCR rider eligibility petition. Updated rates went into effect in January 2021. With this decision, one-half of the projected TCR rider tracker balance at December 2020 of $13.4 million will be included in the 2021 TCR rider annual revenue requirement, with the remainder included in the next annual update. The annual updates provide for recovery of approximately $2.6 million in MISO revenue credits to Minnesota customers through the TCR rider prior to September 30, 2020. As a result, OTP recognized additional rider revenue of $2.6 million during the third quarter of 2020.
LIQUIDITY OVERVIEW
We believe our financial condition is strong and our cash, other liquid assets, operating cash flows, existing lines of credit, access to capital markets, and borrowing ability because of investment-grade credit ratings, when taken together, provide us ample liquidity to conduct business operations and fund capital expenditures related to expansion of existing businesses and development of new projects. Our liquidity, including our operating cash flows and access to capital markets, can be impacted by macroeconomic factors outside of our control, such as those which may be caused by COVID-19. In addition, our liquidity could be impacted by non-compliance with covenants under our various debt instruments. As of December 31, 2021, we were in compliance with all debt covenants (see the Financial Covenant section under Capital Resources below).
The following table presents the status of our lines of credit as of December 31, 2021 and 2020:
| | | | | | | | | | | | | | | | | | | | | | | | | | | | | |
| | | 2021 | | 2020 |
(in thousands) | Line Limit | | Amount Outstanding | | Letters of Credit | | Amount Available | | Amount Available |
| | | | | | | | | |
Otter Tail Corporation Credit Agreement | $ | 170,000 | | | $ | 22,637 | | | $ | — | | | $ | 147,363 | | | $ | 104,834 | |
OTP Credit Agreement | 170,000 | | | 68,526 | | | 13,159 | | | 88,315 | | | 140,068 | |
Total | $ | 340,000 | | | $ | 91,163 | | | $ | 13,159 | | | $ | 235,678 | | | $ | 244,902 | |
We have an internal risk tolerance metric to maintain a minimum of $50 million of liquidity under the OTC Credit Agreement. Should additional liquidity be needed, this agreement includes an accordion feature allowing us to increase the amount available to $290 million, subject to certain terms and conditions. The OTP Credit Agreement also includes an accordion feature allowing OTP to increase that facility to $250 million, subject to certain terms and conditions.
CASH FLOWS
The following is a discussion of our cash flows for the years ended December 31, 2021 and 2020:
| | | | | | | | | | | |
(in thousands) | 2021 | | 2020 |
| | | |
Net Cash Provided by Operating Activities | $ | 231,243 | | | $ | 211,921 | |
| | | |
Net Cash Provided by Operating Activities increased $19.3 million primarily due to a $80.9 million increase in net income, but partially offset by an increase in working capital. Our working capital increase was primarily the result of a $61.0 million increase in accounts receivable and a $54.3 million increase in inventories, which exceeded the increase in accounts payable and accrued and other liabilities. The increase in accounts receivable was primarily due to increased sales prices in our Manufacturing and Plastics segments, as well as increased sales volumes in our Plastics segment in the fourth quarter of 2021 compared to the fourth quarter of 2020. The increase in inventories was largely the result of increased material costs within our Manufacturing and Plastics segments. The increase in material costs of our Plastics segment more than offset the significant decrease in pounds of pipe inventory, which decreased as a result of lower manufacturing output due to resin supply constraints and strong demand for PVC pipe. The increase in accounts payable was largely due to the increased material costs in our Manufacturing and Plastics segments and increased inventory levels primarily in our Manufacturing segment.
| | | | | | | | | | | |
(in thousands) | 2021 | | 2020 |
| | | |
Net Cash Used in Investing Activities | $ | 171,510 | | | $ | 375,652 | |
| | | |
Net Cash Used in Investment Activities decreased $204.1 million primarily related to our Astoria Station natural gas plant and Merricourt wind farm being under construction during 2020, with the capital spend being substantially complete for both projects by year-end 2020.
| | | | | | | | | | | |
(in thousands) | 2021 | | 2020 |
| | | |
Net Cash (Used in) Provided by Financing Activities | $ | (59,359) | | | $ | 143,695 | |
| | | |
Net Cash (Used in) Provided by Financing Activities decreased $203.1 million primarily related to a decrease in construction financing needs within our Electric segment, as capital spending was substantially complete for both Astoria Station and Merricourt by year-end 2020. In 2021 our financing activities included the issuance of $140.0 million in long-term debt at OTP, which was used to repay long-term debt that matured in December 2021, and $10.2 million of net short-term borrowings on our lines of credit, which were primarily used to fund construction expenditures and support operating activities. In 2021, we paid $64.9 million in dividends to common shareholders. In 2020, $75.0 million of long-term debt was issued at OTP, we had $75.0 million of net short-term borrowings on our lines of credit, and we also raised $52.4 million from the issuance of common stock to fund capital expenditures at OTP. In 2020, we paid $60.3 million in dividends to common shareholders.
CAPITAL EXPENDITURES
We have a capital expenditure program for expanding, upgrading and improving our facilities and operating equipment. Typical uses of cash for capital expenditures are investments in electric generation facilities and environmental upgrades, transmission and distribution lines, manufacturing facilities and upgrades, equipment used in the manufacturing process, and computer hardware and information systems. The capital expenditure program is subject to review and is revised in light of changes in demands for energy, technology, environmental laws, regulatory changes, business expansion opportunities, the costs of labor, materials and equipment and our financial condition.
The following provides a summary of capital expenditures for the years ended December 31, 2021 and 2020 for our Electric segment and non-electric businesses and anticipated capital expenditures for the five year period 2022 through 2026:
| | | | | | | | | | | | | | | | | | | | | | | | | | | | | | | | | | | | | | | | | | | | | | | | | | | | |
(in millions) | | | 2020 | | 2021 | | | 2022 | | 2023 | | 2024 | | 2025 | | 2026 | | Total |
| | | | | | | | | | | | | | | | | | |
Electric Segment: | | | | | | | | | | | | | | | | | | |
Renewables and Natural Gas Generation | | | | | | | | $ | 30 | | | $ | 80 | | | $ | 92 | | | $ | 92 | | | $ | 160 | | a | $ | 454 | |
Technology and Infrastructure | | | | | | | | 26 | | | 30 | | | 18 | | | — | | | — | | | 74 | |
Distribution Plant Replacements | | | | | | | | 37 | | | 35 | | | 35 | | | 35 | | | 33 | | | 175 | |
Transmission (includes replacements) | | | | | | | | 26 | | | 28 | | | 24 | | | 20 | | | 27 | | | 125 | |
Other | | | | | | | | 30 | | | 29 | | | 32 | | | 36 | | | 23 | | a | 150 | |
Total Electric Segment | | | $ | 357 | | | $ | 140 | | | | $ | 149 | | | $ | 202 | | | $ | 201 | | | $ | 183 | | | $ | 243 | | | $ | 978 | |
Manufacturing and Plastics Segments | | | 15 | | | 32 | | | | 33 | | | 46 | | | 31 | | | 21 | | | 22 | | | 153 | |
Total Capital Expenditures | | | $ | 372 | | | $ | 172 | | | | $ | 182 | | | $ | 248 | | | $ | 232 | | | $ | 204 | | | $ | 265 | | | $ | 1,131 | |
| | | | | | | | | | | | | | | | | | |
Total Electric Utility Average Rate Base | | | $ | 1,385 | | | $ | 1,575 | | | | $ | 1,630 | | | $ | 1,750 | | | $ | 1,860 | | | $ | 1,980 | | | $ | 2,100 | | | |
Rate Base Growth | | | | | | | | 3.5 | % | | 7.4 | % | | 6.3 | % | | 6.5 | % | | 6.1 | % | | |
CONTRACTUAL OBLIGATIONS
The following table summarizes our contractual obligations at December 31, 2021 and the effect these obligations are expected to have on our liquidity and cash flow in future periods. | | | | | | | | | | | | | | | | | | | | | | | | | | | | | |
(in millions) | Total | | Less than 1 Year | | 1-3 Years | | 3-5 Years | | More than 5 Years |
| | | | | | | | | |
Debt Obligations | $ | 858 | | | $ | 121 | | | $ | — | | | $ | 80 | | | $ | 657 | |
Interest on Debt Obligations | 570 | | | 33 | | | 63 | | | 63 | | | 411 | |
Coal Contracts | 548 | | | 23 | | | 48 | | | 49 | | | 428 | |
Capacity and Energy Requirements | 177 | | | 20 | | | 24 | | | 24 | | | 109 | |
Postretirement Benefit Obligations | 116 | | | 5 | | | 12 | | | 12 | | | 87 | |
Other Purchase Obligations (including land easements) | 58 | | | 2 | | | 18 | | | 4 | | | 34 | |
Operating Lease Obligations | 21 | | | 5 | | | 9 | | | 5 | | | 2 | |
Total Contractual Cash Obligations | $ | 2,348 | | | $ | 209 | | | $ | 174 | | | $ | 237 | | | $ | 1,728 | |
Coal contract obligations are based on estimated coal consumption and costs for the delivery of coal to Coyote Station from Coyote Creek Mining Company under the lignite sales agreement that ends in 2040. Postretirement benefit obligations include estimated cash expenditures for the payment of retiree medical and life insurance benefits and supplemental pension benefits under our unfunded Executive Survivor and Supplemental Retirement Plan, but do not include amounts to fund our noncontributory funded pension plan, as we are not currently required to make a contribution to that plan.
Off-Balance Sheet Arrangements
As of December 31, 2021, we have outstanding letters of credit totaling $15.9 million, a portion of which reduces our borrowing capacity under our lines of credit. No outstanding letters of credit are reflected in outstanding short-term debt on our consolidated balance sheets.
We do not have any other off-balance-sheet arrangements or any relationships with unconsolidated entities or financial partnerships. These entities are often referred to as structured finance special purpose entities or variable interest entities, which are established for the purpose of facilitating off-balance-sheet arrangements or for other contractually narrow or limited purposes. We are not exposed to any financing, liquidity, market or credit risk that could arise if we had such relationships.
COMMON STOCK DIVIDENDS
We paid dividends to our shareholders totaling $64.9 million, or $1.56 per share, in 2021. The determination of the amount of future cash dividends to be paid will depend on, among other things, our financial condition, improvement in earnings per share, cash flows from operations, the level of our capital expenditures and our future business prospects. As a result of certain statutory limitations or regulatory or financing agreements, restrictions could occur on the amount of distributions allowed to be made by our subsidiaries. See Note 14 to our consolidated
financial statements included in this report on Form 10-K for additional information. The decision to declare a dividend is reviewed quarterly by our Board of Directors. On February 4, 2022, our Board of Directors increased the quarterly dividend from $0.39 to $0.4125 per common share.
Financial flexibility is provided by operating cash flows, unused lines of credit, strong financial coverages, investment grade credit ratings and alternative financing arrangements such as leasing. Debt financing will be required in the five-year period from 2022 through 2025 to refinance maturing debt and to finance our capital investments within our Electric segment. Our financing plans are subject to change and are impacted by our planned level of capital investments, a decision to reduce borrowings under our lines of credit, to refund or retire early any of our presently outstanding debt, to complete acquisitions or for other corporate purposes.
REGISTRATION STATEMENTS
On May 3, 2021, we filed a shelf registration statement with the SEC under which we may offer for sale, from time to time, either separately or together in any combination, equity, debt or other securities described in the shelf registration statement. The registration statement expires in May, 2024. No shares were issued pursuant to the registration statement in 2021.
On May 3, 2021, we filed a second registration statement with the SEC for the issuance of up to 1,500,000 common shares under an Automatic Dividend Reinvestment and Share Purchase Plan, which provides shareholders, retail customers of OTP and other interested investors a method of purchasing our common shares by reinvesting their dividends and/or making optional cash investments. Shares purchased under the plan may be new issue common shares or common shares purchased on the open market. The registration statement expires in May 2024. In 2021, we issued 115,180 shares under the plan. All shares issued under the plan to date have been open market purchases and there have been no new issue shares, resulting in no proceeds received by the Company. As of December 31, 2021, 1,384,820 shares remain available for purchase or issuance under the Plan.
SHORT-TERM DEBT
OTC and OTP are each party to a credit agreement (the OTC Credit Agreement and OTP Credit Agreement, respectively) which provides for unsecured revolving lines of credit. The agreements generally bear interest at the London Interbank Offered Rate (LIBOR) plus an applicable credit spread, which is subject to adjustment based on the credit ratings of the issuer. The weighted-average interest rate on all outstanding borrowings as of December 31, 2021 and 2020 was 1.42% and 1.61%.
The following is a summary of key provisions and borrowing information as of and for the year ended December 31, 2021:
| | | | | | | | | | | |
(in thousands, except interest rates) | OTC Credit Agreement | | OTP Credit Agreement |
| | | |
Borrowing Limit | $ | 170,000 | | | $ | 170,000 | |
Borrowing Limit if Accordion Exercised1 | 290,000 | | | 250,000 | |
Amount Restricted Due to Outstanding Letters of Credit at Year-End | — | | | 13,159 | |
Amount Outstanding at Year-End | 22,637 | | | 68,526 | |
Average Amount Outstanding During Year | 49,600 | | | 52,218 | |
Maximum Amount Outstanding During the Year | 79,718 | | | 110,582 | |
Interest Rate at Year-End | 1.6 | % | | 1.4 | % |
Maturity Date | September 30, 2026 | | September 30, 2026 |
| | | |
| | | |
1Each facility includes an accordion featuring allowing the borrower to increase the borrowing limit if certain terms and conditions are met. |
LONG-TERM DEBT
At December 31, 2021, we had $767.0 million of principal outstanding under long-term debt arrangements. Note 9 to our consolidated financial statements included in this report on Form 10-K includes information regarding these instruments. The agreements generally provide for unsecured borrowings at fixed rates of interest with maturities ranging from 2022 to 2051. One OTP debt instrument with a principal balance of $30.0 million matures in August 2022. Pursuant to a Note Purchase Agreement executed in June 2021, OTP intends to issue its Series 2022A notes in May 2022, for aggregate proceeds of $90.0 million, subject to the satisfaction of certain customary conditions to closing, and use a portion of the proceeds to repay the $30.0 million which is maturing in August 2022.
Financial Covenants
Certain of our short- and long-term debt agreements require OTC and OTP to maintain certain financial covenants. As of December 31, 2021, we were in compliance with these financial covenants as further described below:
OTC, under its financial covenants, may not permit its ratio of Interest-Bearing Debt to Total Capitalization to exceed 0.60 to 1.00, may not permit its Interest and Dividend Coverage Ratio to be less than 1.50 to 1.00, and may not permit its Priority Indebtedness to exceed 10% of our Total Capitalization. As of December 31, 2021, our Interest-Bearing Debt to Total Capitalization was 0.46 to 1.00, our Interest and Dividend Coverage Ratio was 6.82 to 1.00 and we had no Priority Indebtedness outstanding.
OTP under its financial covenants, may not permit its ratio of Debt to Total Capitalization to exceed 0.60 to 1.00, may not permit its Interest and Dividend Coverage Ratio to be less than 1.50 to 1.00, and may not permit its Priority Debt to exceed 20% of its Total Capitalization. As of
December 31, 2021, OTP's Interest-Bearing Debt to Total Capitalization was 0.48 to 1.00, its Interest and Dividend Coverage Ratio was 3.24 to 1.00 and it had no Priority Indebtedness outstanding.
None of our debt agreements include any provisions that would trigger an acceleration of the related debt as a result of changes in the credit rating levels assigned to the related obligor by rating agencies.
Credit Ratings
The credit ratings of OTC and OTP as of December 31, 2021 are summarized below:
| | | | | | | | | | | | | | | | | | | | | | | |
| Otter Tail Corporation | | Otter Tail Power Company |
| Moody's | Fitch | S&P | | Moody's | Fitch | S&P |
| | | | | | | |
Corporate Credit/Long-Term Issuer Default Rating | Baa2 | BBB- | BBB | | A3 | BBB | BBB+ |
Senior Unsecured Debt | n/a | BBB- | n/a | | n/a | BBB+ | BBB+ |
Outlook | Stable | Stable | Negative | | Stable | Stable | Stable |
| | | | | | | |
| | | | | |
CRITICAL ACCOUNTING POLICIES INVOLVING SIGNIFICANT ESTIMATES | |
Preparation of financial statements in accordance with accounting principles generally accepted in the United States of America requires management to make estimates and judgments that affect the reported amounts of assets, liabilities, revenues and expenses, and related disclosure of contingent assets and liabilities. While we believe the estimates and judgments we use in preparing our consolidated financial statements are appropriate and are based on the best available information, they are subject to future events and uncertainties regarding their outcome and therefore actual results may materially differ from these estimates. Management has discussed the application of these critical accounting policies and the development of these estimates with the Audit Committee of our Board of Directors. The following critical accounting policies affect the most significant judgments and estimates used in the preparation of our consolidated financial statements.
REGULATORY ACCOUNTING
Our utility business is subject to regulation of rates and other matters by state utility commissions in Minnesota, North Dakota and South Dakota and by the FERC for certain interstate operations. Accordingly, our utility business must adhere to the accounting requirements of regulated operations, which requires the recognition of regulatory assets and regulatory liabilities for amounts that otherwise would impact the statement of income or comprehensive income when it is probable that such amounts will be collected from customers or credited to customers through the rate-making process. This guidance also provides recognition criteria for adjustments to rates outside of a general rate case proceeding which are provided to encourage or incentivize investments in certain areas such as conservation, renewable energy, pollution reduction or control, improved infrastructure of the transmission grid or other programs that provide benefits to the general public under public policy, laws or regulations. Regulatory assets generally represent costs that have been incurred but have been deferred because future recovery from customers, as established through the rate-making process, is probable. Regulatory liabilities generally represent amounts to be refunded to customers or amounts currently collected from customers for future costs.
We assess the probability of recovery of regulatory assets and the obligations arising from regulatory liabilities on a quarterly basis. Our probability estimates incorporate numerous factors, including recent rate making decisions, historical precedents for similar matters, the regulatory environments in which we operate and the impact these incurred costs may have on our customers. Changes in our assessments regarding the likelihood of recovery or settlement of our regulatory assets and liabilities may have a material impact on our operating results and financial position. Further, if we determine that all or a portion of our utility business no longer meets the criteria for continued application of regulatory accounting, or our regulators disallow recovery of a previously incurred cost or eliminate a regulatory liability, we would be required to remove the associated regulatory assets and liabilities from our consolidated balance sheet and recognize in the consolidated statement of income as an expense or income item in the period in which this accounting treatment is no longer applicable.
PENSION AND OTHER POSTRETIREMENT BENEFITS OBLIGATIONS AND COSTS
Pension and postretirement benefit liabilities and expenses are determined by actuaries using assumptions about the discount rate, expected return on plan assets, rate of compensation increase and healthcare cost-trend rates. See Note 10 to our consolidated financial statements included in this report on Form 10-K for additional information on our pension and postretirement benefit plans and related assumptions.
These benefits, for any individual employee, can be earned and related expenses can be recognized and a liability accrued over periods of up to 30 or more years. These benefits can be paid out for up to 40 or more years after an employee retires. Estimates of liabilities and expenses related to these benefits are among our most critical accounting estimates. Although deferral and amortization of fluctuations in actuarially determined benefit obligations and expenses are provided for when actual results on a year-to-year basis deviate from long-range assumptions, compensation increases and healthcare cost increases or a reduction in the discount rate applied from one year to the next can significantly increase our benefit expenses in the year of the change. Also, a reduction in the expected rate of return on pension plan assets in our funded pension plan or realized rates of return on plan assets that are well below assumed rates of return or an increase in the anticipated life expectancy of plan participants could result in significant increases in recognized pension benefit expenses in the year of the change or for many years thereafter because actuarial losses can be amortized over the average remaining service lives of active employees.
We estimate the discount rate through the use of a hypothetical bond portfolio method, which incorporates yields on a collection of high credit quality bonds that produce cash flows similar to our anticipated future benefit payments. We estimate the assumed long-term rate of return on
plan assets based on asset category studies using historical market returns and volatility rates with forward looking estimates based on existing and forecasted future market conditions.
At December 31, 2021, we set the discount rate used to measure our pension plan obligations at 3.03% and at 3.01% to measure postretirement healthcare obligations, a 25 and 26 basis point increase, respectively, from the estimates used at December 31, 2020. Our estimates used to determine benefit cost for 2021 included a discount rate of 2.78% for pension benefits and 2.75% for postretirement healthcare costs, a 69 and 68 basis point decrease, respectively, from 2020 estimates. In addition, we estimated our assumed rate of return on pension assets to be 6.51% for 2021, a 37 basis point decrease from our 2020 estimate.
The following table summarizes the impact on 2021 pension and postretirement costs for a 0.25 increase or decrease, holding all other variables constant, on certain key assumptions:
| | | | | | | | | | | |
(in thousands) | +0.25 | | -0.25 |
| | | |
Pension Plan: | | | |
Discount Rate | $ | (1,249) | | | $ | 1,317 | |
Rate of Increase in Future Compensation | 880 | | | (833) | |
Long-Term Return on Plan Assets | (859) | | | 859 | |
Other Postretirement Benefits: | | | |
Discount Rate | (327) | | | 345 | |
| | | |
For 2022, we expect pension benefit cost for our pension plan to be $3.0 million compared to $7.7 million in 2021, as the amortization of actuarial losses is reduced in 2022 following actuarial gains recognized as of December 31, 2021. The estimated discount rate used to determine annual benefit cost accruals increased from 2.78% in 2021 to 3.03% in 2022. The assumed rate of return on pension plan assets is 6.30% for 2022 compared with 6.51% for 2021.
Subsequent increases or decreases in actual rates of return on plan assets over assumed rates, increases or decreases in the discount rate, increases in future compensation levels, and increases in retiree healthcare cost inflation rates could significantly change projected costs.
We believe the estimates made for our pension and other postretirement benefits are reasonable based on the information that is known at the point in time the estimates are made. These estimates and assumptions are subject to a number of variables and are subject to change.
GOODWILL IMPAIRMENT
Goodwill is required to be evaluated annually for impairment and more frequently as events or circumstances require. Goodwill is tested for impairment at the reporting unit level. We have identified two reporting units which carry a material amount of goodwill.
The goodwill impairment test is a single-step quantitative assessment which compares the estimated fair value of the reporting unit to its carrying value. An impairment charge is recognized if the carrying amount exceeds the estimated fair value in an amount that is equal to the excess but limited to the amount of recorded goodwill of the reporting unit. An optional qualitative impairment assessment may be performed prior to and may eliminate the need to perform the quantitative assessment.
Estimating the fair value of a reporting unit under the quantitative impairment method requires significant judgments and estimates. We estimate the fair value of our reporting units primarily using an income approach, which includes a discounted cash flow methodology to arrive at a fair value estimate by determining the present value of projected future cash flows over a specified period plus a terminal value to reflect cash flows beyond the projection period. The discount rate applied to the estimated future cash flows reflects our estimate of the weighted-average cost of capital of comparable entities. To supplement our income approach, we reference various market indications of fair value, where available, and include fair value estimates using multiples derived from comparable enterprise values to EBITDA, comparable price earnings ratios and, if available, comparable sales transactions for comparative peer companies.
Our discounted cash flow methodology incorporates significant estimates, which include assumptions of future operating results and cash flows, which are impacted by economic and industry conditions, the amount and timing of estimated capital expenditures, an estimated terminal growth rate and the selection of an appropriate weighted-average cost of capital, among others.
Our goodwill impairment testing performed in the fourth quarter of 2021 indicated no impairment was present for either reporting unit and the estimated fair value of each reporting unit substantially exceeded the respective carrying value. As part of our testing we perform various sensitivity analyses to understand if our conclusions are sensitive to changes in certain assumptions. A 1% decrease in projected operating revenues, a one hundred basis point decrease in projected gross profit margins and a twenty five basis point increase in the discount rate would not lead to a goodwill impairment charge for either reporting unit.
We believe the estimates and assumptions used in our impairment assessments are reasonable and based on the best information available. However, these estimates and assumptions inherently include a degree of uncertainty. Significant adverse changes in our expectations for any of these estimates could result in an impairment charge in a future period which may materially impact our operating results and financial position.
| | | | | |
ITEM 7A. | QUANTITATIVE AND QUALITATIVE DISCLOSURES ABOUT MARKET RISK |
Market risk is the potential loss arising from adverse changes in market rates and prices. We are primarily exposed to interest rate and commodity price risk.
Commodity Price Risk
Our Electric segment business is exposed to market risk arising from changes in commodity prices for wholesale energy and natural gas. OTP purchases energy in the wholesale market to supplement its own electricity generation and to respond to changes in demand and variability in generating plant output. In addition, OTP procures natural gas as a fuel source for its combustion turbine peaking facilities. OTP's exposure to price risk for these commodities is largely mitigated by the current ratemaking process and regulatory framework, which generally allows recovery of purchased power and fuel costs from our electric customers.
OTP, where prudent, seeks to further manage its exposure to commodity price variability and reduce volatility in prices for its retail customers through the use of derivative instruments, primarily financial swap agreements. OTP does not engage in derivative and hedging activities for trading purposes. As of December 31, 2021, OTP was party to financial swap agreements with an aggregate notional amount of 263,400 megawatt-hours of electricity with various settlement dates throughout 2022. As of December 31, 2021, the aggregate fair value of these instruments was $6.2 million. Holding other variables constant, a ten percent change in energy prices would have had an approximate $1.5 million impact on the fair value of these instruments.
Our Manufacturing segment businesses are exposed to market risk arising from changes in commodity prices for certain raw material inputs, including steel, aluminum, and polystyrene and other plastics resins. We attempt to manage commodity price risk by passing changes in the cost of these input materials on to our customers. If our efforts to manage commodity price risk are unsuccessful, the operating revenues and earnings of our Manufacturing segment could be impacted.
Our Plastics segment businesses are exposed to market risk arising from changes in prices for PVC resin, the primary raw material commodity used to manufacture PVC pipe. The PVC pipe industry as a whole is highly sensitive to volatility in PVC resin prices, with frequent adjustments to PVC pipe sale prices to reflect volatility in PVC resin costs. Historically, when resin prices are rising or stable, sales volumes have been higher. In contrast, when resin prices are falling, sales volumes have been lower. Due to the commodity nature of PVC resin and dynamic supply and demand factors worldwide, gross profit margins can fluctuate significantly from period to period.
We do not engage in any hedging activities within our Manufacturing and Plastics segments to manage our commodity price risk.
Interest Rate Risk
Our exposure to interest rate risk arises from outstanding short-term debt which is subject to variable rates of interest based on benchmark interest rates, primarily LIBOR. As of December 31, 2021 and 2020, we had $91.2 million and $81.0 million of short-term debt outstanding. Holding other variables constant, a one percentage point change in interest rates would have had an approximate $1.0 million impact to interest charges in 2021 based on our average outstanding short-term debt during the year.
All of our outstanding long-term debt obligations as of December 31, 2021 and 2020 had fixed interest rates and thus were not subject to interest rate risk. We manage our interest rate risk through the issuance of fixed-rate debt with varying maturities, by limiting the amount of variable interest rate debt and the utilization of short-term borrowings to allow flexibility in the timing and placement of long-term debt.
We have not used hedging instruments to manage interest risk arising from our portfolio of borrowings. We maintain a ratio of fixed-rate debt to total debt within a certain range. It is our policy to enter into interest rate transactions and other financial instruments only to the extent considered necessary to meet our stated objectives. We do not enter into interest rate transactions for speculative or trading purposes.
| | | | | |
ITEM 8. | FINANCIAL STATEMENTS |
REPORT OF INDEPENDENT REGISTERED PUBLIC ACCOUNTING FIRM
To the Shareholders and the Board of Directors of Otter Tail Corporation
Opinions on the Financial Statements and Internal Control over Financial Reporting
We have audited the accompanying consolidated balance sheets of Otter Tail Corporation and subsidiaries (the “Company”) as of December 31, 2021 and 2020, the related consolidated statements of income, comprehensive income, shareholders’ equity, and cash flows for each of the three years in the period ended December 31, 2021, and the related notes and the schedules listed in the Index at Item 15 (collectively referred to as the “financial statements”). We also have audited the Company’s internal control over financial reporting as of December 31, 2021, based on criteria established in Internal Control—Integrated Framework (2013) issued by the Committee of Sponsoring Organizations of the Treadway Commission (COSO).
In our opinion, the financial statements referred to above present fairly, in all material respects, the financial position of the Company as of December 31, 2021 and 2020, and the results of its operations and its cash flows for each of the three years in the period ended December 31, 2021, in conformity with accounting principles generally accepted in the United States of America. Also, in our opinion, the Company maintained, in all material respects, effective internal control over financial reporting as of December 31, 2021, based on the criteria established in Internal Control—Integrated Framework (2013) issued by COSO.
Basis for Opinions
The Company’s management is responsible for these financial statements, for maintaining effective internal control over financial reporting, and for its assessment of the effectiveness of internal control over financial reporting, included in the accompanying Management’s Report Regarding Internal Controls Over Financial Reporting. Our responsibility is to express an opinion on these financial statements and an opinion on the Company’s internal control over financial reporting based on our audits. We are a public accounting firm registered with the Public Company Accounting Oversight Board (United States) (PCAOB) and are required to be independent with respect to the Company in accordance with the U.S. federal securities laws and the applicable rules and regulations of the Securities and Exchange Commission and the PCAOB.
We conducted our audits in accordance with the standards of the PCAOB. Those standards require that we plan and perform the audit to obtain reasonable assurance about whether the financial statements are free of material misstatement, whether due to error or fraud, and whether effective internal control over financial reporting was maintained in all material respects.
Our audits of the financial statements included performing procedures to assess the risks of material misstatement of the financial statements, whether due to error or fraud, and performing procedures to respond to those risks. Such procedures included examining, on a test basis, evidence regarding the amounts and disclosures in the financial statements. Our audits also included evaluating the accounting principles used and significant estimates made by management, as well as evaluating the overall presentation of the financial statements. Our audit of internal control over financial reporting included obtaining an understanding of internal control over financial reporting, assessing the risk that a material weakness exists, and testing and evaluating the design and operating effectiveness of internal control based on the assessed risk. Our audits also included performing such other procedures as we considered necessary in the circumstances. We believe that our audits provide a reasonable basis for our opinions.
Definition and Limitations of Internal Control over Financial Reporting
A company’s internal control over financial reporting is a process designed to provide reasonable assurance regarding the reliability of financial reporting and the preparation of financial statements for external purposes in accordance with generally accepted accounting principles. A company’s internal control over financial reporting includes those policies and procedures that (1) pertain to the maintenance of records that, in reasonable detail, accurately and fairly reflect the transactions and dispositions of the assets of the company; (2) provide reasonable assurance that transactions are recorded as necessary to permit preparation of financial statements in accordance with generally accepted accounting principles, and that receipts and expenditures of the company are being made only in accordance with authorizations of management and directors of the company; and (3) provide reasonable assurance regarding prevention or timely detection of unauthorized acquisition, use, or disposition of the company’s assets that could have a material effect on the financial statements.
Because of its inherent limitations, internal control over financial reporting may not prevent or detect misstatements. Also, projections of any evaluation of effectiveness to future periods are subject to the risk that controls may become inadequate because of changes in conditions, or that the degree of compliance with the policies or procedures may deteriorate.
Critical Audit Matters
The critical audit matters communicated below are matters arising from the current-period audit of the financial statements that were communicated or required to be communicated to the audit committee and that (1) relate to accounts or disclosures that are material to the financial statements and (2) involved our especially challenging, subjective, or complex judgments. The communication of critical audit matters does not alter in any way our opinion on the financial statements, taken as a whole, and we are not, by communicating the critical audit matters below, providing separate opinions on the critical audit matters or on the accounts or disclosures to which they relate.
Rate and Regulatory Matters—Impact of Rate Regulation on the Financial Statements—Refer to Notes 1, and 5 to the financial statements.
Critical Audit Matter Description
The Company’s regulated Electric segment accounts for the financial effects of regulation in accordance with ASC 980, Regulated Operations. This guidance allows for the recording of a regulatory asset or liability for certain costs or credits which otherwise would be recognized in the statement of income or comprehensive income based on an expectation that the cost will be recovered or returned in future rates. This guidance also provides for adjustments to rates outside of a general rate case proceeding to encourage or incentivize investments in certain areas such as conservation, renewable energy, pollution reduction or control, improved infrastructure of the transmission grid or other programs that provide benefits to the general public under public policy, laws or regulations.
The Company is subject to rate regulation by state and federal regulatory agencies (collectively, the “Commissions”), which have jurisdiction with respect to the rates of electric distribution companies in Minnesota, North Dakota and South Dakota. The Company assesses the probability of recovery of regulatory assets and the obligations arising from regulatory liabilities on a quarterly basis. Probability estimates incorporate numerous factors, including recent rate making decisions, historical precedents for similar matters, the regulatory environments in which the Company operates, and the impact these incurred costs may have on customers.
Accounting for the economics of rate regulation impacts multiple financial statement line items and disclosures, such as property, plant, and equipment, regulatory assets and liabilities, operating revenues and expenses, depreciation expense, income taxes and multiple disclosures in the notes to the financial statements. There is a risk that the Commissions will not approve full recovery of the costs of providing utility service or full recovery of all amounts invested in the utility business and a reasonable return on that investment. As a result, we identified the impact of rate regulation as a critical audit matter due to the significant judgments made by management to support its assertions about impacted account balances and disclosures and the high degree of subjectivity involved in assessing the impact of future regulatory orders on the financial statements. Management judgments include assessing the likelihood of (1) recovery in future rates of incurred costs, (2) a disallowance of capital expenditures or operating costs that management believes were prudently incurred, and (3) a refund to customers. Given that management’s accounting judgements are based on assumptions about the outcome of future decisions by the Commissions, auditing these judgments required specialized knowledge of accounting for rate regulation and the rate setting process due its inherent complexities.
How the Critical Audit Matter Was Addressed in the Audit
Our audit procedures related to the uncertainty of future decisions by the Commissions included the following, among others:
•We tested the effectiveness of management’s controls over the evaluation of the likelihood of (1) the recovery in future rates of costs incurred as property, plant, and equipment and deferred as regulatory assets, and (2) a refund or a future reduction in rates that should be reported as regulatory liabilities. We also tested the effectiveness of management’s controls over the initial recognition of amounts as property, plant, and equipment; regulatory assets or liabilities; and the monitoring and evaluation of regulatory developments that may affect the likelihood of recovering costs in future rates or of a future reduction in rates.
•We evaluated the Company’s disclosures related to the impacts of rate regulation, including the balances recorded and regulatory developments.
•We read relevant regulatory orders issued by the Commissions for the Company, regulatory statutes, interpretations, procedural memorandums, filings made by interveners, and other publicly available information to assess the likelihood of recovery in future rates or of a future reduction in rates based on precedents of the Commissions’ treatment of similar costs under similar circumstances. We evaluated the external information and compared to management’s recorded regulatory asset and liability balances for completeness.
•We inquired of management about property, plant, and equipment that may be abandoned. We inspected the capital-projects budget and construction-in-process listings and inquired of management to identify projects that are designed to replace assets that may be retired prior to the end of the useful life. We inspected minutes of the board of directors and regulatory orders and other filings with the Commissions to identify any evidence that may contradict management’s assertion regarding probability of an abandonment.
•We compared actual spend for projects that have been capitalized to property, plant, and equipment to budget. We evaluated regulatory filings for any evidence that intervenors are challenging full recovery of the cost of any capital projects.
•We obtained an analysis from management and letters from internal and external legal counsel, as appropriate, regarding probability of recovery for regulatory assets or refund or future reduction in rates for regulatory liabilities not yet addressed in a regulatory order to assess management’s assertion that amounts are probable of recovery or a future reduction in rates.
Goodwill—Manufacturing Reporting Unit—Refer to Notes 1 and 7 to the financial statements
Critical Audit Matter Description
The Company’s evaluation of goodwill for impairment involves the comparison of the fair value of each reporting unit to its carrying value. The Company performs quantitative assessments of goodwill annually as of December 31 (the “measurement date”) and more frequently as events or circumstances require. The Company estimates the fair value of its Manufacturing reporting unit by primarily using the discounted cash flow model. The determination of the fair value using the discounted cash flow model requires management to make significant estimates and assumptions related to forecasts of future operating results and cash flows. The Manufacturing reporting unit’s operating results and cash flows are sensitive to changes in demand. The goodwill balance was $37.6 million as of December 31, 2021, of which $18.3 million relates to the Manufacturing reporting unit. The fair value of the Manufacturing reporting unit exceeded its carrying value as of the measurement date and, therefore, no impairment was recognized.
We identified goodwill for the Manufacturing reporting unit as a critical audit matter because of the significant judgments made by management to estimate its fair value and the difference between its fair value and carrying value and the sensitivity of the Manufacturing reporting unit’s operations to changes in demand. This required a high degree of auditor judgment and an increased extent of effort when performing audit procedures to evaluate the reasonableness of management’s estimates and assumptions related to forecasts of future operating results and cash flows.
How the Critical Audit Matter Was Addressed in the Audit
Our audit procedures related to forecasts of future operating results and cash flows used by management to estimate the fair value of the Manufacturing reporting unit included the following, among others:
•We tested the effectiveness of controls over management’s goodwill impairment evaluation, including those over the determination of the fair value of the Manufacturing reporting unit, such as controls related to forecasts of future operating results and cash flows.
•We evaluated management’s ability to accurately forecast future operating results and cash flows by comparing actual results to management’s historical forecasts.
•We evaluated the reasonableness of management’s operating results and cash flow forecasts by comparing the forecasts to:
–Historical operating results and cash flows.
–Internal communications between management and the Board of Directors.
–Forecasted information included in Company press releases as well as in analyst and industry reports for the Company and certain of its peer companies.
/s/ Deloitte & Touche LLP
Minneapolis, Minnesota
February 16, 2022
We have served as the Company’s auditor since 1944.
OTTER TAIL CORPORATION
CONSOLIDATED BALANCE SHEETS | | | | | | | | | | | |
| December 31, |
(in thousands, except share data) | 2021 | | 2020 |
| | | |
Assets | | | |
Current Assets | | | |
Cash and Cash Equivalents | $ | 1,537 | | | $ | 1,163 | |
Receivables, net of allowance for credit losses | 174,953 | | | 113,959 | |
Inventories | 148,490 | | | 92,165 | |
Regulatory Assets | 27,342 | | | 21,900 | |
Other Current Assets | 17,032 | | | 5,645 | |
Total Current Assets | 369,354 | | | 234,832 | |
Noncurrent Assets | | | |
Investments | 56,690 | | | 51,856 | |
Property, Plant and Equipment, net of accumulated depreciation | 2,124,605 | | | 2,049,273 | |
Regulatory Assets | 125,508 | | | 168,395 | |
Intangible Assets, net of accumulated amortization | 9,044 | | | 10,144 | |
Goodwill | 37,572 | | | 37,572 | |
Other Noncurrent Assets | 32,057 | | | 26,282 | |
Total Noncurrent Assets | 2,385,476 | | | 2,343,522 | |
Total Assets | $ | 2,754,830 | | | $ | 2,578,354 | |
| | | |
Liabilities and Shareholders' Equity | | | |
Current Liabilities | | | |
Short-Term Debt | $ | 91,163 | | | $ | 80,997 | |
Current Maturities of Long-Term Debt | 29,983 | | | 140,087 | |
Accounts Payable | 135,089 | | | 120,618 | |
Accrued Salaries and Wages | 31,704 | | | 27,451 | |
Accrued Taxes | 19,245 | | | 18,831 | |
Regulatory Liabilities | 24,844 | | | 16,663 | |
Other Current Liabilities | 55,671 | | | 32,139 | |
Total Current Liabilities | 387,699 | | | 436,786 | |
Noncurrent Liabilities and Deferred Credits | | | |
Pensions Benefit Liability | 73,973 | | | 114,055 | |
Other Postretirement Benefits Liability | 66,481 | | | 67,359 | |
Regulatory Liabilities | 234,430 | | | 233,973 | |
Deferred Income Taxes | 188,268 | | | 153,376 | |
Deferred Tax Credits | 16,661 | | | 17,405 | |
Other Noncurrent Liabilities | 62,527 | | | 60,002 | |
Total Noncurrent Liabilities and Deferred Credits | 642,340 | | | 646,170 | |
Commitments and Contingencies (Note 13) | | | |
Capitalization | | | |
Long-Term Debt, net of current maturities | 734,014 | | | 624,432 | |
Shareholders' Equity | | | |
Common Stock: 50,000,000 shares authorized of $5 par value; 41,551,524 and 41,469,879 outstanding at December 31, 2021 and 2020 | 207,758 | | | 207,349 | |
Additional Paid-In Capital | 419,760 | | | 414,246 | |
Retained Earnings | 369,783 | | | 257,878 | |
Accumulated Other Comprehensive Loss | (6,524) | | | (8,507) | |
Total Shareholders' Equity | 990,777 | | | 870,966 | |
Total Capitalization | 1,724,791 | | | 1,495,398 | |
Total Liabilities and Shareholders' Equity | $ | 2,754,830 | | | $ | 2,578,354 | |
See accompanying notes to consolidated financial statements.
OTTER TAIL CORPORATION
CONSOLIDATED STATEMENTS OF INCOME | | | | | | | | | | | | | | | | | |
| Years Ended December 31, |
(in thousands, except per-share amounts) | 2021 | | 2020 | | 2019 |
| | | | | |
Operating Revenues | | | | | |
Electric | $ | 480,321 | | | $ | 446,088 | | | $ | 459,048 | |
Product Sales | 716,523 | | | 444,019 | | | 460,455 | |
Total Operating Revenues | 1,196,844 | | | 890,107 | | | 919,503 | |
Operating Expenses | | | | | |
Electric Production Fuel | 59,327 | | | 46,296 | | | 59,256 | |
Electric Purchased Power | 65,409 | | | 61,698 | | | 72,066 | |
Electric Operating and Maintenance Expenses | 159,669 | | | 150,848 | | | 153,529 | |
Cost of Products Sold (excluding depreciation) | 488,370 | | | 329,257 | | | 355,119 | |
Other Nonelectric Expenses | 65,394 | | | 55,051 | | | 50,782 | |
Depreciation and Amortization | 91,358 | | | 82,037 | | | 78,086 | |
Electric Property Taxes | 17,609 | | | 17,034 | | | 15,785 | |
Total Operating Expenses | 947,136 | | | 742,221 | | | 784,623 | |
Operating Income | 249,708 | | | 147,886 | | | 134,880 | |
Other Income and Expense | | | | | |
Interest Charges | 37,771 | | | 34,447 | | | 31,411 | |
Nonservice Cost Components of Postretirement Benefits | 2,016 | | | 3,437 | | | 4,293 | |
Other Income (Expense), net | 2,900 | | | 6,055 | | | 5,112 | |
Income Before Income Taxes | 212,821 | | | 116,057 | | | 104,288 | |
Income Tax Expense | 36,052 | | | 20,206 | | | 17,441 | |
Net Income | $ | 176,769 | | | $ | 95,851 | | | $ | 86,847 | |
| | | | | |
Weighted-Average Common Shares Outstanding: | | | | | |
Basic | 41,491 | | | 40,710 | | | 39,721 | |
Diluted | 41,818 | | | 40,905 | | | 39,954 | |
Earnings Per Share: | | | | | |
Basic | $ | 4.26 | | | $ | 2.35 | | | $ | 2.19 | |
Diluted | $ | 4.23 | | | $ | 2.34 | | | $ | 2.17 | |
See accompanying notes to consolidated financial statements.
OTTER TAIL CORPORATION
CONSOLIDATED STATEMENTS OF COMPREHENSIVE INCOME | | | | | | | | | | | | | | | | | |
| Years Ended December 31, |
(in thousands) | 2021 | | 2020 | | 2019 |
| | | | | |
Net Income | $ | 176,769 | | | $ | 95,851 | | | $ | 86,847 | |
Other Comprehensive Income (Loss): | | | | | |
Unrealized (Loss) Gain on Available-for-Sale Securities, net of tax benefit (expense) of $52, ($42) and ($34) | (196) | | | 155 | | | 129 | |
Pension and Other Postretirement Benefit Plan, net of tax (expense) benefit of ($766), $796 and $576 | 2,179 | | | (2,225) | | | (1,638) | |
Total Other Comprehensive Income (Loss) | 1,983 | | | (2,070) | | | (1,509) | |
Total Comprehensive Income | $ | 178,752 | | | $ | 93,781 | | | $ | 85,338 | |
See accompanying notes to consolidated financial statements.
OTTER TAIL CORPORATION
CONSOLIDATED STATEMENTS OF SHAREHOLDERS' EQUITY | | | | | | | | | | | | | | | | | | | | | | | | | | | | | | | | | | | |
(in thousands, except common stock outstanding) | Common Stock Outstanding | | Par Value, Common Stock | | Additional Paid-In Capital | | Retained Earnings | | Accumulated Other Comprehensive Income (Loss) | | Total Shareholders' Equity |
| | | | | | | | | | | |
Balance, December 31, 2018 | 39,664,884 | | | $ | 198,324 | | | $ | 344,250 | | | $ | 190,433 | | | $ | (4,144) | | | $ | 728,863 | |
Stock Issuances, Net of Expenses | 347,000 | | | 1,735 | | | 15,367 | | | — | | | — | | | 17,102 | |
Stock Issued Under Dividend Reinvestment and Stock Purchase Plans | 53,339 | | | 267 | | | 2,391 | | | — | | | — | | | 2,658 | |
Stock Issued Under Share-Based Compensation Plans, Net of Shares Withheld for Employee Taxes | 92,368 | | | 462 | | | (3,176) | | | — | | | — | | | (2,714) | |
Net Income | — | | | — | | | — | | | 86,847 | | | — | | | 86,847 | |
Other Comprehensive Loss | — | | | — | | | — | | | — | | | (1,509) | | | (1,509) | |
Stranded Tax Transfer | — | | | — | | | — | | | 784 | | | (784) | | | — | |
Stock Compensation Expense | — | | | — | | | 5,958 | | | — | | | — | | | 5,958 | |
Common Dividends ($1.40 per share) | — | | | — | | | — | | | (55,723) | | | — | | | (55,723) | |
Balance, December 31, 2019 | 40,157,591 | | | $ | 200,788 | | | $ | 364,790 | | | $ | 222,341 | | | $ | (6,437) | | | $ | 781,482 | |
Stock Issuances, Net of Expenses | 868,484 | | | 4,342 | | | 32,466 | | | — | | | — | | | 36,808 | |
Stock Issued Under Dividend Reinvestment and Stock Purchase Plans | 365,267 | | | 1,826 | | | 13,221 | | | — | | | — | | | 15,047 | |
Stock Issued Under Share-Based Compensation Plans, Net of Shares Withheld for Employee Taxes | 78,537 | | | 393 | | | (2,515) | | | — | | | — | | | (2,122) | |
Net Income | — | | | — | | | — | | | 95,851 | | | — | | | 95,851 | |
Other Comprehensive Loss | — | | | — | | | — | | | — | | | (2,070) | | | (2,070) | |
Stock Compensation Expense | — | | | — | | | 6,284 | | | — | | | — | | | 6,284 | |
Common Dividends ($1.48 per share) | — | | | — | | | — | | | (60,314) | | | — | | | (60,314) | |
Balance, December 31, 2020 | 41,469,879 | | | $ | 207,349 | | | $ | 414,246 | | | $ | 257,878 | | | $ | (8,507) | | | $ | 870,966 | |
| | | | | | | | | | | |
Stock Issued Under Dividend Reinvestment and Stock Purchase Plans | 11,540 | | | 58 | | | 446 | | | — | | | — | | | 504 | |
Stock Issued Under Share-Based Compensation Plans, Net of Shares Withheld for Employee Taxes | 70,105 | | | 351 | | | (1,840) | | | — | | | — | | | (1,489) | |
Net Income | — | | | — | | | — | | | 176,769 | | | — | | | 176,769 | |
Other Comprehensive Income | — | | | — | | | — | | | — | | | 1,983 | | | 1,983 | |
Stock Compensation Expense | — | | | — | | | 6,908 | | | — | | | — | | | 6,908 | |
Common Dividends ($1.56 per share) | — | | | — | | | — | | | (64,864) | | | — | | | (64,864) | |
Balance, December 31, 2021 | 41,551,524 | | | $ | 207,758 | | | $ | 419,760 | | | $ | 369,783 | | | $ | (6,524) | | | $ | 990,777 | |
See accompanying notes to consolidated financial statements.
OTTER TAIL CORPORATION
CONSOLIDATED STATEMENTS OF CASH FLOWS | | | | | | | | | | | | | | | | | |
| Years Ended December 31, |
(in thousands) | 2021 | | 2020 | | 2019 |
| | | | | |
Operating Activities | | | | | |
Net Income | $ | 176,769 | | | $ | 95,851 | | | $ | 86,847 | |
Adjustments to Reconcile Net Income to Net Cash Provided by Operating Activities: | | | | | |
Depreciation and Amortization | 91,358 | | | 82,037 | | | 78,086 | |
Deferred Tax Credits | (744) | | | (1,221) | | | (1,348) | |
Deferred Income Taxes | 28,896 | | | 15,201 | | | 12,026 | |
Discretionary Contribution to Pension Plan | (10,000) | | | (11,200) | | | (22,500) | |
Allowance for Equity Funds Used During Construction | (822) | | | (4,063) | | | (2,553) | |
Stock Compensation Expense | 6,908 | | | 6,284 | | | 5,958 | |
Other, net | (3,035) | | | 222 | | | 764 | |
Changes in Operating Assets and Liabilities: | | | | | |
Receivables | (60,994) | | | (6,328) | | | (1,860) | |
Inventories | (54,313) | | | 5,686 | | | 8,419 | |
Regulatory Assets | (4,803) | | | (4,070) | | | 710 | |
Other Assets | (14,146) | | | (5,227) | | | 385 | |
Accounts Payable | 38,734 | | | 3,832 | | | (5,060) | |
Accrued and Other Liabilities | 28,386 | | | 19,262 | | | 13,074 | |
Regulatory Liabilities | 1,948 | | | 7,204 | | | 4,258 | |
Pension and Other Postretirement Benefits | 7,101 | | | 8,451 | | | 7,831 | |
Net Cash Provided by Operating Activities | 231,243 | | | 211,921 | | | 185,037 | |
Investing Activities | | | | | |
Capital Expenditures | (171,829) | | | (371,553) | | | (207,365) | |
Proceeds from Disposal of Noncurrent Assets | 9,702 | | | 5,011 | | | 8,519 | |
Purchases of Investments and Other Assets | (9,383) | | | (9,110) | | | (10,626) | |
Net Cash Used in Investing Activities | (171,510) | | | (375,652) | | | (209,472) | |
Financing Activities | | | | | |
Net Borrowings (Repayments) on Short-Term Debt | 10,166 | | | 74,997 | | | (12,599) | |
Proceeds from Issuance of Common Stock | 696 | | | 52,432 | | | 20,338 | |
Proceeds from Issuance of Long-Term Debt | 140,000 | | | 75,000 | | | 100,000 | |
Payments for Retirement of Long-Term Debt | (140,169) | | | (182) | | | (172) | |
Dividends Paid | (64,864) | | | (60,314) | | | (55,723) | |
Payments for Shares Withheld for Employee Tax Obligations | (1,507) | | | (2,069) | | | (2,730) | |
Other, net | (3,681) | | | 3,831 | | | (4,341) | |
Net Cash (Used in) Provided by Financing Activities | (59,359) | | | 143,695 | | | 44,773 | |
Net Change in Cash and Cash Equivalents | 374 | | | (20,036) | | | 20,338 | |
Cash and Cash Equivalents at Beginning of Period | 1,163 | | | 21,199 | | | 861 | |
Cash and Cash Equivalents at End of Period | $ | 1,537 | | | $ | 1,163 | | | $ | 21,199 | |
| | | | | |
Supplemental Disclosures of Cash Flow Information | | | | | |
Cash Paid During the Year for: | | | | | |
Interest, net of amount capitalized | $ | 36,881 | | | $ | 33,199 | | | $ | 30,132 | |
Income Taxes | $ | 8,445 | | | $ | 5,177 | | | $ | 4,797 | |
Supplemental Disclosure of Noncash Investing Activities | | | | | |
Accrued Property, Plant and Equipment Additions | $ | 12,081 | | | $ | 34,265 | | | $ | 37,429 | |
See accompanying notes to consolidated financial statements
OTTER TAIL CORPORATION
NOTES TO CONSOLIDATED FINANCIAL STATEMENTS
1. Summary of Significant Accounting Policies
Overview
Otter Tail Corporation (OTC) and its subsidiaries (collectively, the "Company", "us", "our" or "we") form a diverse, multi-platform business consisting of a vertically integrated, regulated utility with generation, transmission and distribution facilities complemented by manufacturing businesses providing metal fabrication for custom machine parts and metal components, manufacturing of extruded and thermoformed plastic products, and manufacturing of PVC pipe products. We classify our business into three segments: Electric, Manufacturing and Plastics. Note 2 includes an additional description of the segments and financial information regarding each segment.
Principles of Consolidation
These consolidated financial statements are presented in accordance with U.S. generally accepted accounting principles and include the accounts of OTC and its wholly owned subsidiaries. All intercompany balances and transactions have been eliminated in consolidation except, as applicable, profits on sales to our regulated electric utility company from our nonregulated businesses, which is in accordance with the accounting requirements of regulated operations.
Use of Estimates
We use estimates based on the best information available in recording transactions and balances resulting from business operations. As better information becomes available, or actual amounts are known, the recorded estimates are revised. Consequently, operating results can be affected by revisions to prior accounting estimates.
Reclassifications
Certain reclassifications of amounts previously reported have been made to the accompanying consolidated balance sheets and statements of cash flows to maintain consistency and comparability between periods presented. The reclassifications had no impact on previously reported current assets, total assets, current liabilities, noncurrent liabilities and deferred credits, shareholders' equity, net cash provided by operating activities, net cash used in investing activities, net cash (used in) provided by financing activities, or cash and cash equivalents.
Regulatory Accounting
Our regulated electric utility company, Otter Tail Power Company (OTP), is subject to regulation of rates and other matters by state utility commissions in Minnesota, North Dakota and South Dakota and by the Federal Energy Regulatory Commission (FERC) for certain interstate operations. OTP accounts for the financial effects of regulation in accordance with accounting guidance for regulated operations. This guidance allows for the recording of a regulatory asset for certain costs which otherwise would be recognized in the statement of income or comprehensive income based on an expectation that the cost will be recovered in future rates. This guidance also requires the recording of a regulatory liability for certain credits which would otherwise be recognized in the statement of income or comprehensive income based on an expectation that the amount will be returned to customers in future rates. Amounts recorded as regulatory assets and regulatory liabilities are generally recognized in the statements of income at the time they are reflected in customer rates. In the event OTP ceases to meet the criteria to apply the guidance for regulated operations, the regulatory assets and liabilities that no longer meet such criteria would be removed from the consolidated balance sheet and included in the consolidated statement of income as an expense or income item in the period in which the application of this guidance ceases.
Cash Equivalents
We consider all highly liquid debt instruments purchased with maturity of 90 days or less to be cash equivalents.
Revenue from Contracts with Customers
Due to our diverse business operations, the recognition of revenue from contracts with customers depends on the product produced and sold or service performed. We recognize revenue from contracts with customers at prices that are fixed or determinable as evidenced by an agreement with the customer, when we have met our performance obligation under the contract and it is probable that we will collect the amount to which we are entitled in exchange for the goods or services transferred or to be transferred to the customer. Depending on the product produced and sold or service performed and the terms of the agreement with the customer, we recognize revenue either over time, in the case of delivery or transmission of electricity or related services or the production and storage of certain custom-made products, or at a point in time for the delivery of standardized products and other products made to customer specifications where the terms of the contract require transfer of the completed product. Provisions for sales returns, early payment terms discounts, and volume-based variable pricing incentives are recorded as reductions to revenue at the time revenue is recognized based on customer history, historical information and current trends. We include revenues received for shipping and handling in operating revenues. Expenses paid for shipping and handling are recorded as part of cost of goods sold. Sales or other taxes collected from customers are excluded from operating revenues.
Electric Segment Revenues. Most Electric segment revenues are earned from the generation, transmission and sale of electricity to retail customers at rates approved by state regulatory commissions. OTP also earns revenue from the transmission of electricity for others over the transmission assets it owns separately, or jointly with other transmission service providers, under rate tariffs established by the independent transmission system operator and approved by the FERC. A third source of revenue for OTP comes from the generation and sale of electricity to wholesale customers at contract or market rates. Revenues from all these sources meet the criteria to be classified as revenue from contracts with customers and are recognized over time as energy is delivered or transmitted. Revenue is recognized based on the metered quantity of electricity delivered or transmitted at the applicable rates. For electricity delivered and consumed after a meter is read but prior to the end of the reporting period, OTP records revenue and an unbilled receivable based on estimates of the kilowatt-hours (kwh) of energy delivered to the customer.
Manufacturing Segment Revenues. Our Manufacturing segment businesses earn revenue predominantly from the production and delivery of custom-made or standardized parts to customers across several industries and certain businesses also earn revenue from the production and sale of tools and dies to other manufacturers. For the production and delivery of standardized products and other products made to customer specifications where the terms of the contract require transfer of the completed product, we have met our performance obligation and recognize revenue at the point in time when the product is shipped. At this point we have no further obligation to provide services related to such products. The shipping terms used in these transactions are FOB shipping point.
Plastics Segment Revenues. Our Plastics segment businesses earn revenue predominantly from the sale and delivery of standardized PVC pipe products produced at their manufacturing facilities. Revenue from the sale of these products is recognized at the point in time when the product is shipped as there is no further obligation to provide services related to such products and the shipping terms are FOB shipping point. We have one customer within our Plastics segment for which we produce and store a product made to the customer’s specifications and design under a build and hold agreement. For sales to this customer, we recognize revenue as the custom-made product is produced, adjusting the amount of revenue for volume rebate variable pricing considerations we expect the customer will earn and applicable early payment discounts we expect the customer will take. Ownership of the pipe transfers to the customer prior to delivery and we are paid a negotiated fee for storage of the pipe. Revenue for storage of the pipe is also recognized over time as the pipe is stored.
Alternative Revenue
In addition to recognizing revenue from contracts with customers, our Electric segment business also records revenue under alternative revenue program (ARPs) requirements. Certain rate rider mechanisms qualify as ARP revenues as they provide for adjustments to rates outside of a general rate case proceeding to encourage or incentivize investments in certain areas such as conservation, renewable energy, pollution reduction or control, improved infrastructure of the transmission grid or other programs that provide benefits to the general public under public policy, laws or regulations. ARP riders generally provide for the recovery of specified costs and investments and include an incentive component to provide the regulated utility with a return on amounts invested.
We accrue ARP revenue on the basis of cost incurred, investments made and returns on those investments that qualify for recovery through established riders. ARP revenue is disclosed separately from revenue from contracts with customers and we have elected to report ARP revenue on a net basis, whereby amounts initially recorded as ARP revenue in a period are presented net of the reversal of amounts previously recognized as ARP revenue that are reclassified and recorded as revenue from contracts with customers when such amounts are included in the price of electricity to customers.
Receivables and Allowance for Credit Losses
We grant credit to our customers in the normal course of business with repayment terms generally ranging from 30 to 90 days after the invoice date. Late fees are assessed on certain receivables once they are 30 days past due. Unbilled receivables represent estimates of energy delivered to customers but not yet billed.
Receivables are stated at the billed or estimated unbilled amount less an allowance for estimated credit losses. An allowance for credit losses is established based on losses expected to occur over the contractual life of the receivable. We estimate an allowance for credit losses on our trade and unbilled receivables by evaluating historical aging and write-off history, adjusted for current and forecasted economic conditions, for groups of receivables that share similar economic characteristics. Other receivables are evaluated by reviewing individual accounts, considering aging, financial condition of the debtor, recent payment history and other relevant factors. Account balances are written-off in the period they are deemed to be uncollectible.
Inventories
Inventories are valued at the lower of cost or net realizable value. Costs for fuel, material and supply inventories of our Electric segment are determined on an average cost basis. Costs for raw material, work in process and finished goods inventories of our Manufacturing and Plastics segments are determined on a first-in first-out (FIFO) basis.
Inventories consist of the following as of December 31, 2021 and 2020:
| | | | | | | | | | | |
(in thousands) | 2021 | | 2020 |
| | | |
Finished Goods | $ | 39,903 | | | $ | 22,046 | |
Work in Process | 35,705 | | | 16,210 | |
Raw Material, Fuel and Supplies | 72,882 | | | 53,909 | |
Total Inventories | $ | 148,490 | | | $ | 92,165 | |
Investments
We invest in and hold, through a rabbi trust, corporate-owned life insurance policies to provide future funding for obligations under our supplemental pension plan and a non-qualified deferred compensation plan. The polices are recorded at cash surrender value and there are no restrictions on our ability to surrender the policies.
We hold debt, mutual fund investments and money market funds either as investments within our captive insurance entity or to provide future funding for obligations under non-qualified deferred compensation plans. These investments are recorded at fair value. Debt securities are deemed to be available-for-sale securities, accordingly unrealized gains and losses are generally excluded from earnings and recognized in accumulated other comprehensive income. We evaluate whether declines in fair value of debt securities below the cost basis are other-than-temporary. Declines in fair value deemed to be other-than-temporary result in the recognition of unrealized losses, or a portion thereof, in earnings. Unrealized gains and losses on mutual and money market funds are recognized in earnings immediately.
The following is a summary of our investments at December 31, 2021 and 2020:
| | | | | | | | | | | |
(in thousands) | 2021 | | 2020 |
| | | |
Corporate-Owned Life Insurance Policies | $ | 41,078 | | | $ | 36,825 | |
Corporate and Government Debt Securities | 9,202 | | | 9,260 | |
Mutual Funds | 5,432 | | | 1,662 | |
Money Market Funds | 949 | | | 4,075 | |
Other Investments | 29 | | | 34 | |
Total Investments | $ | 56,690 | | | $ | 51,856 | |
The amount of unrealized gains and losses on debt securities as of December 31, 2021 and 2020 is not material and no unrealized losses were deemed to be other-than-temporary. In addition, the amount of unrealized gains and losses on marketable equity securities still held as of December 31, 2021 and 2020 is not material.
Property, Plant and Equipment
Electric plant is stated at original cost. The cost of additions includes contracted work, direct labor and materials, allocable overheads and allowance for funds used during construction. The amount of interest capitalized to electric plant was $0.6 million in 2021, $2.1 million in 2020 and $1.7 million in 2019. The cost of depreciable units of property retired less salvage is charged to accumulated depreciation. Amounts recovered in rates for future removal costs are recorded as regulatory liabilities. Removal costs, when incurred, are charged against the regulatory liability. Maintenance, repairs and replacement of minor items are charged to operating expenses as incurred. The provisions for utility depreciation for financial reporting purposes are made on the straight-line method based on the estimated remaining service lives of the properties. Gains or losses on group asset dispositions are taken to the accumulated provision for depreciation reserve and impact current and future depreciation rates.
Property, plant and equipment of nonelectric operations are carried at historical cost and are depreciated on a straight-line basis over the assets’ estimated useful lives. The cost of additions includes contracted work, direct labor and materials, allocable overheads and capitalized interest. No interest was capitalized in 2021, 2020 or 2019. Maintenance and repairs are expensed as incurred. Gains or losses on asset dispositions are included in the determination of operating income.
The estimated service lives for rate-regulated electric assets and nonelectric assets are included below: | | | | | | | | | | | |
| Service Life Range |
(years) | Low | | High |
| | | |
Electric Assets: | | | |
Production Plant | 9 | | 83 |
Transmission Plant | 51 | | 75 |
Distribution Plant | 16 | | 70 |
General Plant | 5 | | 60 |
Nonelectric Assets: | | | |
Equipment | 2 | | 12 |
Buildings and Leasehold Improvements | 5 | | 40 |
| | | |
Jointly Owned Facilities
OTP is a joint owner in two coal-fired steam-powered electric generation plants: Big Stone Plant near Big Stone City, South Dakota and Coyote Station near Beulah, North Dakota. OTP is also a joint owner, with other regional utilities, in five major transmission lines. OTP's interest in each jointly owned facility is reflected in the consolidated balance sheets on a pro-rata basis and OTP's share of direct revenue and expenses are included in operating revenues and expenses in the consolidated statements of income. Each participant in the jointly owned facilities finances its own investment.
Goodwill and Other Intangible Assets
Goodwill is recognized and initially measured as any excess of the acquisition-date consideration transferred in a business combination over amounts recognized for the net identifiable assets acquired. Goodwill is not amortized but is tested for impairment annually, or more frequently if an event occurs or circumstances change that would more likely than not result in an impairment of goodwill. Impairment testing is performed at the reporting unit level, which is defined as an operating segment or one level below an operating segment. We perform our impairment testing in the fourth quarter of each year and have identified three reporting units that carry a goodwill balance.
Our impairment testing includes both an optional qualitative assessment and the quantitative impairment assessment. Our qualitative assessment includes an analysis of relevant events and circumstances to determine if it is more likely than not that the fair value of the reporting unit exceeds its book value. If, after this assessment, we determine that it is not more likely than not that the fair value of a reporting unit is less than its carrying amount, no additional analysis is necessary. In contrast, if after the assessment we determine it is more likely than not that the fair value of a reporting unit is less than its carrying amount, or if we elect to skip the optional qualitative assessment, the quantitative impairment assessment is performed. The quantitative assessment is a single-step test that identifies both the existence of impairment and the amount of impairment loss by comparing the estimated fair value of a reporting unit to its carrying value, with any excess carrying value over the fair value being recognized as an impairment loss.
Intangible assets with finite lives, which primarily consist of customer relationships, are carried at estimated fair value at the time of acquisition less accumulated amortization. The costs of the intangible assets are amortized over their estimated useful lives, which generally range from 15 to 20 years.
Leases
We recognize right-of-use lease assets and a corresponding lease liability at the lease commencement date. The length of our lease agreements varies from less than one year to approximately ten years. We have elected to not record lease assets and liabilities for leases with a lease term at commencement of 12 months or less; such leases are expensed on a straight-line basis over the lease term. If a lease contains an option to extend the lease term and there is reasonable certainty the option will be exercised, the option is considered in the lease term at inception. We have elected to not separate non-lease components (e.g., common area maintenance) from lease components on real estate leases, accordingly the recognized lease asset and lease liability incorporate in their measurement payments for non-lease components. Certain leases include variable lease payments as the amounts are subject to change over the lease term. We are unable to determine the interest rate implicit in our leases thus we apply our incremental borrowing rate to capitalize the right-of-use asset and lease liability. We estimate our incremental borrowing rate by incorporating considerations of lease term and lessee entity.
Recoverability of Long-Lived Assets
We review our long-lived assets including, among other assets, property, plant and equipment, amortizing intangible assets and right-of-use lease assets, whenever events or changes in circumstances indicate the carrying amount of the assets may not be recoverable. We determine potential impairment by comparing the carrying amount of the assets with the net cash flows expected to be provided by operating activities of the business or related assets. If the sum of the expected future net cash flows is less than the carrying amount of the assets, an impairment loss would be recognized. Such an impairment loss would be measured as the amount by which the carrying amount exceeds the fair value of the asset.
Asset Retirement Obligations
Legal obligations related to the future retirement of long-lived assets are recognized as asset retirement obligations (ARO). An ARO is recognized in the period in which the legal obligation is incurred and the amount of the obligation can be reasonably estimated, with an offsetting increase to the associated long-lived asset. AROs are initially recognized at fair value and increased with the passage of time (accretion), with accretion expense recognized in the consolidated statements of income. ARO estimates are revised periodically with any adjustment reflected in the ARO and associated long-lived asset.
Income Taxes
We use the asset and liability method to account for income taxes. Under this method, deferred tax assets and liabilities are recognized for the expected future tax consequences of all temporary differences between the carrying amounts of assets and liabilities and their respective tax bases. Deferred taxes are recorded using the tax rates scheduled by tax law to be in effect in the periods when the temporary differences reverse. Deferred tax assets are reduced by a valuation allowance when it is more likely than not that a portion or all of the deferred tax assets will not be realized. The realizability of deferred tax assets takes into consideration forecasts of future taxable income, the reversal of other existing temporary differences, available net operating loss carryforwards and available tax planning strategies. Changes in valuation allowances are included in the provision for income taxes in the period of the changes.
We recognize the tax effects of all tax positions that are more-likely-than-not to be sustained on audit based solely on the technical merits of those positions as of the balance sheet date. Changes in the recognition or measurement of such positions are recognized in the provision for income taxes in the period of the changes. We classify interest and penalties on tax uncertainties as components of the provision for income taxes.
We amortize investment tax credits and state wind energy credits over the estimated lives of the related property.
Stock-Based Compensation
Stock-based compensation awards are measured at the grant date fair value of the award and compensation expense is recognized on a straight-line basis over the applicable service or performance period. The service period may be limited to the period until such time that a recipient is retirement eligible as determined under the award agreement. Awards granted to employees eligible for retirement on the date of grant are expensed in the period of grant. We recognize the effects of award forfeitures as they occur.
Fair Value Measurements
Fair value is defined as the price that would be received for an asset or paid to transfer a liability (an exit price) in the principal or most advantageous market for the asset or liability in an orderly transaction between market participants. Three levels of inputs may be used to measure fair value:
Level 1 – Quoted prices are available in active markets for identical assets or liabilities as of the reported date. The types of assets and liabilities included in Level 1 are highly liquid and actively traded instruments with quoted prices, such as equities listed by the New York Stock Exchange and commodity derivative contracts listed on the New York Mercantile Exchange.
Level 2 – Pricing inputs are other than quoted prices in active markets but are either directly or indirectly observable as of the reported date. The types of assets and liabilities included in Level 2 are typically either comparable to actively traded securities or contracts, such as treasury securities with pricing interpolated from recent trades of similar securities, or priced with models using highly observable inputs, such as commodity options priced using observable forward prices and volatilities.
Level 3 – Significant inputs to pricing have little or no observability as of the reporting date. The types of assets and liabilities included in Level 3 are those with inputs requiring significant management judgment or estimation and may include complex and subjective models and forecasts.
In instances where the determination of the fair value measurement is based on inputs from different levels within the hierarchy, the level in the hierarchy within which the entire fair value measurement falls is based on the lowest level input that is significant to the fair value measurement in its entirety.
Variable Interest Entity
In October 2012, the Coyote Station owners, including OTP, entered into a lignite sales agreement (LSA) with Coyote Creek Mining Company, L.L.C. (CCMC), a subsidiary of The North American Coal Corporation, for the purchase of lignite coal to meet the coal supply requirements of Coyote Station for the period beginning in May 2016 and ending in December 2040. The price per ton paid by the Coyote Station owners under the LSA reflects the cost of production, along with an agreed upon profit and capital charge. CCMC was formed for the purpose of mining coal to meet the coal fuel supply requirements of Coyote Station from May 2016 through December 2040 and, based on the terms of the LSA, is considered a variable interest entity (VIE) due to the transfer of all operating and economic risk to the Coyote Station owners, as the agreement is structured so that the price of the coal would cover all costs of operations as well as future reclamation costs. The Coyote Station owners are required to buy certain assets of CCMC at book value should they terminate the contract prior to the end of the contract term and are providing a guarantee of the value of the equity of CCMC because the Coyote Station owners are required to buy the membership interests of CCMC at the end of the contract term at equity value. Under current accounting standards, the primary beneficiary of a VIE is required to include the assets, liabilities, results of operations and cash flows of the VIE in its consolidated financial statements. No single owner of Coyote Station owns a majority interest in Coyote Station and none, individually, has the power to direct the activities that most significantly impact CCMC. Therefore, none of the owners individually, including OTP, is considered a primary beneficiary of the VIE and the Company is not required to include CCMC in its consolidated financial statements.
If the LSA terminates prior to the expiration of its term or the production period terminates prior to December 31, 2040 and the Coyote Station owners purchase all of the outstanding membership interests of CCMC, the owners will satisfy or, if permitted by CCMC’s applicable lenders, assume all of CCMC’s obligations owed to CCMC’s lenders under its loans and leases. The Coyote Station owners have limited rights to assign their rights and obligations under the LSA without the consent of CCMC’s lenders during any period in which CCMC’s obligations to its lenders remain outstanding. In the event the contract is terminated prior to the end of the term due to certain events, OTP’s maximum exposure to additional costs, as a result of its involvement with CCMC, and potential impairment loss if recovery of those costs is denied by regulatory authorities, could be as high as $45.0 million, OTP’s 35% share of CCMC’s unrecovered costs as of December 31, 2021.
2. Segment Information
We classify our business into three segments, Electric, Manufacturing and Plastics, consistent with our business strategy, organizational structure and our internal reporting and review processes used by our chief operating decision maker to make decisions regarding allocation of resources, to assess operating performance and to make strategic decisions.
Electric includes the production, transmission, distribution and sale of electric energy in Minnesota, North Dakota and South Dakota by OTP. In addition, OTP is a participant in the Midcontinent Independent System Operator, Inc. (MISO) markets. OTP’s operations have been our primary business since 1907.
Manufacturing consists of businesses in the following manufacturing activities: contract machining, metal parts stamping, fabrication and painting, and production of plastic thermoformed horticultural containers, life science and industrial packaging, and material handling components. These businesses have manufacturing facilities in Georgia, Illinois and Minnesota and sell products primarily in the United States.
Plastics consists of businesses producing PVC pipe at plants in North Dakota and Arizona. The PVC pipe is sold primarily in the western half of the United States and Canada.
Certain assets and costs are not allocated to our operating segments. Corporate operating costs include items such as corporate staff and overhead costs, the results of our captive insurance company and other items excluded from the measurement of operating segment performance. Corporate assets consist primarily of cash, prepaid expenses, investments and fixed assets. Corporate is not an operating segment, rather it is added to operating segment totals to reconcile to consolidated amounts.
Information for each segment and our unallocated corporate costs for the years ended December 31, 2021, 2020 and 2019 are as follows:
| | | | | | | | | | | | | | | | | |
(in thousands) | 2021 | | 2020 | | 2019 |
| | | | | |
Operating Revenue1 | | | | | |
Electric | $ | 480,321 | | | $ | 446,088 | | | $ | 459,048 | |
Manufacturing | 336,294 | | | 238,770 | | | 277,204 | |
Plastics | 380,229 | | | 205,249 | | | 183,251 | |
Total | $ | 1,196,844 | | | $ | 890,107 | | | $ | 919,503 | |
Depreciation and Amortization | | | | | |
Electric | $ | 71,343 | | | $ | 63,171 | | | $ | 60,044 | |
Manufacturing | 15,436 | | | 14,933 | | | 14,261 | |
Plastics | 4,354 | | | 3,604 | | | 3,451 | |
Corporate | 225 | | | 329 | | | 330 | |
Total | $ | 91,358 | | | $ | 82,037 | | | $ | 78,086 | |
Operating Income (Loss) | | | | | |
Electric | $ | 106,964 | | | $ | 107,083 | | | $ | 98,417 | |
Manufacturing | 24,114 | | | 16,103 | | | 17,869 | |
Plastics | 132,760 | | | 37,823 | | | 28,439 | |
Corporate | (14,130) | | | (13,123) | | | (9,845) | |
Total | $ | 249,708 | | | $ | 147,886 | | | $ | 134,880 | |
Interest Charges | | | | | |
Electric | $ | 33,043 | | | $ | 29,848 | | | $ | 26,548 | |
Manufacturing | 2,239 | | | 2,215 | | | 2,345 | |
Plastics | 587 | | | 644 | | | 718 | |
Corporate | 1,902 | | | 1,740 | | | 1,800 | |
Total | $ | 37,771 | | | $ | 34,447 | | | $ | 31,411 | |
Income Tax Expense (Benefit) | | | | | |
Electric | $ | 1,663 | | | $ | 12,480 | | | $ | 12,867 | |
Manufacturing | 4,704 | | | 2,939 | | | 2,784 | |
Plastics | 34,374 | | | 9,718 | | | 7,309 | |
Corporate | (4,689) | | | (4,931) | | | (5,519) | |
Total | $ | 36,052 | | | $ | 20,206 | | | $ | 17,441 | |
Net Income (Loss) | | | | | |
Electric | $ | 72,458 | | | $ | 66,778 | | | $ | 59,046 | |
Manufacturing | 17,186 | | | 11,048 | | | 12,899 | |
Plastics | 97,823 | | | 27,582 | | | 20,572 | |
Corporate | (10,698) | | | (9,557) | | | (5,670) | |
Total | $ | 176,769 | | | $ | 95,851 | | | $ | 86,847 | |
Capital Expenditures | | | | | |
Electric | $ | 140,031 | | | $ | 356,581 | | | $ | 187,362 | |
Manufacturing | 20,690 | | | 10,587 | | | 14,268 | |
Plastics | 11,040 | | | 4,322 | | | 5,452 | |
Corporate | 68 | | | 63 | | | 283 | |
Total | $ | 171,829 | | | $ | 371,553 | | | $ | 207,365 | |
| | | | | |
1Amounts reflect operating revenues to external customers. Intersegment operating revenues are not material for any period presented. | | | | |
The following provides the identifiable assets by segment and corporate assets as of December 31, 2021 and 2020:
| | | | | | | | | | | |
(in thousands) | 2021 | | 2020 |
| | | |
Identifiable Assets | | | |
Electric | $ | 2,283,776 | | | $ | 2,233,399 | |
Manufacturing | 251,044 | | | 191,005 | |
Plastics | 162,565 | | | 99,767 | |
Corporate | 57,445 | | | 54,183 | |
Total | $ | 2,754,830 | | | $ | 2,578,354 | |
Concentrations
Our Plastics segment businesses use PVC resin as a critical component within their PVC pipe manufacturing process. There are a limited number of PVC resin suppliers in the U.S., and in 2021, we sourced all of our PVC resin needs from two vendors. Although there are a limited number of PVC resin suppliers, we believe that other suppliers could provide PVC resin on comparable terms. Additionally, most U.S. resin production plants are located in the Gulf Coast region. These plants are subject to the risk of damage and production shutdowns because of exposure to hurricanes or other extreme weather events that occur in this region. The loss of a key vendor, or any interruption or delay in the supply of PVC resin could cause production delays, a possible loss of sales, or result in increased costs to secure resin, all of which would adversely affect our operating results.
Entity-Wide Information
No single customer accounted for over 10% of our consolidated operating revenues for the years ended December 31, 2021, 2020 and 2019. All of our long-lived assets are located within the United States and substantially all of our operating revenues are to customers located within the United States.
3. Revenue
We present our operating revenues to external customers, in total and by amounts arising from contracts with customers and ARP arrangements, disaggregated by revenue source and segment for the years ended December 31, 2021, 2020 and 2019:
| | | | | | | | | | | | | | | | | |
(in thousands) | 2021 | | 2020 | | 2019 |
| | | | | |
Operating Revenues | | | | | |
Electric Segment | | | | | |
Retail: Residential | $ | 135,361 | | | $ | 127,260 | | | $ | 131,988 | |
Retail: Commercial and Industrial | 262,408 | | | 254,951 | | | 267,125 | |
Retail: Other | 7,715 | | | 7,311 | | | 7,365 | |
Total Retail | 405,484 | | | 389,522 | | | 406,478 | |
Transmission | 48,835 | | | 44,001 | | | 40,542 | |
Wholesale | 17,936 | | | 4,857 | | | 5,007 | |
Other | 8,066 | | | 7,708 | | | 7,021 | |
Total Electric Segment | 480,321 | | | 446,088 | | | 459,048 | |
Manufacturing Segment | | | | | |
Metal Parts and Tooling | 283,527 | | | 199,463 | | | 236,032 | |
Plastic Products and Tooling | 40,231 | | | 34,055 | | | 35,173 | |
Other | 12,536 | | | 5,252 | | | 5,999 | |
Total Manufacturing Segment | 336,294 | | | 238,770 | | | 277,204 | |
Plastics Segment | | | | | |
PVC Pipe | 380,229 | | | 205,249 | | | 183,251 | |
Total Operating Revenue | 1,196,844 | | | 890,107 | | | 919,503 | |
Less: Noncontract Revenues Included Above | | | — | | | — | |
Electric Segment - ARP Revenues | (791) | | | 6,936 | | | 1,032 | |
Total Operating Revenues from Contracts with Customers | $ | 1,197,635 | | | $ | 883,171 | | | $ | 918,471 | |
4. Receivables
Receivables as of December 31, 2021 and 2020 are as follows:
| | | | | | | | | | | |
(in thousands) | 2021 | | 2020 |
| | | |
Receivables | | | |
Trade | $ | 142,297 | | | $ | 87,048 | |
Other | 10,591 | | | 8,939 | |
Unbilled Receivables | 23,901 | | | 21,187 | |
Total Receivables | 176,789 | | | 117,174 | |
Less Allowance for Credit Losses | (1,836) | | | (3,215) | |
Receivables, net of allowance for credit losses | $ | 174,953 | | | $ | 113,959 | |
The following is a summary of activity in the allowance for credit losses for the years ended December 31, 2021 and 2020:
| | | | | | | | | | | |
(in thousands) | 2021 | | 2020 |
| | | |
Beginning Balance | $ | 3,215 | | | $ | 1,339 | |
Additions Charged to Expense | 93 | | | 3,138 | |
Reductions for Amounts Written-Off, Net of Recoveries | (1,472) | | | (1,262) | |
Ending Balance | $ | 1,836 | | | $ | 3,215 | |
5. Regulatory Matters
Regulatory Assets and Liabilities
The following presents our current and long-term regulatory assets and liabilities as of December 31, 2021 and 2020 and the period we expect to recover or refund such amounts:
| | | | | | | | | | | | | | | | | | | | | | | | | | | | | |
| Period of | | 2021 | | 2020 |
(in thousands) | Recovery/Refund | | Current | | Long-Term | | Current | | Long-Term |
| | | | | | | | | |
Regulatory Assets | | | | | | | | | |
Pension and Other Postretirement Benefit Plans1 | See below | | $ | 7,791 | | | $ | 114,961 | | | $ | 11,037 | | | $ | 146,071 | |
Alternative Revenue Program Riders2 | Up to 2 years | | 11,889 | | | 5,564 | | | 8,871 | | | 9,373 | |
Asset Retirement Obligations1 | Asset lives | | — | | | 742 | | | — | | | 8,462 | |
| | | | | | | | | |
ISO Cost Recovery Trackers1 | Up to 2 years | | — | | | 1,342 | | | 1,079 | | | 867 | |
Unrecovered Project Costs1 | Up to 5 years | | 2,136 | | | 1,455 | | | 361 | | | 2,989 | |
Deferred Rate Case Expenses1 | Various | | 607 | | | 1,131 | | | 360 | | | 230 | |
Debt Reacquisition Premiums1 | Up to 30 years | | 100 | | | 240 | | | 192 | | | 341 | |
Fuel Clause Adjustments1 | Up to 1 year | | 4,819 | | | — | | | — | | | — | |
Other1 | Various | | — | | | 73 | | | — | | | 62 | |
Total Regulatory Assets | | | $ | 27,342 | | | $ | 125,508 | | | $ | 21,900 | | | $ | 168,395 | |
Regulatory Liabilities | | | | | | | | | |
Deferred Income Taxes | Asset lives | | $ | — | | | $ | 129,437 | | | $ | — | | | $ | 134,719 | |
Plant Removal Obligations | Asset lives | | 8,306 | | | 101,595 | | | — | | | 98,707 | |
Fuel Clause Adjustments | Up to 1 year | | 1,554 | | | — | | | 10,947 | | | — | |
Alternative Revenue Program Riders | Various | | 5,772 | | | 3,336 | | | 3,581 | | | 470 | |
Pension and Other Postretirement Benefit Plans | Up to 1 year | | 2,603 | | | — | | | 1,959 | | | — | |
| | | | | | | | | |
Derivative Instruments | Up to 1 year | | 6,214 | | | — | | | — | | | — | |
| | | | | | | | | |
Other | Various | | 395 | | | 62 | | | 176 | | | 77 | |
Total Regulatory Liabilities | | | $ | 24,844 | | | $ | 234,430 | | | $ | 16,663 | | | $ | 233,973 | |
| | | | | | | | | |
1Costs subject to recovery without a rate of return. | | | | | | | | | |
2Amount eligible for recovery includes an incentive or rate of return. | | | | | | | | | |
Pension and Other Postretirement Benefit Plans represent benefit costs and actuarial losses and gains subject to recovery or refund through rates as they are expensed or amortized. These unrecognized benefit costs and actuarial losses and gains are eligible for treatment as regulatory assets or liabilities based on their probable inclusion in future electric rates.
Alternative Revenue Program Riders regulatory assets and liabilities are revenues not yet collected from customers or amounts subject to
refund, respectively, primarily due to investments in qualifying transmission, conservation, renewable resource, environmental and other generation assets.
Asset Retirement Obligations represent the difference in timing of recognition of expense arising from these obligations and the amount recovered from customers.
Independent System Operator (ISO) Cost Recovery Trackers represent costs incurred to serve Minnesota customers or the under-collection of revenue based on expected versus actual construction costs on eligible projects.
Unrecovered Project Costs reflect costs incurred for abandoned generation and transmission assets and accelerated depreciation expense on a to-be-retired generation asset expected to be recovered from customers.
Deferred Rate Case Expenses relate to costs incurred in conjunction with recent rate cases that are currently or are expected to be recovered from customers.
Debt Reacquisition Premiums represent costs to retire debt which are being recovered from customers over the remaining original lives of the reacquired debt.
Fuel Clause Adjustments represent the under- or over-collection of fuel costs to be returned to or collected from customers.
Deferred Income Taxes represent income tax benefits, arising primarily from property-related timing differences, that will be refunded to customers as these timing differences reverse.
Plant Removal Obligations represent amounts collected from customers to be used to cover actual removal costs as incurred.
Derivative Instruments represent unrealized gains recognized on derivative instruments. On final settlement of such instruments, any realized gains or losses are recovered from or paid to customers.
6. Property, Plant and Equipment
Major classes of property, plant and equipment as of December 31, 2021 and 2020 include:
| | | | | | | | | | | |
(in thousands) | 2021 | | 2020 |
| | | |
Electric Plant in Service | | | |
Production | $ | 1,332,067 | | | $ | 1,172,362 | |
Transmission | 722,739 | | | 690,647 | |
Distribution | 574,488 | | | 545,221 | |
General | 129,151 | | | 123,122 | |
Electric Plant in Service | 2,758,445 | | | 2,531,352 | |
Construction Work in Progress | 74,926 | | | 203,078 | |
Total Gross Electric Plant | 2,833,371 | | | 2,734,430 | |
Less Accumulated Depreciation and Amortization | 817,302 | | | 778,988 | |
Net Electric Plant | $ | 2,016,069 | | | $ | 1,955,442 | |
Nonelectric Property, Plant and Equipment | | | |
Equipment | $ | 203,390 | | | $ | 197,389 | |
Buildings and Leasehold Improvements | 56,908 | | | 55,441 | |
Land | 13,652 | | | 5,900 | |
Nonelectric Property, Plant and Equipment | 273,950 | | | 258,730 | |
Construction Work in Progress | 16,611 | | | 9,290 | |
Total Gross Nonelectric Property, Plant and Equipment | 290,561 | | | 268,020 | |
Less Accumulated Depreciation and Amortization | 182,025 | | | 174,189 | |
Net Nonelectric Property, Plant and Equipment | 108,536 | | | 93,831 | |
Net Property, Plant and Equipment | $ | 2,124,605 | | | $ | 2,049,273 | |
Depreciation expense for the years ended December 31, 2021, 2020 and 2019 totaled $85.8 million, $78.6 million and $71.9 million.
The following table provides OTP’s ownership percentages and amounts included in the December 31, 2021 and 2020 consolidated balance sheets for OTP’s share of each of these jointly owned facilities: | | | | | | | | | | | | | | | | | | | | | | | | | | | | | |
(dollars in thousands) | Ownership Percentage | | Electric Plant in Service | | Construction Work in Progress | | Accumulated Depreciation | | Net Plant |
| | | | | | | | | |
December 31, 2021 | | | | | | | | | |
Big Stone Plant | 53.9 | % | | $ | 338,699 | | | $ | 260 | | | $ | (110,604) | | | $ | 228,355 | |
Coyote Station | 35.0 | % | | 182,610 | | | 1,110 | | | (107,894) | | | 75,826 | |
Big Stone South–Ellendale 345 kV line | 50.0 | % | | 106,194 | | | — | | | (4,052) | | | 102,142 | |
Fargo–Monticello 345 kV line | 14.2 | % | | 78,184 | | | — | | | (9,069) | | | 69,115 | |
Big Stone South–Brookings 345 kV line | 50.0 | % | | 52,975 | | | — | | | (3,613) | | | 49,362 | |
Brookings–Southeast Twin Cities 345 kV line | 4.8 | % | | 26,291 | | | — | | | (2,843) | | | 23,448 | |
Bemidji–Grand Rapids 230 kV line | 14.8 | % | | 16,331 | | | — | | | (2,995) | | | 13,336 | |
December 31, 2020 | | | | | | | | | |
Big Stone Plant | 53.9 | % | | $ | 332,611 | | | $ | 2,552 | | | $ | (103,504) | | | $ | 231,659 | |
Coyote Station | 35.0 | % | | 180,991 | | | 732 | | | (108,603) | | | 73,120 | |
Big Stone South–Ellendale 345 kV line | 50.0 | % | | 106,353 | | | — | | | (2,433) | | | 103,920 | |
Fargo–Monticello 345 kV line | 14.2 | % | | 78,184 | | | — | | | (8,029) | | | 70,155 | |
Big Stone South–Brookings 345 kV line | 50.0 | % | | 53,036 | | | — | | | (2,822) | | | 50,214 | |
Brookings–Southeast Twin Cities 345 kV line | 4.8 | % | | 26,291 | | | — | | | (2,468) | | | 23,823 | |
Bemidji–Grand Rapids 230 kV line | 14.8 | % | | 16,331 | | | — | | | (2,670) | | | 13,661 | |
| | | | | | | | | |
7. Intangible Assets
The following table summarizes our goodwill by segment as of December 31, 2021 and 2020:
| | | | | | | | | | | |
(in thousands) | 2021 | | 2020 |
| | | |
Manufacturing | $ | 18,270 | | | $ | 18,270 | |
Plastics | 19,302 | | | 19,302 | |
Total Goodwill | $ | 37,572 | | | $ | 37,572 | |
Our annual goodwill impairment testing, performed in the fourth quarters of 2021 and 2020, indicated no impairment existed as of the test date.
The following table summarizes the components of our intangible assets at December 31, 2021 and 2020:
| | | | | | | | | | | | | | | | | |
(in thousands) | Gross Amount | | Accumulated Amortization | | Net Carrying Amount |
| | | | | |
December 31, 2021 | | | | | |
Customer Relationships | $ | 22,491 | | | $ | 13,469 | | | $ | 9,022 | |
Other | 26 | | | 4 | | | 22 | |
Total | $ | 22,517 | | | $ | 13,473 | | | $ | 9,044 | |
December 31, 2020 | | | | | |
Customer Relationships | $ | 22,491 | | | $ | 12,370 | | | $ | 10,121 | |
Other | 26 | | | 3 | | | 23 | |
Total | $ | 22,517 | | | $ | 12,373 | | | $ | 10,144 | |
| | | | | |
Amortization expense for these intangible assets for the years ended December 31, 2021, 2020 and 2019 totaled $1.1 million, $1.1 million, and $1.2 million.
Annual amortization expense for these intangible assets for the next five years is:
| | | | | | | | | | | | | | | | | | | | | | | | | | | | | |
(in thousands) | 2022 | | 2023 | | 2024 | | 2025 | | 2026 |
| | | | | | | | | |
Amortization Expense | $ | 1,100 | | | $ | 1,100 | | | $ | 1,100 | | | $ | 1,092 | | | $ | 1,090 | |
| | | | | | | | | |
8. Leases
We lease coal rail cars, warehouse and office space, land and certain office, manufacturing and material handling equipment under varying terms and conditions. All leases are classified as operating leases.
The components of lease cost and lease cash flows for the years ended December 31, 2021 and 2020 are as follows:
| | | | | | | | | | | |
(in thousands) | 2021 | | 2020 |
| | | |
Lease Cost | | | |
Operating Lease Cost | $ | 5,298 | | | $ | 5,837 | |
Variable Lease Cost | 1,020 | | | 1,166 | |
Total Lease Cost | $ | 6,318 | | | $ | 7,003 | |
| | | |
Lease Cash Flows | | | |
Operating Cash Flows from Operating Leases | $ | 5,642 | | | $ | 5,431 | |
| | | |
A summary of operating lease right-of-use lease assets and lease liabilities as of December 31, 2021 and 2020 is as follows:
| | | | | | | | | | | | | | |
(in thousands) | | 2021 | | 2020 |
| | | | |
Right of Use Lease Assets1 | | $ | 19,133 | | | $ | 19,114 | |
Lease Liabilities | | | | |
Current2 | | 4,168 | | | 4,479 | |
Long-Term3 | | 15,309 | | | 15,314 | |
Total Lease Liabilities | | $ | 19,477 | | | $ | 19,793 | |
| | | | |
1Included in Other Noncurrent Assets in the consolidated balance sheets. | | | | |
2Included in Other Current Liabilities in the consolidated balance sheets. | | | | |
3Included in Other Noncurrent Liabilities in the consolidated balance sheets. | | | | |
Operating lease assets obtained in exchange for new operating liabilities amounted to $2.1 million and $1.4 million for the years ended December 31, 2021 and 2020.
Maturities of lease liabilities as of December 31, 2021 for each of the next five years and in the aggregate thereafter are as follows: | | | | | |
(in thousands) | Operating Leases |
| |
2022 | $ | 4,998 | |
2023 | 4,766 | |
2024 | 4,225 | |
2025 | 3,384 | |
2026 | 1,614 | |
Thereafter | 2,470 | |
Total Lease Payments | $ | 21,457 | |
Less: Interest | 1,980 | |
Present Value of Lease Liabilities | $ | 19,477 | |
The weighted-average remaining lease term and the weighted-average discount rate as of December 31, 2021 and 2020 are as follows:
| | | | | | | | | | | |
| 2021 | | 2020 |
| | | |
Weighted-Average Remaining Lease Term (in years) | 4.9 | | 5.3 |
Weighted-Average Discount Rate | 5.09 | % | | 5.45 | % |
| | | |
9. Short-Term and Long-Term Borrowings
The following is a summary of our outstanding short- and long-term borrowings by borrower, OTC or OTP, as of December 31, 2021 and 2020:
| | | | | | | | | | | | | | | | | | | | | | | | | | | | | | | | | | | |
| 2021 | | 2020 |
(in thousands) | OTC | | OTP | | Total | | OTC | | OTP | | Total |
| | | | | | | | | | | |
Short-Term Debt | $ | 22,637 | | | $ | 68,526 | | | $ | 91,163 | | | $ | 65,166 | | | $ | 15,831 | | | $ | 80,997 | |
Current Maturities of Long-Term Debt | — | | | 29,983 | | | 29,983 | | | 169 | | | 139,918 | | | 140,087 | |
Long-Term Debt, net of current maturities | 79,746 | | | 654,268 | | | 734,014 | | | 79,695 | | | 544,737 | | | 624,432 | |
Total | $ | 102,383 | | | $ | 752,777 | | | $ | 855,160 | | | $ | 145,030 | | | $ | 700,486 | | | $ | 845,516 | |
Short-Term Debt
The following is a summary of our lines of credit as of December 31, 2021 and 2020:
| | | | | | | | | | | | | | | | | | | | | | | | | | | | | |
| | | 2021 | | 2020 |
(in thousands) | Line Limit | | Amount Outstanding | | Letters of Credit | | Amount Available | | Amount Available |
| | | | | | | | | |
OTC Credit Agreement | $ | 170,000 | | | $ | 22,637 | | | $ | — | | | $ | 147,363 | | | $ | 104,834 | |
OTP Credit Agreement | 170,000 | | | 68,526 | | | 13,159 | | | 88,315 | | | 140,068 | |
Total | $ | 340,000 | | | $ | 91,163 | | | $ | 13,159 | | | $ | 235,678 | | | $ | 244,902 | |
On September 30, 2021, OTC entered into a Fourth Amended and Restated Credit Agreement (the OTC Credit Agreement) and OTP entered into a Third Amended and Restated Credit Agreement (the OTP Credit Agreement) amending and restating the previously existing credit agreements to extend the maturity date of each credit facility to September 30, 2026. The agreements both provide for $170.0 million unsecured revolving lines of credit to support operations, fund capital expenditures, refinance certain indebtedness and provide for the issuance of letters of credit in an aggregate amount not to exceed $40.0 million under the OTC Credit Agreement and $50.0 million under the OTP Credit Agreement. Each credit facility includes an accordion provision allowing the borrower, subject to certain conditions, to increase the borrowing capacity under the facility; up to $290.0 million under the OTC Credit Agreement and up to $250.0 million under the OTP Credit Agreement.
Borrowings under each credit facility are subject to a variable rate of interest on outstanding balances and a commitment fee is charged based on the average unused amount available to be drawn under the respective facility. The variable rate of interest to be charged is based on a benchmark interest rate, either LIBOR or a Base Rate, as defined in the credit agreements, selected by the borrower at the time of an advance, subject to the conditions of each agreement, plus an applicable credit spread. The credit spread ranges from zero to 2.00%, depending on the benchmark interest rate selected and is subject to adjustment based on the credit ratings of the relevant borrowers. The weighted-average interest rate on all outstanding borrowings as of December 31, 2021 and 2020 was 1.42% and 1.61%.
Each credit facility contains a number of restrictions on the borrower, including restrictions on the ability to merge, sell assets, make investments, create or incur liens on assets, guarantee the obligations of any other party and engage in transactions with related parties. The agreements also contain certain financial and non-financial covenants and defined events of default.
Both the OTC Credit Agreement and the OTP Credit Agreement include interest rates determined by a reference to LIBOR. The applicable LIBOR tenors are currently scheduled to be eliminated on June 30, 2023. In the event that LIBOR is no longer available, both credit agreements contain provisions for the replacement of LIBOR as the benchmark rate with the Secured Overnight Finance Rate (SOFR). The transition to SOFR may be triggered by the discontinuation or loss of representativeness of the applicable LIBOR tenors or as earlier elected by the borrowers, subject to approval by the lender.
Long-Term Debt
The following is a summary of outstanding long-term debt by borrower as of December 31, 2021 and 2020:
| | | | | | | | | | | | | | | | | | | | | | | | | | | | | | | | |
| | | | | | | | (in thousands) |
Entity | | Debt Instrument | | Rate | | Maturity | | 2021 | | 2020 |
| | | | | | | | | | |
OTC | | Guaranteed Senior Notes | | 3.55% | | 12/15/26 | | $ | 80,000 | | | $ | 80,000 | |
OTP | | Series 2011A Senior Unsecured Notes | | 4.63% | | 12/01/21 | | — | | | 140,000 | |
OTP | | Series 2007B Senior Unsecured Notes | | 6.15% | | 08/20/22 | | 30,000 | | | 30,000 | |
OTP | | Series 2007C Senior Unsecured Notes | | 6.37% | | 08/02/27 | | 42,000 | | | 42,000 | |
OTP | | Series 2013A Senior Unsecured Notes | | 4.68% | | 02/27/29 | | 60,000 | | | 60,000 | |
OTP | | Series 2019A Senior Unsecured Notes | | 3.07% | | 10/10/29 | | 10,000 | | | 10,000 | |
OTP | | Series 2020A Senior Unsecured Notes | | 3.22% | | 02/25/30 | | 10,000 | | | 10,000 | |
OTP | | Series 2020B Senior Unsecured Notes | | 3.22% | | 08/20/30 | | 40,000 | | | 40,000 | |
OTP | | Series 2021A Senior Unsecured Notes | | 2.74% | | 11/29/31 | | 40,000 | | | — | |
OTP | | Series 2007D Senior Unsecured Notes | | 6.47% | | 08/20/37 | | 50,000 | | | 50,000 | |
OTP | | Series 2019B Senior Unsecured Notes | | 3.52% | | 10/10/39 | | 26,000 | | | 26,000 | |
OTP | | Series 2020C Senior Unsecured Notes | | 3.62% | | 02/25/40 | | 10,000 | | | 10,000 | |
OTP | | Series 2013B Senior Unsecured Notes | | 5.47% | | 02/27/44 | | 90,000 | | | 90,000 | |
OTP | | Series 2018A Senior Unsecured Notes | | 4.07% | | 02/07/48 | | 100,000 | | | 100,000 | |
OTP | | Series 2019C Senior Unsecured Notes | | 3.82% | | 10/10/49 | | 64,000 | | | 64,000 | |
OTP | | Series 2020D Senior Unsecured Notes | | 3.92% | | 02/25/50 | | 15,000 | | | 15,000 | |
OTP | | Series 2021B Senior Unsecured Notes | | 3.69% | | 11/29/51 | | 100,000 | | | — | |
OTC | | PACE Note | | 2.54% | | 03/18/21 | | — | | | 169 | |
Total | | | | | | | | $ | 767,000 | | | $ | 767,169 | |
Less: | Current Maturities Net of Unamortized Debt Issuance Costs | | | | | | 29,983 | | | 140,087 | |
| Unamortized Long-Term Debt Issuance Costs | | | | | | 3,003 | | | 2,650 | |
Total Long-Term Debt Net of Unamortized Debt Issuance Costs | | | | $ | 734,014 | | | $ | 624,432 | |
On June 10, 2021, OTP entered into a Note Purchase Agreement pursuant to which OTP agreed to issue, in a private placement transaction, $230.0 million of senior unsecured notes consisting of (a) $40.0 million of 2.74% Series 2021A Senior Unsecured Notes due November 29, 2031, (b) $100.0 million of 3.69% Series 2021B Senior Unsecured Notes due November 29, 2051 and (c) $90.0 million of 3.77% Series 2022A Senior Unsecured Notes due May 20, 2052. During the year ended December 31, 2021, OTP issued its Series 2021A and Series 2021B notes for aggregate proceeds of $140.0 million, which were used to repay the Series 2011A notes. The issuance of the Series 2022A notes is scheduled to close, subject to the satisfaction of certain customary conditions to closing, in May 2022.
Our guaranteed and unsecured notes require the borrower to maintain various financial covenants, as further described below. These notes provide for prepayment options allowing for a full or partial prepayment at 100% of the principal amount so prepaid, together with unpaid accrued interest and a make-whole amount, as defined. These notes also include restrictions on the borrowers, including its ability to merge, sell assets, create or incur liens on assets, guarantee the obligations of any other party and engage in transactions with related parties.
Aggregate maturities of long-term debt obligations at December 31, 2021 for each of the next five years are as follows:
| | | | | | | | | | | | | | | | | | | | | | | | | | | | | |
(in thousands) | 2022 | | 2023 | | 2024 | | 2025 | | 2026 |
| | | | | | | | | |
Debt Maturities | $ | 30,000 | | | $ | — | | | $ | — | | | $ | — | | | $ | 80,000 | |
| | | | | | | | | |
Financial Covenants
Certain of OTC's and OTP's short-term and long-term debt agreements require the borrower, whether OTC or OTP, to maintain certain financial covenants, including a maximum debt to total capitalization of 0.60 to 1.00, a minimum interest and dividend coverage ratio of 1.50 to 1.00, and a maximum level of priority indebtedness. As of December 31, 2021, OTC and OTP were in compliance with these financial covenants.
10. Employee Postretirement Benefits
Pension Plan and Other Postretirement Benefits
The Company sponsors a noncontributory funded pension plan (the "Pension Plan"), an unfunded, nonqualified Executive Survivor and Supplemental Retirement Plan ("ESSRP"), both accounted for as defined benefit pension plans, and a postretirement healthcare plan accounted for as an other postretirement benefit plan.
The Pension Plan, which previously covered substantially all corporate and OTP employees, was closed to new employees in 2013. The plan provides retirement compensation to all covered employees at age 65, with reduced compensation in cases of retirement prior to age 62.
Participants are fully vested after completing five years of vesting service. The plan assets consist of equity funds, fixed income funds, cash and cash equivalents and alternative investments. None of the plan assets are invested in common stock or debt securities of the Company.
The ESSRP, an unfunded plan, provides for defined benefit payments to executive officers and certain key management employees on their retirement for life, or to their beneficiaries on their death. The ESSRP was amended and restated in 2019 to i) freeze the participation in the restoration retirement benefit component of the plan and ii) freeze benefit accruals under the restoration retirement benefit component of the plan for all participants of the plan, except any participants deemed to be grandfathered participants.
The postretirement healthcare plan, closed to new participants in 2010, provides a portion of health insurance benefits for retired and covered corporate and OTP employees. To be eligible for retiree health insurance benefits, the employee must be 55 years of age with a minimum of 10 years of service. The plan is an unfunded plan and accordingly holds no plan assets.
Pension Plan Assets. We have established a Retirement Plans Administration Committee to develop and monitor our investment strategy for our Pension Plan assets. Our investment strategy includes the following objectives:
•The assets of the plan will be invested in accordance with all applicable laws in a manner consistent with fiduciary standards including Employee Retirement Income Security Act standards of 1974 (ERISA) (if applicable). Specifically:
◦The safeguards and diversity that a prudent investor would adhere to must be present in the investment program.
◦All transactions undertaken on behalf of the Pension Plan must be in the best interest of plan participants and their beneficiaries.
•The primary objective is to provide a source of retirement income for its participants and beneficiaries.
•The near-term primary financial objective is to improve and protect the funded status of the plan.
•A secondary financial objective is to minimize pension funding and expense volatility where possible.
We have developed an asset allocation target, measured at investment market value, to provide guideline percentages of investment mix. This investment mix is intended to achieve the financial objectives of the plan. The permitted range is a guide and will at times not reflect the actual asset allocation due to market conditions, actions of our investment managers and required cash flows to and from the Pension Plan.
The following table presents our target asset allocation permitted range along with the actual asset allocation as of December 31, 2021 and 2020:
| | | | | | | | | | | | | | | | | | | | | | | |
| Permitted | | Actual Allocation |
Asset Class | Range | | 2021 | | 2020 |
| | | | | | | |
Return Enhancement | 20 | | – | 60% | | 47 | % | | 58 | % |
Risk Management | 40 | | – | 80% | | 50 | | | 39 | |
Alternatives | 0 | | – | 20% | | 3 | | | 3 | |
Total | | | | | 100 | % | | 100 | % |
Return Enhancement investments are those that seek to provide equity-like, long-term capital appreciation. Examples include equity securities, including dynamic asset allocation funds, and higher yielding fixed income securities, such as high yield bonds and emerging market debt.
Risk Management investments seek to decrease downside risk or act as a hedge against plan liabilities. Examples are cash and fixed income instruments.
Alternative investments seek to either provide return enhancement through long-term appreciation or risk management through decreased downside risk. The defining characteristic of these asset types is uncorrelated source of returns, less liquidity and private market access. Examples include investments in the SEI Energy Debt Collective Fund.
The following presents the fair value inputs classified within the fair value hierarchy used to measure Pension Plan assets at December 31, 2021 and 2020 and assets measured using the net asset value (NAV) practical expedient: | | | | | | | | | | | | | | | | | | | | | | | | | | | | | |
(in thousands) | Level 1 | | Level 2 | | Level 3 | | NAV | | Total |
| | | | | | | | | |
December 31, 2021 | | | | | | | | | |
| | | | | | | | | |
Equity Funds | $ | 149,479 | | | $ | — | | | $ | — | | | $ | — | | | $ | 149,479 | |
Fixed Income Funds | 184,987 | | | — | | | — | | | — | | | 184,987 | |
Hybrid Funds | 11,776 | | | — | | | — | | | — | | | 11,776 | |
U.S. Treasury Securities | 28,173 | | | — | | | — | | | — | | | 28,173 | |
SEI Energy Debt Collective Fund | — | | | — | | | — | | | 12,797 | | | 12,797 | |
Total | $ | 374,415 | | | $ | — | | | $ | — | | | $ | 12,797 | | | $ | 387,212 | |
December 31, 2020 | | | | | | | | | |
Cash Equivalents | $ | 4 | | | $ | — | | | $ | — | | | $ | — | | | $ | 4 | |
Equity Funds | 180,169 | | | — | | | — | | | — | | | 180,169 | |
Fixed Income Funds | 159,556 | | | — | | | — | | | — | | | 159,556 | |
Hybrid Funds | 11,729 | | | — | | | — | | | — | | | 11,729 | |
SEI Energy Debt Collective Fund | — | | | — | | | — | | | 9,220 | | | 9,220 | |
Total | $ | 351,458 | | | $ | — | | | $ | — | | | $ | 9,220 | | | $ | 360,678 | |
The investments held by the SEI Energy Debt Collective Fund on December 31, 2021 and 2020 consist mainly of below investment grade high yield bonds and loans of U.S. energy companies which trade at a discount to fair value. Redemptions are allowed semi-annually with a 95-day notice period, subject to fund director consent and certain gate, holdback and suspension restrictions. Subscriptions are allowed monthly with a three-year lock up on subscriptions. The fund’s assets are valued in accordance with valuations reported by the fund’s sub-advisor or the fund’s underlying investments or other independent third-party sources, although SEI in its discretion may use other valuation methods, subject to compliance with ERISA, as applicable. On an annual basis, as determined by the investment manager in its sole discretion, an independent valuation agent is retained to provide a valuation of the illiquid assets of the fund and of any other asset of the fund.
Funded Status. The following table provides a reconciliation of the changes in the fair value of plan assets and the actuarially computed benefit obligation for the years ended December 31, 2021 and 2020 and the funded status of the plans as of December 31, 2021 and 2020:
| | | | | | | | | | | | | | | | | | | | | | | | | | | | | | | | | | | |
| Pension Benefits (Pension Plan) | | Pension Benefits (ESSRP) | | Postretirement Benefits |
(in thousands) | 2021 | | 2020 | | 2021 | | 2020 | | 2021 | | 2020 |
| | | | | | | | | | | |
Change in Fair Value of Plan Assets: | | | | | | | | | | | |
Fair Value of Plan Assets at January 1 | $ | 360,678 | | | $ | 329,781 | | | $ | — | | | $ | — | | | $ | — | | | $ | — | |
Actual Return on Plan Assets | 32,816 | | | 35,474 | | | — | | | — | | | — | | | — | |
Company Contributions | 10,000 | | | 11,200 | | | 1,562 | | | 1,505 | | | 2,695 | | | 2,662 | |
Benefit Payments | (16,282) | | | (15,777) | | | (1,562) | | | (1,505) | | | (8,385) | | | (6,694) | |
Participant Premium Payments | — | | | — | | | — | | | — | | | 5,690 | | | 4,032 | |
Fair Value of Plan Assets at December 31 | 387,212 | | | 360,678 | | | — | | | — | | | — | | | — | |
Change in Benefit Obligation: | | | | | | | | | | | |
Benefit Obligation at January 1 | $ | 428,396 | | | $ | 384,785 | | | $ | 47,894 | | | $ | 43,966 | | | $ | 70,185 | | | $ | 71,437 | |
Service Cost | 7,462 | | | 6,621 | | | 187 | | | 179 | | | 1,722 | | | 1,847 | |
Interest Cost | 11,660 | | | 13,053 | | | 1,228 | | | 1,449 | | | 1,891 | | | 2,393 | |
| | | | | | | | | | | |
Benefit Payments | (16,282) | | | (15,777) | | | (1,562) | | | (1,505) | | | (8,385) | | | (6,694) | |
Participant Premium Payments | — | | | — | | | — | | | — | | | 5,690 | | | 4,032 | |
Plan Amendments | — | | | — | | | — | | | — | | | — | | | (3,891) | |
Actuarial Loss (Gain) | (14,539) | | | 39,714 | | | (907) | | | 3,805 | | | (1,792) | | | 1,061 | |
Benefit Obligation at December 31 | $ | 416,697 | | | $ | 428,396 | | | $ | 46,840 | | | $ | 47,894 | | | $ | 69,311 | | | $ | 70,185 | |
Funded Status | $ | (29,485) | | | $ | (67,718) | | | $ | (46,840) | | | $ | (47,894) | | | $ | (69,311) | | | $ | (70,185) | |
| | | | | | | | | | | |
Amounts Recognized in Consolidated Balance Sheet at December 31: | | | | | | | | |
Current Liabilities | $ | — | | | $ | — | | | $ | (2,352) | | | $ | (1,557) | | | $ | (2,830) | | | $ | (2,826) | |
Noncurrent Liabilities and Deferred Credits | (29,485) | | | (67,718) | | | (44,488) | | | (46,337) | | | (66,481) | | | (67,359) | |
Total Liabilities | $ | (29,485) | | | $ | (67,718) | | | $ | (46,840) | | | $ | (47,894) | | | $ | (69,311) | | | $ | (70,185) | |
The accumulated benefit obligation of our Pension Plan was $378.3 million and $385.3 million as of December 31, 2021 and 2020. The accumulated benefit obligation of our ESSRP was $46.8 million and $47.7 million as of December 31, 2021 and 2020.
The following assumptions were used to determine benefit obligations as of December 31, 2021 and 2020: | | | | | | | | | | | | | | | | | | | | | | | | | | | | | | | | | | | |
| Pension Benefits (Pension Plan) | | Pension Benefits (ESSRP) | | Postretirement Benefits |
| 2021 | | 2020 | | 2021 | | 2020 | | 2021 | | 2020 |
| | | | | | | | | | | |
Discount Rate | 3.03 | % | | 2.78 | % | | 2.93 | % | | 2.61 | % | | 3.01 | % | | 2.75 | % |
Rate of Increase in Future Compensation | n/a | | n/a | | 3.00 | % | | 3.00 | % | | n/a | | n/a |
Participants to Age 39 | 4.50 | % | | 4.50 | % | | n/a | | n/a | | n/a | | n/a |
Participants Ages 40 to 49 | 3.50 | % | | 3.50 | % | | n/a | | n/a | | n/a | | n/a |
Participants Age 50 and Older | 2.75 | % | | 2.75 | % | | n/a | | n/a | | n/a | | n/a |
Healthcare Cost Immediate Trend Rate | n/a | | n/a | | n/a | | n/a | | 6.16 | % | | 6.44 | % |
Healthcare Cost Ultimate Trend Rate | n/a | | n/a | | n/a | | n/a | | 4.50 | % | | 4.50 | % |
Year the Rate Reaches the Ultimate Trend Rate | n/a | | n/a | | n/a | | n/a | | 2038 | | 2038 |
| | | | | | | | | | | |
The pension benefit liability of our Pension Plan decreased $38.2 million from December 31, 2020 to December 31, 2021 primarily due to an increase in the discount rate used to measure the obligation, from 2.78% to 3.03%, respectively, and from actual returns on Pension Plan investments in 2021 exceeding the expected return for the year.
Net Periodic Benefit Cost. A portion of service cost may be capitalized as a cost of self-constructed property, plant and equipment. When recognized in the consolidated statements of income, service cost is recognized within one of the components of operating expenses. Nonservice cost components of net periodic benefit cost may be deferred and recognized as a regulatory asset under the accounting guidance for regulated operations. When recognized in the consolidated statements of income, nonservice cost components are recognized as nonservice cost components of postretirement benefits.
The following table lists the components of net periodic benefit cost of our defined benefit pension plans and other postretirement benefits for the years ended December 31, 2021, 2020 and 2019:
| | | | | | | | | | | | | | | | | | | | | | | | | | | | | | | | | | | | | | | | | | | | | | | | | | | | | |
| Pension Benefits (Pension Plan) | | Pension Benefits (ESSRP) | | Postretirement Benefits |
(in thousands) | 2021 | | 2020 | | 2019 | | 2021 | | 2020 | | 2019 | | 2021 | | 2020 | | 2019 |
| | | | | | | | | | | | | | | | | |
Service Cost | $ | 7,462 | | | $ | 6,621 | | | $ | 5,491 | | | $ | 187 | | | $ | 179 | | | $ | 418 | | | $ | 1,722 | | | $ | 1,847 | | | $ | 1,286 | |
Interest Cost | 11,660 | | | 13,053 | | | 14,412 | | | 1,228 | | | 1,449 | | | 1,735 | | | 1,891 | | | 2,393 | | | 3,083 | |
Expected Return on Assets | (22,359) | | | (22,021) | | | (21,297) | | | — | | | — | | | — | | | — | | | — | | | — | |
Amortization of Prior Service Cost | — | | | — | | | 14 | | | — | | | — | | | 22 | | | (5,733) | | | (4,792) | | | — | |
Amortization of Net Actuarial Loss | 10,914 | | | 9,144 | | | 4,756 | | | 620 | | | 434 | | | 472 | | | 3,774 | | | 4,310 | | | 1,609 | |
Net Periodic Benefit Cost | $ | 7,677 | | | $ | 6,797 | | | $ | 3,376 | | | $ | 2,035 | | | $ | 2,062 | | | $ | 2,647 | | | $ | 1,654 | | | $ | 3,758 | | | $ | 5,978 | |
The following table includes the impact of regulation on the recognition of periodic benefit cost arising from pension and other postretirement benefits for the years ended December 31, 2021, 2020, 2019:
| | | | | | | | | | | | | | | | | |
(in thousands) | 2021 | | 2020 | | 2019 |
| | | | | |
Net Periodic Benefit Cost | $ | 11,366 | | | $ | 12,617 | | | $ | 12,001 | |
Net Amount Amortized (Deferred) Due to the Effect of Regulation | 21 | | | (533) | | | (513) | |
Net Periodic Benefit Cost Recognized | $ | 11,387 | | | $ | 12,084 | | | $ | 11,488 | |
The following assumptions were used to determine net periodic benefit cost for the years ended December 31, 2021, 2020 and 2019:
| | | | | | | | | | | | | | | | | | | | | | | | | | | | | | | | | | | | | | | | | | | | | | | | | | | | | |
| Pension Benefits (Pension Plan) | | Pension Benefits (ESSRP) | | Postretirement Benefits |
| 2021 | | 2020 | | 2019 | | 2021 | | 2020 | | 2019 | | 2021 | | 2020 | | 2019 |
| | | | | | | | | | | | | | | | | |
Discount Rate | 2.78 | % | | 3.47 | % | | 4.50 | % | | 2.61 | % | | 3.36 | % | | 4.46 | % | | 2.75 | % | | 3.43 | % | | 4.44 | % |
Long-Term Rate of Return on Plan Assets | 6.51 | % | | 6.88 | % | | 7.25 | % | | n/a | | n/a | | n/a | | n/a | | n/a | | n/a |
Rate of Increase in Future Compensation | n/a | | n/a | | n/a | | 3.00 | % | | 3.50 | % | | 3.40 | % | | n/a | | n/a | | n/a |
Participants to Age 39 | 4.50 | % | | 4.50 | % | | 4.50 | % | | n/a | | n/a | | n/a | | n/a | | n/a | | n/a |
Participants Ages 40 to 49 | 3.50 | % | | 3.50 | % | | 3.50 | % | | n/a | | n/a | | n/a | | n/a | | n/a | | n/a |
Participants Age 50 and Older | 2.75 | % | | 2.75 | % | | 2.75 | % | | n/a | | n/a | | n/a | | n/a | | n/a | | n/a |
| | | | | | | | | | | | | | | | | |
We develop our estimated discount rate through the use of a hypothetical bond portfolio method. This method derives the discount rate from the average yield of a collection of high credit quality bonds which produce cash flows similar to our anticipated future benefit payments. We estimate the assumed long-term rate of return on plan assets based primarily on asset category studies using historical market return and volatility data with forward looking estimates based on existing financial market conditions and forecasts of capital markets. Modest excess return expectations versus
some market indices are incorporated into the return projections based on the actively managed structure of the investment programs and their records of achieving such returns historically.
The following table presents the amounts not yet recognized as components of net periodic benefit cost as of December 31, 2021 and 2020:
| | | | | | | | | | | | | | | | | | | | | | | | | | | | | | | | | | | |
| Pension Benefits (Pension Plan) | | Pension Benefits (ESSRP) | | Postretirement Benefits |
(in thousands) | 2021 | | 2020 | | 2021 | | 2020 | | 2021 | | 2020 |
| | | | | | | | | | | |
Regulatory Assets: | | | | | | | | | | | |
Unrecognized Prior Service Cost | $ | — | | | $ | — | | | $ | — | | | $ | — | | | $ | (13,989) | | | $ | (19,579) | |
Unrecognized Actuarial Loss | 102,737 | | | 137,500 | | | 2,525 | | | 2,681 | | | 26,852 | | | 32,238 | |
Total Regulatory Assets | $ | 102,737 | | | $ | 137,500 | | | $ | 2,525 | | | $ | 2,681 | | | $ | 12,863 | | | $ | 12,659 | |
Accumulated Other Comprehensive Loss: | | | | | | | | | | | |
Unrecognized Prior Service Cost | $ | — | | | $ | — | | | $ | — | | | $ | 1 | | | $ | (242) | | | $ | (386) | |
Unrecognized Actuarial (Gain) Loss | (1,020) | | | 128 | | | 10,660 | | | 12,030 | | | (160) | | | 21 | |
Total Accumulated Other Comprehensive Loss | $ | (1,020) | | | $ | 128 | | | $ | 10,660 | | | $ | 12,031 | | | $ | (402) | | | $ | (365) | |
Cash Flows. We made discretionary contributions to our Pension Plan of $10.0 million, $11.2 million and $22.5 million in 2021, 2020 and 2019, respectively. As of December 31, 2021, we had no minimum funding requirements for our Pension Plan, but made a discretionary contribution of $20.0 million in February 2022. Contributions to our ESSRP and postretirement healthcare plan are equal to the benefits paid to plan participants.
The following reflects anticipated benefit payments to be paid in each of the next five years and in the aggregate for the five year period thereafter under our pension plans and postretirement healthcare plan:
| | | | | | | | | | | | | | | | | | | | | | | | | | | | | | | | | | | |
(in thousands) | 2022 | | 2023 | | 2024 | | 2025 | | 2026 | | 2027-2032 |
| | | | | | | | | | | |
Projected Pension Plan Benefit Payments | $ | 17,200 | | | $ | 17,860 | | | $ | 18,428 | | | $ | 18,947 | | | $ | 19,427 | | | $ | 102,905 | |
Projected ESSRP Benefit Payments | 1,981 | | | 2,570 | | | 2,781 | | | 2,715 | | | 2,828 | | | 14,941 | |
Projected Postretirement Benefit Payments | 3,001 | | | 3,126 | | | 3,209 | | | 3,324 | | | 3,432 | | | 17,225 | |
Total | $ | 22,182 | | | $ | 23,556 | | | $ | 24,418 | | | $ | 24,986 | | | $ | 25,687 | | | $ | 135,071 | |
401K Plan
We sponsor a 401K plan for the benefit of all corporate and subsidiary company employees. Contributions made to these plans totaled $6.5 million for 2021, $5.3 million for 2020 and $5.3 million for 2019.
11. Asset Retirement Obligations (AROs)
We have recognized AROs related to our coal-fired generation plants, natural gas combustion turbines and wind turbines. The cost of AROs include items such as site restoration, closure of ash pits, and removal of certain structures, generators, asbestos and storage tanks. We have other legal obligations associated with the retirement of a variety of other long-lived tangible assets used in electric operations where the estimated settlement costs are individually and collectively immaterial. We have no assets legally restricted for the settlement of any AROs.
A reconciliation of the carrying amounts of AROs for the years ended December 31, 2021 and 2020 is as follows:
| | | | | | | | | | | |
(in thousands) | 2021 | | 2020 |
| | | |
Beginning Balance | $ | 23,821 | | | $ | 12,656 | |
New Obligations Recognized | — | | | 8,062 | |
Adjustments Due to Revisions in Cash Flow Estimates | (568) | | | 3,110 | |
Accrued Accretion | 938 | | | 570 | |
Settlements | — | | | (577) | |
Ending Balance | $ | 24,191 | | | $ | 23,821 | |
The new AROs recognized during the year ended December 31, 2020 arose from obligations associated with our Merricourt wind farm and Astoria Station natural gas plant.
12. Income Taxes
Income before income taxes for the years ended December 31, 2021, 2020 and 2019 consists entirely of domestic earnings.
The provision for income taxes charged to income for the years ended December 31, 2021, 2020 and 2019 consisted of the following:
| | | | | | | | | | | | | | | | | |
(in thousands) | 2021 | | 2020 | | 2019 |
| | | | | |
Current | | | | | |
Federal Income Taxes | $ | 6,806 | | | $ | 3,631 | | | $ | 5,156 | |
State Income Taxes | 939 | | | 2,415 | | | 1,333 | |
Deferred | | | | | |
Federal Income Taxes | 18,180 | | | 11,450 | | | 8,859 | |
State Income Taxes | 10,716 | | | 3,751 | | | 3,167 | |
Tax Credits | | | | | |
North Dakota Wind Tax Credit Amortization, Net of Federal Tax | (586) | | | (1,033) | | | (1,033) | |
Investment Tax Credit Amortization | (3) | | | (8) | | | (41) | |
Total | $ | 36,052 | | | $ | 20,206 | | | $ | 17,441 | |
The reconciliation of the statutory federal income tax rate to our effective tax rate for each of the years ended December 31, 2021, 2020 and 2019 is as follows:
| | | | | | | | | | | | | | | | | |
| 2021 | | 2020 | | 2019 |
| | | | | |
Federal Statutory Rate | 21.0 | % | | 21.0 | % | | 21.0 | % |
Increases (Decreases) in Tax from: | | | | | |
State Taxes on Income, Net of Federal Tax | 4.7 | | | 4.0 | | | 3.4 | |
Production Tax Credits (PTCs) | (5.9) | | | (1.1) | | | — | |
Amortization of Excess Deferred Income Taxes | (2.0) | | | (3.6) | | | (3.2) | |
North Dakota Wind Tax Credit Amortization, Net of Federal Tax | (0.3) | | | (0.9) | | | (1.0) | |
Allowance for Equity Funds Used During Construction | (0.1) | | | (0.7) | | | (0.5) | |
Other, Net | (0.5) | | | (1.3) | | | (3.0) | |
Effective Tax Rate | 16.9 | % | | 17.4 | % | | 16.7 | % |
We began to generate PTCs from our Merricourt wind farm in the fourth quarter of 2020, once the asset was placed in service and commenced operations.
Deferred tax assets and liabilities were composed of the following on December 31, 2021 and 2020:
| | | | | | | | | | | |
(in thousands) | 2021 | | 2020 |
| | | |
Deferred Tax Assets | | | |
Benefit Liabilities | $ | 41,724 | | | $ | 41,292 | |
Retirement Benefits Liabilities | 40,766 | | | 40,650 | |
Tax Credit Carryforward | 32,420 | | | 35,132 | |
Regulatory Tax Liability | 34,527 | | | 33,124 | |
Cost of Removal | 26,512 | | | 25,920 | |
Differences Related to Property | 10,251 | | | 7,486 | |
Net Operating Loss Carryforward | 1,323 | | | 1,379 | |
Other | 6,999 | | | 3,423 | |
Valuation Allowance | — | | | (800) | |
Total Deferred Tax Assets | $ | 194,522 | | | $ | 187,606 | |
Deferred Tax Liabilities | | | |
Differences Related to Property | $ | (307,542) | | | $ | (271,064) | |
Retirement Benefits Regulatory Asset | (40,766) | | | (40,650) | |
Excess Tax Over Book Pension | (24,578) | | | (18,696) | |
Other | (9,904) | | | (10,572) | |
Total Deferred Tax Liabilities | $ | (382,790) | | | $ | (340,982) | |
Deferred Income Taxes | $ | (188,268) | | | $ | (153,376) | |
At December 31, 2021, we concluded, based upon all available evidence, it was more likely than not that we will generate sufficient future taxable income to realize certain of our state deferred tax assets. As a result, we released the $0.8 million valuation allowance associated with these deferred tax assets and recognized a corresponding benefit from income taxes in the consolidated statements of income for the year ended
December 31, 2021. Our conclusions regarding the realizability of such deferred tax assets was based on anticipated future taxable income within the respective state jurisdiction and the recent extension of the net operating loss carryforward period in this state.
The following is a schedule of tax credits and tax net operating losses available as of December 31, 2021 and the respective periods of expiration:
| | | | | | | | | | | | | | | | | | | | | | | |
(in thousands) | Amount | | 2022-2032 | | 2033-2038 | | 2039-2043 |
| | | | | | | |
Federal Tax Credits | $ | 9,136 | | | $ | — | | | $ | — | | | $ | 9,136 | |
State Net Operating Losses | 1,675 | | | 1,675 | | | — | | | — | |
State Tax Credits | 29,318 | | | — | | | 39 | | | 29,279 | |
| | | | | | | |
The following table summarizes the activity for unrecognized tax benefits for the years ended December 31, 2021, 2020 and 2019:
| | | | | | | | | | | | | | | | | |
(in thousands) | 2021 | | 2020 | | 2019 |
| | | | | |
Balance on January 1 | $ | 771 | | | $ | 1,488 | | | $ | 1,282 | |
Increases (decreases) for tax positions taken during a prior period | 11 | | | (178) | | | 37 | |
Increases for tax positions taken during the current period | 189 | | | 175 | | | 339 | |
Decreases due to settlements with taxing authorities | — | | | (575) | | | — | |
Decreases as a result of a lapse of applicable statutes of limitations | (144) | | | (139) | | | (170) | |
Balance on December 31 | $ | 827 | | | $ | 771 | | | $ | 1,488 | |
The balance of unrecognized tax benefits as of December 31, 2021 would reduce our effective tax rate if recognized. The total amount of unrecognized tax benefits as of December 31, 2021 is not expected to change significantly within the next 12 months. We classify interest and penalties on tax uncertainties as components of the provision for income taxes in the consolidated statements of income.
The Company and its subsidiaries file a consolidated U.S. federal income tax return and various state income tax returns. As of December 31, 2021, with limited exceptions, we are no longer subject to examinations by taxing authorities for tax years prior to 2018 for federal and North Dakota income taxes and prior to 2017 for Minnesota state income taxes.
13. Commitments and Contingencies
Commitments
Construction and Other Purchase Commitments: As of December 31, 2021, OTP had commitments under contracts, including its share of construction program and other commitments, extending into 2023 of approximately $68 million. OTP’s other commitments charged to rent expense totaled $0.3 million, $0.1 million and $0.3 million in 2021, 2020 and 2019, respectively.
Electric Utility Capacity and Energy Requirements and Coal Purchase and Delivery Contracts: OTP has commitments for the purchase of capacity and energy requirements under agreements extending into 2044. OTP also has contracts providing for the purchase and delivery of a significant portion of its current coal requirements. OTP’s current coal purchase agreements for Coyote Station expire at the end of 2040. OTP has an agreement for the purchase of Big Stone Plant’s coal requirements through December 31, 2022. There is no fixed minimum purchase requirement under this agreement but all of Big Stone Plant’s coal requirements for the period covered must be purchased under this agreement.
OTP Land Easements: OTP has commitments to make future payments for land easements not classified as leases, extending into 2050, of approximately $34.5 million. Land easement payments charged to rent expense totaled $1.3 million, $1.3 million and $0.6 million in 2021, 2020 and 2019, respectively.
Our future construction program and other commitments, capacity and energy agreement commitments, coal purchase and coal delivery contract commitments and contractual land easements payments as of December 31, 2021 are as follows:
| | | | | | | | | | | | | | | | | | | | | | | |
(in thousands) | Construction Program and Other Commitments | | Capacity and Energy Requirements | | Coal Purchase Commitments | | Land Easement Payments |
| | | | | | | |
2022 | $ | 889 | | | $ | 20,390 | | | $ | 22,793 | | | $ | 1,364 | |
2023 | 14,678 | | | 11,854 | | | 23,955 | | | 1,388 | |
2024 | 879 | | | 11,828 | | | 23,955 | | | 1,412 | |
2025 | 886 | | | 11,784 | | | 24,369 | | | 1,437 | |
2026 | 479 | | | 11,753 | | | 25,103 | | | 1,432 | |
Beyond 2026 | 6,697 | | | 109,003 | | | 428,304 | | | 27,461 | |
Total | $ | 24,508 | | | $ | 176,612 | | | $ | 548,479 | | | $ | 34,494 | |
Contingencies
FERC ROE. In November 2013 and February 2015, customers filed complaints with the FERC seeking to reduce the ROE component of the transmission rates that MISO transmission owners, including OTP, may collect under the MISO tariff rate. The FERC's most recent order, issued on November 19, 2020, adopted a revised ROE methodology and set the base ROE at 10.02% (10.52% with an adder) effective for the fifteen-month period from November 2013 to February 2015 and on a prospective basis beginning in September 2016. The order also dismissed any complaints covering the period from February 2015 to May 2016. The November 2020 opinion is subject to judicial review. We have deferred recognition and recorded a refund liability of $2.5 million as of December 31, 2021. This refund liability reflects our best estimate of required refunds to customers once all regulatory and judicial proceedings are finalized.
Regional Haze Rule (RHR). The RHR was adopted in an effort to improve visibility in national parks and wilderness areas. The RHR requires states, in coordination with the EPA and other governmental agencies, to develop and implement plans to achieve natural visibility conditions. The second RHR implementation period covers the years 2018-2028. States are required to submit a state implementation plan to assess reasonable progress with the RHR and determine what additional emission reductions are appropriate, if any.
Coyote Station, OTP's jointly owned coal-fired power plant in North Dakota, is subject to assessment in the second implementation period under the North Dakota state implementation plan. In September 2021, the North Dakota Department of Environmental Quality (NDDEQ) made public a draft of its state implementation plan. The plan concluded it is not reasonable to require additional emission controls during this planning period. Following a consultation and public comment period, and any subsequent modifications to the plan, the NDDEQ will submit its state implementation plan to the EPA for approval. In January 2022, prior to the submission to the EPA by the NDDEQ, the EPA provided preliminary comments on the draft North Dakota state implementation plan in which it expressed disagreement with the NDDEQ's recommendation to forgo additional emission controls.
We cannot predict with certainty the impact the state implementation plan may have on our business until the state implementation plan has been approved or otherwise fully acted on by the EPA. However, significant emission control investments could be required and the recovery of such costs from customers would require regulatory approval. Alternatively, investments in emission control equipment may prove to be uneconomic and result in the early retirement of, or the sale of our interest in, Coyote Station, subject to regulatory approval. We cannot estimate the financial effects such a retirement or sale may have on our consolidated operating results, financial position or cash flows, but such amounts could be material and the recovery of such costs from customers would be subject to regulatory approval.
Westmoreland Coal Company (Westmoreland) Arbitration. In December 2018, insurers for Westmoreland, Westmoreland and its affiliated companies filed an arbitration demand against the co-owners of Coyote Station, including OTP, a 35% co-owner. The claimant insurers were pursuing recovery in the amount of $5.5 million, plus prejudgment interest to recover business interruption insurance proceeds paid to Westmoreland or its affiliates arising from a boiler feed pump explosion in December 2014 at the facility. The explosion and ensuing repairs reduced the amount of coal purchased from a Westmoreland affiliate under an existing coal purchase agreement. The Westmoreland insurers claimed the co-owners breached the minimum purchase obligations in the coal purchase agreement. As of December 31, 2021, an agreement to settle the matter was reached, and OTP's proportionate share of the settlement payment did not have a material effect on its 2021 financial results.
Other Contingencies. We are party to litigation and regulatory enforcement matters arising in the normal course of business. We regularly analyze relevant information and, as necessary, estimate and record accrued liabilities for matters in which a loss is probable of occurring and can be reasonably estimated. We believe the effect on our consolidated operating results, financial position and cash flows, if any, for the disposition of all matters pending as of December 31, 2021, other than those relating to the RHR, will not be material.
14. Stockholders' Equity
Capital Structure
In addition to authorized and outstanding common stock, the Company has 1,500,000 authorized no par value cumulative preferred shares and 1,000,000 authorized no par value cumulative preference shares. No cumulative preferred or cumulative preference shares were outstanding at December 31, 2021 or 2020.
Shelf Registrations
On May 3, 2021, upon the expiration of a prior shelf registration, we filed a shelf registration statement with the SEC under which we may offer for sale, from time to time, either separately or together in any combination, equity, debt or other securities described in the shelf registration statement. The registration statement expires in May 2024. No shares were issued pursuant to the shelf registration in 2021.
On May 3, 2021, upon the expiration of a second prior shelf registration, we filed a second registration statement with the SEC for the issuance of up to 1,500,000 common shares under an Automatic Dividend Reinvestment and Share Purchase Plan, which provides shareholders, retail customers of OTP and other interested investors a method of purchasing our common shares by reinvesting their dividends and/or making optional cash investments. Shares purchased under the plan may be new issue common shares or common shares purchased on the open market. In 2021, we issued 115,180 shares under this program and no proceeds were received, as all shares issued were purchased on the open market. As of December 31, 2021, 1,384,820 shares remain available for purchase or issuance under the Plan. The shelf registration for the plan expires in May 2024.
Dividend Restrictions
OTC is a holding company with no significant operations of its own. The primary source of funds for payments of dividends to our shareholders is from dividends paid or distributions made by our subsidiaries. As a result of certain statutory limitations or regulatory or financing agreements, restrictions could occur on the amount of distributions allowed to be made by our subsidiaries. Both the OTC Credit Agreement and OTP Credit
Agreement contain restrictions on the payment of cash dividends upon a default or event of default, including failure to maintain certain financial covenants. As of December 31, 2021, we were in compliance with these financial covenants.
Under the Federal Power Act, a public utility may not pay dividends from any funds properly included in a capital account. What constitutes “funds properly included in a capital account” is undefined in the Federal Power Act and the related regulations; however, the FERC has consistently interpreted the provision to allow dividends to be paid as long as i) the source of the dividends is clearly disclosed, ii) the dividend is not excessive and iii) there is no self-dealing on the part of corporate officials.
The MPUC indirectly limits the amount of dividends OTP can pay to the Company by requiring an equity-to-total-capitalization ratio between 47.5% and 58.1% based on OTP’s capital structure requirements as of December 31, 2021. As of December 31, 2021, OTP’s equity-to-total-capitalization ratio including short-term debt was 52.5% and its net assets restricted from distribution totaled approximately $681.2 million. Under the current capital structure requirement as of December 31, 2021, total capitalization for OTP could not exceed $1.7 billion. The MPUC approved OTP’s most recent capital structure petition on January 26, 2022, allowing for an equity-to-total-capitalization ratio between 48.0% and 58.7%, with total capitalization not to exceed $1.7 billion.
15. Accumulated Other Comprehensive Income (Loss)
The Company's other comprehensive income consists of unamortized actuarial losses and prior service costs related to pension and other postretirement benefits and unrealized gains and losses on marketable securities classified as available-for-sale. The income tax expense or benefit associated with amounts reclassified from accumulated other comprehensive income (loss) and reflected in the consolidated statement of income are recognized in the same period as the amounts are reclassified.
The following table shows the changes in accumulated other comprehensive loss for the years ended December 31, 2021, 2020 and 2019:
| | | | | | | | | | | | | | | | | |
(in thousands) | Pension and Other Postretirement Benefits | | Net Unrealized Gain (Losses) on Available-for-Sale Securities | | Total |
| | | | | |
Balance, December 31, 2018 | $ | (4,059) | | | $ | (85) | | | $ | (4,144) | |
Other Comprehensive Income (Loss) Before Reclassifications, net of tax | 418 | | | 116 | | | 534 | |
Amounts Reclassified from Accumulated Other Comprehensive Income (Loss) | (2,056) | | (1) | 13 | | (2) | (2,043) | |
Total Other Comprehensive Income (Loss) | (1,638) | | | 129 | | | (1,509) | |
Stranded Tax Transfer | (794) | | | 10 | | | (784) | |
Balance, December 31, 2019 | (6,491) | | | 54 | | | (6,437) | |
Other Comprehensive Income (Loss) Before Reclassifications, net of tax | 418 | | | 145 | | | 563 | |
Amounts Reclassified from Accumulated Other Comprehensive Income (Loss) | (2,643) | | (1) | 10 | | (2) | (2,633) | |
Total Other Comprehensive Income (Loss) | (2,225) | | | 155 | | | (2,070) | |
Balance, December 31, 2020 | (8,716) | | | 209 | | | (8,507) | |
Other Comprehensive Income (Loss) Before Reclassifications, net of tax | 1,638 | | | (132) | | | 1,506 | |
Amounts Reclassified from Accumulated Other Comprehensive Income (Loss) | 541 | | (1) | (64) | | (2) | 477 | |
Total Other Comprehensive Income (Loss) | 2,179 | | | (196) | | | 1,983 | |
Balance, December 31, 2021 | $ | (6,537) | | | $ | 13 | | | $ | (6,524) | |
(1) Included in the computation of net periodic pension and other postretirement benefit costs. See Note 10 for further information. |
(2) Included in other income (expense), net on the accompanying consolidated statements of income. |
16. Share-Based Payments
Employee Stock Purchase Plan
The 1999 Employee Stock Purchase Plan authorizes the issuance of 1,400,000 common shares, allowing eligible employees to purchase our common shares through payroll withholding at a discount of up to 15% off the market price at the end of each six-month purchase period. Employee withholding amounts may not be less than $10 or more than $2,000 per month, subject to certain limitations, as described in the plan. A plan participant may cease making payroll deductions at any time. A participant may not purchase more than 2,000 shares in a given six month purchase period under the plan and may not purchase more than $25,000 (fair market value) of common shares under the plan and all other purchase plans (if any) in a calendar year. A participant may withdraw from the plan at any time and elect to receive the balance of their contributions to the plan that have not yet been used to purchase shares in cash. Shares purchased under the plan are automatically enrolled in the Company's dividend reinvestment plan. Shares purchased under the plan may not be assigned, transferred, pledged, or otherwise disposed, except for certain situations allowed by the plan, such as upon death, for a period of 18 months after purchase. For purchase periods between January 1, 2018 and June 30, 2019, the purchase price was 100% of the market price at the end of each six-month purchase period. For purchase periods beginning after June 30, 2019, the purchase price is 85% of the market price at the end of each six-month purchase period. At our discretion, shares purchased under the plan can be either new issue shares or shares purchased in the open market. The plan shall automatically terminate when all of the shares authorized under the plan have been issued.
We recognize the 15% discount to the fair market value of the purchased shares as stock-based compensation expense, which amounted to $0.2 million, $0.2 million and $0.1 million for the years ended December 31, 2021, 2020, and 2019. For the years ended December 31, 2021, 2020, and 2019 the amount of shares issued under the plan amounted to 27,975, 31,661 and 17,104 shares. As of December 31, 2021, there was 290,127 shares available for purchase under the plan.
Share-Based Compensation Plan
The 2014 Stock Incentive Plan, which was approved by our shareholders in April 2014, authorizes the issuance of 1,900,000 common shares for the granting of stock options, stock appreciation rights, restricted stock, restricted stock units, performance awards and other stock and stock-based awards. As of December 31, 2021, 722,200 shares were available for issuance under the plan. The plan terminates on December 31, 2023.
We grant restricted stock awards to our employees and members of our Board of Directors and stock performance awards to our executive officers and certain other key employees as part of our long-term compensation and retention program. Stock-based compensation cost, recognized within operating expenses in the consolidated statements of income, amounted to $6.7 million, $6.1 million and $5.9 million for the years ended December 31, 2021, 2020 and 2019. The related income tax benefit recognized for these periods amounted to $1.8 million, $2.1 million and $2.3 million.
Restricted Stock Awards. Restricted stock awards are granted to employees and members of the Company's Board of Directors. The awards vest, depending on award recipient, either ratably over a period of three to four years or cliff vest after four years. Vesting is accelerated in certain circumstances, including upon retirement. Awards granted to members of the Board of Directors are issued and outstanding upon grant and carry the same voting and dividend rights of unrestricted outstanding common stock. Awards granted to executive officers and other key employees are eligible to receive dividend equivalent payments during the vesting period, subject to forfeiture under the terms of the agreement, but such awards are not issued or outstanding upon grant and do not provide for voting rights.
The grant date fair value of each restricted stock award is determined based on the market price of the Company's common stock on the date of grant adjusted to exclude the value of dividends for those awards that do not receive dividend or dividend equivalent payments during the vesting period.
The following is a summary of restricted stock award activity for the year ended December 31, 2021:
| | | | | | | | | | | |
| Shares | | Weighted Average Grant-Date Fair Value |
| | | |
Nonvested, Beginning of Year | 128,664 | | | $ | 44.30 | |
Granted | 59,150 | | | 43.55 | |
Vested | (47,646) | | | 42.98 | |
Forfeited | (2,075) | | | 40.95 | |
Nonvested, End of Year | 138,093 | | | $ | 44.48 | |
The weighted-average grant date fair value of granted awards was $43.55, $45.97 and $48.18 during the years ended December 31, 2021, 2020 and 2019. The fair value of vested awards was $2.1 million, $2.8 million and $2.4 million during the years ended December 31, 2021, 2020 and 2019. As of December 31, 2021, there was $2.4 million of unrecognized compensation costs for non-vested restricted stock awards to be recognized over a weighted-average period of 1.83 years.
Stock Performance Awards. Stock performance awards are granted to executive officers and certain other key employees. The awards vest at the end of a three-year performance period. The number of common shares awarded, if any, at the end of the performance period ranges from zero to 150% of the target amount based on two performance measures: i) total shareholder return relative to a peer group and ii) return on equity. The awards have no voting or dividend rights during the vesting period. Vesting of the awards is accelerated in certain circumstances, including upon retirement. The amount of common shares awarded on an accelerated vesting is based either on actual performance at the end of the performance period or the amount of common shares earned at target.
The grant date fair value of stock performance awards granted during the years ended December 31, 2021, 2020 and 2019 was determined using a Monte Carlo fair value simulation model incorporating the following assumptions:
| | | | | | | | | | | | | | | | | |
| 2021 | | 2020 | | 2019 |
| | | | | |
Risk-free interest rate | 0.18 | % | | 1.42 | % | | 2.52 | % |
Expected term (in years) | 3.00 | | 3.00 | | 3.00 |
Expected volatility | 32.00 | % | | 19.00 | % | | 21.00 | % |
Dividend yield | 3.60 | % | | 2.80 | % | | 3.00 | % |
| | | | | |
The risk-free interest rate was derived from yields on U.S. government bonds of a similar term. The expected term of the award is equal to the three-year performance period. Expected volatility was estimated based on actual historical volatility of our common stock over a three- or five-year period. Dividend yield was estimated based on historic and future yield estimates.
The following is a summary of stock performance award activity for the year ended December 31, 2021 (share amounts reflect awards at target):
| | | | | | | | | | | |
| Shares | | Weighted Average Grant-Date Fair Value |
| | | |
Nonvested, Beginning of Year | 164,600 | | | $ | 42.32 | |
Granted | 79,000 | | | 38.34 | |
Vested | (54,000) | | | 35.73 | |
Forfeited | — | | | — | |
Nonvested, End of Year | 189,600 | | | $ | 42.54 | |
The weighted-average grant date fair value of granted awards was $38.34, $47.79 and $42.87 during the years ended December 31, 2021, 2020 and 2019. The fair value of vested awards was $2.5 million, $3.4 million and $6.1 million during the years ended December 31, 2021, 2020 and 2019. As of December 31, 2021, there was $0.4 million of unrecognized compensation costs of non-vested stock performance awards to be recognized over a weighted-average period of 1.19 years.
17. Earnings Per Share
The numerator used in the calculation of both basic and diluted earnings per share is net income. The denominator used in the calculation of basic earnings per share is the weighted average number of shares outstanding during the period. The denominator used in the calculation of diluted earnings per share is derived by adjusting basic shares outstanding for the dilutive effect of potential shares outstanding, which consist of time and performance based stock awards and employee stock purchase plan shares.
The following includes the computation of the denominator for basic and diluted weighted-average shares outstanding for the years ended December 31, 2021, 2020 and 2019:
| | | | | | | | | | | | | | | | | |
(in thousands) | 2021 | | 2020 | | 2019 |
| | | | | |
Weighted Average Common Shares Outstanding – Basic | 41,491 | | | 40,710 | | | 39,721 | |
Effect of Dilutive Securities: | | | | | |
Stock Performance Awards | 226 | | | 116 | | | 147 | |
Restricted Stock Awards | 87 | | | 63 | | | 81 | |
Employee Stock Purchase Plan Shares and Other | 14 | | | 16 | | | 5 | |
Dilutive Effect of Potential Common Shares | 327 | | | 195 | | | 233 | |
Weighted Average Common Shares Outstanding – Diluted | 41,818 | | | 40,905 | | | 39,954 | |
The amount of shares excluded from diluted weighted-average common shares outstanding because such shares were anti-dilutive was not material for the years ended December 31, 2021, 2020 and 2019.
18. Derivative Instruments
OTP enters into derivative instruments to manage its exposure to future commodity price variability and reduce volatility in prices for our retail electric customers. These derivative instruments are not designated as qualifying hedging transactions but provide for an economic hedge against future price variability. The instruments are recorded at fair value on the consolidated balance sheets, with changes in fair value recorded in the consolidated statements of income. However, in accordance with rate-making and cost recovery processes, we recognize a regulatory asset or liability to defer losses or gains from derivative activity until settlement of the associated derivative instrument.
As of December 31, 2021, OTP had outstanding pay-fixed, receive-variable swap agreements with an aggregate notional amount of 263,400 megawatt-hours of electricity, and various settlement dates throughout 2022. As of December 31, 2021, the aggregate fair value of these contracts was $6.2 million, which is included in other current assets on the consolidated balance sheets. During the year ended December 31, 2021, contracts matured and were settled in an aggregate amount of $3.1 million.
19. Fair Value Measurements
The following tables present our assets measured at fair value on a recurring basis as of December 31, 2021 and 2020 classified by the input method used to measure fair value: | | | | | | | | | | | | | | | | | |
| Level 1 | | Level 2 | | Level 3 |
| | | | | |
December 31, 2021 | | | | | |
Investments: | | | | | |
Money Market Funds | $ | 949 | | | $ | — | | | $ | — | |
Mutual Funds | 5,432 | | | — | | | — | |
Corporate Debt Securities | — | | | 1,333 | | | — | |
Government-Backed and Government-Sponsored Enterprises’ Debt Securities | — | | | 7,869 | | | — | |
Derivative Instruments | — | | | 6,214 | | | — | |
Total Assets | $ | 6,381 | | | $ | 15,416 | | | $ | — | |
December 31, 2020 | | | | | |
Investments: | | | | | |
Money Market Funds | $ | 4,075 | | | $ | — | | | $ | — | |
Mutual Funds | 1,662 | | | — | | | — | |
Corporate Debt Securities | — | | | 2,627 | | | — | |
Government-Backed and Government-Sponsored Enterprises’ Debt Securities | — | | | 6,633 | | | — | |
Total Assets | $ | 5,737 | | | $ | 9,260 | | | $ | — | |
The level 2 fair value measurements for government-backed and government-sponsored enterprises’ and corporate debt securities are determined on the basis of valuations provided by a third-party pricing service which utilizes industry accepted valuation models and observable market inputs to determine valuation. Some valuations or model inputs used by the pricing service may be based on broker quotes.
The level 2 fair value measurements for derivative instruments are determined by using inputs such as forward electric commodity prices, adjusted for location differences. These inputs are observable in the marketplace throughout the full term of the instrument, can be derived from observable data, or are supported by observable levels at which transactions are executed in the marketplace.
In addition to assets recorded at fair value on a recurring basis, we also hold financial instruments that are not recorded at fair value in the consolidated balance sheets but for which disclosure of the fair value of these financial instruments is provided. The following reflects the carrying value and estimated fair value of these assets and liabilities as of December 31, 2021 and 2020:
| | | | | | | | | | | | | | | | | | | | | | | |
| December 31, 2021 | | December 31, 2020 |
(in thousands) | Carrying Amount | | Fair Value | | Carrying Amount | | Fair Value |
| | | | | | | |
Assets: | | | | | | | |
Cash and Cash Equivalents | $ | 1,537 | | | $ | 1,537 | | | $ | 1,163 | | | $ | 1,163 | |
Total | 1,537 | | | 1,537 | | | 1,163 | | | 1,163 | |
Liabilities: | | | | | | | |
Short-Term Debt | 91,163 | | | 91,163 | | | 80,997 | | | 80,997 | |
Long-Term Debt | 763,997 | | | 878,272 | | | 764,519 | | | 858,455 | |
Total | $ | 855,160 | | | $ | 969,435 | | | $ | 845,516 | | | $ | 939,452 | |
| | | | | | | |
The following methods and assumptions were used to estimate the fair value of each class of financial instruments:
Cash Equivalents: The carrying amount approximates fair value because of the short-term maturity of these instruments.
Short-Term Debt: The carrying amount approximates fair value because the debt obligations are short-term in nature and balances outstanding are subject to variable rates of interest which reset frequently, a Level 2 fair value input.
Long-Term Debt: The fair value of long-term debt is estimated based on current market indications for borrowings of similar maturities with similar terms, a Level 2 fair value input.
| | | | | |
ITEM 9. | CHANGES IN AND DISAGREEMENTS WITH ACCOUNTANTS ON ACCOUNTING AND FINANCIAL DISCLOSURE |
None.
| | | | | |
ITEM 9A. | CONTROLS AND PROCEDURES |
Evaluation of Disclosures Controls and Procedures. Under the supervision and with the participation of the Company’s management, including the Chief Executive Officer and the Chief Financial Officer, the Company evaluated the effectiveness of the design and operation of its disclosure controls and procedures (as defined in Rule 13a-15(e) under the Securities Exchange Act of 1934 (the Exchange Act)) as of December 31, 2021, the end of the period covered by this report. Based on that evaluation, the Chief Executive Officer and Chief Financial Officer concluded that the Company’s disclosure controls and procedures were effective as of December 31, 2021.
Changes in Internal Control over Financial Reporting. There were no changes in the Company’s internal control over financial reporting (as defined in Rules 13a-15(f) under the Exchange Act) during the fourth quarter ended December 31, 2021 that have materially affected, or are reasonably likely to materially affect, the Company’s internal control over financial reporting.
Management’s Report Regarding Internal Control Over Financial Reporting. Management is responsible for the preparation and integrity of the consolidated financial statements and representations in this report on Form 10-K. The consolidated financial statements of the Company have been prepared in conformity with generally accepted accounting principles applied on a consistent basis and include some amounts that are based on informed judgments and best estimates and assumptions of management.
In order to assure the consolidated financial statements are prepared in conformance with generally accepted accounting principles, management is responsible for establishing and maintaining adequate internal control over financial reporting, as such term is defined in Exchange Act Rule 13a-15(f). These internal controls are designed only to provide reasonable assurance, on a cost-effective basis, that transactions are carried out in accordance with management’s authorizations and assets are safeguarded against loss from unauthorized use or disposition.
Management has completed its assessment of the effectiveness of the Company’s internal control over financial reporting as of December 31, 2021. In making this assessment, management used the criteria set forth by the Committee of Sponsoring Organizations of the Treadway Commission in Internal Control - Integrated Framework (2013) to conduct the required assessment of the effectiveness of the Company’s internal control over financial reporting. Based on this assessment, management concluded that, as of December 31, 2021, the Company’s internal control over financial reporting was effective based on those criteria. The Company’s independent registered public accounting firm, Deloitte & Touche LLP, has audited the Company’s consolidated financial statements included in this report on Form 10-K and issued an attestation report on the Company’s internal control over financial reporting.
Attestation Report of Independent Registered Public Accounting Firm. The attestation report of Deloitte & Touche LLP, the Company’s independent registered public accounting firm, regarding the Company’s internal control over financial reporting is provided in Item 8 of this report on Form 10-K.
| | | | | |
ITEM 9B. | OTHER INFORMATION |
None.
| | | | | |
ITEM 9C. | DISCLOSURE REGARDING FOREIGN JURISDICTIONS THAT PREVENT INSPECTIONS |
Not applicable.
PART III
| | | | | |
ITEM 10. | DIRECTORS, EXECUTIVE OFFICERS AND CORPORATE GOVERNANCE |
The information required by this Item regarding Directors is incorporated by reference to the information under “Election of Directors” in the Company's definitive Proxy Statement for the 2022 Annual Meeting. The information regarding executive officers and family relationships is set forth in Item 3A of this report on Form 10-K. The information required by this Item regarding the Company’s procedures for recommending nominees to the board of directors is incorporated by reference to the information under “Corporate Governance – Director Nomination Process” in the Company’s definitive Proxy Statement for the 2022 Annual Meeting. The information required by this Item regarding the Audit Committee and the Company’s Audit Committee financial experts is incorporated by reference to the information under “Committees of the Board of Directors – Audit Committee” in the Company’s definitive Proxy Statement for the 2022 Annual Meeting.
The Company has adopted a code of business ethics that applies to all of its directors, officers (including its principal executive officer, principal financial officer, and its principal accounting officer or controller or person performing similar functions) and employees. The Company’s code of business ethics is available on its website at www.ottertail.com. The Company intends to satisfy the disclosure requirements under Item 5.05 of Form 8-K regarding an amendment to, or waiver from, a provision of its code of business ethics by posting such information on its website at the address specified above. Information on the Company’s website is not deemed to be incorporated by reference into this report on Form 10-K.
| | | | | |
ITEM 11. | EXECUTIVE COMPENSATION |
The information required by this Item is incorporated by reference to the information under “Compensation Discussion and Analysis,” “Report of Compensation and Human Capital Management Committee,” “Executive Compensation,” “Pay Ratio Disclosure” and “Director Compensation” in the Company's definitive Proxy Statement for the 2022 Annual Meeting.
| | | | | |
ITEM 12. | SECURITY OWNERSHIP OF CERTAIN BENEFICIAL OWNERS AND MANAGEMENT AND RELATED STOCKHOLDER MATTERS |
The information required by this Item regarding security ownership is incorporated by reference to the information under “Security Ownership of Certain Beneficial Owners” in the Company’s definitive Proxy Statement for the 2022 Annual Meeting.
EQUITY COMPENSATION PLAN INFORMATION
The following table sets forth information as of December 31, 2021 about the Company’s common stock that may be issued under all its equity compensation plans: | | | | | | | | | | | | | | | | | | | | | | | |
| Number of securities to be issued upon exercise of outstanding options, warrants and rights | | | Weighted average exercise price of outstanding options, warrants and rights | | Number of securities remaining available for future issuance under equity compensation plans (excluding securities reflected in column (a)) | |
Plan Category | (a) | | | (b) | | (c) | |
| | | | | | | |
Equity compensation plans approved by security holders: | | | | | | | |
2014 Stock Incentive Plan | 387,313 | | (1) | | $ | 0.00 | | | 722,200 | | (2) |
1999 Employee Stock Purchase Plan | — | | | | N/A | | 290,127 | | (3) |
Equity compensation plans not approved by security holders | — | | | | — | | | — | | |
Total | 387,313 | | | | — | | | 1,012,327 | | |
(1)Includes 118,500, 82,500 and 83,400 performance-based share awards, assuming a maximum payout, granted in 2021, 2020 and 2019, respectively, 102,265 restricted stock units outstanding as of December 31, 2021, and 648 stock units outstanding as part of the director deferred compensation program and excludes 35,828 shares of restricted stock issued to members of the board of directors.
(2)The 2014 Stock Incentive Plan provides for the issuance of any shares available under the plan in the form of restricted stock, restricted stock units, performance awards and other types of stock-based awards, in addition to the granting of options, warrants or stock appreciation rights.
(3)Shares to be issued based on employee’s election to participate in the plan.
| | | | | |
ITEM 13. | CERTAIN RELATIONSHIPS AND RELATED TRANSACTIONS, AND DIRECTOR INDEPENDENCE |
The information required by this Item is incorporated by reference to the information under “Policy and Procedures Regarding Transactions with Related Persons,” “Election of Directors” and “Committees of the Board of Directors” in the Company’s definitive Proxy Statement for the 2022 Annual Meeting.
| | | | | |
ITEM 14. | PRINCIPAL ACCOUNTANT FEES AND SERVICES |
The information required by this Item is incorporated by reference to the information under “Ratification of Independent Registered Public Accounting Firm – Fees” and “Ratification of Independent Registered Public Accounting Firm – Pre-Approval of Audit/Non-Audit Services Policy” in the Company’s definitive Proxy Statement for the 2022 Annual Meeting.
PART IV
| | | | | |
ITEM 15. | EXHIBITS AND FINANCIAL STATEMENT SCHEDULES |
1. Financial Statements | | | | | |
| Page |
| |
Consolidated Balance Sheets | |
Consolidated Statements of Income | |
| |
| |
| |
| |
2. Financial Statement Schedules
Schedule I - Condensed Financial Information of Registrant
Schedule II - Valuation and Qualifying Accounts and Reserves
SCHEDULE I - CONDENSED FINANCIAL INFORMATION OF REGISTRANT
OTTER TAIL CORPORATION (PARENT COMPANY)
CONDENSED BALANCE SHEETS
| | | | | | | | | | | |
| December 31, |
(in thousands) | 2021 | | 2020 |
| | | |
Assets | | | |
Current Assets | | | |
Cash and Cash Equivalents | $ | 3 | | | $ | — | |
Accounts Receivable | 25 | | | 148 | |
Accounts Receivable from Subsidiaries | 2,817 | | | 2,734 | |
Interest Receivable from Subsidiaries | 117 | | | 117 | |
Notes Receivable from Subsidiaries | 6,767 | | | — | |
Other | 1,410 | | | 1,063 | |
Total Current Assets | 11,139 | | | 4,062 | |
Investments in Subsidiaries | 1,184,564 | | | 1,061,009 | |
Notes Receivable from Subsidiaries | 78,900 | | | 79,069 | |
Deferred Income Taxes | 29,619 | | | 28,793 | |
Other Assets | 44,749 | | | 40,848 | |
Total Assets | $ | 1,348,971 | | | $ | 1,213,781 | |
| | | |
Liabilities and Stockholders' Equity | | | |
Current Liabilities | | | |
Short-Term Debt | $ | 22,637 | | | $ | 65,166 | |
Current Maturities of Long-Term Debt | — | | | 169 | |
Accounts Payable to Subsidiaries | 181 | | | 7 | |
Notes Payable to Subsidiaries | 190,204 | | | 134,352 | |
Other | 14,526 | | | 12,931 | |
Total Current Liabilities | 227,548 | | | 212,625 | |
Other Noncurrent Liabilities | 50,900 | | | 50,495 | |
Commitments and Contingencies | | | |
Capitalization | | | |
Long-Term Debt, Net of Current Maturities | 79,746 | | | 79,695 | |
Common Stockholders' Equity | 990,777 | | | 870,966 | |
Total Capitalization | 1,070,523 | | | 950,661 | |
Total Liabilities and Stockholders' Equity | $ | 1,348,971 | | | $ | 1,213,781 | |
See accompanying notes to condensed financial statements.
OTTER TAIL CORPORATION (PARENT COMPANY)
CONDENSED STATEMENTS OF INCOME | | | | | | | | | | | | | | | | | |
| Years Ended December 31, |
(in thousands) | 2021 | | 2020 | | 2019 |
| | | | | |
Income | | | | | |
Equity Income in Earnings of Subsidiaries | $ | 188,375 | | | $ | 106,379 | | | $ | 93,731 | |
Interest Income from Subsidiaries | 2,826 | | | 2,859 | | | 3,063 | |
Other Income | 1,290 | | | 1,317 | | | 1,566 | |
Total Income | 192,491 | | | 110,555 | | | 98,360 | |
Expense | | | | | |
Operating Expenses | 14,825 | | | 14,007 | | | 10,529 | |
Interest Charges | 4,727 | | | 4,599 | | | 4,863 | |
Interest Charges from Subsidiaries | 3 | | | 136 | | | 306 | |
Nonservice Cost Components of Postretirement Benefits | 1,097 | | | 1,150 | | | 1,297 | |
Total Expense | 20,652 | | | 19,892 | | | 16,995 | |
Income Before Income Taxes | 171,839 | | | 90,663 | | | 81,365 | |
Income Tax Benefit | 4,930 | | | 5,188 | | | 5,482 | |
Net Income | $ | 176,769 | | | $ | 95,851 | | | $ | 86,847 | |
See accompanying notes to condensed financial statements.
OTTER TAIL CORPORATION (PARENT COMPANY)
CONDENSED STATEMENTS OF CASH FLOWS
| | | | | | | | | | | | | | | | | |
| Years Ended December 31, |
(in thousands) | 2021 | | 2020 | | 2019 |
| | | | | |
Cash Flows from Operating Activities | | | | | |
Net Cash Provided by Operating Activities | $ | 60,695 | | | $ | 54,027 | | | $ | 52,263 | |
Cash Flows from Investing Activities | | | | | |
Investment in Subsidiaries | — | | | (150,000) | | | (34,990) | |
Debt Repaid by Subsidiaries | 169 | | | 182 | | | 1,338 | |
Cash Used in Investing Activities | (884) | | | (2,419) | | | (257) | |
Net Cash Used in Investing Activities | (715) | | | (152,237) | | | (33,909) | |
Cash Flows from Financing Activities | | | | | |
Net (Repayments) Borrowings on Short-Term Debt | (42,529) | | | 59,166 | | | (3,215) | |
Borrowings from Subsidiaries | 49,085 | | | 44,741 | | | 28,985 | |
Proceeds from Issuance of Common Stock | 696 | | | 52,432 | | | 20,338 | |
Payments for Shares Withheld for Employee Tax Obligations | (1,507) | | | (2,069) | | | (2,730) | |
Payments for Retirement of Long-Term Debt | (169) | | | (182) | | | (172) | |
Dividends Paid | (64,864) | | | (60,314) | | | (55,723) | |
Other, net | (689) | | | (523) | | | (878) | |
Net Cash Used in (Provided by) Financing Activities | (59,977) | | | 93,251 | | | (13,395) | |
Net Change in Cash and Cash Equivalents | 3 | | | (4,959) | | | 4,959 | |
Cash and Cash Equivalents at Beginning of Period | — | | | 4,959 | | | — | |
Cash and Cash Equivalents at End of Period | $ | 3 | | | $ | — | | | $ | 4,959 | |
See accompanying notes to condensed financial statements.
OTTER TAIL CORPORATION (PARENT COMPANY)
NOTES TO CONDENSED FINANCIAL STATEMENTS
Incorporated by Reference
OTC’s consolidated statements of comprehensive income and common shareholders’ equity in Part II, Item 8 are incorporated by reference.
Basis of Presentation
The condensed financial information of OTC is presented to comply with Rule 12-04 of Regulation S-X. The unconsolidated condensed financial statements do not reflect all of the information and notes normally included with financial statements prepared in accordance with GAAP. Therefore, these condensed financial statements should be read with the consolidated financial statements and related notes included in this report on Form 10-K.
OTC’s investments in subsidiaries are presented under the equity method of accounting. Under this method, the assets and liabilities of subsidiaries are not consolidated. The investments in net assets of the subsidiaries are recorded in the balance sheets. The income from operations of the subsidiaries is reported on a net basis as equity income in earnings of subsidiaries.
Related Party Transactions
Outstanding receivables from and payables to our subsidiaries as of December 31, 2021 and 2020 are as follows:
| | | | | | | | | | | | | | | | | | | | | | | | | | | | | | | | | | | |
(in thousands) | Accounts Receivable | | Interest Receivable | | Current Notes Receivable | | Long-Term Notes Receivable | | Accounts Payable | | Current Notes Payable |
| | | | | | | | | | | |
December 31, 2021 | | | | | | | | | | | |
Otter Tail Power Company | $ | 2,503 | | | $ | — | | | $ | — | | | $ | — | | | $ | 7 | | | $ | — | |
Northern Pipe Products, Inc. | — | | | 7 | | | — | | | 5,000 | | | 4 | | | 32,057 | |
Vinyltech Corporation | 13 | | | 18 | | | — | | | 11,500 | | | — | | | 34,881 | |
BTD Manufacturing, Inc. | — | | | 77 | | | 6,767 | | | 52,000 | | | 170 | | | — | |
T.O. Plastics, Inc. | 20 | | | 15 | | | — | | | 10,400 | | | — | | | 5,995 | |
Varistar Corporation | — | | | — | | | — | | | — | | | — | | | 117,271 | |
Otter Tail Assurance Limited | 281 | | | — | | | — | | | — | | | — | | | — | |
| $ | 2,817 | | | $ | 117 | | | $ | 6,767 | | | $ | 78,900 | | | $ | 181 | | | $ | 190,204 | |
December 31, 2020 | | | | | | | | | | | |
Otter Tail Power Company | $ | 2,698 | | | $ | — | | | $ | — | | | $ | — | | | $ | 7 | | | $ | — | |
Northern Pipe Products, Inc. | — | | | 8 | | | — | | | 5,169 | | | — | | | 9,103 | |
Vinyltech Corporation | — | | | 17 | | | — | | | 11,500 | | | — | | | 18,004 | |
BTD Manufacturing, Inc. | — | | | 77 | | | — | | | 52,000 | | | — | | | 30,344 | |
T.O. Plastics, Inc. | — | | | 15 | | | — | | | 10,400 | | | — | | | 3,101 | |
Varistar Corporation | — | | | — | | | — | | | — | | | — | | | 73,800 | |
Otter Tail Assurance Limited | 36 | | | — | | | — | | | — | | | — | | | — | |
| $ | 2,734 | | | $ | 117 | | | $ | — | | | $ | 79,069 | | | $ | 7 | | | $ | 134,352 | |
Dividends
Dividends paid to OTC (the Parent) from its subsidiaries were as follows:
| | | | | | | | | | | | | | | | | |
(in thousands) | 2021 | | 2020 | | 2019 |
| | | | | |
Cash Dividends Paid to Parent by Subsidiaries | $ | 64,790 | | | $ | 55,614 | | | $ | 55,660 | |
| | | | | |
See OTC’s notes to consolidated financial statements in Part II, Item 8 for other disclosures.
SCHEDULE II - VALUATION AND QUALIFYING ACCOUNTS AND RESERVES
OTTER TAIL CORPORATION
Below is a summary of activity within valuation and qualifying accounts for the years ended December 31, 2021, 2020 and 2019:
| | | | | | | | | | | | | | | | | | | | | | | |
(in thousands) | Balance, January 1 | | Charged to Cost and Expenses | | Deductions 1, 2 | | Balance, December 31 |
| | | | | | | |
Allowance for Credit Losses | | | | | | | |
2021 | $ | 3,215 | | | $ | 93 | | | $ | (1,472) | | | $ | 1,836 | |
2020 | 1,339 | | | 3,138 | | | (1,262) | | | 3,215 | |
2019 | 1,407 | | | 986 | | | (1,054) | | | 1,339 | |
Deferred Tax Asset Valuation Allowance | | | | | | | |
2021 | $ | 800 | | | $ | — | | | $ | (800) | | | — | |
2020 | 800 | | | — | | | — | | | 800 | |
2019 | 600 | | | 200 | | | — | | | 800 | |
| | | | | | | |
1Amounts under Allowance for Credit Losses reflect deductions to the allowance for amounts written-off, net of recoveries. | | | | |
2Amounts under Deferred Tax Asset Valuation Allowance reflect a release of a valuation allowance based on current expectations of the realizability of the associated deferred tax asset. |
3. Exhibits
The following Exhibits are filed as part of, or incorporated by reference into, this report. | | | | | | | |
| | |
No. | | | Description |
| | | |
| | | |
| | | |
3.1 | | | |
3.2 | | | |
4.1 | | | |
10.1.0 | | | |
10.1.1 | | | |
10.1.2 | | | |
10.1.3 | | | |
| | | |
10.2 | | | |
10.3 | | | |
10.4 | | | |
10.5 | | | |
10.6 | | | |
10.7 | | | |
10.8 | | | |
10.9.0 | | | Agreement for Sharing Ownership of Generating Plant by and between the Company, Montana-Dakota Utilities Co., and Northwestern Public Service Company (dated as of January 7, 1970). Previously filed as Exhibit 10-F in Form 10-K for the year ended December 31, 1989. |
10.9.1 | | | Letter of Intent for purchase of share of Big Stone Plant from Northwestern Public Service Company (dated as of May 8, 1984). Previously filed as Exhibit 10-F-1 in Form 10-K for the year ended December 31, 1989. |
10.9.2 | | | Supplemental Agreement No. 1 to Agreement for Sharing Ownership of Big Stone Plant (dated as of July 1, 1983). Previously filed as Exhibit 10-F-2 in Form 10-K for the year ended December 31, 1991. |
10.9.3 | | | Supplemental Agreement No. 2 to Agreement for Sharing Ownership of Big Stone Plant (dated as of March 1, 1985). Previously filed as Exhibit 10-F-3 in Form 10-K for the year ended December 31, 1991. |
10.9.4 | | | Supplemental Agreement No. 3 to Agreement for Sharing Ownership of Big Stone Plant (dated as of March 31, 1986). Previously filed as Exhibit 10-F-4 in Form 10-K for the year ended December 31, 1991. |
10.9.5 | | | |
10.9.6 | | | Amendment I to Letter of Intent dated May 8, 1984, for purchase of share of Big Stone Plant. Previously filed as Exhibit 10-F-5 in Form 10-K for the year ended December 31, 1992. |
10.10 | | | |
10.11.0 | | | Agreement for Sharing Ownership of Coyote Station Generating Unit No. 1 by and between the Company, Minnkota Power Cooperative, Inc., Montana-Dakota Utilities Co., Northwestern Public Service Company and Minnesota Power & Light Company (dated as of July 1, 1977). Previously filed as Exhibit 5-H in filing 2-61043. |
10.11.1 | | | Supplemental Agreement No. One, dated as of November 30, 1978, to Agreement for Sharing Ownership of Coyote Generating Unit No. 1. Previously filed as Exhibit 10-H-1 in Form 10-K for the year ended December 31, 1989. |
10.11.2 | | | Supplemental Agreement No. Two, dated as of March 1, 1981, to Agreement for Sharing Ownership of Coyote Generating Unit No. 1 and Amendment No. 2 dated March 1, 1981, to Coyote Plant Coal Agreement. Previously filed as Exhibit 10-H-2 in Form 10-K for the year ended December 31, 1989. |
10.11.3 | | | Amendment, dated as of July 29, 1983, to Agreement for Sharing Ownership of Coyote Generating Unit No. 1. Previously filed as Exhibit 10-H-3 in Form 10-K for the year ended December 31, 1989. |
10.11.4 | | | Agreement, dated as of September 5, 1985, containing Amendment No. 3 to Agreement for Sharing Ownership of Coyote Generating Unit No. 1, dated as of July 1, 1977, and Amendment No. 5 to Coyote Plant Coal Agreement, dated as of January 1, 1978. Previously filed as Exhibit 10-H-4 in Form 10-K for the year ended December 31, 1992. |
10.11.5 | | | |
10.11.6 | | | |
10.12.0 | | | |
10.12.1 | | | |
10.12.2 | | | |
10.13 | | | |
| | | | | | | |
| | |
No. | | | Description |
10.14.0 | | | |
10.14.1 | | | |
10.14.2 | | | |
10.15 | | | |
10.16 | | | |
10.17 | | | |
10.18 | | | |
10.19 | | | |
10.20 | | | |
10.21 | | | |
10.21 | | | |
10.22 | | | |
10.23 | | | |
10.24 | | | |
10.25 | | | |
10.26 | | | |
10.27 | | | |
10.28 | | | |
10.29 | | | |
| | | |
10.30 | | | |
10.31 | | | |
10.32 | | | |
10.33 | | | |
10.34 | | | |
10.35 | | | |
10.36 | | | |
10.37 | | | |
21 | | | |
23 | | | |
24 | | | |
31.1 | | | |
31.2 | | | |
32.1 | | | |
32.2 | | | |
101.SCH | | | Inline XBRL Taxonomy Extension Schema Document. |
101.CAL | | | Inline XBRL Taxonomy Extension Calculation Linkbase Document. |
101.LAB | | | Inline XBRL Taxonomy Extension Label Linkbase Document. |
101.PRE | | | Inline XBRL Taxonomy Extension Presentation Linkbase Document. |
101.DEF | | | Inline XBRL Taxonomy Extension Definition Linkbase Document. |
104 | | | Cover Page Interactive Data File (formatted as Inline XBRL and contained in Exhibit 101). |
| | | |
*Management contract, compensatory plan or arrangement required to be filed pursuant to Item 601(b)(10)(iii)(A) of Regulation S-K.
**Confidential information has been omitted from this Exhibit and filed separately with the Securities and Exchange Commission pursuant to a confidential treatment request under Rule 24b-2.
The Company hereby undertakes to furnish copies of any of the omitted schedules and exhibits to the Securities and Exchange Commission upon request.
Pursuant to Item 601(b)(4)(iii) of Regulation S-K, copies of certain instruments defining the rights of holders of certain long-term debt of the Company are not filed, and in lieu thereof, the Company agrees to furnish copies thereof to the Securities and Exchange Commission upon request.
| | | | | |
ITEM 16. | FORM 10-K SUMMARY |
None.
SIGNATURES
Pursuant to the requirements of Section 13 or 15(d) of the Securities Exchange Act of 1934, the registrant has duly caused this report to be signed on its behalf by the undersigned, thereunto duly authorized.
| | | | | | | | |
| OTTER TAIL CORPORATION |
| | |
| By: | /s/ Kevin G. Moug |
| | Kevin G. Moug Chief Financial Officer and Senior Vice President (authorized officer and principal financial officer) |
| | |
| | Dated: February 16, 2022 |
Pursuant to the requirements of the Securities Exchange Act of 1934, this report has been signed below by the following persons on behalf of the registrant and in the capacities and on the dates indicated:
Signature and Title
| | | | | | | | | | | |
Charles S. MacFarlane | ) | | |
President and Chief Executive Officer | ) | | |
(principal executive officer) and Director | ) | | |
| ) | | |
Kevin G. Moug | ) | | |
Chief Financial Officer and Senior Vice President | ) | | |
(principal financial and accounting officer) | ) | | |
| ) | By | /s/ Charles S. MacFarlane |
Nathan I. Partain | ) | | Charles S. MacFarlane |
Chairman of the Board and Director | ) | | Pro Se and Attorney-in-Fact |
| ) | | Dated: February 16, 2022 |
Karen M. Bohn, Director | ) | | |
| ) | | |
John D. Erickson, Director | ) | | |
| ) | | |
Steven L. Fritze, Director | ) | | |
| ) | | |
Kathryn O. Johnson, Director | ) | | |
| ) | | |
Timothy J. O’Keefe, Director | ) | | |
| ) | | |
James B. Stake, Director | ) | | |
| ) | | |
Thomas J. Webb, Director | ) | | |
| ) | | |
Michael E. LeBeau, Director | ) | | |